Vacuum casting of metal in the industry represents a sophisticated method where the introduction of molten metal into molds is performed under a vacuum. This specialized approach is designed to significantly elevate the quality and detail of metal components. By drastically reducing the presence of air and potential impurities during the casting process. This method effectively minimizes the likelihood of oxidation and various casting defects. The primary benefit of using a vacuum is that it makes it easier to facilitate a more precise and regulated metal flow into the mold.
This is essential for producing parts with excellent surface finishes, exceptional dimensional accuracy, and fewer internal flaws. This technique is highly recognized in areas including automotive, aerospace, and medical equipment manufacturing. Where the highest precision and quality standards are required. Because vacuum casting works with a wide range of metals and alloys. It’s a flexible method that may be utilized to make complex and high-quality metal parts.
Table of Contents
- 1 Details of A Vacuum Casting of Metal
- 1.1 Principle of vacuum casting of metal Operation
- 1.2 Quality and Precision
- 1.3 Material Flexibility of vacuum casting of metal
- 1.4 Complex Geometries
- 1.5 Reduced Porosity and Better Mechanical Properties in vacuum casting of metal
- 1.6 Alternative to Investment Casting
- 1.7 Prototyping and Short Production Runs
- 1.8 Environmental Considerations of vacuum casting of metal
- 1.9 Limitations and Challenges
- 1.10 Applications
- 2 Selecting a company to do vacuum casting of metal for a project
- 3 Types of projects best suited for vacuum casting of metals
- 4 Conclusion
Details of A Vacuum Casting of Metal
Principle of vacuum casting of metal Operation
Vacuum casting operates through a meticulous process. Where air is systematically removed from both the mold chamber and the molten metal before and during the metal pouring phase. By creating a vacuum, this method substantially lowers the risk of oxidation and various other imperfections that are more likely in conventional casting. Air evacuation ensures a purer environment, substantially reducing the chances of gas entrapments and other common die casting defects.
Quality and Precision
By leveraging a vacuum environment, the casting process enables the production of components characterized by their exceptional surface finishes, precise dimensions, and a notable reduction in internal flaws. In addition to producing a smoother, more uniform fill, reducing turbulence during the metal’s flow into the mold in a vacuum helps produce parts with unparalleled accuracy and surface quality.
Material Flexibility of vacuum casting of metal
A variety of metals and alloys, including copper, steel, aluminum, and magnesium, can be worked with using the flexible vacuum casting process. Because of its adaptability, it can be used in a wide range of applications with different material requirements. It consequently becomes an essential technology for a wide range of sectors, easily meeting their unique needs.
Complex Geometries
The method shines when tasked with producing parts featuring complex shapes, detailed intricacies, and slender walls — challenges that may pose significant hurdles for other casting techniques. Vacuum casting’s meticulous control over metal flow enables it to faithfully replicate complex designs with high fidelity, meeting stringent specifications with ease.
Reduced Porosity and Better Mechanical Properties in vacuum casting of metal
Using a vacuum significantly reduces the porosity often present in cast items. This reduction in porosity directly contributes to the products’ increased longevity and usefulness by enhancing their mechanical qualities, such as strength and durability.
Alternative to Investment Casting
acuum casting is a strong contender in situations where improved mechanical qualities are needed or if larger pieces with better surface finishes and dimensional precision need to be cast. It stands out for its ability to meet or exceed quality benchmarks with greater efficiency in specific contexts.
Prototyping and Short Production Runs
Not only is vacuum casting an effective strategy for fabricating high-quality rapid prototypes, but it also proves to be cost-efficient for limited production runs. It is adept at producing end-use parts or prototypes for thorough testing and validation phases ahead of committing to full-scale production, ensuring design integrity and functionality.
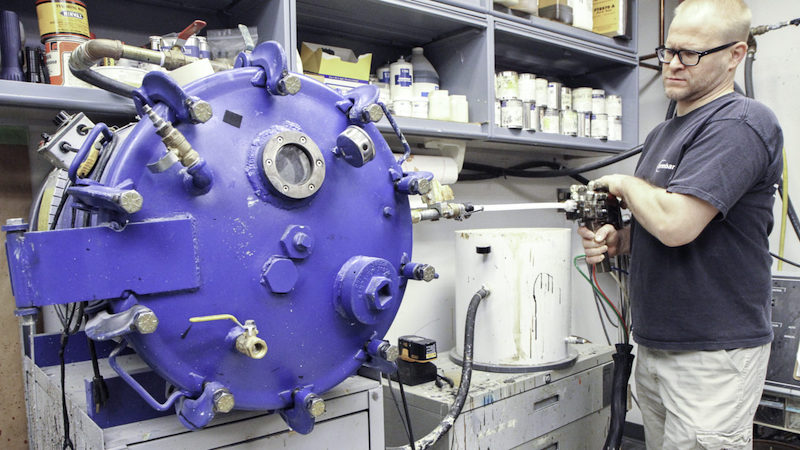
Environmental Considerations of vacuum casting of metal
By its very nature, vacuum casting reduces emissions and waste, positioning it as a more environmentally considerate choice among casting methods. The controlled vacuum environment significantly diminishes the release of harmful substances, aligning with sustainable rapid manufacturing practices.
