CNC cutting comes in different methods and techniques. In today’s manufacturing, wire EDM machining is a prominent CNC cutting process that you can use as a substitute for regular cutting tools. It is compatible only with specific material workpieces. Also, it uses complex components to run this manufacturing process.
Table of Contents
Wire EDM Machining Components
Wire EDM is 100% programmable. You can take control of each component of this machining operation to ensure a smooth rapid manufacturing process. Learn about the workings of these wire EDM components:
CNC control unit equipment
EDM machining uses a CNC control unit as the tool to control the movements of the components. Like any other CNC machining services processes, you can program your EDM wire machining to follow your exact design blueprint with the highest accuracy. This control unit equipment will become the brain for the EDM wire machining operation.
Dielectric water
It is a specialized water that you will use during the EDM cutting process. You must submerge the electrode and the workpiece into this formulated water medium to ensure a smooth electrical discharge process. Aside from that, the dielectric water can also help remove unnecessary waste during EDM wire cutting.
Wire electrode
It is the primary cutter for the EDM wire machining operation. This wire electrode will cut through the material workpiece using the high heat and generated sparks. You can control the angles of the wire electrode during EDM cutting.
Power supply
The power supply unit will generate the primary power source for the entire wire EDM machining equipment. It generates the electrical power for the control unit and the EDM tools. It uses a high-voltage unit to ensure a steady electrical supply for the EDM equipment.
Flushing mechanism
The flushing mechanism connects with the primary dielectric bath chamber. It allows you to flush out the dielectric water after its usage. Thus, you can fill the bath chamber with the new dielectric water.
Wire EDM machining can’t work without these components in place. Figuring out the working of these components can help you run this manufacturing process better.
How Wire EDM Machining Process Works
Regular cutting tools might not provide the best cuts for certain material workpieces. EDM wire cuts are the best substitute for regular cuts in certain situations. Learn about how this machining works in manufacturing:
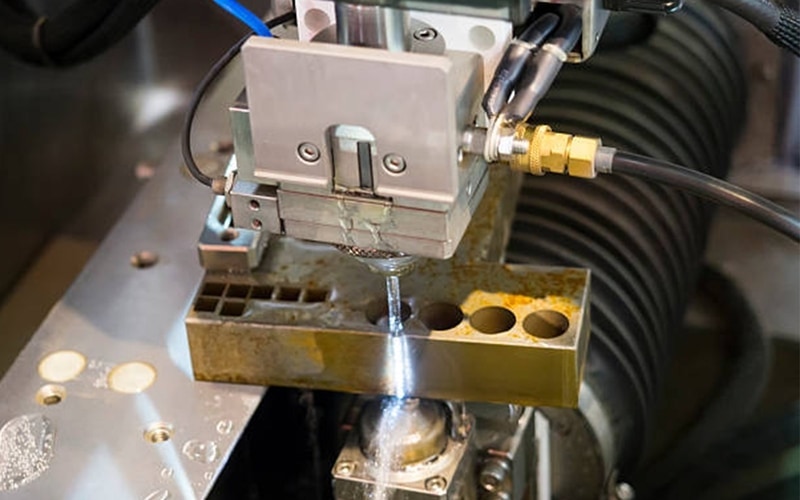
Prepare the wire electrode for wire EDM Machining
The process won’t work without the use of the wire electrode. The first step is to prepare the wire electrode and put it at a specific angle. The wire will act as an electrode during the electrical discharge process.
Deionized water
The next step is to put the workpiece material and the wire electrode in the deionized water. You must submerge the pair into the deionized water during EDM cutting. This specialized water will serve as an insulator during the EDM machining.
Electrical discharge
The electrical discharge reaction will start when you move the wire toward the material workpiece. The electrical discharge will generate high heat around the surface of the material workpiece. This heat will begin to cut the material workpiece during application.
Apply the heat in wire EDM machining
It’s time to use the wire to cut the specific parts from the material workpiece. Use the high temperature generated from the electrical discharge to do that. Applying specific angles will make the cutting process as smooth as possible.
