The manufacturing industry is developing faster and faster, and injection molding technology is also “raging” along the way. This technology is amazing, fast, and accurate, and can make all kinds of products. Whether it is plastic, metal, or ceramic, as long as it can be shaped according to the appearance of the mold, it can be processed. There are so many types of injection molding technology that can be used in so many different places. What types types of injection molding technology do they have and how do they work? Let’s take a look today.
Table of Contents
- 1 Common Types of Injection Molding Technology
- 2 Specialized Injection Molding Techniques
- 3 Applications of Types of Injection Molding Technology
- 4 Advantages of Injection Molding
- 5 Factors to Consider When Choosing Types of Injection Molding Technology
- 6 Conclusion: Best Types of Injection Molding Technology for Your Project
Common Types of Injection Molding Technology
Plastic Injection Molding: Most Common Type of Injection Molding Technology
The injection molding plastic type is the common of all the types. As the name infers, the plastic injection moulding technology deals with thermoplastic or thermosetting polymer. Because thermoplastics can melt and reshape many times, such as ABS, PP, and PC, they are widely used. This technical step is not very complex in its course. Firstly, the plastic particles melt in the heated bucket. After that, by the function of a reciprocating screw, the plastic at high pressure pushes into the mold cavity. After these materials cool and cure, the parts we want can be ejected. This method is suitable for large quantities of consumer goods such as plastic bottles, toys, and electronic product shells.
Metal Injection Molding (MIM)
Metal injection molding combines the design versatility of plastic injection molding with the metal’s durability and characteristics. In this process, manufacturers mix fine metal powder—typically stainless steel, titanium, or nickel alloy—with a binder to create a feedstock. Next, they inject this material into a mold. After injection, the parts undergo degreasing to remove the binder, followed by sintering to fuse the metal particles into solid, dense components. As a result, this method is widely used in industries such as medical, automotive, and aerospace to produce high-precision parts, including surgical tools and turbine blades.
Ceramic Injection Molding (CIM)
Ceramic injection molding involves blending ceramic powder with a binder and injecting the mixture into a mold. The ceramic powders used can include materials such as alumina, zirconia, or other ceramic compounds. This process shares similarities with metal injection molding, as both methods involve injection, followed by a degreasing step to remove the binder, and then high-temperature sintering to achieve dense ceramic components. This technique is commonly employed to produce ceramic parts for electronics, such as substrates and insulators, as well as high-performance components for industrial machinery.
Specialized Injection Molding Techniques
In addition to the above common injection molding technology types, there are some specialized injection molding technologies in actual production, which further expand the application range of injection molding for specific product needs.
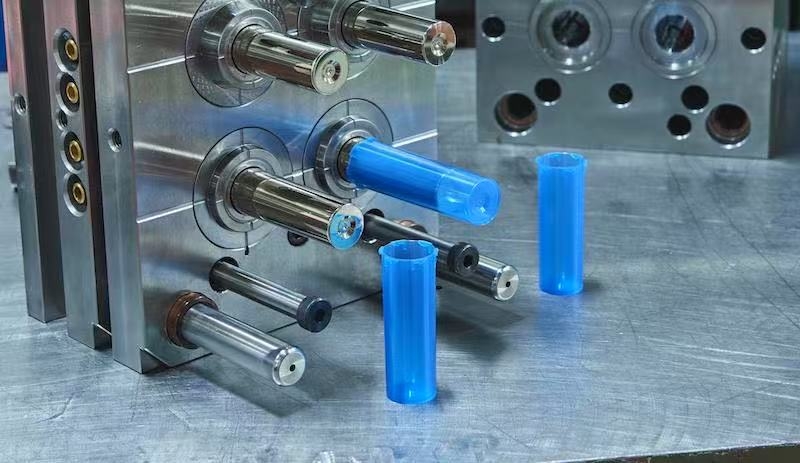
Gas-Assisted Injection Molding
When it comes to gas-assisted injection molding, we need to inject a certain amount of molten plastic into the mold, and then inject an inert gas (often nitrogen) into the core of the part. The gas forms hollow channels inside the parts, which helps reduce material usage, increase part strength and improve surface finish. If you want to produce large plastic parts, such as car bumpers and furniture parts, gas-assisted injection molding comes as a wise option!
Advantages | Disadvantages |
Reduced material consumption | Requires specialized equipment for gas injection |
Improved part strength | Complex mold design |
Enhanced surface finish | Higher initial setup cost |
Overmolding
Encapsulation molding is the injection molding of two or more different materials on the base substrate in turn. For example, in production, a rigid plastic base can be coated with a soft elastomer to provide a better grip or rubber seal. This method is ideal for manufacturing tool handles, consumer electronics featuring soft-touch surfaces, and medical devices that need a blend of rigid and flexible materials.
Insert Molding
If we need to use insert injection molding, we need to place the pre-formed insert into the mold before injecting the molten material, so that the insert becomes an integral part of the final product. This method is widely used in the manufacture of electrical connectors, where metal terminals are embedded in plastic housings to ensure reliable electrical connections.
Applications of Types of Injection Molding Technology
Injection molding technology has a variety of types and unique advantages, and can be widely used in many industries.
Industry | Applications |
Automotive | Produces a wide range of components including dashboards, door panels, gearshift knobs, bumpers, and side mirrors. Gas-assisted for large hollow parts to reduce weight; metal injection for high-strength engine components. |
Electronics | Manufactures product housings, connectors, small precision components. Plastic injection molding is dominant. Micro injection molding for tiny components like microswitches and IC sockets. |
Medical | Plays a crucial role in producing sterile and biocompatible products such as medical tubing, seals, prosthetics. Liquid silicone for tubing and seals; metal injection for surgical instruments and implants. |
Advantages of Injection Molding
Injection molding technology has significant advantages. These advantages make it occupy an extremely important position in the manufacturing industry and become the preferred process for the production of many products.
