When it comes to crafting plastic components, injection molding mold and blow molding mold takes the spotlight. Despite their shared concept of molding melted plastic, they embark on distinct journeys to create a diverse range of objects. Injection molding surges forward by infusing liquefied plastic into a tailor-made mold, forging sturdy end products. Conversely, blow molding orchestrates the birth of hollow wonders like bottles by heating and inflating plastic preforms.
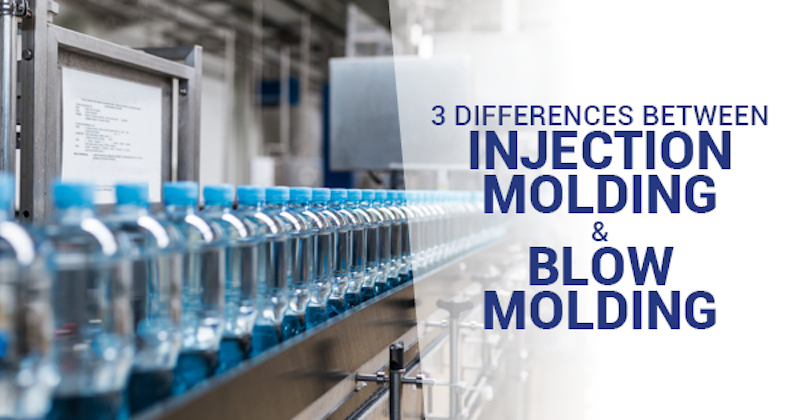
Table of Contents
- 1 Sculpting Plastic Marvels: A Tale of Injection Molding Mold and Blow Molding Mold
- 2 Crafting Realities: From Hollow Echoes to Solid Foundations
- 3 Distinguishing Injection Molding Mold from Blow Molding Mold
- 4 Conclusion
Sculpting Plastic Marvels: A Tale of Injection Molding Mold and Blow Molding Mold
Injection molding, the maestro of solid creations, orchestrates its masterpiece with meticulous precision. This symphony commences by crafting a custom mold, often hewn from steel or aluminum. This mold finds its stage within an injection molding machine, ready to bring the drama to life. Here, molten plastic takes its cue, propelled into the mold under formidable pressure. Cooling, setting, and solidifying, it metamorphoses into a tangible marvel. As the curtains rise the mold unveils its creation, delivering a resolute and distinct product.
Now, enter the realm of blow molding, the enigmatic conjurer of hollow marvels. This performance kicks off with the crafting of a preform or parison, a molten plastic tube, a mere whisper of its final glory. This ethereal preform takes center stage within a blow mold, awaiting its transformation. As warmth envelops it and compressed air takes its cue, the preform unfolds, blooming into a hollow masterpiece, think bottles and containers that grace our daily lives. A spellbinding act where heated plastic breathes life into emptiness.
Crafting Realities: From Hollow Echoes to Solid Foundations
Blow molding graces the world of hollowness, fashioning the very vessels that cradle life’s elixirs. Picture bottles and containers, delicate yet resilient, their lightweight frames perfectly suited to embrace liquids and essences. The process orchestrates the birth of slender, hollow marvels, making it a prime choice for crafting items like water bottles, shampoo vials, and detergent reservoirs. The dance of plastic breathes life into voids, birthing wonders that we reach for daily.
Conversely, plastic molding wields its prowess in the realm of solidity. Here, the stage is set for crafting robust, tangible pieces that underpin modern existence. Automotive landscapes come to life as it births intricate components; medical realms are enriched with devices like syringes and inhalers, all cast in precise plastic form. The process thrives in complexity, embracing tight tolerances to shape items like electronic housings, gears, and levers. Each creation is a testament to plastic’s adaptability.
The tale unfolds: blow molding weaves elegance into hollowness while injection molding cements reality with solidity. As our narrative deepens, let’s venture into the very choreography that births these plastic dreams.