Limitations and Challenges
Despite its numerous benefits, vacuum casting can entail higher costs and longer production times when compared to other casting techniques, largely due to the specialized equipment and intricate mold preparation required. Additionally, there are practical limitations concerning the size of parts that can be efficiently and effectively produced through this method.
Applications
The process is extensively utilized across multiple sectors for the creation of parts demanding high precision and enhanced mechanical properties. These include, but are not limited to, engine components, medical equipment, aerospace components, and delicately crafted jewelry, highlighting its adaptability and critical role in the manufacturing of complex and high-quality products.
Selecting a company to do vacuum casting of metal for a project
Choosing the right vacuum casting company is vital for the quality and precision of your parts. Aim for a firm with a proven success history, demonstrated through a diverse portfolio and positive client feedback. It’s essential to prioritize companies with a strong emphasis on innovation, modern technology, and quality control, including ISO certifications. Additionally, a focus on excellent communication and customer service will ensure a smooth and efficient partnership. By evaluating these aspects, you can identify a company that meets your project’s requirements and upholds the highest manufacturing standards.
Types of projects best suited for vacuum casting of metals
Vacuum metal casting is essential for projects needing precise detail, excellent surface quality, and complex designs. It offers an economical route for developing prototypes and is perfect for small to medium-sized production runs, avoiding the high costs of traditional manufacturing. Ideal for the medical, aerospace, and automotive industries, it also suits the production of bespoke jewelry and art, as well as electronic components requiring strict tolerances. Vacuum casting navigates complex geometries and thin profiles with ease, serving as a reliable method from design to production, ensuring consistent quality throughout.
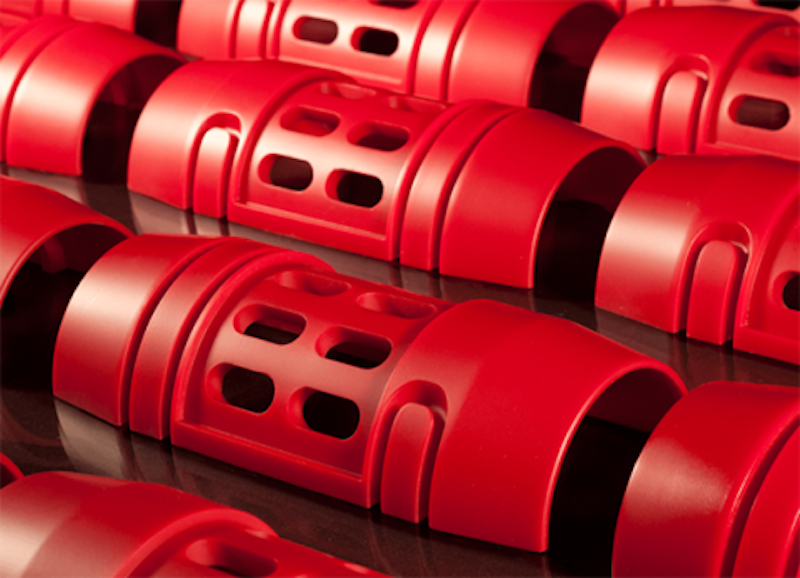
Conclusion
In summary, metal vacuum casting is an incredibly advantageous manufacturing process that stands out for its amazing ability to create parts that are flawless in every way and incredibly exact. These parts’ remarkable mechanical properties such as strength, durability, and resistance to wear and tear—make them perfect for a wide range of applications. The wide array of metals and alloys compatible with this method showcases its flexibility and unlocks numerous possibilities for industrial use.
This versatility ensures that vacuum casting can meet the specific needs of projects requiring intricate and complex designs. Thereby making it a preferred method for producing detailed components in industries as varied as aerospace, automotive, medical devices, and beyond. The convergence of these benefits—quality, precision, mechanical integrity, and material versatilities. solidifies vacuum casting of metal as a cornerstone technique in the realm of manufacturing, catering to the evolving demands of modern industry.
Besides from vacuum casting, TEAM Rapid also offers CNC machining, 3D printing, and injection moulding to meet your low to high volume quantities needs. Contact us today to request a free quote now!