An injection moulding process that uses silicone rubbers as the base materials, with diverse moulding techniques. Adding other material components is possible with silicone rubber injection molding. This process will use the basic and expanded moulding techniques based on the end products you want to make. Varying grades of silicone rubber materials are available.
Silicone Rubber Molding requires you to perform the tooling process at the start of production. There are also diverse injection moulding types of machinery available for the expanded Silicone Rubber Molding techniques.
Table of Contents
- 1 Knowing More about Silicone Rubber Injection Molding Advantages
- 1.1 Exceptional Resilience and Flexibility of Silicone Rubber Injection Molding
- 1.2 Resistance to High Temperature and Electrical Flows
- 1.3 Easier Tooling and Mold Creation by Silicone Rubber injection Molding
- 1.4 Cheaper Tooling Costs Compared to Other Materials
- 1.5 Different Applications with Different Mechanisms
- 2 List of Different Silicone Rubber Injection Molding Methods
- 3 Conclusion of Silicone Rubber Injection Molding
Knowing More about Silicone Rubber Injection Molding Advantages
Silicone Rubber injection Moulding offers many benefits, from its applications to production timelines. Medical and consumer electronic industries are the primary applications of Silicone Rubber Molding. Here are some advantages of silicone rubber moulding techniques:
Exceptional Resilience and Flexibility of Silicone Rubber Injection Molding
Silicone rubbers are resilient and flexible against physical forces. It has a high level of flexibility, allowing you to stretch it without breaking its material structure. Also, silicone rubber’s resilience makes it always return to its default form or shape after you apply any physical force to it.
Resistance to High Temperature and Electrical Flows
Silicone rubbers are best for insulating high temperatures and high-voltage electricity. Silicone rubber parts can operate in environments with high temperatures or high voltage, with applications for household appliances and consumer electronics. You can put your silicone rubber moulded parts or components in environments with high temperatures and high electrical flows with no issues.
Easier Tooling and Mold Creation by Silicone Rubber injection Molding
Silicone rubber plastic molding offers easier tooling and mould creation than other materials. The tooling process of silicone rubber moulding will also take a faster time due to its lighter and less intensive tooling materials. You can benefit from the easier tooling of silicone rubber moulding in terms of your production timeline and budget.
Cheaper Tooling Costs Compared to Other Materials
The tooling/ rapid tooling process is easy for silicone rubber moulding, and it is also more affordable. You can create the mould for the silicone rubber moulding with fewer tooling materials and fewer steps, meaning less money to spend on tooling. You can also perform the silicone rubber moulding process faster, getting you into the production process as soon as possible.
Different Applications with Different Mechanisms
The moulding of silicone rubber materials doesn’t use only a single Injection Molding method. It also uses various unique injection moulding techniques with different applications. It gives you flexibility in choosing the most suitable moulding method for your production. You can set up custom features, properties, and characteristics for the silicone rubber items you produce.
List of Different Silicone Rubber Injection Molding Methods
Processing silicone rubber materials using the injection moulding method requires various techniques based on your applications and project requirements. Different silicone rubber end products need distinct moulding methods to make. There are also diverse techniques to process liquid silicone rubbers and their more solid counterparts. Here’s the list of different silicone rubber moulding techniques:
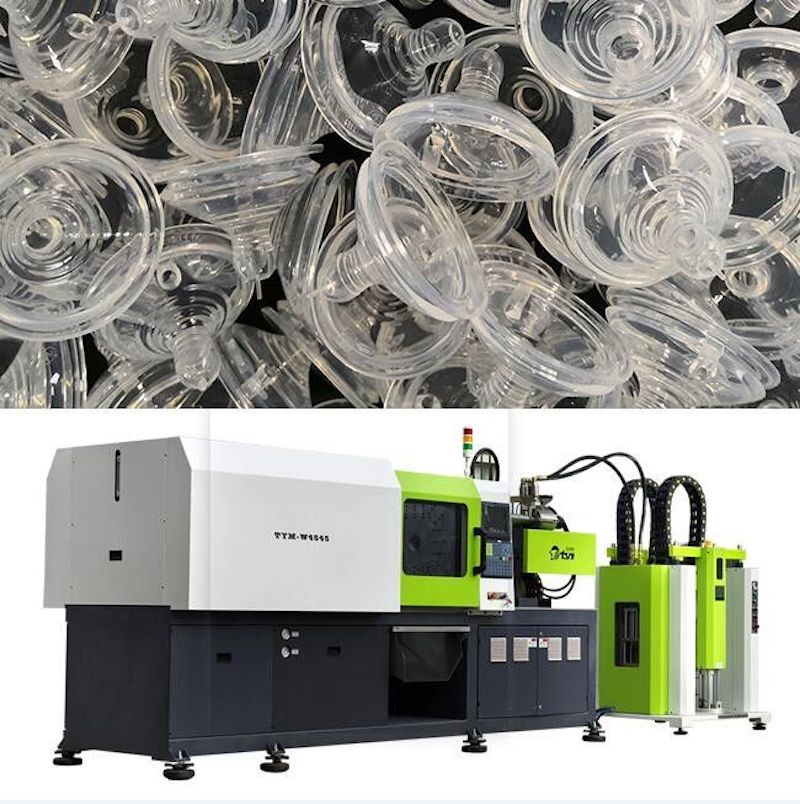
Compression Molding
Compression Molding uses a clasping mechanism to compress the silicone rubber material inside the uniquely shaped cavity. You can create various shapes for the silicone rubber materials with this Compression Molding technique. In this compression rubber molding technique, you will place the silicone rubber directly into the cavity before clasping the mould and applying pressure. You must maintain the pressure until the silicone rubbers assume the new form based on the cavity shape.
