Rough edges on sheet metals can cause issues in your production sooner or later. For this reason, manufacturers need to apply hemming to eliminate those rough edges. Without sheet metal hemming, achieving the best quality for the final product will be burdensome.
Table of Contents
Benefits of Sheet Metal Hemming
Keeping some rough edges on your sheet metal components is not a wise step in creating the best sheet-metal-based products. Hemming is essential to turn the rough edges on the sheet metal parts into neater edges. Here are the benefits of this process:
Sheet Metal Hemming – Aesthetic improvements
Applying a hemming procedure on your sheet metal materials can help improve the aesthetics of the final product. Hemming edges are even more tidy compared to the un-hemmed edges. Better-looking edges will increase the overall value of your sheet metal products.
Connect to other parts
Hemming can also help your sheet-metal components to connect well with others. It will improve the quality of product assembly. Two hemmed sheet metals will form a strong joint that can help create a durable assembly for any product you build.
Sheet Metal Hemming – Safer handling
The cut sheet metal components will often have rough edges, which pose a safety risk when you handle them. Applying a hemming procedure can eliminate the rough edges on these sheet metals. It will result in safer handling for these sheet metal components, especially for the craft such as keychains, medal, and badges etc.
Conceal defects
Some defects might appear around the edges of the sheet metal materials after you perform specific cutting operations. These defects can affect the aesthetic look of the final product if you don’t prevent them from taking the limelight. With the hemming process, you can conceal the defects around the sheet metal edges for a better aesthetic look.
Add more strength to the edges
Hemming can also help add more strength to the edges of your sheet metal products. With this technique, you can double up the durability of the sheet metal material you work on. The better strength on the edges will help improve the overall longevity of the final product.
Understanding the advantages of this process can help improve the quality of your sheet metal products further. Hemming is a procedure you shouldn’t skip in your sheet metal production.
Sheet Metal Hemming – How It Works
Hemming is the next step of bending. In sheet metal fabrication, hemming becomes essential to add more durability to your final product. Here’s the process:
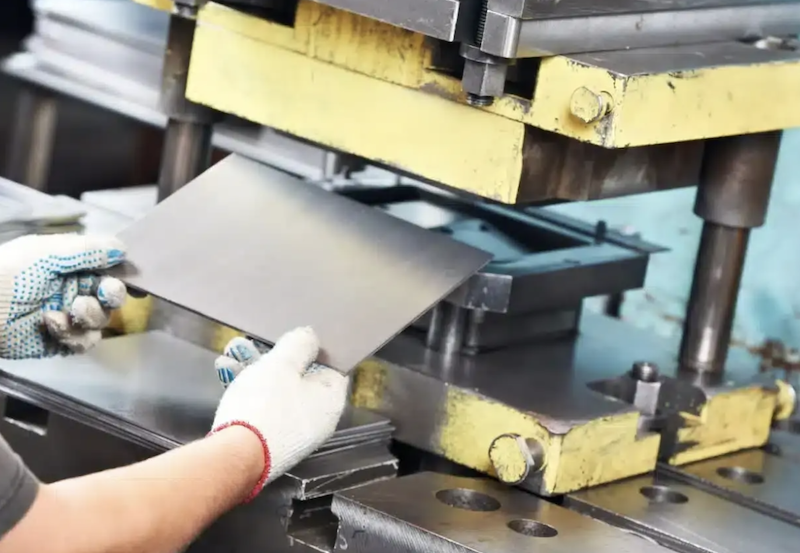
Select the suitable material
Certain hem types will only be compatible with specific material types. So, selecting the proper sheet metal material is a must. You also need to match the sheet metals with the product requirements you want to achieve.
Cut the sheet metal
Cutting the sheet metal to the proper dimensions is the pre-requisite you need to do before hemming. Depending on your design requirements, you can cut the sheet metal pieces into suitable measurements using regular cutting tools. After that, you can prepare it for the hemming process.
Sheet Metal Hemming – Select hem type
There are various hem types you can apply for the sheet metal materials. Each hem type will help your subsequent assembly processes. You can perform the proper hem type based on specialized details, such as sheet metal thickness and material types.
Bend the sheet metal
Initial bending is the procedure you can apply before performing the hemming process. It is to make the hemming process smoother and avoid any issues during the operation. The hemming equipment will perform the initial bending to bend the sheet metal to a 90-degree angle.
Hem the edges
Next, the hemming equipment will perform the hemming process on the sheet metal edges according to your chosen hemming type. The edge areas around the sheet metal will bend and roll to the inner side of the sheet metal during this process. It will double the sheet metal thickness around the edges.
Quality control
Now that you finish the hemming process, it’s time to do some finishing and quality control checks. You can use the finishing tools to check imperfect hems around the sheet metal edges. You must ensure that the hems are even throughout the edge areas.
The hemming process is quite simple to follow. It doesn’t require any complex calculations, unlike the other forming rapid manufacturing processes.
Hem Types in Sheet Metal Hemming
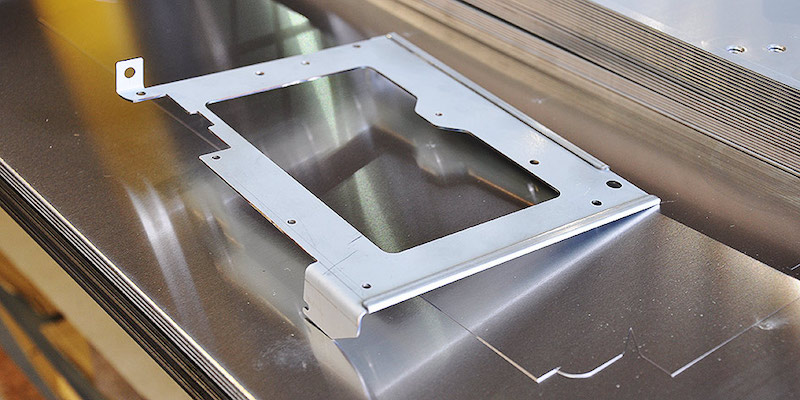
Open
The open hem type allows you to fold the edge of the sheet metal to a 180-degree angle while leaving some space between the hem part and the primary sheet metal area. You can use the open hem space for various purposes, such as to ease the assembly process. Please note that the space between the hem part and the sheet metal area must not be too broad.
Close
You can only apply the closed hem type for the sheet metals with less than 2mm thickness, as the hemming equipment uses more tonnage power to apply the hem. In closed hem, you will fold the sheet metal edge inside to a 180-degree angle. It will leave no open space between the hem and the primary sheet metal area.
Teardrop
The teardrop hem type is just the continuation of the open hem type. With the teardrop hem type, you will fold the tip of the hem further in until the hem area resembles the shape of a teardrop. This hem type is suitable for aluminum sheet metals due to their lack of ductility characteristics.
Roll
With this hem type, you only need to roll the edge inside the sheet metal part. It is similar to a teardrop but without a tip at the end of the hem. You will roll only a modest portion of the edge area of the sheet metal.
Rope
The rope hem type is similar to teardrop. The only difference is that you will flatten half of the hem tip until it resembles a rope shape. In short, this hem type combines the open and closed hem types and adds some rope-shaped space in between.
Conclusion
Sheet metal hemming becomes an integral part of any sheet metal fabrication operation. No matter the industry, there is always a need for a hemming process for sheet metals. A successful hemming operation will improve the overall product quality and strength. TEAM Rapid applies different manufacturing processes to help you make the parts successfully, contact our team at [email protected] today to request a free quote now.