Injection molding, a prevalent manufacturing technique, fabricates plastic components through the injection of molten material into molds. This method, known for its efficiency and precision, contributes significantly to diverse industries. It molds products with intricate designs and ensures cost-effective production. Injection molding system it has significance extended across sectors, from automotive to healthcare, making it a vital player in contemporary manufacturing.
Table of Contents
Injection Molding System Components: Crafting Precision
The injection molding system, a marvel of modern manufacturing, is an ensemble of crucial components, each vested with a pivotal role. Let’s take a closer look at these integral parts and their respective functions:
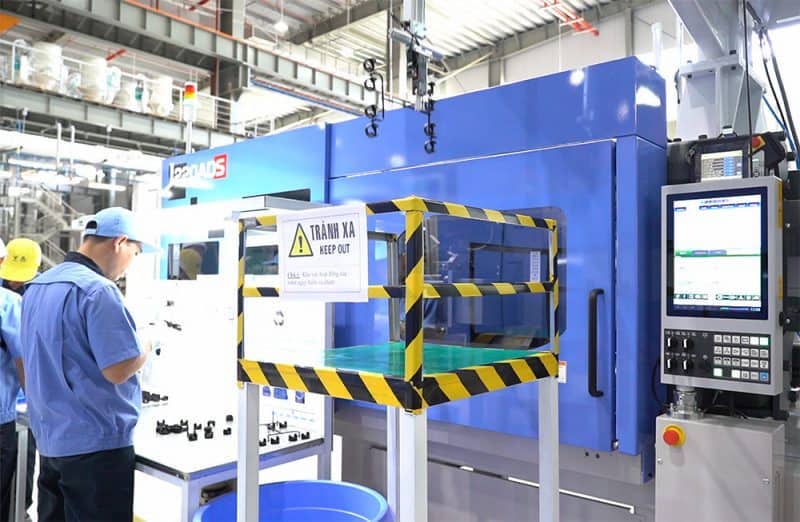
Heating Unit
Nestled within the machinery is the heating unit, where the plastic granules are subjected to a controlled transformation. This is where they undergo the transition from solid granules to a molten state. Temperature control in this unit is paramount, ensuring that the plastic reaches the perfect consistency without degradation.
Screw
The screw, a vital component, takes center stage next. It serves a dual role. First, it expertly blends the molten plastic, ensuring uniform temperature and consistency throughout the material. Second, it propels the molten plastic into the awaiting mold/ rapid tooling.
Mold
The mold, a masterpiece of custom mold design, is up next. Comprising two halves, it’s a critical element in the process, giving shape to the final product. During the injection, these mold halves come together to form the foundation of the product.
Clamping Unit
Ensuring precision and integrity during injection and cooling is the clamping unit. This unit firmly holds the mold halves together as the plastic takes its form. After the part has solidified, the clamping unit gracefully separates the mold halves, allowing the finished product to emerge.
Ejection System
Once the newly injection molded part has cooled and reached its final form, it’s the ejection system’s moment to shine. This system skillfully nudges the part out of the mold, setting the stage for the next cycle.
Control System
Overseeing this intricate dance of components is the control system. It is the maestro, directing the entire orchestra. Monitoring temperature, pressure, speed, and various other variables, the control system ensures a harmonious and successful injection molding process.
Each of these components is a vital instrument in this symphony of precision and efficiency. Their orchestration guarantees the production of high-quality parts, making the injection molding system an essential player in modern rapid manufacturing.
The Injection Molding Process: Crafting Precision, Step by Step under injection molding system
The injection molding process, a fundamental pillar of modern manufacturing, is characterized by its exacting nature. To comprehend its intricacies, let’s systematically dissect the various steps, appreciating the profound significance of each in guaranteeing the quality of the end product.
Material Preparation
• Step: Our journey commences with material preparation, where a judicious selection of plastic pellets or granules is made, aligning with the intended product’s specific attributes. These chosen materials are subsequently introduced into the hopper.
• Importance: The foremost pivotal decision in this process, material selection significantly influences the product’s structural and functional qualities, from its strength and flexibility to its thermal resilience.
Heating and Melting in injection molding system
• Step: Within the confines of the heating unit, the plastic undergoes a transformative process, transitioning from its solid state to a molten form. Stringent temperature control safeguards against material degradation.
• Importance: The meticulous management of temperature is paramount, ensuring a homogeneous melt. Temperature deviations during this phase can give rise to defects or inconsistencies in the final product.
Injection
• Step: Guided by the screw, the molten plastic is ushered into the mold cavity, meticulously filling every contour, thus bestowing the product with its definitive shape.
