Two different sub-processes in injection molding allow you to add more steps to the regular molding operation. The first one is insert molding–an plastic molding process that lets you add a metal insert into an existing plastic mold. The second one is over-molding–an injection molding process that allows the addition of secondary plastic material on top of the primary plastic part. For beginners, these two sub-processes of injection molding might be perplexing. So, let’s learn about the differences between overmolding and insert molding.
Table of Contents
- 1 Here are the differences between overmolding and insert molding:
- 1.1 Overmolding and Insert Molding: Metal and Plastic vs. Plastic and Plastic Materials
- 1.2 A Single Mold vs. Two Molds
- 1.3 Overmolding and Insert Molding: Single vs. Multiple Injection Molding Processes
- 1.4 One Color Option vs. Multiple Colors
- 1.5 Faster vs. Slower Production Process
- 1.6 Overmolding and Insert Molding: Lower Costs vs. Bigger Expenses
- 1.7 Straightforward Process vs. Risk of Material Incompatibility
- 2 Conclusion
Here are the differences between overmolding and insert molding:
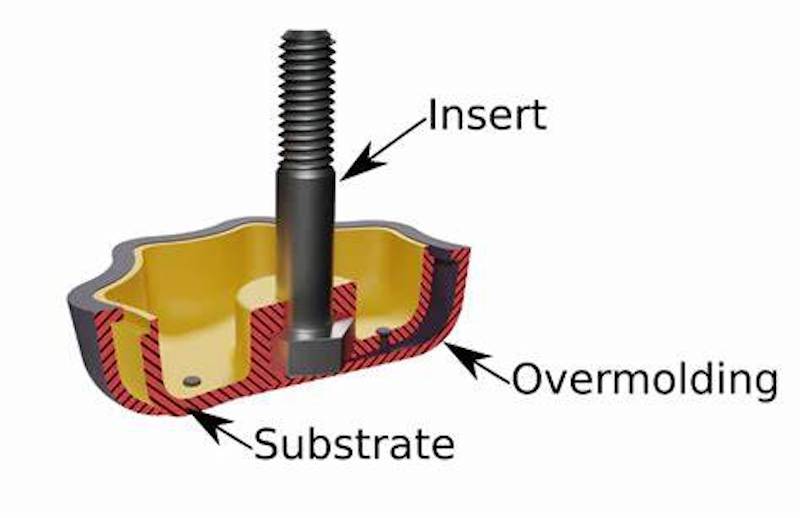
Overmolding and Insert Molding: Metal and Plastic vs. Plastic and Plastic Materials
Insert molding combines the metal and plastic material in one mold, allowing you to add a metal insert to the primary plastic mold. The metal insert used in this process can be a metal bar, screw part, or electrical wiring. With insert molding, you will only need to perform a single molding process to build this combination of metal and plastic parts with no additional steps.
Meanwhile, overmolding allows you to combine two different plastic parts in your injection molding operation. You will need to create the first plastic part in the primary mold. Then, you can put the second plastic part over the primary plastic mold. You can combine two different plastic material types with overmolding while ensuring that these plastic materials are compatible with each other.
A Single Mold vs. Two Molds
Insert molding only needs a single mold for you to perform it. The single mold in insert molding will contain the primary plastic mold / rapid tooling and the cavity for the metal insert. You need to add the metal insert part at the start of the molding process before pouring the primary mold with the molten plastic material of your choice.
In over-molding, you will use two different molds for the molding process. The first mold will be for the primary plastic part, and you will use the second plastic mold for the secondary or over-molded plastic part. You will need to perform the overmolding process in two or more steps.
Overmolding and Insert Molding: Single vs. Multiple Injection Molding Processes
With insert molding, you will only need a single injection molding step to perform this process. You simply insert the metal part into the mold before filling the primary plastic mold with the plastic molten material. Then, you will finish the insert molding process after the plastic material cools down and the metal insert gets integrated into the resulting plastic part.
