Snap-fits have become a preferable solution for joining components in differing industries. You can configure the shapes and geometries of the snap-fit locks to match your component’s design. Also, you don’t need to use any external tool to lock or unlock the snap-fit mechanism.
Table of Contents
Benefits of Snap-fits
A reliable and secure locking mechanism is essential to join two components together. Snap-fits can provide the best locking mechanism for your products. Here are the benefits of snap-fits:
Ideal mechanical joiner
Unlike any other mechanical joiner solutions, snap-fit offers the optimal way to join different mechanical items without issues. You can create a specific snap-fit design that becomes an excellent match for your product or item. Snap-fits offer mechanical joiners that are easy to use, precise, and durable for differing purposes.
Snap Fits: Design options
Snap-fits allow you to create custom key lock configurations for your product needs. Each snap-fit design can offer you geometrical configurations with complex shapes. Each design will give you the flexibility based on your rapid manufacturing project goals.
Simple assembly process
Compared to the screws, snap-fits offer an easy assembly and disassembly process for the user. Users can lock and unlock the snap-fit locking system without much complications. Also, you don’t need extra tools to assemble or disassemble a snap-fit system.
Aesthetics
Another benefit of snap-fits is the aesthetics of each key lock for your product. It offers differing aesthetical designs that you can match with the primary product without issues. The catchy and aesthetic design of snap-fits makes it easier to attract more customers to your product.
Durability
The durability factor is also an essential benefit of snap-fits. Snap-fits can withstand millions of snaps from users without getting damaged. So, you can use the snap-fit system for many years to come. It can always provide an effective locking system for your product.
Snap-Fits is Reliability
Snap-fits also offer reliability in terms of the usage life cycle. This locking system will be much more reliable for long-term usage, providing an efficient and reliable lock mechanism. In manufacturing, snap-fits can withstand continuous assembly and disassembly processes without losing their locking grip.
Long-term sustainability
Using snap-fits in your manufacturing assembly means contributing to long-term manufacturing sustainability. Snap-fits are great for producing lock mechanisms that don’t generate too much material waste. Each snap-fit design will use an efficient number of materials while minimizing potential waste.
Snap-fits offer benefits that are often better than regular joiner solutions. Also, this locking method provides a secure lock for your product without a complicated locking system. The ease of assembly and disassembly will give the snap fits a better chance of offering the best user experience.
Design Tips of Snap-fits
The best snap-fit mechanism will follow the proper design aspects in its blueprint. Snap-fits allow you to design the mechanical lock or enclosure freely. However, it must follow the best design guidelines to keep it up with the highest quality standards. Here are some snap-fit design tips:
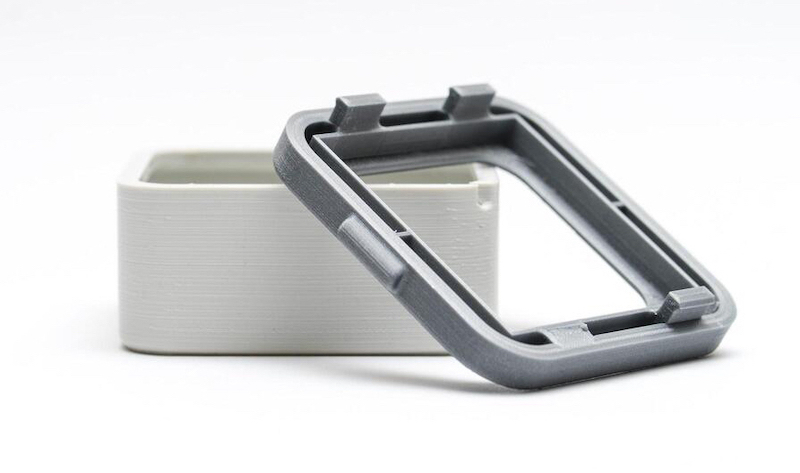
Rapid Prototyping
Rapid prototyping is an essential step in snap-fit designing. It will allow you to test the snap-fit samples before production. You can use plastic prototypes to determine the quality standards of each sample. This way, you can filter the good from the bad and only produce the snap-fits that follow your quality standards.
Aesthetic appeal
Consider the aesthetic appeal of your snap-fit design. Also, consider the design usability alongside it. The aesthetic appeal will help catch the attention of your potential customers, whereas the usability factor will keep them comfortable when using your product especially for the craft, medal, bottle openers etc.
Snap-fits: Clip width
It’s best to use a bigger clip width in your snap-fit design. It can help improve the snap-fit durability and increase its longevity factor. Also, avoid designing a snap-fit with narrow clips due to its weak strength.
No sharp corners
Adding sharp corners is a bad idea for your snap-fit design. Sharp corners can make it difficult for the snap-fit mechanism to work well. It can also create unnecessary surface stress for the snap-fit mechanism, and it might lead to damage.
Taper
Tapering is a technique to make the snap-fit areas thinner toward their edges. It is essential in a successful snap-fit design, as tapering can help distribute the surface stress to all areas more evenly. Also, tapering can help you reduce materials usage during snap-fit production.
Material variation
Be sure to pick the material that can cover all your project needs for the snap-fit design. Some materials will offer better durability and longevity than others at a higher price. It’s best to have material variations in your snap-fit designs to distribute all your desired features.
