Insert molding design optimization is essential to help you create a better product in this manufacturing process. With no optimization in your insert molding design, problems can occur during and after the production operation. Know the insert molding key factors, and think about your insert molding design well before running your manufacturing project.
Table of Contents
Here are some insert molding key factors to consider
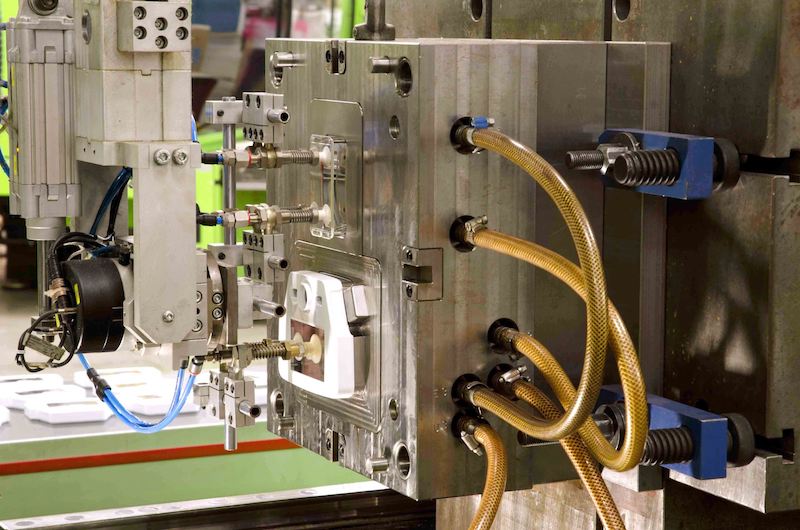
Proper Drafting
Product damage is quite common during the insert molding operation. The damage often happens during the ejection process. You might rip out the part of the final product due to improper drafting of the mold. Thus, proper drafting is essential to ensure you can eject the final product without damaging it.
The draft angle you apply to the mold / rapid tooling should not disturb the mold’s movement during ejection. It should allow for a smooth ejection process without scraping the surface of the final product.
Insert Molding key factors: No Sharp Corners
In the design process of your insert molding operation, sharp corners can often cause production problems later. With sharp corners, you can potentially create two big problems during production. First, you might halt the movements of the liquid materials inside the mold. Second, you might crack the final product during ejection.
In your injection molding design, it’s best to eliminate any sharp corners. You can turn sharp corners into rounded corners to smoothen the insert molding operation.
Wall Thickness Optimization
Insert molding requires thick walls for the mold to operate well. Thin walls on the mold compartments might lead to inconsistent product dimensions. With thin-walled molds, the thin walls might not withstand the hot temperature of the liquid materials very well. As a result, you might come up with unstable or inconsistent product shapes.
Cracking and damage can also happen with the final product when you design thinner walls for the mold. Thus, it’s essential to optimize the wall thickness of the mold to ensure the best durability. Thicker walls can handle the hot liquid materials better during the molding operation.
insert molding key factors: Mold Size
The size of the mold also matters in your insert molding mold design. It is another aspect that needs proper optimization to ensure the best result in your production. The general rule is that the insert size must not be too big for the mold. It’s best to design your mold a bit bigger than the insert.
Optimizing the mold size can give the liquid materials more space to enter the mold compartment. It will also prevent any issues during the solidification process. A more sizable mold will also bring more smoothness during the ejection process.
Insert Size
The insert design is the key to success in insert molding. The size of the insert you use will also affect the success rate of your molding operations. Optimizing the insert size can help minimize damage to your final product. The insert size should be proportionately less than the mold size.
A smaller insert can help optimize the ejection process for the mold. It can also help minimize surface cracking on your final product.
insert molding key factors: Rounded Knurling
Applying the rounded knurling design for your insert can also help ease the ejection process in your production. Rounded knurling makes the edges of your insert smoother and safer for your product ejection mechanism. With the rounded knurling design for your insert, you can minimize the potential product deformations.
You can also get a better grip with the rounded knurling design for your insert. It will make an easier ejection when you perform that manually. You can also move the insert more carefully during the ejection process.
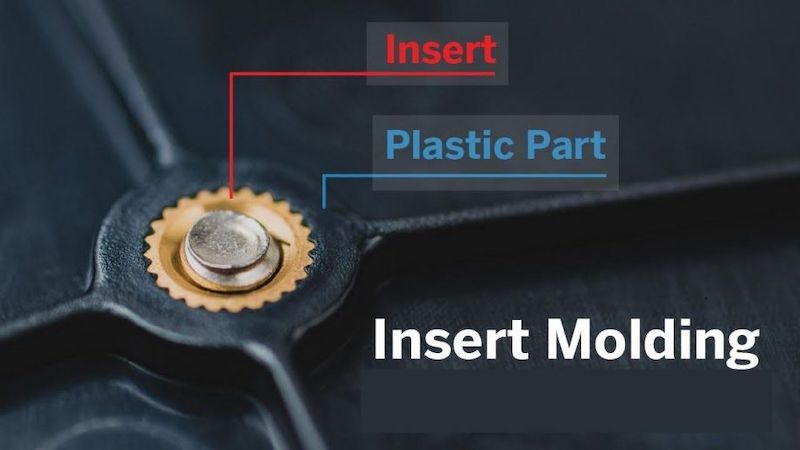
Strategic Undercut Placement
Undercuts can make your mold design appear even more complicated than usual. Thus, it’s better not to use undercuts most of the time. However, undercuts can simplify the assembly process of your final product later. You can optimize the undercut design if you want to use this feature.
Note that undercuts can make it hard to eject the final product from the mold. Be sure to surround the undercut area with plenty of open spaces inside the mold. Also, design your undercut with a 30 to 45-degree angle for maximum benefit.
insert molding key factors: Insert Material
The material for the insert will also be a game changer for your insert molding operation. There is something called “material bonding” you need to consider. The bonding between the insert and the liquid material can make or break your production cycle. You will experience many issues in production when the insert and liquid materials have poor bonding.
Meanwhile, a strong bond between the insert and liquid materials will increase the smoothness of your production. This strong bond will make the final product smoother to eject without damaging it. Also, it will help to build a smoother solidification process for the final product. It can often result in a more polished finish.
Avoid Cracks
Cracking is the most common potential issue you can have with insert molding. It often happens during the ejection process. Cracking can also appear because of poor design choices for the mold or insert. It’s best to focus on your insert molding design to avoid cracking as much as possible.
Even a tiny crack can make your final product look ugly. A crack can also disturb the overall functionality of the final product. It can also weaken your assembly line. By optimizing the design factors in your insert molding, you can avoid cracking in your final product.
Conclusion of Insert Molding key factors
These key factors will make or break your insert molding operations. Be sure to keep these essential factors in mind when you create the mold and inserts for the insert molding. It can help you prevent product defects during manufacturing. Also, it can increase your success rate.
Insert Molding Services from Team Rapid
Team Rapid provides professional rapid manufacturing services for insert molding and related manufacturing processes. We can provide the best quality tools and inserts for your insert molding projects. Let us know your project requirements, and we will give you the best quote! Our services are available for all clients worldwide for all industrial applications. Email us at [email protected] today!