In the realm of manufacturing marvels, injection moulding emerges as a star, crafting parts by injecting molten material into moulds. Step onto the stage of innovation, and there’s a term that takes centre stage: shot size. This term holds the reins in injection moulding, dictating the material’s molten journey into moulds with every cycle. Grasping shot size’s essence is like wielding a master key for top-notch parts and streamlined injection moulding.
Table of Contents
- 1 Unveiling the Craftsmanship of Injection Molding: A Journey into Precision Production
- 2 The Crucial Role of Shot Size in Injection Molding: Balancing Precision and Efficiency
- 3 Navigating the Influences on Shot Size in Injection Molding: A Symphony of Variables
- 4 Demystifying Shot Size Calculation: A Practical Guide
- 5 The Ripple Effect of Shot Size Errors: Navigating Quality Quandaries
- 6 Conclusion of shot size in injection molding
Unveiling the Craftsmanship of Injection Molding: A Journey into Precision Production
Imagine a process that marries the intricacies of material science with the finesse of artistry. Welcome to the world of injection moulding, a manufacturing marvel that orchestrates the transformation of molten substances, primarily plastics, into finely crafted components through meticulous precision.
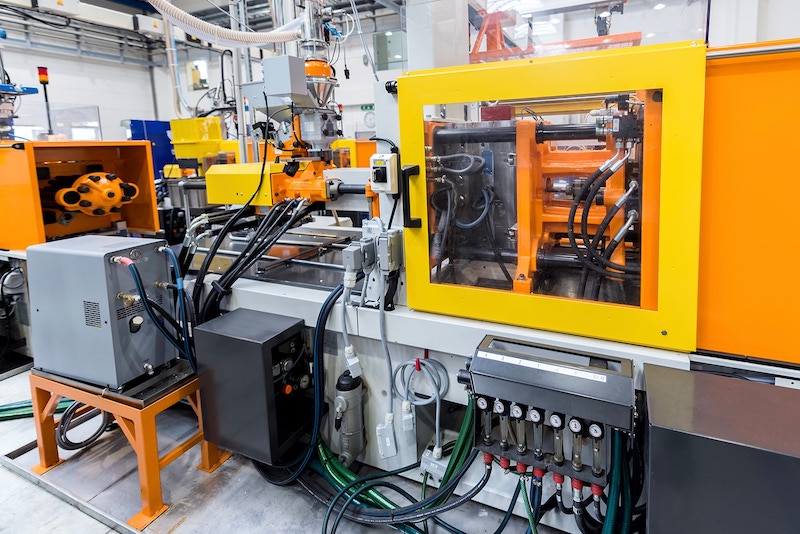
The Fundamental Principle
Injection moulding operates on a foundational principle: the transformation of solid plastic into a liquid state through controlled heating. This molten material is then meticulously injected into a mould cavity, assuming its form as it cools and solidifies. This technique epitomizes the marriage of precision and production.
Precision Beyond Measure
One of the most remarkable facets of plastic moulding is its prowess in producing components with intricate designs and exacting precision. Its ability to replicate complex geometries and details with consistency is an unparalleled feat, rendering it indispensable in industries that demand perfection.
Economical Ingenuity
Beyond its artistic finesse, injection moulding exhibits economic prowess. Though the initial investment in tooling and equipment is substantial, its economies of scale come to the forefront during large-scale production. This financial efficiency makes it a cornerstone for industries seeking high-quality output at a reasonable cost.
A Multifaceted Influence
As we traverse various industries, injection moulding’s impact becomes evident. It graces the automotive realm with intricately designed components, bestows consumer goods with ergonomic elegance, supports medical advancements through precision components, and adorns electronics with sleek casings.
The Crucial Role of Shot Size in Injection Molding: Balancing Precision and Efficiency
In the realm of injection moulding, the term “shot size” takes centre stage, referring to the volume of material injected into the mould during a single cycle. This vital parameter serves as the cornerstone of the moulding process, directly impacting the outcome of each production run.
Precision and Parameters: The Significance of Shot Size
It assumes a paramount role in the injection moulding landscape. Its magnitude is a key determinant in achieving optimal part quality. An inadequate size could result in incomplete mould filling, leading to defects in the finished product. Conversely, an excessive shot size might lead to material overflow, causing waste and potential damage to the mould.
Calculating the Ideal Balance: A Delicate Equation base on shot size
Attaining the perfect shot size requires a delicate equilibrium between mould cavity volume, part thickness, and material density. This intricate interplay ensures that the mould is adequately filled without excessive material spillage. Achieving this equilibrium demands meticulous calculation and understanding of material behaviour.
Crafting Excellence Through Precision
Injection moulding professionals navigate the complexities of size through a blend of technical expertise and practical experience. By carefully analyzing material properties, mould specifications, and production requirements, they fine-tune the injection process to achieve precision and efficiency.
Material Composition: Density’s Dictation
Within the realm of injection moulding, the intricacies of shot size are a result of several intertwining factors. The type of material employed stands as a significant influencer. Distinct materials possess varying densities, leading to a proportional impact on shot size. Denser materials necessitate larger sizes to ensure complete plastic multi-cavity mould filling, a dance of physics that resonates throughout the moulding process.
