Building prototypes from sheet metal materials has never been an easy task. It involves the meticulous manufacturing process, which includes designing, forming, and finishing. Thankfully, the computerization and automation aspects of sheet metal prototype manufacturing help keep this production process simpler and more streamlined.
Table of Contents
The Sheet Metal Prototype Manufacturing – How It Works
Building a working prototype with sheet metal fabrication requires long and often complicated rapid manufacturing processes. From the design to the finishing phase, you can bring your prototyping project to life with sheet metal manufacturing. Customizing your project requirements is always possible. Here’s the processing of sheet metal prototyping in manufacturing:
CAD design preparation
You can’t work on the sheet metals without creating a blueprint design for the component you want to build. Preparing the CAD design for the final product will be an essential part of the prototyping process. Most CAD software will allow the creation of a blueprint design for the sheet metal components with utmost dimensional precision.
Material assessment in sheet Metal prototype Manufacturing
Assessing the use of metal sheet materials is also essential to the success of your prototyping process. Choosing the proper materials for each component design will help build a durable prototype that can withstand regular damage. You can also assess which materials are the most suitable for creating the final product by checking their characteristics.
Cut the sheet metals into shapes
You must cut the sheet metal materials into different shapes before you can work on them. Sheet metal cutting is the next step you must go through during the prototyping process. The cuts will follow the dimensional measurements as presented in the blueprint.
Sheet metal forming
The forming process of sheet metals will come after cutting. You can form the sheet metal materials into different shapes. This process will follow your design requirements. The primary rapid prototyping operation will happen during the forming process.
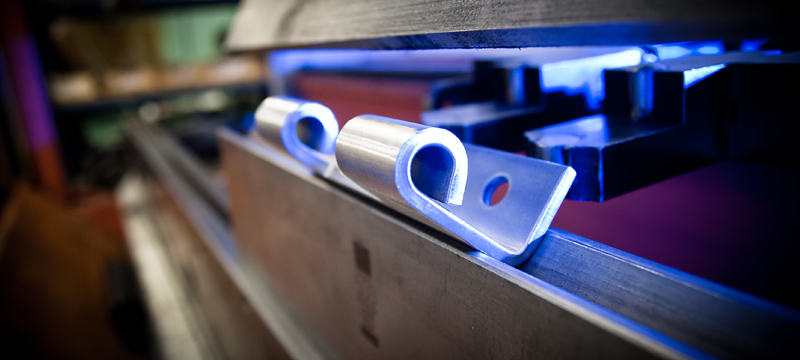
The joining process
You must follow the joining process after forming the sheet metals into various shapes. You can complete your prototype by joining the sheet metal components using rivets or other fasteners. The joining process will also serve as a pre-requisite to the assembly process.
Finish
You must polish the sheet metal parts before using them as prototypes. You can go through various steps to create the best surface polish for the sheet metal parts. The primary goal is to ensure that the sheet metal parts are ready to use as prototypes.
With these processes, you can build sheet metal prototypes with various features and characteristics that follow your requirements. You can apply these processes for both commercial and non-commercial projects.
Sheet Metal Prototype Manufacturing Techniques
From automotive components to medical tools, sheet metal prototyping is an essential production process many industries rely on. Learn about the various techniques in sheet metal prototyping:
Laser and plasma cutting
The cutting process for metal sheets involves laser, plasma, and other cutting techniques. Laser is a valid cutting medium for sheet metals, which can provide highly defined and precise cuts. Plasma, on the other hand, uses a combination of high-temperature plasma flow and electricity.
Shearing
Shearing is a cutting process of sheet metals that uses specialized shearing machinery with up-and-down cutting blades. The goal is to create precision cuts for the sheet metals. You can use shearing for different sheet metal material types with various thicknesses.
Sheet Metal prototype manufacturing: Punching process
Punching is the sheet metal technique to create various holes around the sheet metal materials. The hole sizes will vary depending on the design you apply for the sheet metals. You can use the punching process to create rivet holes to join different sheet metals.
