Vacuum casting uses a wide selection of resin-type materials made from plastics. You will melt the materials and send them into the vacuum chamber to shape the final product. However, each material will have its characteristics and properties that separate it from the others. It is essential to have the proper vacuum casting material selection for your project.
Table of Contents
Vacuum Casting Material Selection: What to Consider
Choosing a material for vacuum casting is not about randomly picking and using them. Each vacuum casting material has the characteristics that set them apart from the others. Here are the factors to consider:
Durability
Some factors contribute to the durability characteristics of vacuum casting materials. Tensile strength and impact resistance are among the most essential aspects. Choose the materials that can meet your quality standards regarding durability and strength.
Vacuum casting material selection: Processing
Varying materials offer different processing characteristics. Some materials are more effortless to process, which might affect the production time and cost. Easier-to-process materials can contribute to smoother production operations.
Performance
How will the material perform as a final product? It is something you have to consider as well. You can choose the materials that can perform best in their designated applications.
Finish
Different materials will offer varying finishing options for the final products. Some materials will give you a finer finish than others, which can result in the aesthetics of the final products. Creating high-quality products with the best aesthetics is often the best way to make a successful and marketable product.
Vacuum casting material selection: Compatibility
Not all materials will be compatible with the final product’s application. You will need to use specific vacuum casting materials for particular applications. It is essential to pick the material that has full compatibility with the intended usage application of the final product.
Affordability
Also, consider the cost factor of the material you use for vacuum casting. Each material type has specific grades or quality levels, making it more or less expensive. The affordability factor of the material will help give you the best consideration regarding the price-to-value of the end product.
Environmental usage
The final products manufactured with vacuum casting will have varying compatibility for their uses in specific environments. You must use specific materials to comply with particular usage scenarios for the final product. Each material will have different characteristics regarding how the material can work under particular environments.
Vacuum casting material selection: Regulatory
Some material types require the manufacturers to follow specific regulatory requirements before use. It is often for the benefit of the environment or any other factors. You must only use the materials that comply with the regulations. This way, you can manufacture your products with full responsibility.
These are the essential factors to consider before choosing the materials for vacuum casting. By following these guidelines, you can ensure the best result in your manufacturing process. Also, it can offer the best-use scenario for each production and rapid manufacturing application.
Material Types in Vacuum casting material selection
Vacuum casting uses resin-type materials that you can cast inside the vacuum chamber to shape the final products. This process uses only plastic-type resins with varying characteristics to accommodate your design requirements. Here are the available material types:
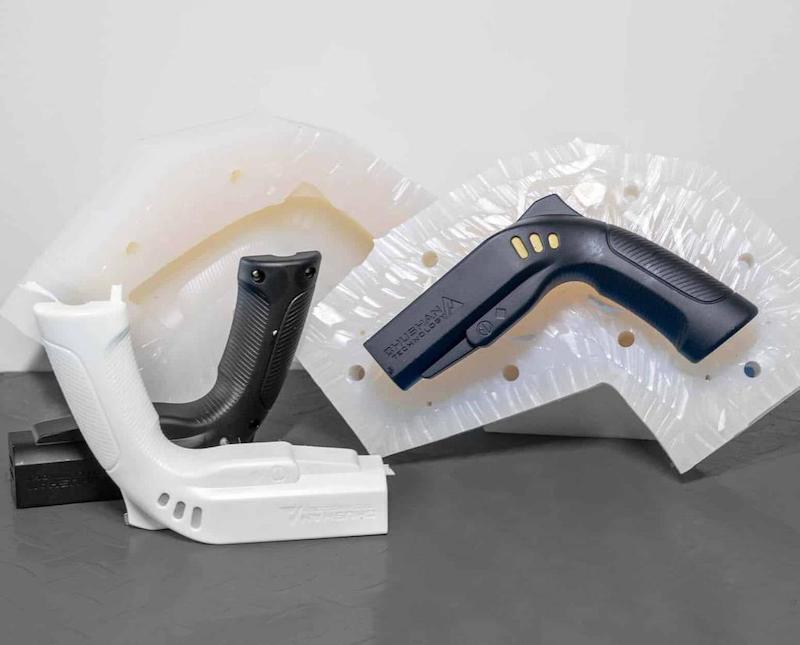
ABS
A durable material for vacuum casting, offering high impact resistance and thermal stability. The material has the best dimensional stability to keep a consistent shape when put under high-temperature environments. Also, it provides a surface finish that you can polish with flexibility to help increase its aesthetic value. The ABS material type ranges from PU8150 to UP4280, each with differing characteristics and designated applications.
PC
With the PC resin material, you can get several benefits. The benefits of this material include shape versatility, resistance to cracks, glass part replacement, and best thermal resistance. It also has a transparent form that offers high UV resistance and a high level of stiffness. The material ranges from PU8098 to PX23HT with differing properties and applications.
PP
This material offers the best properties to make gaskets, seals, and transparent components in various industries. The benefits of PP include minimum shrinkage, smooth-flowing performance during production, toughness, and flexibility. The low shrinkage feature helps this material to maintain its dimensional stability during high or low-temperature applications. It ranges from 8550 to UP5690, offering slightly different characteristics.
Vacuum casting material selection: Acrylic
The acrylic material offers two primary characteristics for your final products–transparency and durability. Other benefits of acrylic materials include aesthetics, versatility, and precision. In vacuum casting, you can use acrylic to build optical lenses, protective enclosures, decorations, and medical device parts. The material ranges from PX5210HT to X522HT, which offers differing properties and practical usage.