Wire EDM Machining Precise cuts
It allows for the precision cuts of the material workpiece, provided that the material is electrically conducive. The high heat executed on the material surface will create the most accurate cuts. You can measure exactly how you need to perform the cuts on the material workpiece.
Cooldown
Cooldown will come after applying the EDM cuts on the material workpiece. This process will also entail removing any unnecessary particles from the material surface. This way, you can end up with the clean cuts for the workpiece.
These steps explain how this process works in manufacturing. It results in burr-free and natural cuts that you can rely on regarding accuracy.
Wire EDM Machining Challenges
Wire EDM is a manufacturing process that is not without flaws. You must understand some challenges in this manufacturing process to ensure dependable and high-quality cuts. Here are the most common issues in this process:
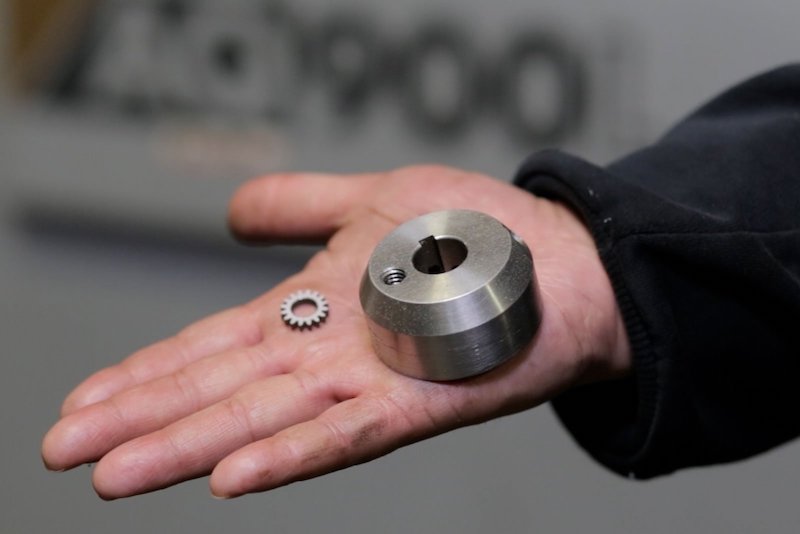
Wire damage
Damage to the wire electrode is a commonplace occurrence during the wire EDM operation. Damaged wires can cause problems during the cutting process. Replacing the damaged wire is essential to ensure the best result in each cut. Running the wire EDM operation with damaged wires can significantly reduce the cutting quality and accuracy.
Workpiece compatibility
Wire EDM machining is only compatible with material workpieces that have electrical conductivity. Without this specific characteristic of the material workpiece, the electrical discharge will not start during this process. So, you can’t use plastics or other non-conductive materials for the wire machining.
Operating adjustments
Sometimes, the cutting quality from the wire EDM machining is not consistent. You will need to constantly check the components of this process to ensure the best cutting quality in your manufacturing operation. It includes checking the wires and dielectric water conditions from time to time.
Slow progression
The cutting process for wire EDM is slower than the regular cuts. Also, this manufacturing operation requires meticulous preparation and configuration before starting it. You can add the prep time of wire EDM machining to the overall speed of this manufacturing operation. This process is not suitable for those looking for fast-paced cutting.
Always keep in mind these challenges in the wire EDM machining process. You can prevent any issues during your manufacturing operation by understanding these challenges.
Conclusion
Wire EDM machining can become the best cutting method for conductive workpiece materials. It produces straightforward and precise cuts that will follow your design requirements accurately, it is commonly used in sheet metal cutting such as badge and keychains. However, addressing the challenges in this manufacturing process is essential to help you gain reliable cuts for each material workpiece. This process can offer an overall better-quality cut compared to regular CNC cutting.
Besides from wire machining, TEAM Rapid also offers CNC machining, injection molding, and die casting for your rapid prototypes, small volume production, and mass production needs. Contact our team today to request a free quote now!