• Importance: This is the stage where the envisioned product takes physical form. Precise injection molding guarantees the faithful replication of the mold’s design.
Cooling in injection molding system
• Step: After the injection, the mold is swiftly subjected to a cooling process, causing the plastic to solidify and embrace the designated form.
• Importance: The cooling phase imparts the product’s ultimate characteristics, encompassing its strength and structural integrity. Inadequate cooling may lead to defects and warping.
Mold Opening and Ejection
• Step: The clamping unit releases the mold, while the ejector system exquisitely ushers the completed product out.
• Importance: Flawless ejection is a prerequisite for safeguarding the product against adherence to the mold, thereby precluding any deformations during extraction.
Inspection and Quality Control
• Step: The freshly molded product is subjected to rigorous scrutiny, designed to unveil any potential flaws or imperfections.
• Importance: Stringent quality control procedures serve as the vanguard, permitting only the most refined products to reach the market. The presence of defects can usher in product failures and necessitate costly recalls.
Repeating the Cycle
• Step: The process reiterates, with the mold seamlessly closing for the commencement of the ensuing injection molding cycle.
• Importance: Maintaining the fluidity and consistency of the process cycle is instrumental in preserving both product quality and production efficiency.
At each juncture, these meticulously executed steps coalesce harmoniously, yielding precise and top-tier plastic products. Meticulous attention to detail and precision throughout these stages is the linchpin of the process, ensuring that the final products adhere to the highest quality standards and perform according to expectations. Injection molding thus retains its indispensable status in an array of industries, exemplifying a manufacturing method par excellence.
Advantages and Challenges of Injection Molding
Injection molding presents an array of advantages, rendering it a popular choice for producing a wide range of parts. It boasts high plastic molding production rates, ensuring efficient output. This process excels in dimensional accuracy and accommodates an extensive selection of materials. Moreover, it allows for the manufacture of complex shapes that would otherwise pose manufacturing challenges.
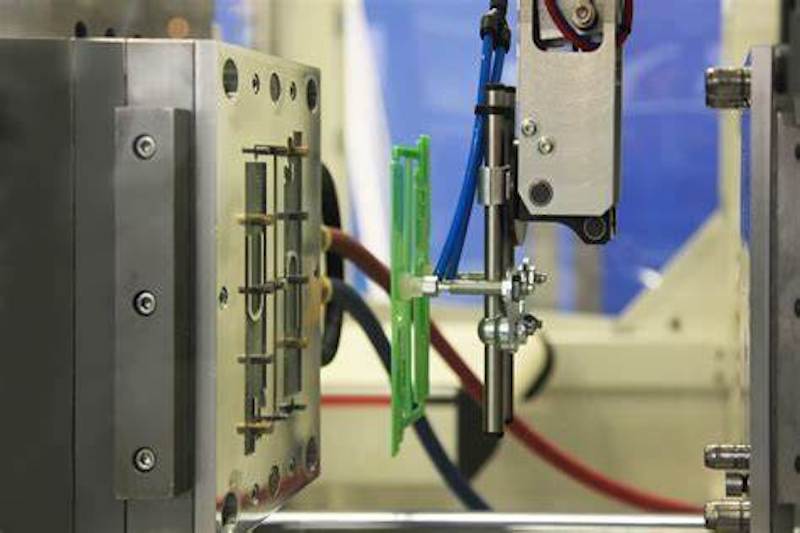
Nonetheless, challenges coexist with these advantages. The upfront costs can be significant, primarily due to the requirement for tailor-made molds. Additionally, meticulous control of parameters like temperature and pressure is imperative for ensuring consistent quality.
To tackle these obstacles, manufacturers frequently employ computer-aided design (CAD) and computer-aided manufacturing (CAM) software for mold creation, reducing time and expenses. Embracing process automation also maintains uniform quality and curbs labor costs.
Despite these hurdles, the merits of injection molding often surpass the drawbacks, firmly establishing it as an invaluable asset within the manufacturing industry.
Conclusion of injection molding system
The injection molding system remains an indispensable linchpin in contemporary manufacturing, delivering precision, efficiency, and adaptability. Its pivotal role in influencing various industries, spanning from automotive to healthcare, is incontrovertible. With its capacity to produce intricate, top-tier products, injection molding perpetuates its drive for innovation and advancement within the manufacturing domain.
Besides from injection molding, TEAM Rapid also offers rapid prototyping, CNC machining, and die casting to meet your projects needs. Contact our team today to request a free quote now!