Aluminum is a common metal used in various manufacturing processes. It is the metal extracted and processed from bauxites through a long and complex production process. Manufacturers use different types of aluminum alloys for a wide range of industrial applications, such as consumer electronics, automotive, aerospace, construction, and many others.
There are two types of aluminum alloys you can use in rapid manufacturing and mass production, which are wrought aluminum alloys and cast aluminum alloys. These are the common alloys used in aluminum processing today. In this guide, you will learn about comparing aluminum alloys used in aluminum processing.
Table of Contents
Primary Types of Aluminum Alloys
There are two primary types of aluminum alloys, which are wrought aluminum alloys and cast aluminum alloys. Each aluminum alloy type has its own properties and characteristics. For instance, wrought aluminum alloys are stronger than cast aluminum alloys, which is the reason manufacturers often use them for creating metal fixtures in various industries by CNC milling and CNC turning, such as automotive, aerospace, and construction.
Meanwhile, cast aluminum alloys are cheaper die cast metal to use, while still maintaining their lightweight and durable properties. Manufacturers use cast aluminum alloys to mass-produce various rapid sheet metal parts, components, and sheet metal prototype. Cast aluminum alloys can speed up the production process since these alloys are easy to cast.
Wrought Aluminum Alloys
Wrought aluminum alloys are the types of aluminum alloys used for shaping processes in the manufacturing industry. It has quite a high melting point, and it is available in various thickness options, offering the foil-like thickness as the thinnest version. Wrought aluminum alloys have a weaker temperature tolerance compared to cast aluminum alloys.
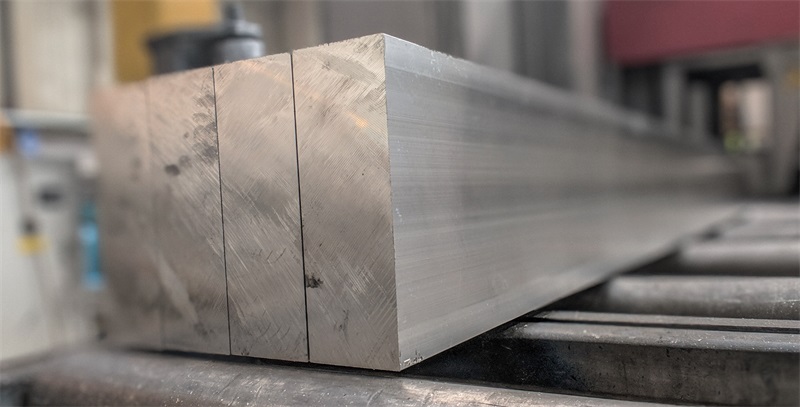
There are two types of wrought aluminum alloys, which are heat-treatable and non-heat-treatable. For the heat-treatable alloys, you can strengthen the wrought aluminum alloys using the heat treatment method. For the non-heat-treatable alloys, you can’t use the heat treatment method to strengthen the wrought aluminum alloys. Instead, you can use the strain-hardening method to do that.
●Better mechanical properties.
Wrought aluminum alloys have better mechanical properties than cast aluminum alloys. You can rely on the strength and durability of the wrought aluminum alloys for various industrial applications by CNC machining services, while still maintaining their lightweight characteristics.
●No internal or external defects.
With wrought aluminum alloys, you can find no internal or external defects. Wrought aluminum alloys are solid alloys that have excellent structural integrity, which makes them great to create metal fixtures.
●Smoother surface finishes.
Wrought aluminum alloys also have smoother surface finishes when compared to cast aluminum alloys. With wrought aluminum alloys, you can create various metal parts for a wide range of industries without needing to use additional processes to smoothen the surface finishes.
●Best for shaping processes.
Wrought aluminum alloys are best for shaping processes in manufacturing, making them suitable to use in various metal-forming processes, such as extrusion. You can also use wrought aluminum alloys to create custom-designed parts and components for various industrial applications.
Cast Aluminum Alloys
Cast aluminum alloys are the types of aluminum alloys that contain various casting properties. It means you can use these aluminum alloys in various casting production processes, such as die casting. Cast aluminum alloys can help speed up the production process because of their low melting point, which makes it easier to produce by aluminum die casting.
