As industrialization continues to surge, multi-axis CNC machining emerges as a promising technology. It offers the ability to craft intricate shapes and precise features with exceptional manufacturing precision. We will show you the details of how to define multi-axis machining, how it works, what its types are, the components, the limitations, the applications, and so on. Let’s learn about it!
Table of Contents
What’s Multi-axis Machining?
Multi-axis machining is a modern machining method used in engineering processes as the complex parts to be manufactured even in simple Settings. It’s different from traditional machining (only X, Y, and Z axes) because it allows upward rotation or movement on multiple axes. Multi-axis machining makes it convenient to use advanced tools and improves production efficiency by reducing errors, which also makes the application of high-performance materials to be used.
How Does CNC Multi-axis Machining Work?
The goal of multi-axis CNC machining is to manufacture complex parts when it is used in computer numerically controlled(CNC) programming. The movement of these axes allows the tool to cut in various planes and angles, creating complex geometries. The process involves programming the machine tool’s controller to move the tool along specified paths and at specific speeds. This programming is done using Computer Numerical Control (CNC) programming languages, which are similar to be used in single-axis machines but extended to handle multiple axes.
In multi-axis machining, one not only needs to calculate the point coordinate data but also needs to get the vector direction data on the coordinate points, this vector direction is usually used to express the tool axis direction in machining, which poses a challenge to the computing power.
Different Types of CNC Multi-axis Machining
Type | Description | Pros |
3-axis CNC Machining | 3-axis CNC machining center is the most traditional type, including X, Y, Z three linear moving axes. | 3-axis CNC machining is suitable for most routine milling, drilling and cutting operations, which performs well in machining flat parts and simple 3D parts. |
4-axis CNC Machining | A 4-axis CNC machining center incorporates an additional rotating axis, typically the X-axis, alongside the three standard axes. | 4-axis CNC machining is perfect for creating parts with sloped surfaces or precise angle specifications. It enables the machine tool to rotate the workpiece during the machining process, achieving more complex geometric shape machining. |
5-axis CNC Machining | 5-axis CNC machining center consists of three linear axes (X, Y, Z) and two rotational axes (two of A, B, C). | 5-axis CNC machining has five motion axes, which can achieve all-round machining and is suitable for machining high complexity and high-precision parts. |
3+2 axis CNC Machining | 3+2-axis machines are nearly equivalent to 5-axis machines, with the primary distinction being the number of axes the machine operates on. | This is useful for machining features that require an appropriate angle. |
6-axis CNC Machining | 6-axis machining center is A CNC machine with six degrees of freedom , which can accurately position and move on three linear axes (X, Y, Z) and three rotating axes (A, B, C). | Achieving high precision in machining complex parts is possible. Six-axis machining centers are usually used to manufacture complex shaped parts, such as automotive parts, medical devices, aerospace parts, etc., which usually require machining at multiple angles to complete. |
7-axis CNC Machining | 7-axis machining center refers to the CNC machine tool, at the same time there are 7 movement axes that can be controlled and programmed. | The seven-axis machining center is characterized by its multi-axis control capability, which enables more complex machining tasks. This machine tool is usually used for parts processing requiring high precision and high complexity. |
9-axis CNC Machining | 9 axis machining center is a kind of high-precision CNC machine tool, it integrates a variety of machining functions, through an automatic tool-changing device and CNC system control, and can complete a variety of machining tasks in a single clamping. | It’s well-suited for machining intricate parts and can greatly enhance production efficiency and precision. |
12-axis Machining | 12-axis machining center refers to a CNC machining center with 12 independent control axes. | This kind of machining center is usually used for precision machining of complex parts and can carry out multi-axis linkage machining to improve processing efficiency and accuracy. |
Parts of Multi-Axis Machining Systems
Multi-axis machine tool system refers to a CNC machine tool system with multiple axes, which can complete multiple processes, such as milling, boring and drilling, in a single clamping, thereby improving the processing efficiency and accuracy .
Cutter
A tool is the contact of machine parts at work with its function is to cut, drill or grind materials according to the requirements of the job. The tool’s nature, quality, and movement impact the workpiece’s surface quality and accuracy.
Principal axis
Multi-axis CNC lathe is one of the main components of machine tools. It is a special device that must quickly clamp and rotate cutting tools and ensure the correct state is maintained for necessary cutting operations.
Multi-Axes
Multi-axis milling allows the manufacture of parts with rotating forced rotation and axial rotation end mills on many other related axes.
Multi-Axis Machining Device
It refers to a device used in the machining process, in which cutting actions are performed using many cutting tools. During the machining process, one tool is used to replace another tool that is not fixed in the device. This part improves efficiency by reducing the required manual operations and machine downtime.
Work retention device
How do these workpiece clamping devices work? They firmly grasped the workpiece to avoid any movement, thereby improving precision machining capabilities.
Multi-Axis Machining – CNC Controller
The control panel is the final component of a CNC machine tool, serving as the interface between the operator and the machine tool. CNC controllers allow operators to design and control the rapid manufacturing process, and make changes as needed to achieve desired results.
How to Choose A Multi-Axis Machining Tool for Your Project
Looking for a multi-axis machine tool that meets all the requirements and needs of the entire project? Good! Please consider the following points.
