You can process silicone materials in different ways. First, through vacuum casting. And second, through silicone molding. Each method will bring different technical requirements, mold preparation, and restrictions. Vacuum casting vs. silicone molding, Understanding each of these production methods can help improve your overall result.
Table of Contents
- 1 Vacuum Casting vs. silicone molding – Manufacturing Process Differences
- 2 Vacuum Casting vs. silicone Molding – Production Volume Differences
- 3 Prototyping
- 4 Vacuum Casting vs. Silicone Molding – Tooling Process Differences
- 5 Product Modification
- 6 Vacuum Casting vs. Silicone molding: Limitations of Vacuum Casting
- 7 Vacuum Casting vs. Silicone molding: Silicone Molding Limitations
- 8 Conclusion of Vacuum Casting vs. Silicone Molding
Vacuum Casting vs. silicone molding – Manufacturing Process Differences
The difference in the rapid manufacturing process lies in how the plastic materials get processed during production. During vacuum casting, you will turn the materials into the final product within the vacuum chamber. Air bubbles within the liquid plastic materials might form during the casting process. It can affect the final product’s appearance. Eliminating these bubbles within the vacuum chamber is essential to avoid defects.
Meanwhile, silicone molding uses a high-pressure system to keep the liquid material flowing smoothly during production. Solidification will happen inside the mold cavity. Then, you can eject the final silicone product from there.
Vacuum Casting vs. silicone Molding – Production Volume Differences
You can create master model for vacuum casting with CNC machining or 3D printing. So, the production process can go very fast for vacuum casting. However, the quick production process doesn’t make vacuum casting qualify for high-volume production. At best, you can use it only for prototyping or small-batch production.
Meanwhile, silicone molding has a lengthier production process that qualifies it for large-scale production. The production process gets more refined with this procedure. It allows you to make high-quality items with consistency in their characteristics.
Prototyping
Rapid prototyping is essential in any manufacturing project. It allows you to perform trials and errors for the product samples. Proper prototyping improves the readiness of the product for market distribution. It also minimizes potential issues or defects. Vacuum casting is the best candidate for fast-paced prototyping. It can produce a rough version of the final product as a sample. The process is also fast and efficient.
Meanwhile, silicone molding is not suitable for prototyping. The meticulous production process makes silicone molding appropriate for final production. Also, the more expensive preparation costs will make silicone molding even more unsuitable for fast-paced prototyping.
Vacuum Casting vs. Silicone Molding – Tooling Process Differences
There’s also a difference in the tooling process between these two manufacturing methods. Tooling is much faster and cheaper with vacuum casting. However, it gives you only a rough version of the mold. It means the vacuum casting mold can break easily after a short-term production run. Vacuum casting gives you lower-quality tools.
Meanwhile, silicone molding has a slow tooling process with more meticulous preparation steps. The molds created for this process will be better in their overall quality. It can also withstand thousands of production cycles.
Product Modification
At some point during production, you might need to modify the product. It can be challenging to apply modifications to the final product. It will also involve changing the product’s mold in some capacity, which can be very complicated. However, product modification is still viable for these two manufacturing methods.
Vacuum casting is the easiest method to deal with product modifications. With its fast-paced tooling, modifying the mold will be a breeze. It will only take a few hours to apply any modifications to make the new mold and change the production outcome. Mold modifications will also be cheaper with vacuum casting.
As for silicone molding, the process of product modification will be more complex. It requires redoing the tool preparation from the start using the new design. It can also be an expensive endeavor to do. So, while possible, product modifications are not quick in silicone molding production.