In overmolding, you will need two different plastic molds and two or more injection molding steps to perform. The first molding step is to fill the primary plastic part mold with the molten plastic material of your choice and let it cool down. The second step involves filling the second plastic mold with another molten plastic. The overmolded part will cool down and become glued onto the primary plastic mold. As a result, this over-molding process will integrate the two plastic parts from the different molds as a unified product.
One Color Option vs. Multiple Colors
You can only use one plastic color with insert molding because you just need to add a metal insert into the primary plastic mold. So, there will be no room to add more colors to the plastic part you produce with insert molding. It’s just one metal insert and one-colored plastic material.
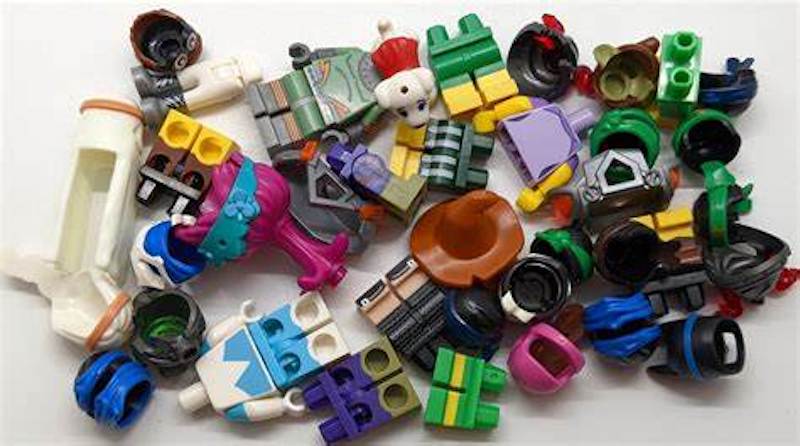
With over-molding, you can have the flexibility of adding multiple colors to the plastic part you produce because you are combining two different plastic material types. With these two plastic materials, you can choose different colors for each. So, overmolding will allow you to create different variations of your plastic parts by using multiple color combinations.
Faster vs. Slower Production Process
Insert molding offers a faster production process because of the single injection molding step. This simplicity of production can speed up your rapid manufacturing process. Also, you can produce large volumes of plastic parts much faster. Insert molding is also a suitable production method if you must finish your production plan within a tight deadline or production schedule.
Meanwhile, over-molding offers a slower production process when compared to insert molding because of its multiple injection molding steps. This production process can even get more complicated when you must deal with some issues during the two injection molding steps.
Overmolding and Insert Molding: Lower Costs vs. Bigger Expenses
Insert molding is more economical because you only need to create one mold for this manufacturing operation. Metal inserts typically can be reused/remold, so you don’t need to spend too much money on the plastic part production with insert molding. It’s one of the best methods for companies to cut costs on their production plan without lowering the quality of their resulting plastic parts, even for low volume manufacturing services.
In overmolding, you will need to spend more money on the production operation because of the need to use two plastic molds. Building two different molds for the overmolding process can cost double the amount of money you use for insert molding. Also, you will need to use two plastic materials, which can double your material costs.
Straightforward Process vs. Risk of Material Incompatibility
In short, insert molding offers a straightforward injection molding process that doesn’t require any complicated steps. You can also add metal inserts in insert molding with the robotic arm to make the process even more uncomplicated and less labor-intensive. You can get the job done much quicker with insert molding, with fewer potential issues.
With overmolding, you must make sure that the two plastic materials are compatible with each other. There is a risk of material incompatibility that can cause various issues for the resulting plastic parts, such as debonding and damage.
Conclusion
Insert molding and over-molding have their strengths and weaknesses, and these molding processes will have usefulness in various applications. Manufacturers use both insert molding and over-molding for different production projects. Understand the differences between insert molding and overmolding when you plan your manufacturing project to utilize these manufacturing methods in the best way.
Besides from overmolding and insert molding, TEAM Rapid also offers rapid prototyping, CNC machining services, and die casting to meet your projects needs. Contact our team today to request a free quote now!