Mould Precision: Design’s Signature
The blueprint of the mould intricately shapes the size narrative. Its dimensions, contours, and cavity intricacies silently dictate the required shot size. A capacious mould cavity extends a demand for a larger shot size to match. In this choreography of design and dimension, the mould emerges as a silent conductor of size intricacies.
Machine Mastery: Calibration’s Role
Central to the orchestration of size is the injection moulding machine, armed with settings akin to musical notes. Factors such as injection pressure and speed wield influence harmonizing with material and mould dynamics. The resonance of higher injection pressure, for instance, may herald an elevated shot size requirement.
The Fusion of Influences: A Synchronized Production
These variables—a blend of material properties, mould geometry, and machine orchestration—unite to execute a choreographed precision in shot size. This harmonization of elements crafts a symphony of production where shot size emerges as the conductor’s baton, brushing precision onto each manufactured piece. Understanding the interplay of these influences becomes the hallmark of moulding mastery—a realm where size assumes the role of a sculptor’s chisel, refining excellence in every stroke.
Demystifying Shot Size Calculation: A Practical Guide
The Equation Unveiled: A Simple Approach
Calculating shot size in injection moulding involves a straightforward process, relying on the mould cavity’s volume and the material’s density. The formula? A multiplication that bridges the gap:
Shot Size (grams) = Volume of Mold Cavity (cm³) × Material Density (g/cm³)
• Illustrating Precision: A Practical Demonstration
Imagine a scenario where a mould cavity occupies 100 cubic centimetres while the material of choice boasts a density of 1.2 grams per cubic centimetre.
1. Volume of Mold Cavity Calculation: Volume of mould cavity = 100 cm³
2. Material Density: 1.2 g/cm³
Shot Size Calculation: Shot size = 100 cm³ × 1.2 g/cm³ = 120 g
In this case, the shot size tallies to 120 grams—a precise calculation that crafts the foundation for moulding mastery.
Melding Science and Craftsmanship: The Essence of Calculation
Beyond the formula lies an art of precision. Injection moulding connoisseurs wield this calculation like a sculptor’s chisel, ensuring each shot size calculation resonates with accuracy. This equation embodies the fusion of mathematics and craftsmanship, a blend that yields parts of perfection born from the symphony of numbers and moulds.
In the realm of injection moulding, an improperly calculated or set shot size can cast a shadow over the final product. A shot size that’s too small might lead to incomplete mould filling, birthing parts marred by imperfections and structural frailties.
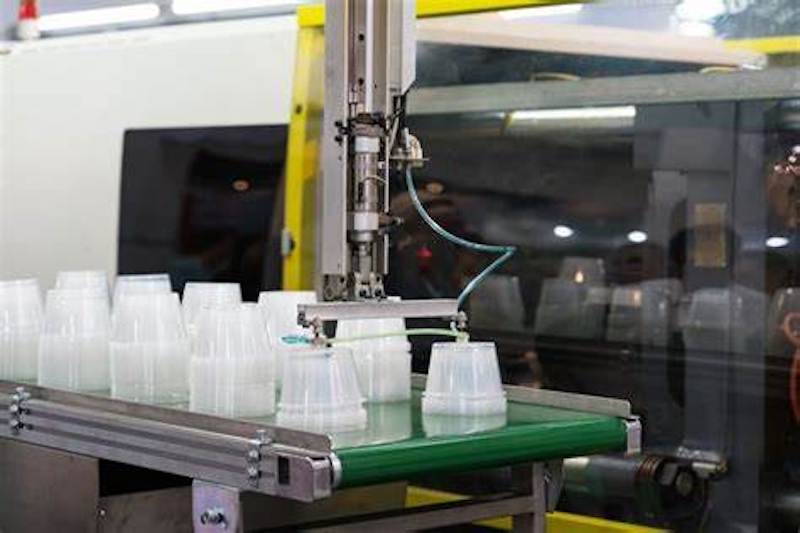
Overflow Woes: Material Mishap
Conversely, an oversized size can invite chaos. The mould’s boundaries are breached, spilling excess material and incurring wastage. Worse yet, this material overflow can inflict harm upon the mould itself, causing damage that reverberates through the production line.
Mastery in Precision: A Necessity
In essence, the size wields an unparalleled influence on the outcome. Its miscalculation can cascade into defects, inefficiencies, and compromised quality. Thus, a harmonious equilibrium in size calculation and setup is the guardian of injection moulding’s excellence, ensuring each part emerges as a testament to precision and mastery.
Conclusion of shot size in injection molding
In the realm of injection moulding, the comprehension and precise calculation of shot size stand as pivotal pursuits. This critical parameter wields a profound impact, influencing not only the quality of the final product but also the structural integrity and visual appeal. Accurate size calibration safeguards against defects and inefficiencies that may ripple through the production process. As such, mastering shot size’s nuances becomes the cornerstone for achieving manufacturing excellence, a realm where precision prevails, and each moulded piece attests to the mastery of the craft.
Besides from injection molding, TEAM Rapid also offers rapid prototyping, CNC machining, and die casting to meet your projects needs. Contact our team today to request a free quote now!