Selecting the ideal rubber molding process is essential for producing rubber items that are both economical and effective. It is also being built to last. The exceptional capacity of silicone rubber molding to transform high-grade silicone into various intricate shapes stands out as a key advantage. This method showcases unmatched flexibility, along with the material’s impressive ability to withstand fluctuating temperatures and its excellent electrical insulation qualities. Such attributes make it an excellent choice for a wide array of applications, from detailed parts in the automotive industry to essential equipment in the medical field, demonstrating its critical role in manufacturing items that demand high precision and dependability.
Table of Contents
Rubber Molding Processes
There are several molding methods like compression, transfer, and injection molding. Each suited to different rubber types with their specific features and intended uses. When evaluating these against silicone rubber molding, distinct benefits and drawbacks become apparent. For instance, silicone rubber molding is more precise compared to the straightforward and older method of compression molding. It involves warming a rubber blend in a mold to create large, uncomplicated objects. Transfer molding, while providing more intricate details and accuracy for complex models, demands more extensive material handling and could result in greater waste. Meanwhile, injection molding, which forcefully injects rubber into a mold cavity under high pressure. It is renowned for its ability to deliver consistent, high-quality output in bulk. However, the higher upfront costs and extended setup times associated with injection molding may deter smaller-scale operations.
Silicone rubber molding’s thermal and chemical robustness outshines many standard rubbers, making it preferable for harsh conditions. Its low viscosity allows for the creation of intricate designs without compromising material strength. Moreover, its biocompatibility makes it a prime choice for medical uses where other rubbers might not meet strict standards.
Choosing silicone rubber molding entails careful consideration could affect production schedules. Ultimately, the decision between silicone rubber molding and other rubber molding processes hinges on a detailed assessment of the product’s requirements . Such as purpose, environmental conditions, production volume, and budget. Each method offers distinct advantages, underlining the need for a thorough analysis to find the most appropriate plastic molding strategy. This process not only ensures the product’s viability but also drives innovation in rubber molding. It expands the possibilities for product quality, functionality, and creativity.
Cost differences in Rubber Molding Processes
The price variation between silicone rubber and its counterparts, such as natural, styrene-butadiene (SBR), and nitrile (NBR) rubbers. It arises from differences in raw material prices, manufacturing complexity, and the specific performance needs for their respective applications. Here’s a closer examination of the factors making silicone rubber generally more expensive:
Cost of Base Materials
Silicon, obtained from the energy-intensive transformation of quartz sand, serves as the cornerstone for silicone rubber molding processing. This process demands significant energy, pushing up the cost base for silicone materials. In contrast, natural rubber is sourced from rubber tree sap, and synthetic alternatives like SBR and NBR come from less expensive petrochemical origins.
Complexities in Rubber Molding Process Manufacturing
Crafting silicone rubber involves a sophisticated process that typically requires pricey catalysts, such as platinum, for polymerization. Additionally, the vulcanization of silicone rubbers, utilizing an additional cure system, may need more energy or extra stages like post-curing to ensure the product meets all desired specifications such as SPI surface finish need, further elevating production costs.
Exceptional Performance Features
Known for its wide temperature endurance (-55°C to +300°C), excellent electrical insulating properties, resistance to chemicals and UV radiation, and biocompatibility, silicone rubber’s development to satisfy stringent criteria often means the use of higher-grade, and thus costlier, materials and compounds.
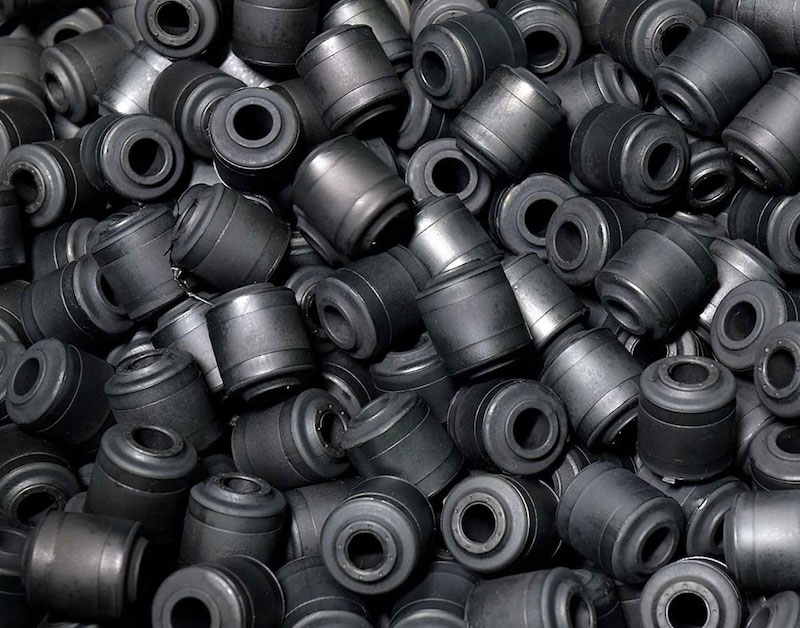
Targeted Market and Specific Applications
Silicone rubber is predominantly used in specific fields. It requires its unique attributes, including aerospace, automotive, medical devices, and electronics. The targeted nature of these applications usually translates to lower production volumes than for more commonly used rubbers. It leads to a decrease in economies of scale and higher individual unit costs.
