Within the manufacturing landscape, injection molding stands as a pivotal technique for the mass production of plastic parts. This intricate process, both captivating and complex, holds significant sway over multiple industries. Delving into its mechanics, particularly the elusive cycle time uncovers pathways to enhanced production efficiency and fiscal advantages. This exposition embarks on a comprehensive exploration of the enigmatic cycle time within the realm of injection molding.
Table of Contents
- 1 Mastering Injection Molding: Unveiling the Process and Cycle Time Dynamics
- 2 Unraveling the Dynamics: Cycle Time in Injection Molding
- 3 Unveiling the Choreography: Factors Shaping Injection Molding’s Cycle Time
- 4 Part Design And cycle time
- 5 Refining the Cadence: Enhancing Cycle Time in Injection Molding
- 6 Conclusion of injection molding cycle time
Mastering Injection Molding: Unveiling the Process and Cycle Time Dynamics
In the realm of manufacturing, injection molding reigns supreme as the go-to method for crafting parts on a grand scale. This captivating dance of creation involves injecting liquefied material into a mold, where it transforms from fluid to solid, birthing the desired component. This versatile technique finds its canvas in an array of materials, from metals to glasses, and even the beloved thermoplastic and thermosetting polymers. The journey of plastic molding unfolds through several distinct stages, each playing a crucial role in crafting perfection:
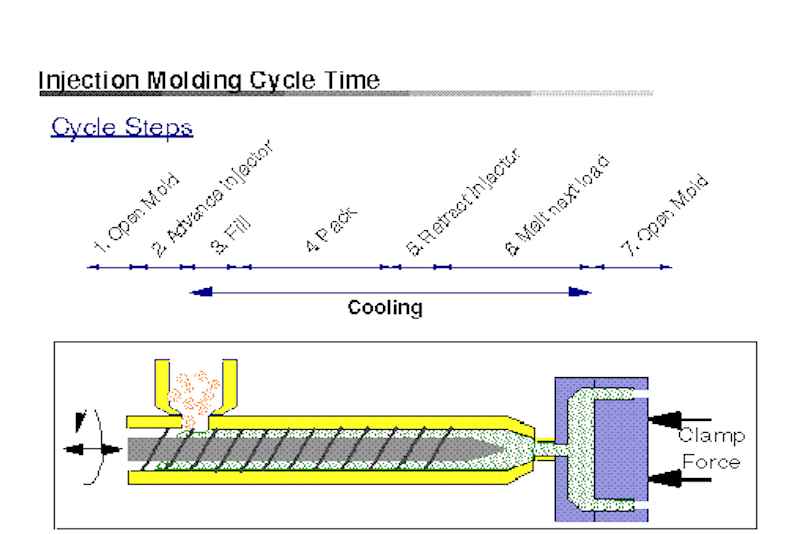
Clamping
The mold halves join hands, embracing the magic about to unfold.
Injection
Heat coerces the polymer into liquid surrender, and it eagerly fills the mold’s embrace.
Cooling
Patience takes form as the molten polymer morphs into its solid self, honoring the mold’s contours.
Ejection
The masterpiece emerges from its cocoon, ready to dazzle the world, often with finishing touches to enhance its allure.
In this intricate ballet, where every move matters, the cycle time emerges as the maestro, orchestrating the rhythm of efficiency. This enigmatic duration encapsulates the full swing of the injection molding pendulum – clamping, injecting, cooling, and finally, ejection. Efficiency hinges on the art of synchronizing these steps, and the cycle time’s heartbeat is the pulse of productivity. In essence, comprehending this cycle time symphony unlocks the door to injection molding’s mastery, where science, art, and precision unite in a harmonious production crescendo.
Unraveling the Dynamics: Cycle Time in Injection Molding
Cycle time in injection molding is akin to the heartbeat of the process. It encompasses the full span of a single journey through the molding routine. From the initial clasp of the mold’s embrace to the final closure before the next endeavor begins, it envelops the pivotal phases of injection, cooling, and ejection.
Fueling the Rhythm of Efficiency
Cycle time is the compass guiding the course of injection molding’s efficiency. It’s the timekeeper, the pacer, and the conductor all in one. A compressed cycle isn’t just a testament to speed; it’s the linchpin of production rates. With a shorter cycle time, parts multiply, productivity soars and the manufacturing arena hums with vibrant life.
The Dance of Quality and Pace
But, this journey isn’t just about racing against the clock. Quality waltzes in tandem with speed. Forging exquisite parts requires time for cooling, allowing the material to solidify perfectly. Rushing this delicate process could birth defects and imperfections, tarnishing the grace of the final creation.
Balancing the Budget by adjusting Cycle time
Cost efficiency also shares the stage with cycle. A swift cycle means less energy spent per part, nudging operational costs to a graceful low. The symphony of optimization plays out as manufacturer’s finesse the cycle time, seeking the sweet spot where quality, productivity, and budgetary harmony intersect.
Unveiling the Choreography: Factors Shaping Injection Molding’s Cycle Time
The grandeur of the rapid tooling and mold’s design holds sway over the tempo. Complexity might extend the cycle, granting time for intricate forms to solidify flawlessly.