Distribute the surface stress
Design your snap-fits to distribute the surface stress evenly. It is essential to avoid damaging the snap-fit mechanism during use. Uneven surface stress can trigger damage or cracks around the heavy-stress areas of the snap-fit mechanism after prolonged use.
Snap-fits is Easy assembly
The ease of assembly process should also be an essential consideration when you design a snap-fit mechanism. Build the snap-fit mechanism and make it easy to lock and unlock without much struggle. The ease of assembly will also help you assemble the components for a more advanced manufacturing process.
Follow these proper design tips to find a snap-fit design that will meet the best quality standards. Build your snap-fit designs creatively while still considering the usage value of the design. You can test several designs using prototypes before launching them to complete production.
Snap-Fits’ Types
Designing a snap-fit mechanism requires creativity and a deep understanding of its function. The limitless snap-fit designs only stem from the primary types of snap-fits. Here they are:
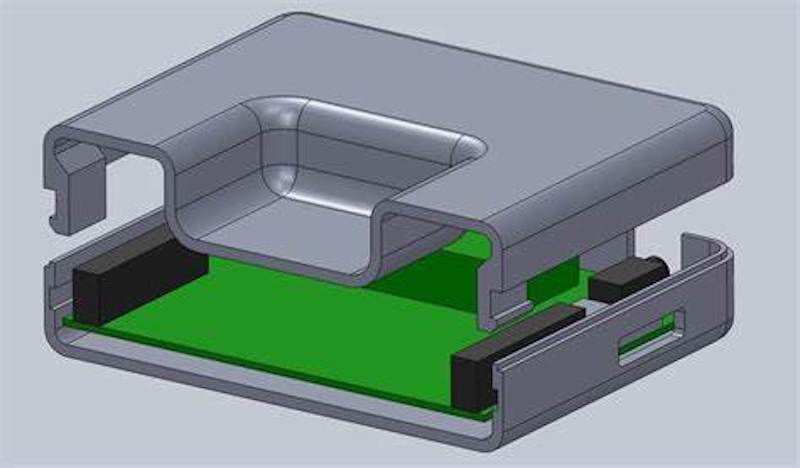
Torsional
The torsional snap-fits have a rotational design that allows you to twist the snap-fits to lock or unlock the mechanism. This snap-fit type will become very usable in specific applications requiring rotational locks. However, it is very uncommon to use in everyday applications for consumer products.
Annular
The annular snap-fit has a circular shape suitable for joining cylindrical components. It will give you a 360-degree movement to lock and unlock the snap-fit mechanism. This snap-fit type can strengthen the base of a cylindrical part with its uniform hold.
Cantilever
It is a hook-type snap-fit that provides the method to lock or unlock the mechanism using the cantilever-style hook. You can find this snap-fit type in many consumer products, like helmets, bags, and more. The hook part of the snap-fit is very flexible, which allows you to move it in and out of the lock mechanism.
These are the primary snap-fit types you can use as the base of your design. Any design variations will stem from one of these snap-fit types, which depend on your design goals. Snap-fits offer the best flexibility in terms of design to match the components you are working on.
Common Problems in Snap-fits
There will always be potential issues when you design a snap-fit mechanism. Poor material or poor environment can make or break your snap-fit design. What are the common problems with snap-fits?
Snap-fits: Poor stress distribution
Stress distribution on the surface level of the snap-fits can affect how it works. Poor stress distribution can cause the snap-fits to fail over time. It can also cause permanent damage to the hook area of the snap-fit mechanism.
Poor material choice
The choice of material can also cause problems during the practical usage of snap-fits. It’s essential to choose the correct material for each snap-fit application. Using the wrong material can only put the snap-fit mechanism at risk of failure or damage.
Degradation due to the environment
Snap-fits can also degrade over time in extreme environmental conditions. It can be bad news that your snap-fit mechanism is no longer working due to environmental-related degradation. It’s best to use material types suitable for specific environments.
Loose on the lock mechanism
The lock mechanism of the snap-fit can loosen during continuous use. It might not hold enough retention to lock the snap-fit mechanism. The solution is to inspect the hook part and try to enlarge the size of the hook.
Crack on the snap-fits joint
You might also find cracking on the snap-fit joint after some usage period. The reason might be that the snap-fit design is not fitting for handling the pressure during the locking mechanism. You can change the design to distribute the pressure on the snap-fit surface more evenly.
Deformation on prolonged use
Snap-fits can also deform during prolonged usage because of various factors. Always use the snap-fit on regular operating environments and temperatures to avoid this problem. Also, using a more durable material can offer the best solution to this problem.
You can experience these problems when you design a snap-fit mechanism. Test your snap-fits before producing them on a large scale. Be sure to fix these problems before using the snap-fits for your final products.
Conclusion
Snap-fits offer one of the best joining mechanisms for various components in differing industrial applications. Designing a snap-fit requires careful consideration of its functions and design shapes. An efficient snap-fit mechanism must be free of potential problems that might cause the mechanism to fail. Are you looking for a ODM and OEM supplier for your prototypes and volume production? Contact TEAM Rapid at [email protected] today to get free supports now!