Investment casting is a casting process in manufacturing that uses a certain wax pattern to create a ceramic mold that you can dispose of later. Meanwhile, die casting involves casting molten metals into mold cavities by using high pressure. Both casting processes have their own advantages and disadvantages, but they both have a wide range of industrial applications. In this guide, you will learn about how to choose the right casting process for your application between investment casting and die casting.
Table of Contents
Pros and Cons of Investment Casting for Industrial Applications
There is a wide range of industrial applications for investment casting, and the applications for this casting process are unbounded. However, there are certain industries that use investment casting the most in rapid manufacturing, such as military, aerospace, oil and gas, food services, energy, firearms, and power generation industries.
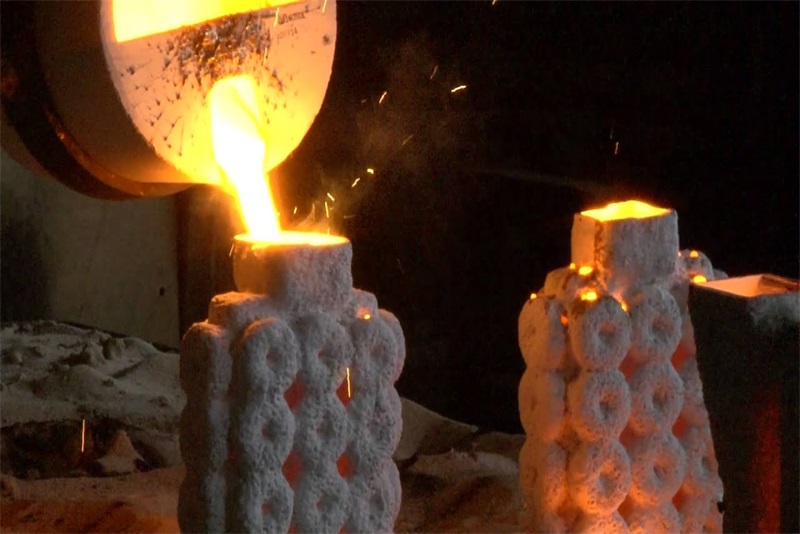
Pros
●Complex parts production.
No matter how intricate the parts you need to produce, you can get it done with investment casting. Also, you can use almost any material for this casting process, so you will have the flexibility to pick your casting materials.
●Flexible casting size.
You can use investment casting to produce both small and big parts. Investment casting offers a flexible casting size, and you can use this process to create lightweight or heavyweight parts, components, and prototypes.
●Dimensional accuracy.
Investment casting also has excellent dimensional accuracy, which is something you would need when you create complex parts. You can get the net-shape parts with investment casting, even without having to apply any additional processes.
●Casting at a 90-degree angle.
You can also use investment casting to cast parts at a 90-degree angle. There will be no additional machining process necessary, as this casting process has no shrinkage allowance.
Cons
●Complex casting process.
Investment casting is a very complex process, and there are complex steps involved in this process from start to finish.
●High costs and labor requirements.
Investment casting is also a process that is quite expensive to do, as the price for tooling and materials can go up depending on what you are making. Also, it has high labor requirements, meaning that you will need more workers to work on each project and oversee the investment casting operations.
●Long production time.
This casting process can also take a long production time since the process is very complex and time-consuming from start to finish. Compared to die casting, you will need to wait longer just to get your parts or components ready when you use this casting process.
Pros and Cons of Die Casting for Industrial Applications
Manufacturers use the die casting process to produce complex metal and mechanical objects, such as locks, gears, housings, containers, hooks, doorknobs, and many others. There’s a wide range of die casting for industrial components in our daily life, including automotive, aerospace, home appliances, computers, consumer electronics, and construction.
