Polishing is essential for removing micro-imperfections from the surfaces of manufactured goods and machined components. Its main goal is to eliminate these flaws and sanding marks, leaving a glossy finish. This article will concentrate on vapor polishing, a popular technique known for its effectiveness in enhancing the transparency of plastic materials. This method is particularly beneficial when plastics are used in making lightweight optical lenses, where high transparency is crucial. Let’s explore the details of what is vapor polishing.
Table of Contents
What’s Vapor Polishing?
Vanish polishing is a method of polishing plastics commonly used to achieve high transparency of plastics or to improve the surface smoothness, such as plastics used to make lightweight optical quality lenses.
In order to enhance surface smoothness, components are typically exposed to flowing chemical vapor. Vapor polishing, in this context, is one of the most effective and quickest methods to achieve optimal transparency.
Advantages of Using Vapor Polishing
- Enhance the look and performance, offering greater beauty and superior protection.
- Improve their surface with enhanced waterproof performance.
- Improve endurance.
- Improve Moisture proofing.
- Accurate data for dimensional accuracy and geometries of the printed part.
How Does Vapor Polishing Process Work?
Because of the different kinds of smoothing the surface of different materials, vapor polishing may be the best choice. Maintaining accurate pressure and temperature control during the vapor polishing process is crucial. Here is an overview of the vapor polishing procedure:
Step 1: Unprocessed plastic components are placed in a sealed chamber where precision machining agents like FA 326 are utilized. This agent is generally appropriate for various plastic materials, though different agents may be employed depending on the specific material being processed.
Step 2: It will generate the vapor around the part when the unprocessed plastic parts is in the sealed chamber with heating the agent to the desired temperature.
Step 3: Vapor adheres to the surface of the component, resulting in chemical melting. The liquefaction and redistribution of molten materials help reduce surface valleys and peaks, thereby eliminating surface roughness.
Step 4: The material obtains better gloss and luster because of the chemical melting. And the finishing agent and processing material makes more glosser on the enhancement.
Step 5: After completing the task, heat up the polishing chamber immediately and remove the finishing agent and steam. The remaining workpieces will be clean and do not require the use of other materials for processing and removal.
Step 6: After finished the process of vapor polishing, the workpiece will be arranged other surface treatments such as painting and dyeing.
Tips for Selecting Solvents for Steam Polishing
The choice of solvent is important because there must be a strong affinity between the solvent and polymer vapor for processing. Here’s a recommended list used for vapor smoothing:
- Acetone: A transparent organic liquid renowned for its efficiency and adaptability as a solvent, ideal for ABS components.
- Methyl ethyl ketone (MEK): A colorless liquid with a pungent smell, this highly flammable substance is both corrosive and naturally oxidized, serving as an efficient solvent.It is soluble in both water and alcohol and is widely employed in industrial environments. This liquid ketone is ideal for polishing thermoplastic materials like acrylic, polycarbonate, and ABS, as well as thermosetting plastics such as resins.
- Tetrahydrofuran (THF): A heterocyclic compound (cyclic ether), widely used as a solvent in organic synthesis. and suitable for polishing PLA parts.
- Dichloromethane (DCM): A colorless, volatile liquid with a chloroform-like, sweet odor is widely used as a solvent, and suitable for ABS components.
- Ethyl acetate: A mild solvent works well for polishing PLA, although it might require extended exposure to achieve the best results. It is commonly utilized as a solvent in several industries, including adhesives, paints, and coatings.
Part 1: Before Vapor Polising
- Selection of solvents
Various solvents can be effectively paired with different types of 3D printing materials. For instance, key solvents include methyl ethyl ketone, acetone, dichloromethane, tetrahydrofuran, and ethyl acetate, among others. Specifically, when working with ABS-manufactured components, acetone or dichloromethane is preferred. In the meantime, methyl ethyl ketone emerges as the ideal option for thermoplastic materials. Additionally, when dealing with PLA components, tetrahydrofuran or ethyl acetate is utilized.
- Temperature regulation
The solvent’s temperature greatly influences this process. In general, increased temperatures result in quicker smoothing.
- Safety precautions
When using solvents during the vapor polishing process, it is crucial to exercise caution. Besides, it’s crucial to always wear protective equipment such as safety goggles and gloves. Then, ensure you work in well-ventilated, cool areas, avoiding any exposure to sparks or open flames.
- Make the parts clean before polishing
Before polishing, make sure the parts are free of dirt, grease, and debris. Use a reliable degreaser to dissolve surface oils, then rinse well with water. Completely dry the parts to avoid water spots. A spotless surface is essential for achieving a smooth, high-quality polish, boosting the final shine and finish.
Part 2: During Vapor Polising
- Exposure to vapor polish
Then, the exposure time is the most important part of the process of vapor polishing with solvent temperature, material type, and polishing level. It not only serves to protect the plastic from damage but also to ensure the task is fully completed.
- Partial orientation
The positioning of the parts influences the polishing quality. Typically, you should arrange the parts so that the surface intended for polishing is oriented downwards and directed towards the solvent.
