We are lured into a world of awe by the exquisite workmanship of machinery . We are wondering at the methods and deft artistry that allowed them to materialize. You are following a well-traveled route of curiosity. Die casting and sand casting are emerged as the leading methods in the fascinating field of metal casting. They are the basis for creating these amazing metal creations. Everyone has a unique set of qualities, benefits, and drawbacks. But what distinguishes them specifically? Let’s examine die casting and sand casting side by side, figuring out the circumstances that determine which is preferable.
Table of Contents
Chronicles of Castings
Let’s indulge in a metaphor where metal casting mirrors the art of baking. Within this metaphorical realm, die casting and sand casting are akin to two diverse baking recipes for forging metal components. Each demanding specific ingredients, apparatus, and methods to breathe life into the final product. However, akin to the culinary arts, the choice between these methodologies is influenced by the sought-after outcome. The resources at hand and the complexity are entailed in the crafting process.
The Virtuoso of Precision: Die Casting
Pressure die casting as leveraging an intricately designed, high-precision baking mold, adept at delivering complex forms with sleek surfaces and exacting tolerances. This method propels molten metal under formidable pressure into a steel mold or “die.” It is fashioned from two hardened tool steel halves. These dies can be exquisitely engineered to fabricate complex shapes with unparalleled precision and consistency.
Envision crafting a chocolate figure using a highly detailed mold that encapsulates every nuance, from the strands of hair to the gleam in the eyes. That’s the degree of detail attainable through die-casting with metal. However, this meticulous precision comes with a price tag. The design and upkeep of the dies entail significant expenses and time, positioning die casting as a more suitable fit for large-scale production where the initial costs are amortized over numerous parts.
Die casting is a preferred technique in realms like automotive, aerospace, and electronics. They are the requirements for accuracy, robustness, and volume production are paramount. The materials typically engaged in die casting include aluminum die casting, zinc die casting, and magnesium. Metals are known for their lower melting points, making them ideal for the rapid production of parts that demand strength, lightness, and resistance to corrosion.
The Craftsman Baker: Sand Casting
Conversely, sand casting resembles the process of artisanal bread baking, where molds are shaped from sand, enabling a blend of creativity and flexibility but with a more textured, rustic finish. This age-old technique entails packing sand around a model that mirrors the desired part’s shape. Once the model is extracted, it leaves a cavity in the sand that serves as the mold. The molten metal is poured into this void and left to solidify. After cooling, the sand mold is dismantled to unveil the cast part.
The allure of sand casting lies in its simplicity and adaptability. It can accommodate nearly any metal alloy and part size, ranging from diminutive components to colossal industrial parts. The creation of sand moulds is relatively straightforward and cost-effective, making a sand casting a feasible choice for both low and high-volume productions. Nonetheless, this flexibility comes at the cost of the finish and precision of the end product. Items manufactured through sand casting generally possess a coarser surface and might necessitate further machining or finishing treatments to meet specific dimensions and surface requirements.
Sand casting is extensively employed in the fabrication of hefty machinery components, automotive parts, and artistic sculptures, offering an unmatched mix of versatility and accessibility among casting techniques.
The Decision Crucible
Choosing between die casting and sand casting ultimately hinges on a balance of considerations: the intricacy and precision of the part, the volume of production, the properties of the material, and budget constraints. Die casting excels in situations where high precision, intricate shapes, and large volumes justify the initial investment in die creation. On the other hand, sand casting provides flexibility, lower upfront costs. The capability to cast sizable and complex parts, albeit with a less refined finish and lesser precision.
Who can benefit from either type of casting
Thriving with Die Casting
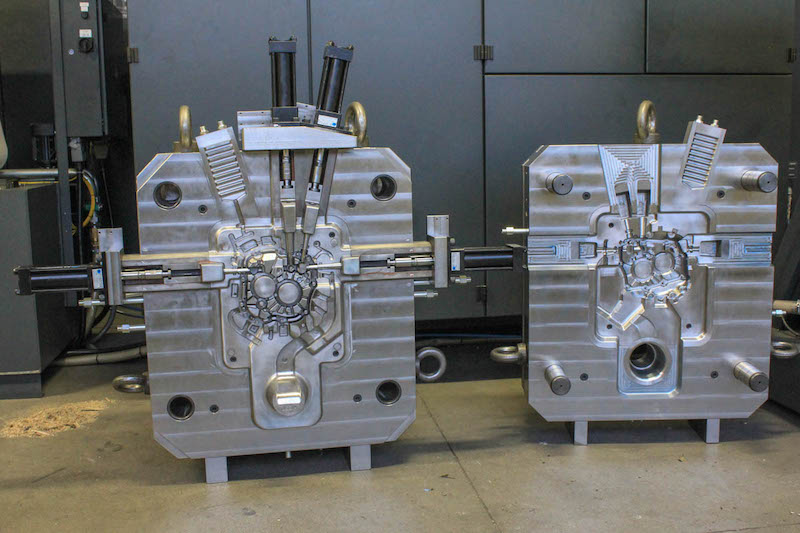
Automotive Visionaries
Imagine sleek, durable components making up the heart and soul of vehicles. From engine parts to door handles, the automotive sector can harness die casting for its high volume and precision needs.