Material Properties
Materials enter the stage with their unique traits. Swift solidification materials might bow to a quicker cycle time, while others, more leisurely, contribute their rhythm.
Molding Conditions
In this orchestra of creation, molding conditions take center stage. Injection speed, back pressure, and melt temperature become the conductors, orchestrating the harmony of speed and quality.
Machine Capabilities
The machine’s capabilities perform as supporting actors. The strength of its clasp, the force of injection—it all influences the cadence of completion.
Part Design And cycle time
Part design whispers its melody. Thin walls waltz to a quicker tune, their swift cooling reducing the cycle’s duration. Each factor plays its note, composing the symphony of cycle time. But this composition extends beyond the stage, impacting the broader production picture.
Balancing Efficiency and Output by adjusting cycle time
Imagine a scenario where a rapid-cooling material propels a swifter cycle. Yet, if haste leads to a surge in faulty pieces, efficiency falters. Likewise, an intricate mold design might extend the cycle, yet its intricate allure elevates the end product’s value. In this delicate dance, where speed, quality, and yield perform together, each factor plays a part. A material’s cool elegance, a mold’s elaborate embrace—they mold not only the part but also the process’s rhythm.
An Orchestra of Optimization
The symphony of cycle time reveals that it’s not just about speed. It’s about the interplay, the harmony between diverse elements. Mold, material, conditions—they step in unison to craft efficiency’s melody.
Refining the Cadence: Enhancing Cycle Time in Injection Molding
Optimizing cycle time in injection molding entails an amalgamation of calculated strategies:
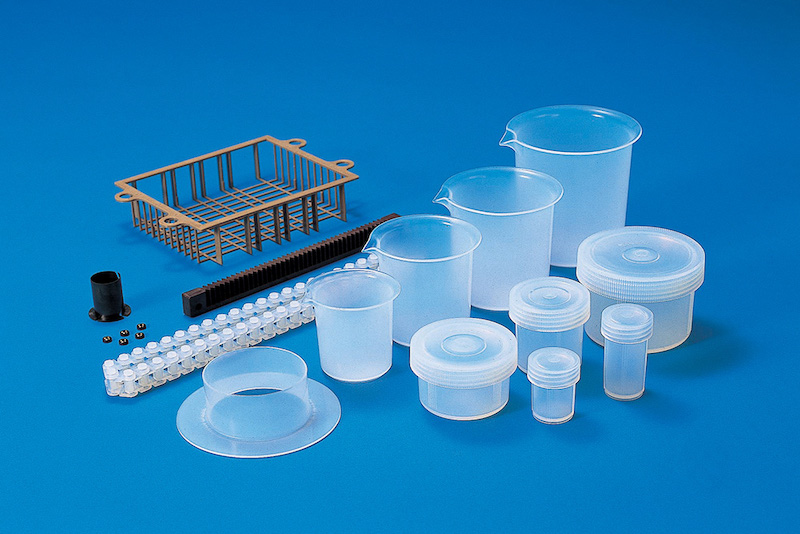
Material Selection
The choice of material carries substantial weight. Opting for materials with expedited cooling properties can orchestrate a swifter cycle. Nevertheless, this must harmonize with the material’s compatibility for the intended part application.
Process Parameter Optimization
A symphony of adjustments is at play. Fine-tuning molding conditions, encompassing injection speed, back pressure, and melt temperature, compose the melody of cycle time. Often, this symphony involves a meticulous process of trial and refinement to arrive at a harmonious tempo.
Machine Maintenance
Regular maintenance of the injection molding machine directs the ensemble’s consistency. Ensuring the machine operates at peak efficiency orchestrates seamless transitions within the cycle.
Leveraging Technology
The integration of advanced methodologies, such as computer-aided engineering (CAE), ushers in an era of innovation. This technology orchestrates intricate simulations, harmonizing the composition of potential time reduction.
Harvesting the Benefits
Optimizing cycle time echoes a well-coordinated symphony; its benefits resonate in multifaceted chords. The crescendo of productivity reverberates as more parts pirouette through time. Simultaneously, a harmonious note of cost-effectiveness is struck, curtailing energy consumption per part. However, the underlying axiom remains steadfast: the quality of the final piece must never waver.
A Harmonious Convergence
In this meticulously orchestrated symphony of optimization, no instrument plays in solitude. Mold design, mold flow analysis, material choice, parameter calibration, and technological integration—all contribute to the tempo of the cycle. The aspiration is a magnum opus—efficient, economically viable, yet unwavering in quality. The symphony of cycle time spins a tale where innovation and precision twirl hand in hand, ultimately crafting a virtuoso performance.
Conclusion of injection molding cycle time
In drawing the final curtain on this discourse, a mosaic of strategies and factors comes into view, all converging on the pivotal theme of optimizing cycle time. From meticulous mold design to calculated material choices, every element partakes in the orchestration. Recognizing and fine-tuning this choreography isn’t just a technical endeavor; it’s a harmonious mastery that aligns productivity, efficiency, and quality in a resounding crescendo.
Besides from injection molding, TEAM Rapid also offers rapid prototyping, 3d printing services, and die casting to meet your projects needs. Contact our team today to request a free quote now!