Today’s production demands require you to be selective in choosing the rapid manufacturing process for your projects. Some projects require you to produce plastic-based components or products for various industries, urethane casting vs. injection molding, the equipment and production differences .
Table of Contents
Urethane Casting
Urethane casting equipment holds the essential components to produce cast products in small quantities. However, it can handle a faster tooling process.
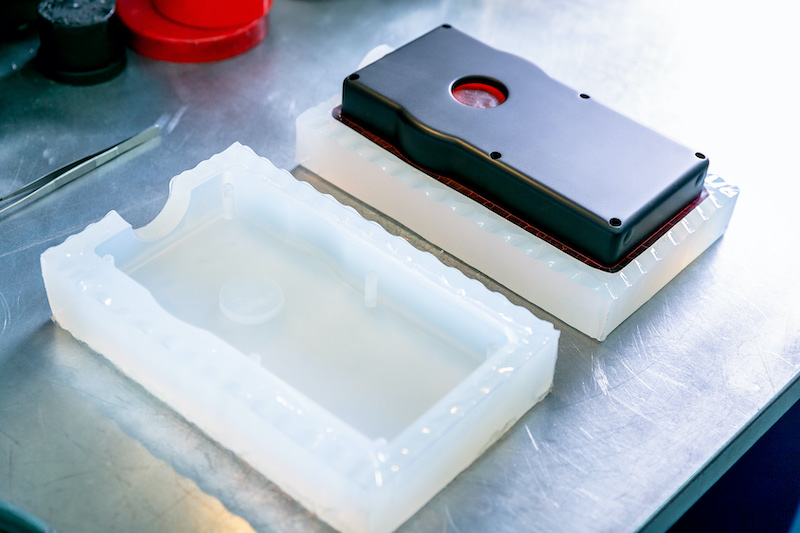
Urethane casting vs. injection molding: Equipment of urethane casting
Urethane casting uses the equipment containing the molds and vacuum chamber as the primary parts. It is a manufacturing process more suitable for short-term production or prototyping. Here are the parts of the urethane casting equipment:
Vacuum chamber
It is the place where the primary urethane casting operation happens. The solidification process of the casted plastic materials will occur in this chamber. The plastic materials will follow the mold design inside the vacuum chamber and turn into the complete product.
Pump
The pumping system in urethane casting will help move the liquid plastics into the designated mold. The casting process won’t work smoothly without it. The pump will ensure all liquid materials go into the vacuum chamber for further processing.
Mixing system
With urethane casting, mixing plastic resins is common. The mixing system contains containers and measuring tools to help combine suitable plastic materials. You must find compatible resins to use in the urethane casting for the best quality result.
Urethane casting vs. injection molding: Mold Insert system
The urethane casting equipment contains the mold inserts mechanism if needed to make it easier to remove the completed product from the mold. This system also helps prevent the casted product from sticking around the mold. It has a special agent to remove the casted product without issues.
PPE
PPE or Personal Protection Equipment is the special equipment for the urethane casting operator to ensure their protection. The operator must use PPE for the best safety during the urethane casting operation. Without this protective equipment, urethane casting might pose a safety risk for the operator.
Heating system
Urethane casting works at a specific high temperature, which makes the heating system an essential part of this process. The equipment has a heating system that will also function as the curing tool for the casted product. It helps make the casted product much more polished with better physical characteristics.
Workbench
The function of the workbench is to support the urethane casting equipment. It helps stabilize the equipment during operation. It also provides the flat surface required to deliver the casted products with no issue.
Clamps
Urethane casting requires the use of molds during its operation. Clamps are the tapes or fixture that will hold the molds in place. It will provide secure support for each mold during the casting process.
These are the parts of the urethane casting equipment. These parts ensure that the casting process will go smoothly. Any problem occurring on these parts will affect the casted products you produce.
Urethane casting vs. injection molding: Casted Products
What product types can you expect from urethane casting?
Prototypes
With the fast-paced preparation, you can use urethane casting to create rapid prototyping for various industrial applications. Urethane casting can produce prototypes with the same shapes and dimensional measurements as the final product. However, there are limitations to the prototype’s features.