Standards Compliance and Quality Maintenance Rubber Molding Process Costs
For use in the medical, food service, and child care industries, silicone rubber injection molding process must comply with rigorous regulatory standards for safety and compatibility with the human body. Achieving and upholding these standards incurs significant additional expenditure for testing, ensuring quality, and obtaining certifications.
Despite its higher initial cost, the unparalleled performance and longevity of silicone rubber in demanding settings often make it a worthwhile investment. When the distinct advantages of silicone are not a necessity, other types of rubber might provide a more economically feasible solution.
Which Rubber Molding process is the right one for you?
Selecting between silicone rubber molding and alternative rubber molding techniques requires a deep dive into the unique specifications and ambitions of your venture. Here are several inventive and distinctive points to ponder when making your choice:
The Elemental Conjurer’s Inquiry
Deciphering Material Mysteries – Envision yourself as a conjurer, decoding the secret traits of each substance. Should your invention need to endure the wrath of extreme environments or resist the allure of chemical seductions? silicone rubber might emerge as your mythical substance, thriving where others falter. On the flip side, for creations demanding resilience and resistance to wear, akin to an ancient shield, consider the virtues of natural rubber or SBR.
The Historian’s Quest
Projecting Your Artifact’s Legacy – Were your product to journey through the annals of time, would it emerge unscathed or worn? Silicone rubber is lauded for its ability to defy the ravages of time, maintaining its integrity against the elements. For artifacts meant to last, resisting the trials of environmental exposure, silicone’s enduring nature is an invaluable trait.
The Culinary Alchemist’s Concern
Ensuring Purity in Interaction – Consider if your product were an ingredient in a culinary masterpiece. Does it meet the stringent standards of taste and safety? For endeavors touching upon the culinary, healthcare, or infant care realms, the non-toxic and hypoallergenic qualities of silicone rubber endorse it as the ingredient of choice, safeguarding the essence of your creation.
The Guardian of Gadgets
Wielding the Shield of Insulation – In the realm of devices and machinery. If your product acts as a guardian against electrical forces, silicone’s exceptional insulating prowess could be the protective ward. For encasing electronics or insulating conductive paths, silicone rubber ensures your technological treasures are kept safe from electrical harm.
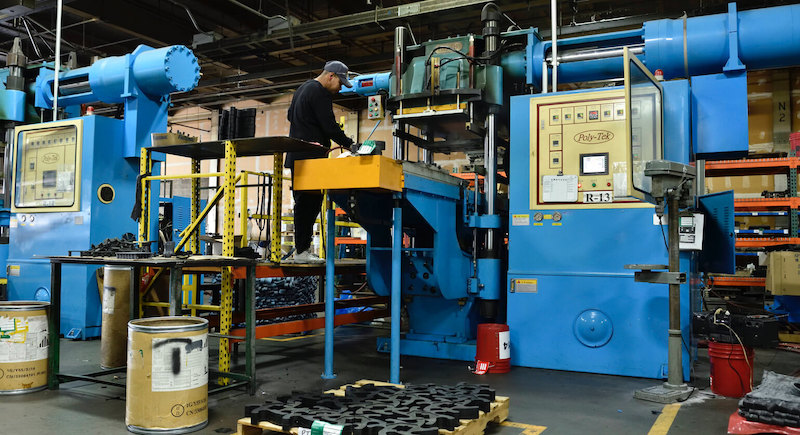
The Eco-Warrior’s Pact
Embracing Green Practices If your mission includes a commitment to environmental stewardship. It is better to reflect on the life cycle and green credentials of your materials. Despite its durability, silicone presents recycling quandaries. Should ecological responsibility be paramount, assess whether silicone’s advantages outweigh its environmental downsides, or explore rubbers with greener legacies.
The Craftsperson’s Vision of Rubber molding process
Crafting with Aesthetic Intent If your endeavor is a fusion of functionality and artistry. The versatility in the appearance of silicone might appeal to your creative spirit. With its capability for vibrant coloration and translucency, silicone rubber transforms utilitarian items into objects of visual intrigue, marrying form with function.
The Economist’s Ledger
Weighing Cost Against Benefit – Embark on a journey to unearth the most valuable materials for your quest. With its superior qualities, silicone rubber commands a higher price. Determine if the distinctive properties of silicone are worth the expenditure or if alternate rubber materials might fulfill your requirements more economically. Striking a harmony between financial outlay and material performance is crucial for a wise decision.
By examining these innovative considerations, you can navigate the choice between silicone rubber molding and other rubber molding methods with a blend of technical knowledge, eco-consciousness, and an eye for design. This approach ensures your decision aligns perfectly with the unique spirit and demands of your project.
Access Team Rapid Tooling high rubber molding process services today
We offer various silicone rubber molding services to clients. And we’re able to do this at a high capacity. Here’s a short case study demonstrated our capabilities. TEAM Rapid sped up a U.S. firm’s fan cover project in China with mirror EDM for quicker machining and polishing. The project began with a Google search response, leading to recommending injection molding with a 16-day tooling timeframe. After quick approval, a 1000-part order was filled in 5 days with pre-stocked PC/ABS, shipped before Chinese New Year. The client praised the swift service and quality. For different silicone rubber molding needs, reach out to TEAM Rapid at [email protected].