Aerospace Architects
The sky’s the limit when aerospace designers utilize die casting for lightweight yet robust parts that meet the stringent requirements of air travel and space exploration, such as turbine blades or cockpit instruments.
Electronics Innovators
For the tech wizards creating the next generation of gadgets, die casting offers the precision needed for complex. It is miniaturized components like smartphone frames or camera housings.
Medical Equipment Makers
In the realm of health, precision and reliability are paramount. Die casting can provide medical device manufacturers with the high-quality, durable parts needed for life-saving equipment.
Home Appliance Pioneers
For those crafting the next wave of smart home devices, die casting can produce the intricate, reliable components that power our daily conveniences, from coffee machines to air purifiers.
Flourishing with Sand Casting
Industrial Giants: Companies in heavy machinery can benefit from sand casting’s ability to create large, sturdy components that keep our world moving, such as engine blocks or turbine casings.
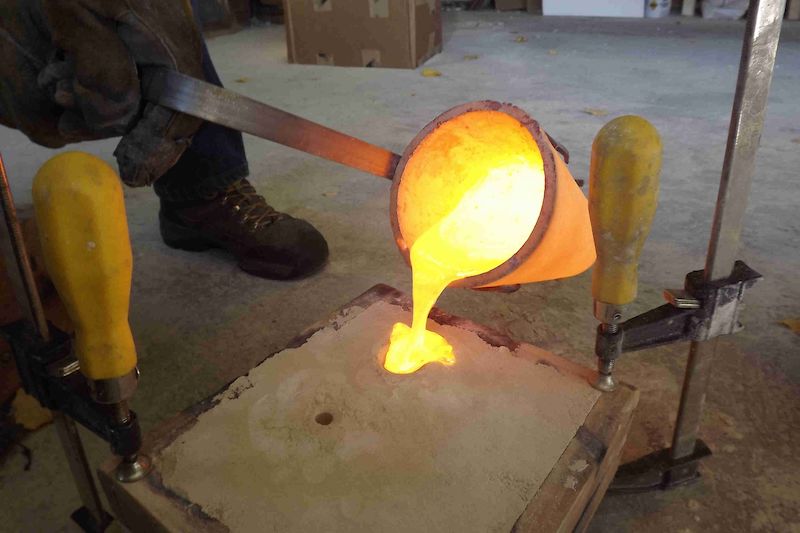
Architectural Artisans
For those sculpting the future skyline, sand casting can bring to life large architectural elements that blend strength with beauty, from decorative facades to robust supports.
Custom Automotive Crafters
Boutique car builders looking for unique, one-off components can turn to sand casting for its flexibility in producing distinct parts that add character to custom vehicles.
Maritime Engineers
The builders of ships and marine equipment can utilize sand casting for large, robust parts that withstand the harsh marine environment, such as propellers and anchors.
Renewable Energy Developers
For innovators in the renewable energy sector, sand casting offers a method to create substantial, durable components for wind turbines or hydroelectric plants, contributing to a sustainable future.
Artistic Sculptors
Creatives looking to cast their visions into tangible art can use sand casting for its adaptability and ability to handle unique, large-scale projects, bringing their monumental sculptures to life.
Our portfolio of services includes various die casting solutions like aluminum die casting and zinc die casting, CNC machining. Available at high-volume production levels. A concise case study below highlights what we can do. TEAM Rapid created a MUD-based mold for small metal parts for a U.S. company’s project in 14 days. The process, known for speed, design flexibility, and cost-effectiveness, allowed immediate mold trial approval by the visiting client. Production ensued, delivering 510 parts the next day. TEAM Rapid underscores its proficiency in quick, quality die casting solutions and are ready to offer competitive quotes at [email protected].
Conclusion
Within the expansive saga of creation and aesthetics, die casting and sand casting each carve out their distinct niches. They offer unique contributions to the birth of metal artefacts and sculptures. Also it drives our technology, enhance our spaces, and captivate our imagination. When you come across a piece of metalwork or a sculpture, take a moment to ponder the intricate dance of dynamics, substances, and creativity involved in its making, a testament to the fascinating methodologies of die casting and sand casting.