Soft rubbers
Next, the soft rubber materials allow you to make softer industrial components using vacuum casting. Also, this material is smooth-flowing during the vacuum casting application, making the production process faster and more controllable. It offers various benefits for your final products, including freedom in design, flexibility, transparency, and durability. The material has two primary types–UPX8400 and T0387, offering varied industrial applications.
Considering the correct material type in your vacuum casting production will help ensure the best output. Also, choose the material grade level suitable for your current budget or project goals. Each material gives the flexibility to select the varying quality levels you can use in your manufacturing operations.
Things to Avoid in Vacuum casting material selection
Choosing the proper materials for your vacuum casting project can help avoid any issues or pitfalls in manufacturing production. Avoid selecting materials that are not good for your vacuum casting project. Here are the things to avoid:
Material incompatibility
Not all plastic or resin materials will be compatible with vacuum casting production. Choose only the materials that meet the specific conditions of vacuum casting production. Also, ensure that the material will be suitable for the particular industrial application of the final product.
Vacuum casting material selection: Wall thickness inconsistency
The inconsistency of the wall thickness of the material can pose some issues when you use it for vacuum casting. Physical defects can happen during the vacuum casting operation, affecting the overall quality of the final product. Consistent wall thickness is essential to keep the final product’s dimension stable.
Poor flow
Some materials offer a smooth flow when you put them into the vacuum casting chamber. However, some others will have a poor flow. Choose plastic materials that have a smooth flow in the vacuum casting process. It can help ease the production and give you the best quality products.
Poor surface condition
The poor surface condition will affect the aesthetic look of the final product. It will also be more difficult to surface polishing. A defective surface condition will affect the overall value of your vacuum-casted products. It will even make the product unusable for subsequent production processes.
Vacuum casting material selection: Cost-to-value
How much does the material cost? Avoid buying vacuum casting materials that are too expensive for your budget. Also, avoid materials that offer a bad cost-to-value ratio. Find the best deals from reputable material suppliers to get the best value for your material purchase.
High-temperature curing
Please note that vacuum casting uses room-temperature curing in its operation. Materials that require high-temperature curing will not be compatible with vacuum casting. Ensure that the materials use room-temperature curing as the requirements before you pick them as your vacuum casting materials.
Consider the things to avoid before choosing the materials for your vacuum casting project. It can help filter the good from the bad. The proper materials will also give you the best result in your vacuum casting production.
Benefits of Choosing Proper Materials in Vacuum casting material selection
Vacuum casting requires specific materials to allow a smooth production operation. Why choose the proper materials for vacuum casting? Here are the benefits:
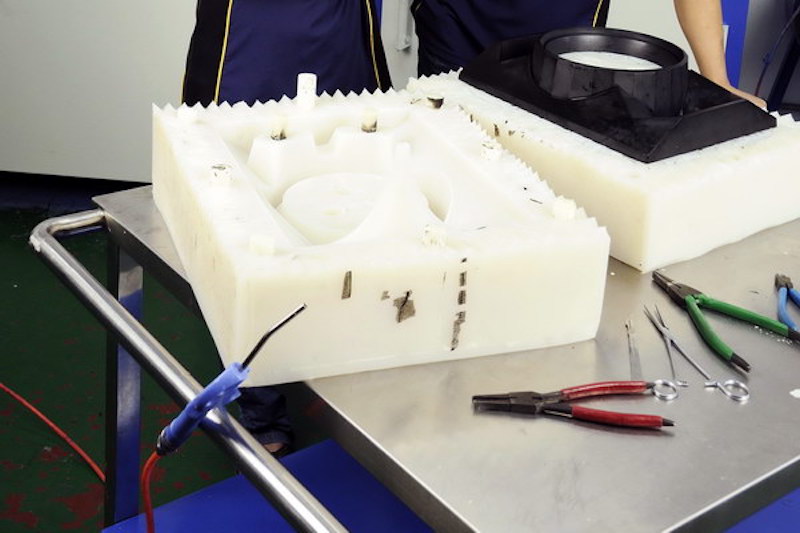
Better aesthetics
Selecting the correct materials for your vacuum casting project will give your final products the best aesthetics. You can polish your final products / ABS keychains even more effortlessly with suitable finishing options. The polished surface will show no defects, increasing the value of your vacuum-casted components.
Best performance for industrial applications
The proper materials will ensure the best performance when you use them in specific industrial applications. The final products you make will work best for the intended usage in various industries. It will also withstand daily wear and tear, and you can use it for the long term.
Faster production and cost-effectiveness
The correct materials for vacuum casting will ensure a smooth flow during manufacturing production. It will also contribute to the quicker production time. The proper materials will also be cost-effective and produce the best results in your manufacturing operation.
Ensuring the best quality and proper material usage for your vacuum casting operation will give you the best result in your production run. It will also provide the best overall performance for the industrial application of the vacuum-casted components.
Conclusion
Choosing the best materials for the process is essential to make a successful product with vacuum casting. Each material will have specific characteristics suitable for your current project goals. You must evaluate the project requirements before selecting the materials for your vacuum casting operation. Weigh the pros and cons of the materials before deciding to use them in your manufacturing project. Contact TEAM Rapid at [email protected] today for your upcoming projects now.