Sheet metal fabrication involves the conversion of thin steel or aluminum mills or buildings. This is achieved through various processes such as cutting, punching, folding, and stacking. The versatility of sheet metal allows it to be produced in almost any form, usually by cutting and heating techniques. Unique tools are used in the fabrication of sheet metal. Band saws and chop saws are commonly used to ensure consistent cuts. For cutting larger sections effortlessly, cutting torches is particularly effective.
The process is further simplified by using a press brake, which helps the steel bend with an even angle. There are different types of press brakes, each serving a specific function and purpose. Welding is an essential part of sheet metal fabrication. After forming the components, they are assembled and temporarily welded in place. Various techniques are applied to prevent distortion and other issues during welding. These include covering the metal with sand as it cools, employing specific straightening methods, welding in a staggered pattern, and using robust fixtures. Subsequently, the metallic is finished via sandblasting, priming, along with painting. This process not only complements its appearance but gets it ready for shipping out to clients.
Table of Contents
The Sheet Metal Fabrication Technique was Examined in-depth.
Sheet steel fabrication is a complicated process that starts with raw components like metal, aluminum, and copper, often in massive and thick states. The flexibility of sheet metal permits it to be manipulated into nearly any form using cutting, bending, and stretching.
Here is a more in-depth look at every sheet Metal Fabrication step of the procedure:
Design Phase
The design stage is the core of the project. Designers commonly make use of computer-aided design (CAD) software or from time to time, manual sketching to create preliminary 2D or 3D models of the intended item. This stage involves strong attention to the product’s supposed use, exact dimensions, tolerances, and specific musts concerning materials and finishes. The aim is to ensure the final product meets all functional and aesthetic criteria before moving to production.
Sheet metal Fabrication: Cutting Process
Typically, a laser cuts and starts the process. This method is known for its high accuracy, as the laser can precisely follow the planned cutting of the newspaper. Laser cutting provides a clean, precise cut, laying a solid foundation for the next step in the rapid manufacturing process.
Bending tactics
Typically, the bending stage using CNC machining (Computer Numerical Control) folding involves machines ranging from manual press brakes to automatic panel bending machines. These machines work by wrapping sheet metal and applying pressure to a curvature desired upon it, forming exact shapes according to the directions of the metal.
Sheet Metal Fabrication: Formation stage
Construction differs from cutting in that it reshapes the material without reducing its dimensions. At this point, the sheet metal is bent or deformed as necessary to ensure the product is accurate to the design specifications.
Welding Methods
Sheet metal fabrication makes use of various welding techniques, like MIG (metallic inert fuel) welding, TIG (tungsten inert fuel) welding, robotic MIG welding, and spot welding. MIG welding is a quicker choice appropriate for thicker substances, while TIG welding, also called gas tungsten arc welding (GTAW), gives extra control for thinner materials. Robotic MIG welding automates traditional MIG welding for efficiency, and spot welding uses an electrical resistance welding process.
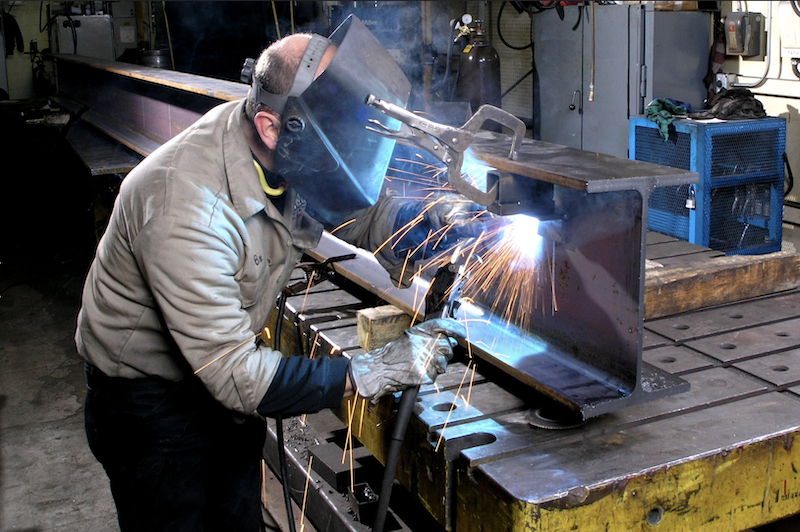
Sheet Meta Fabrication Finishing Touches
Finishing is vital in heightening the durability and aesthetics of metallic products. It consists of making the goods better able to fight against corrosion while at the same time giving them an aesthetically desirable appearance. Standard finishing techniques involve surface preparation, polishing, powder coating in various colours, anodizing, passivation, and laser marking for adding logos or text.