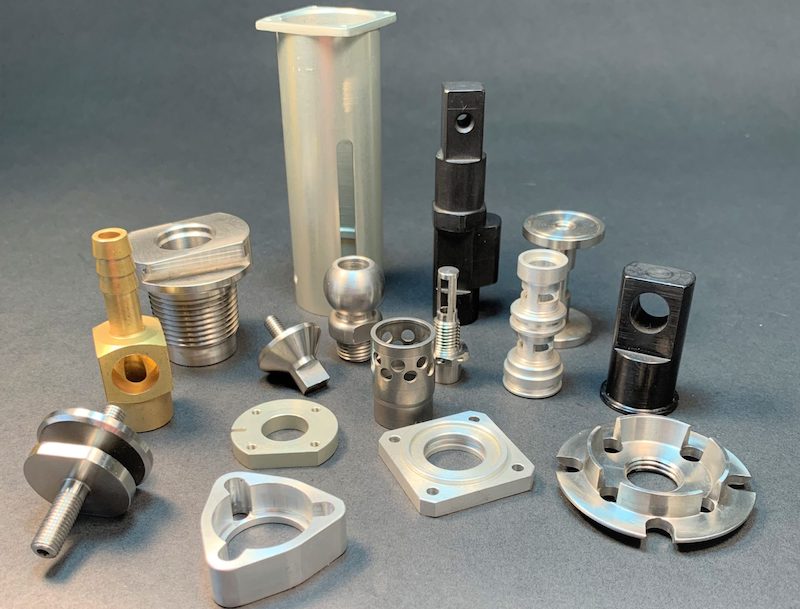
Requirement of the Project
Firstly you need to do is analyze the complexity of the parts you are measuring to manufacture. In addition, the accuracy of the material and the final workpiece should also be considered.
The Correct Number of Axes to Choose
It’s crucial to choose the correct number of axes, as this determines the machine’s capability to produce complex parts.
The Capabilities of Machine to Evaluate
Assess all machine performance specifications and parameters, including spindle speed, power, and available tools, to ensure the machine aligns with the project’s material, size, and specifications.
Rigidity and Stability of Multi-Axis Machining machine
When ensuring the quality and accuracy of parts, consider the rigidity and stability of the machine. Parts machines with good rigidity and stability could be useful for reducing quality errors.
Total Cost of Ownership to Choose
The final “total cost of ownership” that includes TCO is the cost of the machine and its maintenance, equipment, and operation. It’s possible to choose a multi-axis machine tool that will meet your needs as it is project-related if considering all these factors.
Best Tips on Outsourcing Precision Multi-Axis
Good news! You have come to the right place. To achieve expected results within acceptable quality standards, several aspects need to be considered.
- Design the components including a detailed description of dimensions, shapes, or materials, as well as any other tolerances required to complete the project. According to the design, the corresponding CAD model is developed.
- Once the CAD model has been drafted, all illustrations should be included in a specific CAM session created in some way.
- The machine needs to be set up. Once the setup is complete, the next step is to execute the program that has already been set up. At this stage, regular testing should be conducted to prevent any issues from arising.
- Identify any physical characteristics of the components involved to ensure that the finished parts comply with quality standards and specifications. This step also verifies that the machining process has been executed correctly, confirming the parts are ready for use.
You will know how to manage the entire process after you select TEAM Rapid Tooling precision multi-axis machining services. How to follow each stage with TEAM Rapid’s expertise further to enhance the normal functionality of most stages (ensuring high-quality output) in the shortest possible time.
Conclusion
Considering the above situation, multi-axis machining is very useful for industries that manufacture parts with complex shapes and features as well as high precision. It improves the accuracy and surface smoothness of manufactured parts, as well as overall productivity.
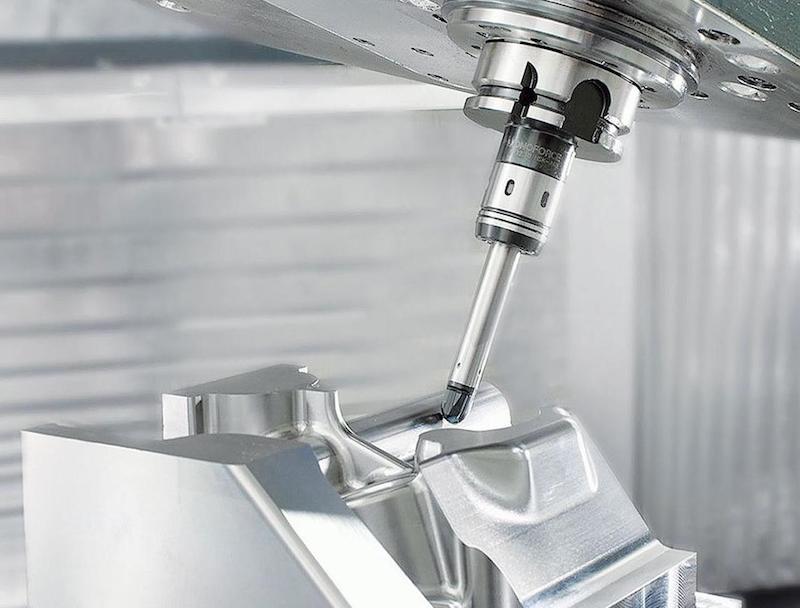
As one of the best CNC machining China manufacturer, TEAM Rapid Tooling meets such a challenge because of its precision machining services. It organizes production stages in sequence, ensuring maximum possible production quality within appropriate time windows. Thanks to high technology and advanced skills, TEAM Rapid Tooling will assist your manufacturing efforts from CNC rapid prototyping to CNC manufacturing by achieving almost impossible levels of precision and efficiency. Contact us at [email protected] today!