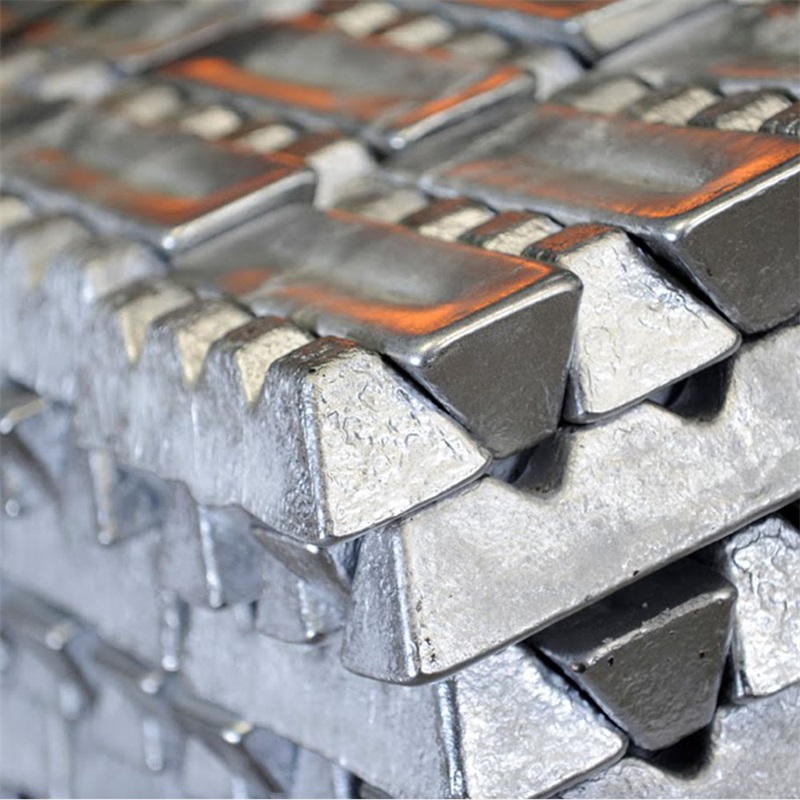
Cast aluminum alloys are lightweight and durable, and it is suitable for various applications across a wide range of industries. It is also cheaper to use than wrought aluminum alloys.
●Cost-effectiveness.
Cast aluminum alloys are much cheaper than wrought aluminum alloys. Manufacturers use cast aluminum alloys in various production processes to help cut down on their manufacturing costs, while still maintaining high-quality production results.
●Best for casting processes.
Cast aluminum alloys are best for casting processes in manufacturing, as it is straightforward to cast, and it is also easy to shape according to the manufacturer’s design requirements. Manufacturers use cast aluminum alloys in the die-casting process, as well as for various tooling equipment.
●A wide range of applications.
You can use cast aluminum alloys for a wide range of applications, such as creating farming equipment, window fittings, device housings, containers, and many others. It is also lightweight, durable, and corrosion-resistant, making it a valuable metal material for various applications.
●Excellent temperature tolerance.
Compared to wrought aluminum alloys, which have poor tolerance to high temperatures, cast aluminum alloys have excellent tolerance to high temperatures. So, you can use cast aluminum alloys to create hardware parts or components that will get exposed to high temperatures all the time, such as engine parts.
●Low melting point.
With the low melting point of cast aluminum alloys, you can use it for fast-production casting processes in manufacturing. The low melting point means it will be easier and faster to cast, which also means it can help improve your production speed.
Differences between Wrought and Cast Aluminum Alloys
There are differences between wrought and cast aluminum alloys. These aluminum alloys have their own purposes and industrial applications. Also, these types of aluminum alloys have their own unique properties and characteristics. Here are some common differences between wrought and cast aluminum alloys:
●Usage in the manufacturing process.
Wrought aluminum alloys are the alloys suitable for shaping processes in manufacturing, whereas cast aluminum alloys are suitable for casting processes in manufacturing.
●Melting point.
Wrought aluminum alloys have a high melting point, whereas cast aluminum alloys have a low melting point.
●Temperature tolerance.
Wrought aluminum alloys have poor tolerance to high temperatures, whereas cast aluminum alloys have excellent tolerance to high temperatures.
●Material defects.
Wrought aluminum alloys have superior material quality with no internal and external defects, whereas cast aluminum alloys have both internal and external defects, which include shrinkage porosity.
●Costs.
Wrought aluminum alloys are more expensive to use in manufacturing, whereas cast aluminum alloys are cheaper to use for mass production.
●Grades.
Wrought aluminum alloys have types of aluminum alloys grading system, which includes 1000 Series, 2000 Series, 3000 series, 4000 series, 5000 series, 6000 series, and 7000 series, which are popularly used in rapid prototyping services. Meanwhile, cast aluminum alloys have a grading system, which includes 1xx.x, 2xx.x, 3xx.x, 4xx.x, 5xx.x, 6xx.x, and 7xx.x.
Conclusion
Both wrought and cast aluminum alloys have their own usage in manufacturing, with types of aluminum alloys offering their own benefits for different production processes.
For overall quality, wrought aluminum alloys are better than cast aluminum alloys. However, with cheaper pricing, cast aluminum alloys offer a wider range of applications in various manufacturing industries. Are you looking for a manufacturer to help with aluminum parts manufacturing? Contact us today to request a free quote now!