Small-batch products
Urethane casting is only suitable for small-batch production runs. The reason is that the mold can’t physically retain the large-batch production without breaking. So, you can only maintain limited quantities for the urethane casting products.
Injection Molding
The equipment in injection molding will affect the end product you can make from it. Also, it will affect the prep time.
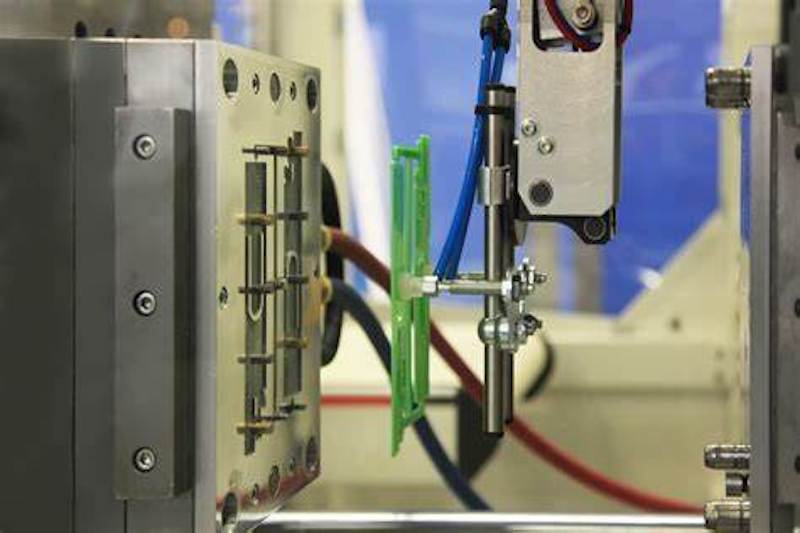
Urethane casting vs. injection molding: Equipment of Injection Molding
Injection molding requires a complex preparation and equipment to operate. This process is suitable for high-volume productions. Here are the parts of the injection molding equipment:
Mold
The primary shaper for the end product. You will send the liquid materials into the mold and solidify it to follow the design blueprint. The mold comes in different shapes and sizes. It depends on your project requirements.
Clamping
It is a support system for the molds you install on the plastic molding equipment. You must apply the proper clamping force to keep the mold secure in its place. The clamping force must not be too tight or too loose. A wrong clamping force setting can destabilize the mold placement.
Ejector system
It helps you to eject the molded product from its mold. A high-quality ejector will help maintain the accurate shape of the molded product without damaging it during the removal process. It is an essential mechanism in the finishing process of injection molding.
Configuration tool
Injection molding is a complex manufacturing process that requires computerized configurations to work smoothly. The configuration tool provides a control center where you can configure various aspects of the injection molding process. You can configure the temperature, pressure, cooling down time, and many other settings.
Injection unit
It is the part that will handle the injection molding process, including the mechanism to move the liquid materials into the mold. It connects directly to the mold. The nozzle will inject liquid materials into the mold cavity.
Unit base
The unit base provides a flat, durable surface that allows the injection molding equipment to work well throughout the production cycle. It provides the support that the whole equipment needs.
Each production cycle will require equipment cleaning and maintenance. An expert in injection molding will need to ensure that all components are in their best condition before starting a new production cycle.
Molded Products – Urethane casting vs. injection molding
What products can you expect from injection molding?
Medium and Large-scale production
Injection molding has more durable molds capable of handling medium & large-scale production runs. So, this method is not suitable for just prototyping. With injection molding, you can produce various plastic-based products such as daily necessaries, precision parts, or custom made keychains in large quantities.
End products
You can use injection molding to produce final products for the end users. You can also use this method to make industrial components for further assembly processes. It allows for complex geometrical shapes.
Conclusion of Urethane casting vs. injection molding
Urethane casting has a similar production method to injection molding, as they both use molds. However, the technical aspects of these production methods differ in their processing, equipment, and final products. Urethane casting will be best for short-term production, whereas injection molding is an excellent long-term production method.
Both urethane casting and injection molding are our main services, TEAM Rapid is a leading manufacturer in China, we help lots of customers to make their prototypes and volume parts successfully. want to have engineering supports from us? Contact our team at [email protected] today to request a free quote.