Distinguishing Injection Molding Mold from Blow Molding Mold
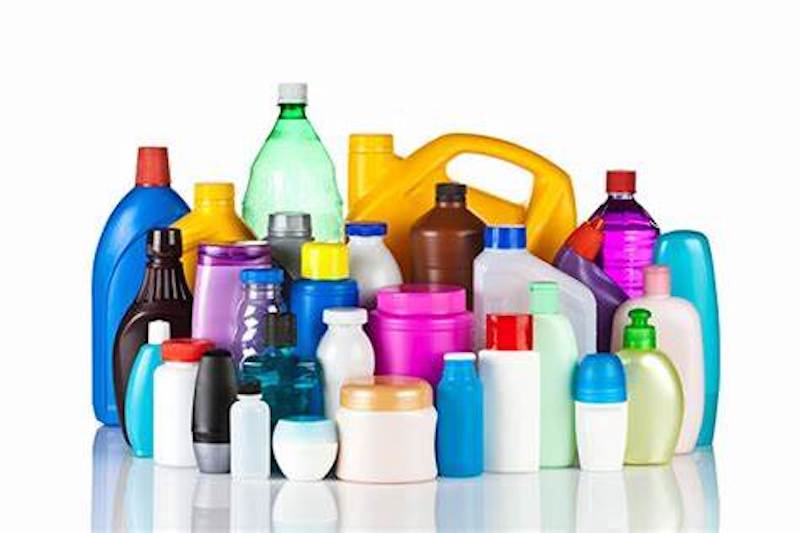
Shaping Plastic Realms with Precision
The differentiation between injection molding mold and blow molding mold unveils a remarkable contrast in the artistry of crafting plastic objects.
Injection molding mold commands the realm of solidity, shaping its creations with meticulous detail. This process commences with the intricate design and fabrication of a tailored mold, often constructed from steel or aluminum. Taking center stage within an injection molding machine, the mold becomes the conduit for molten plastic material. Under heightened pressure, the liquefied plastic is infused into the mold, obediently assuming its prescribed form. Cooling and solidifying, the plastic transforms into a tangible masterpiece. As the curtain rises, the mold unveils its product, resolute, distinct, and meticulously formed.
In stark comparison, blow molding mold embraces hollowness as its canvas. The journey unfolds with the crafting of a preform or parison, a molten plastic tube destined for transformation. This ethereal prelude occupies a blow mold, a setting where its magic unfolds. With warmth and the gentle persuasion of compressed air, the preform gracefully expands, conforming to the mold’s desires.
Choice of Materials in Injection Molding and Blow Molding: A Study in Polymers
The realm of plastic transformation finds its essence in the careful selection of materials. Both injection molding and blow molding harness the versatility of thermoplastic materials, yet their preferences carve distinct pathways.
In the world of blow molding, HDPE (High-Density Polyethylene) reigns as the cornerstone. This resilient material is uniquely suited to the creation of hollow forms, a testament to its structural integrity. The process finds its signature in the crafting of bottles and containers, embodying simplicity and functionality.
Conversely, injection molding enters a more expansive arena. While it maintains a foundation in thermoplastics, it explores the vast landscape of thermosetting polymers. This broader palette allows for the creation of intricate, high-precision components, ranging from medical devices to automotive parts.
Production Rates in Injection Molding and Blow Molding: Precision in Swiftness
The prowess of injection molding and blow molding shines in their ability to generate substantial product volumes within tight timeframes. However, their respective production rates are subject to intricate variables, exemplifying the intersection of complexity, material, and machinery.
Injection Molding: Automated Precision
The realm of injection molding unfolds as an automated symphony. This method yields high-speed production through a meticulously designed process. Cycle times range from mere seconds to minutes, dictated by the part’s intricacy and dimensions. The introduction of multi-cavity molds elevates the rhythm, enabling the concurrent production of multiple components in each cycle.
Blow Molding: The Artistry of Extended Cycles
In contrast, blow molding dons a rhythm characterized by slightly longer cycles, attributed to the sequence of steps involved in heating and expanding plastic tubes. However, this cadence carries its grace. Machines equipped with multiple cavities bring a surge of efficiency, augmenting the production tempo. Specific blow molding techniques, like extrusion blow molding, unveil a sophisticated choreography where multiple parisons are extruded in unison, ushering in parallel production.
In summary, both injection molding and blow molding manifest the capacity for swift creation yet diverge in the details of their process intricacies. The nexus of intricate part geometry, chosen material, and machinery’s efficacy charts the course of their production tempo. Whether it’s the meticulous precision of injection molding or the graceful orchestration of blow molding, their shared mission remains rooted in achieving voluminous outputs within the constraints of time.
Conclusion
In essence, injection molding and blow molding unite in shaping molten plastic, yet their paths diverge in processes, products, materials, and production rates. This understanding is pivotal for manufacturers, guiding the selection of the apt technique for their envisioned creations.
Besides from injection molding and blow molding, TEAM Rapid also offers 3D printing services, die casting, and CNC machining for your needs. Contact our team today to request a free quote now!