- Partial geometry
To fully grasp the process, it’s crucial to understand that a component’s geometric form and wall thickness are key to guiding the vapor polishing procedure. Moreover, these elements greatly affect the interaction of vapor with the surface and the final results. Additionally, thoughtfully designed geometry supports effective vapor flow, which is essential for achieving a consistent, high-quality finish. Specifically, wall thickness determines the necessary duration and intensity needed for successful polishing.
Part 3: After Vapor Polising
- After processing
At last, in order to remove residual solvents and improve surface smoothness, there needs post-processing after polishing the part.
Types of Plastics for Vapor Polishing
Vapor smoothing is highly effective on thermoplastics, especially those with high solubility in certain solvents. Furthermore, this technique efficiently enhances the surface quality of a wide range of plastic materials, making it a versatile solution for achieving a polished finish across numerous types of thermoplastics. Therefore, let’s explore some types that can be vapor polished. Shall we take a look?
Types of Plastics | Description |
Acrylic (PMMA) | Acrylic (PMMA) is a man-made resin formed through the polymerization process of methyl methacrylate. This transparent and sturdy plastic frequently serves as an alternative to glass in items like shatter-resistant windows, skylights, illuminated signage, and aircraft canopies. |
ABS | Acetone smoothing for ABS is a post-processing method used on ABS 3D printed filament to remove layer lines by dissolving them with acetone. This process entails exposing the raw ABS prints to acetone vapors, which causes the layers to blend together. Consequently, the surface achieves a sleek and shiny finish, eradicating any noticeable lines. |
Acetone | Acetone is a clear organic liquid renowned for its versatile effectiveness as a solvent. Its chemical structure, featuring both polar and nonpolar traits, allows it to dissolve diverse materials. Thus, acetone effectively interacts with a range of organic and inorganic substances. Moreover, because it mixes completely with water, it aids in dissolving various chemicals in different settings. Despite being organic, its non-toxic nature further enhances its broad usage in numerous applications. |
Polycarbonate (PC) | For polycarbonate (PC) components, steam polishing provides a solution for surface defects that damage appearance as well as functionality. |
Nylon | Vapor polishing also effectively improves the surface smoothness of nylon parts and eliminates roughness during processing or 3D printing. |
Use for Different Industries
Kinds of industries | Description |
Aerospace industry | Vapor polishing plays a vital role in enhancing the surface finish of plastic parts utilized in control systems, instrument panels, and the interiors of aircraft. |
Automotive industry | It is an appropriate precision machining procedure for parts with durability, tactile feel, and smooth surface. |
Medical devices | Use vapor polishing to ensure the manufacture of components with sweat resistant and comfortable to wear. |
Consumer product industry | Manufacture parts with ultra-smooth surfaces by using vapor polishing. |
Industrial manufacturing | This process improves the surface smoothness of industrial parts. |
How to Reduce the Cost of Vapor Polishing?
In order to achieve a smooth and glossy finish on plastic parts by reducing the cost of vapor polishing achieving a smooth, glossy finish on plastic parts, here are some tips:
Firstly, simplify the part design to reduce the amount of polishing required. Additionally, choose the appropriate materials to shorten the processing time. Furthermore, group multiple parts for polishing to improve efficiency. Moreover, automation can simplify processes and reduce labor costs. Finally, outsourcing to a professional company that provides polishing services may be more cost-effective, as these suppliers typically have optimized their processes to reduce the cost of each component.
Conclusion
As can be seen, vapor polishing offers various benefits with optically clearer, higher transparency, and smoother polished surfaces. To maximize the advantages of steam polishing, it’s essential to make informed decisions. Among rapid manufacturing group, Team Rapid Tooling performs the best. It provides customized steam polishing components and parts for you. As a manufacturing firm, we possess significant expertise in producing parts using a variety of post-processing methods.
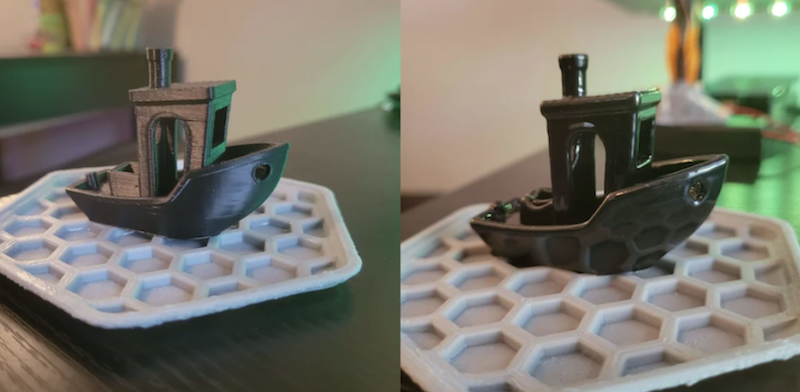
In summary, thanks to cutting-edge technology and advanced expertise, Team Rapid Tooling, a trusted CNC machining China supplier, can enhance your manufacturing processes by reaching exceptional precision as well as efficiency. Why not get in touch with them today?