Injection molding a useful production method which enable manufacturers to produce identical parts with consistent quality and characteristics in high volume. In injection molding process, a pressurized nozzle shoots molten plastic into a metal mold to make the parts cool and be ejected quickly. When the parts are ejected, the press closes and the operation repeats. There are many plastic products in our daily life like bottles caps, cart parts and gears are produced by injection molding. In the past, injection molded parts needed to be produced in high volume to cover the high setup costs. It will cost even ten of thousand of dollar and weeks to months to build a hardened steel mold. Injection molds are durable which allow manufacturer to recoup their investment and also lower the cost per unit. As market evolve, small batch products are increasingly needed. More and more plastic businesses are looking at low-volume injection molding. Customer expectations are going for lower volume which allows business to develop new products and markets with less risk. Manufacturers adapted their operation to take advantages of new methods. Low volume injection molding is one of those methods. Low volume injection molding is a priority for plastic businesses in small or medium production.
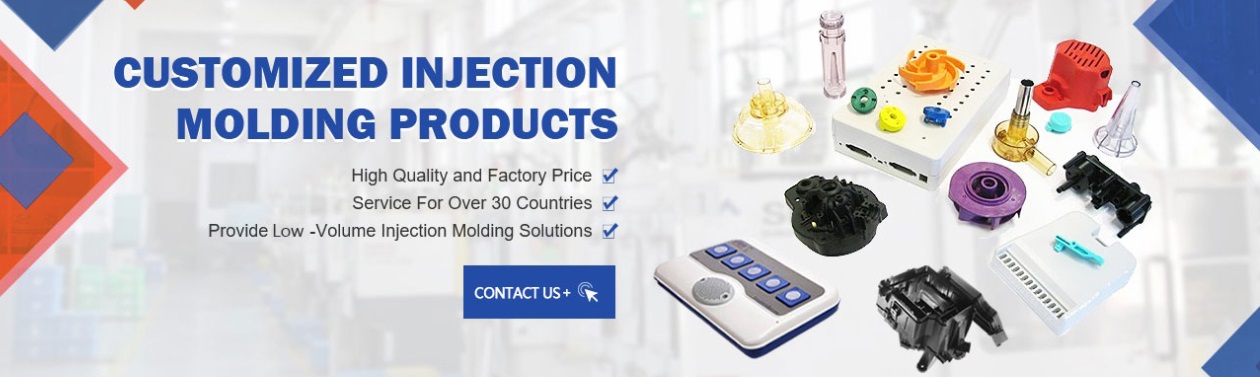
Table of Contents
Why Low Volume Molding?
Plastic parts manufacturing is a fast-paced business but plastic parts production is not a quick process. Plastic parts manufacturing is a complex process to start with. Depending on the plastic parts design, every design needs a customized injection mold to get right tolerance, finish and functionality. It also takes time to build injection molds. Some low volume plastic parts manufacturing manufacturers order the plastic molds from other mold shops to save expenses. Low volume injection molding is a perfect method to solve the problems that low volume plastic manufacturing companies face. Low volume injection molding shortens the lead time to achieve fast production. Low volume injection molding is a cost-effective method, it is perfect for companies that have limited budget.
What is Injection Molding Process?
Like regular plastic production, low volume injection molding process needs a 2D or 3D design and use wire cutting and polishing to create the molds. Traditional plastic manufacturing use aluminum or low grate steel to make molds which cannot withstand hundreds of thousand times of injection press. This is fast and cheaper. Injection molding molds made out of aluminum and hardened steels can withstand 10,000 to 100,000 molding cycles that is enough for low volume injection molding. The manufacturing process is shortened as steel does not to be hardened. Soft steel is better to be work with compared to hardened steel which makes the whole process easier and faster. Low volume injection molding is a cost-effective method.
What are the advantages of low volume Manufacturing?
The main advantage of low volume injection molding is the low cost. Hardened steel production mold is a high investment and small and medium business may not able to adapt to the fast-paced environment if they are in limited budget. Low volume injection molding is flexible and allow them to work around their finances. Another advantage of low volume injection molding is the short lead time that leads to faster production. Low volume injection molding takes around 3-4 weeks for manufacturers to get ready. This allows manufacturers to launch their new products to the market faster and get some returns immediately from their business investment.
What are the disadvantages of this Molding?
The main disadvantage of low volume plastic injection molding is that is it not a method for large mass production quantities. It is for suitable for companies which produce thousands of parts at a quick rate. Low volume injection molding accustomed for small to medium businesses.
Low Volume Molding Services at TEAM Rapid
Contact us today to discover more about low-volume injection molding.