Assembly and Delivery
The final step in sheet metal fabrication is the assembly of the products. This involves putting together the fabricated components before they are packaged and shipped to their destination. This stage ensures that all parts are correctly assembled, meet quality standards, and are ready for use upon delivery.
Diverse Materials Used in Sheet Metal Fabrication
Various metals are used in wrought iron, each with unique properties that make them suitable for different construction needs. Here’s an extended look at some of the unique features:
Iron
Iron is a highly versatile material for sheet metal, known for its high strength and durability. It falls into four main categories, each with distinctive characteristics:
Carbon steel for Sheet Metal Fabrication
Carton steel recognized for its sturdiness and flexibility, it’s a good fit for a wide range of different applications. Alloy steels contribute diverse elements for enhanced strength, resistance to corrosion, or other distinct elements/properties.
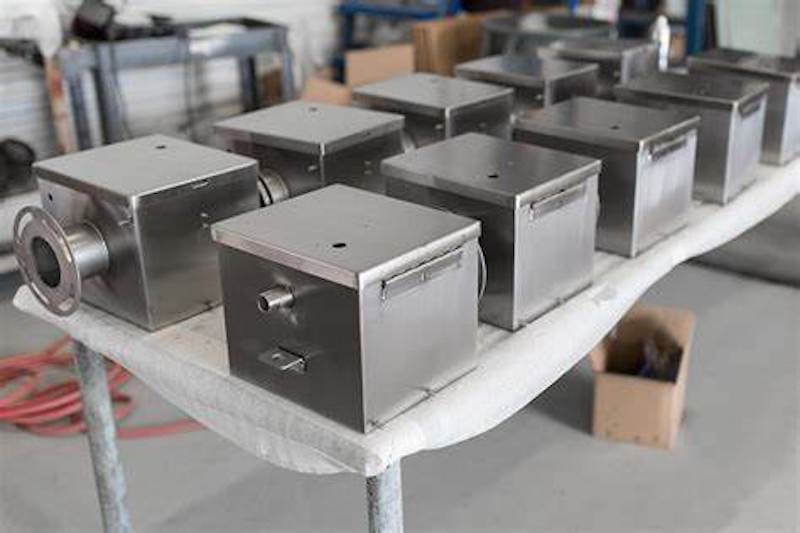
Stainless Steel
Stainless steel is often applied in places where rust and corrosion are an issue because it has a strong track record for being corrosion-resistant.
Tool metal for Sheet Metal fabrication
Tool metal acknowledged for its resilience and hardness, this material is regularly used to create tools.
Metal is the element of preference for many commercial and business purposes because of its softness, corrosion resistance, and ability to sustain tensile strain.
Alloys manufactured from aluminum
Aluminum is specific in that it is a sturdy material that isn’t heavy. Because of the lower level of density over steel, it is a feasible option for situations where lowering weight without sacrificing strength is essential. Aluminum is regularly utilized in the aerospace, automobile, and construction spaces and is specifically well-known for its corrosion resistance.
Magnesium for Sheet Metal fabrication
Magnesium is another lightweight metal characterized by its shiny appearance and strength. Its low density makes it ideal for applications that require structural stiffness without adding significant weight. Magnesium is often used in automotive and aerospace industries for components that benefit from weight savings.
Bronze
Bronze is a flexible metal that is frequently used in applications needing excellent corrosion resistance but less structural strength. It is distinguished by its very high ductility and lower melting point when compared to steel and aluminum. Its unusual qualities make it excellent for sculptures, bearings, and electrical connectors.
Copper
The best-known properties of copper, a soft and pliable metal, are its superior heat and electrical conductivity. It is often utilized in plumbing, architectural, and electrical components. Within the food processing and healthcare fields, copper is one of the primary choices of compounds. This is due to its antimicrobial solid elements.
Conclusion
To sum up, sheet metal fabrication is a complicated and multipronged process that turns metal into functional aesthetic systems or elements. Sheet metal is processed efficiently using various steps consisting of making plans, cutting, bending, forming, welding, completing, and assembly metal, aluminum, magnesium, and copper. When different metals, such as copper, are used, each has unique properties, allowing for a wide range of construction projects. These materials are chosen to ensure that the finished product not only fulfils its intended function but also maintains quality and durability. These choices include strength, weight, corrosion resistance, and permeability. The combination of sophisticated techniques, specialized equipment, and industry experts in metal framework highlights the importance and quality of the materials in a variety of industries, including construction and aerospace, and its impact on modernity, emphasizing the development of the world.
Besides from sheet metal fabrication, TEAM Rapid also offers rapid prototyping, CNC machining, injection moulding, and die casting for your needs. Contact us today!