Among the various welding methods available today, ultrasonic welding is perhaps the most advanced type of welding technique you can use in various manufacturing processes. The ultrasonic vibration applied in the welding process allows you to weld thermoplastic and metal materials while minimizing the potential damage on the surface area.
The traditional welding method uses electric sparks to weld different materials together, and the process can be slow and quite dangerous if you are not wearing a welding helmet and other protection. However, with ultrasonic welding, the welding process can get so much easier to do. The process uses ultrasonic vibration that allows you to perform a fast and safe welding process with the best result you can get. In this guide, you will learn about what ultrasonic welding is, how it works, its applications, and its benefits.
Table of Contents
How Ultrasonic Welding Works
It uses ultrasonic vibration to apply the weld for two different materials, such as thermoplastics and metals. First, you will need to prepare the two materials you want to weld on the fixture for the welding equipment. Then, you will need to place the horn of the equipment at the place you would like to weld. Next, you will need to apply electric pressure to the horn, so that the horn can produce the ultrasonic vibration needed to weld the two materials.
After enough electric pressure, the ultrasonic vibration will get applied in the designated area. Once the weld gets applied, you will need to wait for some time to cool down the welded area and to fix the weld joint on the two materials. Next, you can remove the horn from the welded area and place it in another area you would like to weld. This process will continue until you apply all welds in the designated areas.
Ultrasonic Welding Applications
There’s a wide range of applications for this welding. With the welding quality, it can provide and the fast application of this method, you can find various products that use ultrasonic welding in their manufacturing process. From producing the smallest components in consumer electronics to the biggest components in the aerospace industry, you can find many uses of ultrasonic welding in various applications.
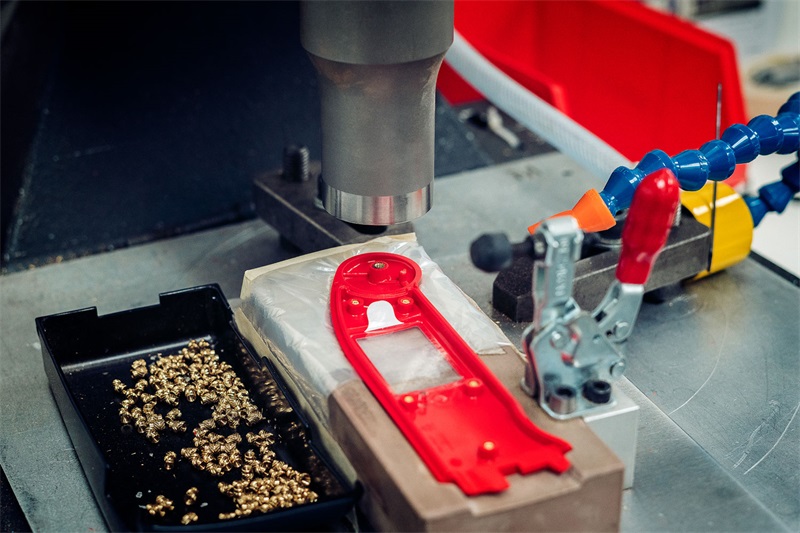
●Consumer electronics by ultrasonic welding.
In most consumer electronic products, you will often find components that need to have small, precise, and delicate connections with other components. You will need a special welding method to join them, which is the reason manufacturers will use ultrasonic welding to join these CNC turning components together. This welding method will prevent you from damaging the complex circuit boards in most consumer electronic products.
●Automotive.
Manufacturers often use this welding to join the parts in cars and other vehicles for bigger hardware parts. These plastic injection molding service parts include door instrument panels, vehicle engines, vehicle computer systems, and many others.
●Aerospace.
A reliable welding method is also useful for building various parts and components in the aerospace industry. Aircraft production uses various metals that require strong joints to work best, and ultrasonic welding is the best method to create such strong joints in the aircraft production process. It can create strong and tidy joints in various aircraft CNC milling services parts and components.
●Everyday consumer products by Ultrasonic welding.
Toys and household equipment often use the ultrasonic welding technique to weld various parts and components inside them. This is the preferred welding method used to join delicate and small parts in various toys and everyday household rapid sheet metal tools you are using.
●Medical.
It is also safe to build various medical tools, as they will not give any dangerous effects. Medical equipment and small insert molding tools, such as pipettes and filters, use ultrasonic welding to assemble their parts. The medical industry uses this welding method on a large scale to help medical professionals treat their patients in the best way.
The Benefits of Ultrasonic Welding
Ultrasonic welding is an advanced version of the traditional welding method, allowing you to get much better results in your welding activities. When you weld different metals using the ultrasonic welding method, you can do it without waiting too long for the curing process. The welding is instantaneous, and you can get your results right away. Here are the benefits:
●Fast welding process.
With ultrasonic welding, you can speed up your production, as this method allows you to get the welding process done fast. You don’t need to wait for the curing process to be ready before you can use it. You can use the welding process in an instant, with no hassles.
●Best joint quality.
The result of this welding process is quite impressive. With this welding process, you can get the best joint quality, no matter what materials you are using. Each joint will produce the best form and shape on the material surface, leaving little or no mistakes in the resulting joint.
●Reliable and flexible process.
The equipment for welding can give you reliable results, which means you don’t need to worry that the equipment will make some mistakes and ruin all the joining operations. It also has the flexibility that allows you to apply this welding process to various types of parts and materials.
●Safe to use.
The sparks generated from the traditional welding process might hurt you somehow, if you are not careful. However, with ultrasonic welding, you don’t need to worry about it, as this process doesn’t pose any danger to use.
●Lower cost of the material.
You don’t need to include some additional materials when you use this welding method. Thus, it can help lower your costs of material preparation. Also, you can perform this welding process with minimal labor, meaning you can keep your hiring costs at a minimum.
Conclusion
When compared to the traditional welding method, ultrasonic welding offers a more refined welding technique that allows you to get the best quality welds for various materials, including thermoplastics and metals, rapid prototyping services, and mass production. It can also provide plenty of benefits for the manufacturers, although the initial costs of buying the welding equipment might be high.
This advanced welding technique also has many applications in various industries, which makes it even more preferable for manufacturers to use this welding technique in the different production processes they have today. Are you looking for a manufacturer who can help with welding and other rapid manufacturing needs? Contact us today to request a free quote now!