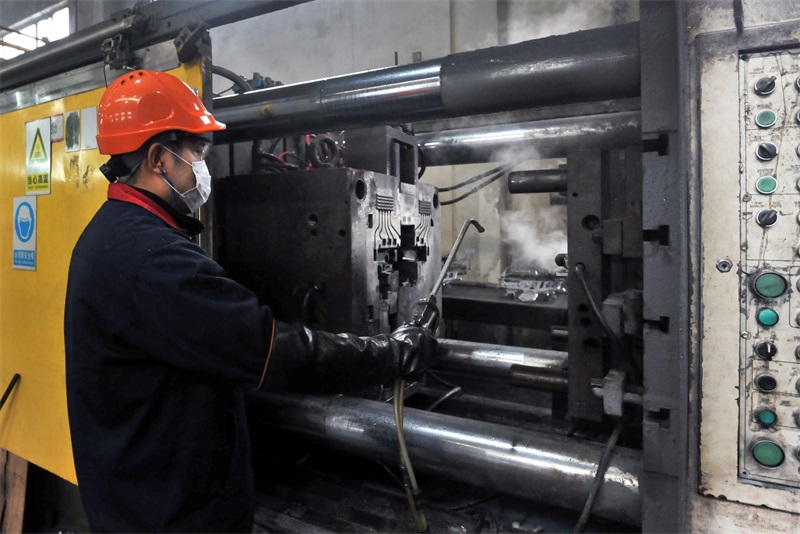
Pros
●Cost-effectiveness for large volume production.
The die casting process is quite cost-effective when you use it for large-volume production, especially for aluminum die casting and zinc die casting. The profit from the large volume production can offset the tooling and equipment cost of die casting, which can be quite expensive. Thus, die casting is best used only for large-volume production.
●High tolerance and high mechanical properties.
Die casting can also offer you high dimensional tolerance, meaning that you can maintain the dimensional accuracy of the parts, prototypes, and components you produce with this process, even in harsh environmental conditions. Also, the high mechanical properties will provide the parts, components, and prototypes you produce with the best material strength, hardness, durability, and conductivity.
●Better surface finishes.
The die casting process can also provide better surface finishes for the metal parts, components, and prototypes you are producing. With the smoother surface finishes, you can fit these parts with other parts or components with ease, without the need to perform any additional process.
●Suitable for complex designs.
With its high dimensional tolerance, you can use the die casting process to create metal die casting parts, components, and prototypes with complex designs. You can even create complex designs with thin walls on the prototypes, parts, and components you are producing. This is useful in industrial applications that require you to create complex mechanical objects to work with other components or parts.
Cons
●Porosity is bound to happen.
Porosity will happen during the die casting process because of the high-speed casting process that each metal will go through. The high-speed casting can often create gas bubbles inside the metal body, which can then create porosity on the metal materials. This porosity can then affect the structural integrity of your parts, prototypes, or components, and it can also affect its material durability.
●Short-term dies.
The dies used in the die casting process can only last for a short time. The reason is that the high melting point of the metal materials used in die casting can affect the durability of the steel dies. Thus, you will need to replace the dies from time to time during your production cycles.
●Only good for large production volumes.
The tooling process and the initial capital investment for die casting are quite expensive, which is the reason you shouldn’t use this process for small production volumes. You will only incur more expensive production costs if you use die casting in small production.
Conclusion – Investment Casting and Die Casting, Which Casting Process is Right for Your Application?
Both investment casting and die casting offer their unique casting process and different finished products, and these casting methods are suitable for a wide range of industrial applications. So, depending on your needs, you can use either the investment casting or die casting method.
You can use investment casting if you want to get the best quality for the finished products, with complex designs, the best dimensional accuracy, and no porosity. However, you will need to deal with the high production costs to use this casting method.
Meanwhile, you can use die casting if you want to produce large volumes of products with the best cost-to-value ratio. The quality of most finished products will be excellent enough for you to use, but there will be risks of porosity in the parts you are producing with this method.
So, depending on your needs, you can consider all the pros and cons of the investment casting and die casting methods before deciding to pick which one is best for your application. Looking for a manufacturer for your casting projects? TEAM Rapid offers the very beginning rapid prototyping services to later mass production services under one roof, Contact our team to get a free quote today!