Vacuum Casting vs. Silicone molding: Limitations of Vacuum Casting
Faster lead time doesn’t mean better for high-volume production. Vacuum casting has its restrictions you might need to consider. Please note these limitations of vacuum casting:
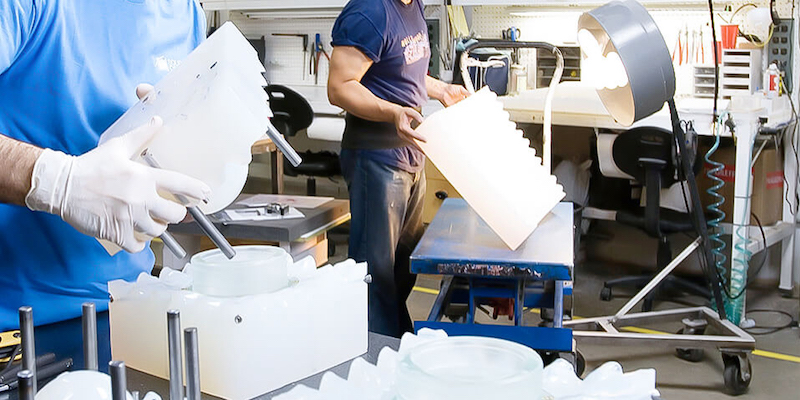
Best only for prototyping or low-volume production
You can’t rely on vacuum casting to produce items or products in high quantities. The faster and rougher process of vacuum casting only allows you to use it as a prototyping or low-production tool. Higher productions will require a more thorough manufacturing process to ensure better-quality results.
Material availability is limited
There are not many options you can have regarding materials for vacuum casting. Vacuum casting only works best for polyurethane-type resins as the primary material option. It will restrict you on the items or products you can manufacture with this process.
Rough surfaces
Another limitation of vacuum casting is that it produces items with rough surface finishes. It is not quite ideal for high-volume production. However, with this rough finishing, vacuum casting is advantageous for prototype building and testing them in small batches.
Despite its limitations, vacuum casting is perfect for rapid prototyping. It is not suitable for high-volume production. The resulting items produced with vacuum casting are only best for use as a rough draft to test the functionality of your products.
Vacuum Casting vs. Silicone molding: Silicone Molding Limitations
Flexibility and resilience are primary characteristics of silicone products. However, silicone molding has its restrictions. Learn about these silicone molding limitations:
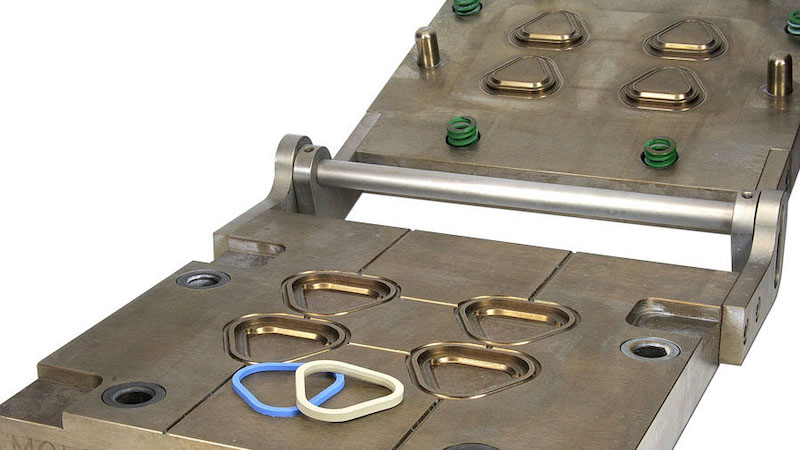
Slower Tooling process
You might risk slowing down your production with silicone mold tooling. It is because of the longer tool manufacturing time. The tool building time will be much slower than the vacuum-casting counterparts. Also, the tooling prep can make the production time much slower.
Inconsistent material quality
Silicone materials use different formulas that can affect their overall quality. These materials are prone to inconsistency in quality unless you use the ones from the same trusted supplier. Inconsistent silicone quality can produce final products with inconsistent quality, which can be bad for your business reputation.
Silicone molding might have these limitations, but this method is perfect for volume production. It also offers better polish for the final products such as rubber covers, sealer, and rubber keychains.
Conclusion of Vacuum Casting vs. Silicone Molding
Both silicone molding and vacuum casting have different purposes in manufacturing. Each method has its uses and limitations. To achieve the best result, you should use these two similar manufacturing production methods side-by-side. It is better than preferring one method over the other. Both vacuum casting and silicone molding are our main services, contact our team at [email protected] today to request a free quote now!