Bending process
Bending is the primary technique in sheet metal forming, allowing you to create different shapes to follow the blueprint design. You can create various curvatures and angles for the sheet metal materials. Bending can accommodate complex geometries to get the best prototype result that follows your production needs. The process is commonly used in many production from automobile cover to metal badges.
Welding
Welding involves joining sheet metals with other metal objects using a high-temperature application. You will apply a laser-focused, high-temperature gas to melt the surface level of the sheet metals. Then, you will allow the applied surface to cool down and solidify, creating a powerful bonding around that area.
Deep drawing
It is a forming process that involves drawing the blank of sheet metal materials and punching them exceeding the material’s diameter. It can result in forming various shapes for the sheet metals. It uses steel dies to roll the sheet metal blanks before applying the deep drawing process.
Curling
Curling involves removing the sharp edges of the sheet metal materials for better safety and assembly. This process will make the sheet metal components look more polished at the end of production. It uses steel-based curling dies to perform this forming operation.
Ironing process
You can apply the ironing process throughout certain areas to prevent inharmonious dimensional thickness throughout the sheet metal components. This process helps keep a uniform thickness throughout the sheet metal parts to avoid any mismatch during assembly. You can apply this ironing process after the other forming processes on the sheet metal.
These are the commonplace techniques in sheet metal prototyping that you must use to build various prototypes across different industries.
Common Challenges in Sheet Metal Prototype Manufacturing
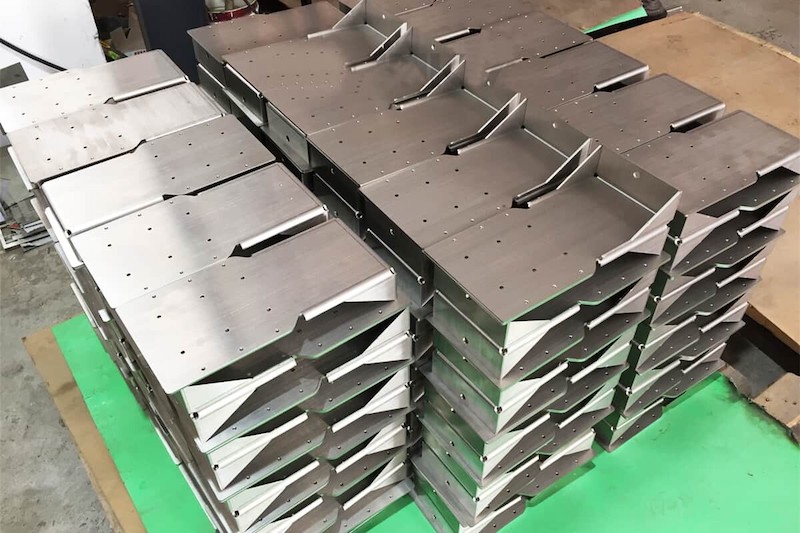
Slow configuration
The first-time configuration can be very slow because you must adjust various cutting and forming processes. The process can also be slower when you try to apply a new design for your prototype.
Expenses for trial and error
Creating prototypes for the first time can cost you a lot of money. The trial-and-error aspect can be expensive, depending on the complexity of your prototypes.
Inaccurate dimensional measurements in Sheet Metal Prototype Manufacturing
Inaccurate measurements can happen for your first-time sheet metal prototype, which can be daunting. It is often because of the lack of previous samples or measurements that you can follow. So, you have to start everything from scratch.
Conclusion of sheet metal prototype manufacturing
Sheet metal prototyping involves following various manufacturing steps, from designing to finishing. It also uses different forming techniques to get the shapes you need to build. You have to undergo a series of forming techniques to create the prototype as portrayed in the design blueprint. Contact TEAM Rapid at [email protected] for your sheet metal prototype manufacturing!