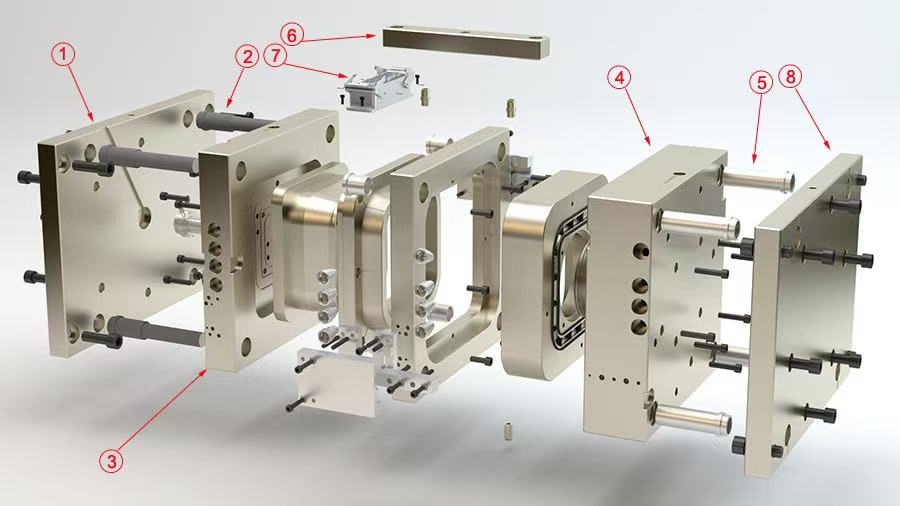
High Production Efficiency
Injection molding machines operate continuously, with cycle times from seconds to minutes, enabling efficient mass production and lower unit costs.
Complex Part Geometry
The technology excels at creating intricate parts with precise molds, producing detailed backdrops, internal cavities, and fine features.
Material Versatility of Different Types of Injection Molding Technology
It supports a wide range of materials, including plastics, metals, ceramics, and composites, allowing tailored material selection for desired product properties.
Factors to Consider When Choosing Types of Injection Molding Technology
When choosing the appropriate injection molding technology, we need to evaluate several critical factors, which may influence the final product quality, cost, production efficiency, and so on.
Material Properties:
- The mechanical, thermal, and chemical requirements of the end product determine the manufacturer’s choice of material.
- If you need high strength and heat resistance, you can usually choose metal or high-performance thermoplastics.
- It is important to understand the melting point, viscosity, and shrinkage characteristics of the material.
Part Design Complexity:
- Complex designs may require specialized skills. For example, multiple injection molding or gas assisted injection molding, this requires specialized technology.
- In order to ensure that the parts can be filled and shot correctly, the manufacturer must consider factors such as mold inclination, wall thickness uniformity, gate and exhaust port location.
Production Volume:
- Mass production is suitable for traditional plastic injection molding and other technologies. With mass production, automated production lines helps to achieve high efficiency and low unit costs.
- If it is a small batch or prototype production, then more flexible methods such as 3D printing or low-pressure injection molding will be better.
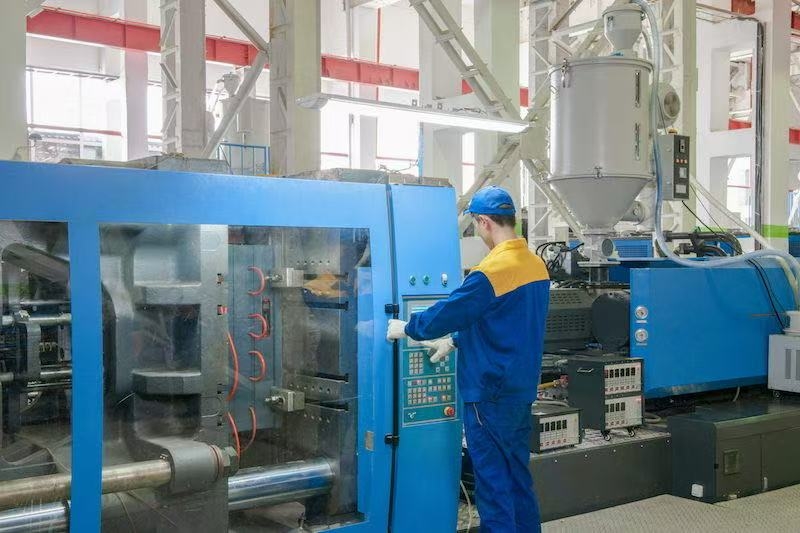
Conclusion: Best Types of Injection Molding Technology for Your Project
If you understand the different types of injection molding technologies, their applications, advantages, and considerations, you can make informed decisions to optimize your production process to meet changing market demands. In today’s competitive manufacturing environment, it is essential to find a professional and reliable partner when you meet with many options for injection molding technology. TEAM Rapid Tooling is such a trustworthy partner.
TEAM Rapid Tooling takes pride in its advanced equipment and an experienced professional team. Whether it is plastic injection molding, metal injection molding or ceramic injection molding, as well as various special injection molding technologies, we have a deep understanding and rich practical experience. When you face different production batch requirements, TEAM Rapid Tooling can also provide flexible and efficient solutions.
Click now to start your cooperation journey>>>
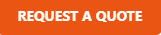