LSR Injection Molding
LSR (Liquid Silicone Rubber) moulding uses liquid silicone rubbers and injects them into mould cavities like the ordinary injection moulding system. However, LSR Injection Molding will always produce high-quality silicone rubber parts or items with high strength and resistance against high temperatures and electrical flows. With LSR Injection Molding, you will use the liquid version of silicone rubber materials, making it easy to control the flow and speed of the liquid materials during the moulding process.
HCR Injection Molding
HCR (High Consistency Rubber) Injection Molding can provide excellent mechanical stability for silicone rubber items or products. It uses the regular injection moulding system to create more solid or consistent silicone rubber products. You can combine silicone rubber materials with metals or plastics for the HCR Injection Molding to improve the solidity of the end products. Silicone rubber enclosures and insulators are the ordinary applications of HCR Injection Molding.
Calendering
Calendering uses the double roll mechanism to create continuous silicone sheet shapes. The uninterrupted use of the rolling machine in calendering allows you to spike up your production process. The rolling machine in the calendering process can also customize the end products you want, including its features and surface finishing. The calendering process allows you to mix the silicone rubber with other materials, such as glass and plastics.
Extrusion Molding
You can use the Extrusion Molding process to create silicone rubber-based products with long and cylindrical forms. There are various applications for this Extrusion Molding method, such as cables, hoses, and long-shape electrical insulators. For this method to succeed, it is imperative to use high-grade silicone rubbers with the right temperature and speed settings during extrusion moulding. With extrusion moulding for silicone rubbers, you can create multi-layered components with custom characteristics, such as tolerances, flexibility, and more.
Transfer Molding
Similar to the Compression Molding technique, Transfer Molding uses compression and pressure for the moulding process of silicone rubber materials. The difference is transfer moulding will transfer the compressed silicone rubbers into the Transfer Pot. Transfer moulding provides much better accuracy and precision for the silicone rubber items or parts you make.
Conclusion of Silicone Rubber Injection Molding
Silicone Rubber Molding offers diverse Injection Molding techniques to create unique silicone rubber items and parts in various industries. Each Silicone Rubber Molding technique has its mechanism for creating unique silicone rubber shapes with differing qualities, features, and characteristics. With these Silicone Rubber Molding techniques, you can create products with flat, solid, and long cylindrical shapes. Also, you can incorporate other material selections with some of these Silicone Rubber Molding techniques.
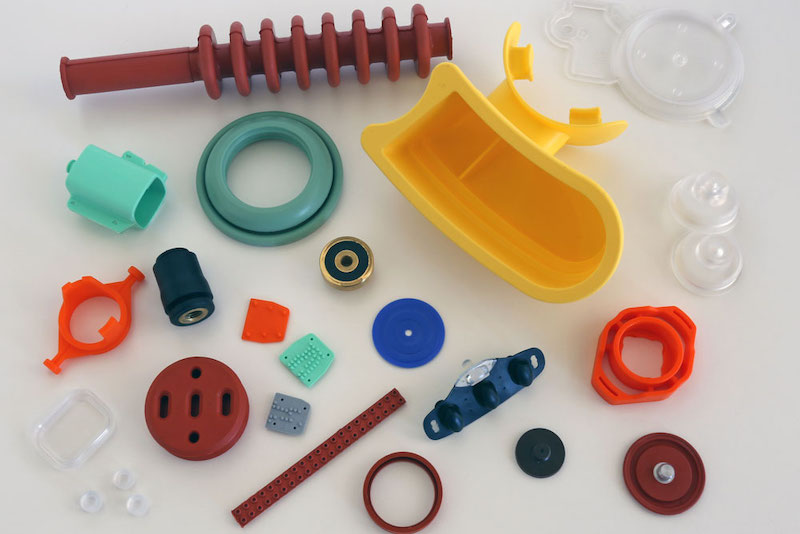
TEAM Rapid applies different molding techniques to meet your rapid prototyping, low volume manufacturing, and mass production needs. Contact us today to request a free quote now!