Threaded holes are the holes you create inside a hardware part, featuring the screw system you can use to lock another part or component in it. So, when creating a threaded hole, it’s not just about drilling the hole. You will also need to create a thread inside the hole to match with the external threaded part you want to insert into it later.
With threaded holes, you will need to make careful measurements to ensure that both the internal and external threads match each other. Otherwise, you can’t make both parts work with each other. You also need to take into consideration the lengths of the external parts and the internal threads.
Table of Contents
Types of Threaded Holes
There are two types of threaded holes you can make for your rapid prototypes, sheet metalwork and components. You can create the screw system or threads depending on your needs. The two threaded hole types will give you two-side threads and one-side thread. Here are the threaded hole types you can make:
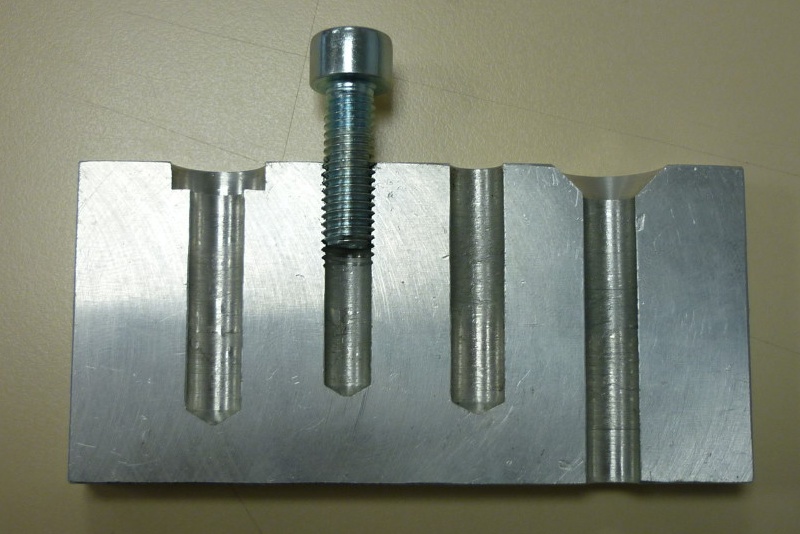
Thread holes type 1: Through Holes.
Through holes are the threaded holes that will go through the two sides of the hardware and plastic injection molding service parts . So, you can use the hole from either side to insert the external threaded part into it.
Thread holes type 2: Blind Holes.
Blind holes are the threaded holes that will only go through one side of the CNC machining parts. The threaded hole will stop at the center of the internal part, without piercing all the way to the other side. You can only insert the external threaded part from one side.
Step-by-Step Method of Creating Threaded Holes
1.Create the Right Diameter for the Hole
The first thing you need to do is to create the right diameter for the hole. You will ruin the threaded holes if you don’t create the right diameter for it. In this process, you need to use the regular drill tool to create the right diameter for the hole.
Then, you will need to drill the hardware and sheet metal fabrication part to the length that will match with the length of the external thread. You can choose whether to create the blind hole or the through hole type.
2.The Chamfering Process
Chamfering is a kind of smoothening process that can help you smoothen the hole, which can also help increase the hole’s durability for long-term use. You can perform the chamfering process by using a special drill bit designed for chamfering the hole you have created inside the rapid manufacturing part.
The chamfering process will also ensure that the bolt will have the right alignment when you create the threads on it. The right alignment is important to ensure a perfect match for the threaded holes with the external thread.
3.Drilling the Hole to Straighten It
Next, you will need to drill the hole once more. This time, the goal is to straighten the hole, which can prevent it from getting bent inside, so that the external thread can enter the hole with no problem.
During this process, you will need to measure the size of the hole and the size of the external thread. The external thread or bolt size needs to fit well with the size of the hole you are creating. However, please note that, in the straightening process, the external thread size will always be bigger than the size of the hole. The reason is that you can match the size of the external thread with the size of the internal thread when you go through the tapping process later.
Also, you will need to ensure that the length of the internal thread will match well with the length of the external thread. Any discrepancies will make the screw system not too secure, meaning that you will not fit the external and internal threads later. So, unless you want to create a through hole, you will need to match the length of the external thread with the length of the hole.
4.Tapping the Hole
The last step is the tapping process. Tapping will increase the size of the hole, and the goal for this process is to ensure that the external thread can fit well within the internal thread, so that the fastening system(types of fasteners) will work with no problem. You will need to use the tapping tool and tap it in the clockwise and counterclockwise rotation inside the hole.
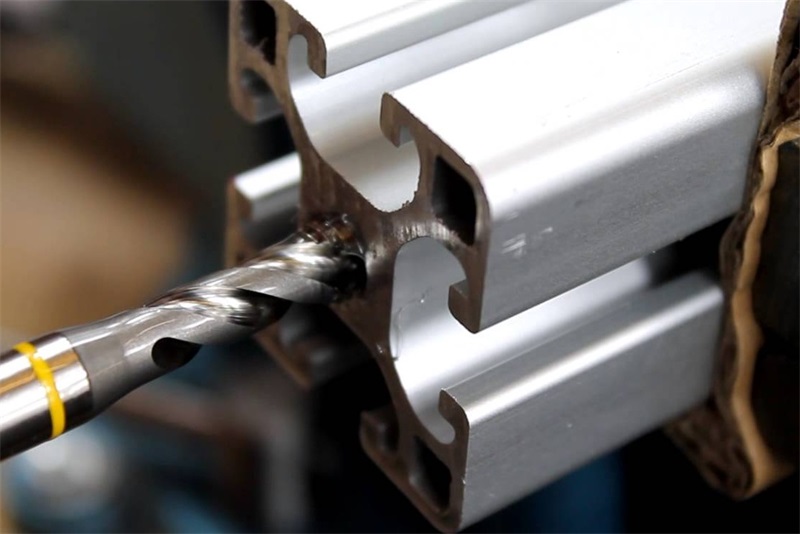
You can also use the tapping process to push the internal hole deeper. So, depending on your design requirements, you can use the tapping process to get the right size and length for the threaded hole. Aside from that, you will also need to keep the internal hole clean from any material waste or chip accumulation during the tapping process.
Precautions to Look for when Making Threaded Holes
You will need to ensure that the threaded holes you make will fit best for the external and internal threads. Otherwise, the threaded holes won’t work well as a fastening system for your parts and components. Here are some precautions you need to look for when making threaded holes:
Take care of the thread length.
The length of the thread is very important, because it will affect the fastening system. Make sure that the length of the internal and external thread matches each other.
Testing the threaded holes before mass production.
You will need to test the quality of the threaded hole before putting it into mass production. It is also important to fix any defects that might happen during the threading process.
Use suitable threading equipment.
Different materials will need to use different threading equipment. Also, there are variations of the threading tools you can use, which will help create the best threaded holes for different materials.
the material hardness If is sufficient for threaded holes.
The material hardness is something you need to keep in mind, because you might break the material if you are using the wrong threading tools or equipment. The drilling speed and drilling bits you use also need to be suitable for the materials you are working on.
Conclusion
The best quality threaded holes are the ones made with precautions and follow the right step-by-step method. The goal of making threaded holes is to create the fastening system for your material parts, so you need to ensure the best match for both the internal and external threads.
Depending on the materials you are using, you will need to adjust the way you make the threads for those materials to prevent any production mistakes or defects.
Looking for a manufacturer who can help with precision machining? Contact TEAM Rapid today, we offers a series of manufacturing services such as 3d print services, injection molding services, die casting services etc to meet your prototypes to large volume production needs.