Nowadays, in such a fast-paced global market, mold design must evolve to meet contemporary industrial needs. With products having increasingly shorter lifespans, in order to maintain a competitive edge, mold manufacturers should provide innovative solutions. Here comes the injection molding side action which offers a transformative solution for managing complex geometries and challenging tricky undercuts.
As designers and engineers, what should they do first? They must understand how to fully unlock the potential of the side actions. If you’re going to explore everything you need to know about injection molding side action, including how it works, various types for different applications, and tips on improving precision molding skills, then you’ve come to the right place! Let’s read on!
Table of Contents
Brief Introduction of Injection Molding Side Action
Injection molding side actions are specialized components, also called “features”, integrated into the mold to facilitate the formation of undercut geometries. Owing to their specific characteristics, they cannot be produced with a traditional straight-pull mold. Making full use of the function of side actions for the mold design, the material can flow around them to create the undercut features.
The injection molding side action can enhance design flexibility by enabling the creation of intricate part geometries, such as holes for cables or slots for assembly. It is specifically designed to address the challenges posed by the undercut geometries in traditional straight-pull injection molding, where the direct action of the mold is inadequate to release the part with undercuts. The injection molding side action happens to overcome this limitation by adopting a cam-driven mechanism that retracts the mold surface and promotes safe part ejection.
However, careful consideration is quite needed before you decide to employ side actions. Once a part is molded, side actions must be removed, either manually or automatically, to allow for part ejection. Moreover, the key is to assess whether they are necessary or whether alternative design strategies, such as incorporating slot features, can also achieve the desired results.
Pros
- Greater design flexibility
- Reduce the need for secondary operations
- Lower overall project costs
Cons
- Increase the complexity and cost of the mold
How Does injection molding Side Action Work?
Side actions can create complex geometries featuring undercuts that standard two-part molds cannot achieve. These undercuts involve inward-facing angles or projections, thus making part removal difficult without potential damage.
In order to effectively address this, CNC machining manufacturers often employ lateral movements, , incorporating sideways sliding or cam action to interact with the mold cavity when it is closed. Angle pins, crucial components in injection molding, are used in conjunction with side actions to provide precise guidance for accurately positioning them to create undercuts. This approach makes it easier to create an undercut area on the part. These pins drive the side actions into a specified place during mold closure.
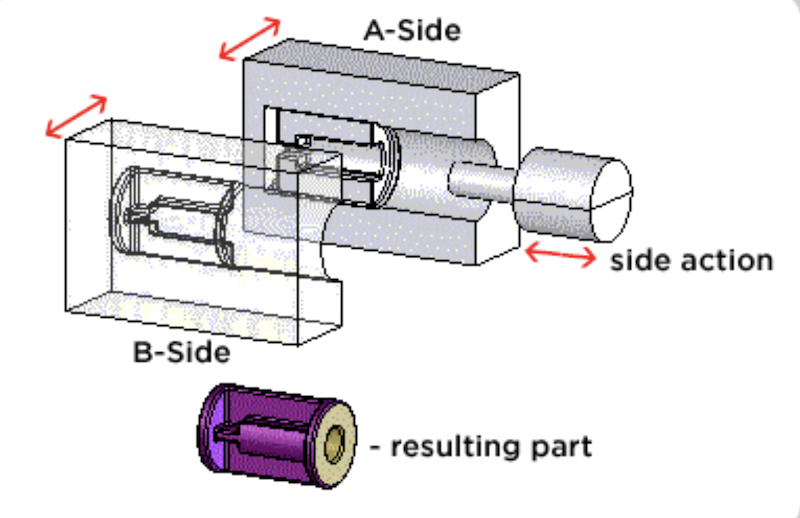
After plastic molding, the side action is controlled to shrink, so that the parts are ejected smoothly and without interference. Hydraulic or mechanical actuators handle this process, which ensures smooth and seamless operations. By retracting side actions before the part ejection, damage to the molded elements with undercuts can be avoided. This may contributes to the efficient production of parts and crafts of high quality with complex details.
Different Types of injection molding Side Actions
When side actions are unavoidable in the injection molding process, it’s crucial to understand which type of side action helps to minimize injection mold costs and boost better project performance. Manufacturers like TEAM Rapid can offer professional guidance on the best option for your particular injection molded part, as each type comes with different cost impacts on your tooling costs. Here are different side action types for your consideration.
injection molding side action: Cams
Cams are ingenious mechanisms that open the mold by removing the undercut mold surfaces from the part. A common cam design involves an angled pin that controls the movement of the action, reflecting the speed at which the mold is opened and closed. This design allows for more complex geometries in part design without external adjustment or operator intervention.
They facilitate the production of components with complex details that would be challenging with traditional molding methods, offering enhanced precision and accuracy in part design. In addition, they minimize the necessity for additional processes such as drilling or machining and can be used alongside other mechanisms such as lifters or sliders. However, it’s crucial to keep monitoring the cam pins during the whole production cycle. Due to the compressibility of steel, excessive load can cause pin deformation, impacting part quality. Regular maintenance and inspection of cam pins are essential for maintaining consistent performance and part precision.
Lifters
In injection molding, lifters play a crucial role in forming and releasing internal undercut features, such as internal threads or bosses that require a specific orientation. Lifters are especially useful for parts with complex internal geometries, offering mold design flexibility by eliminating the need for angled pins, thus minimizing the risk of pin deformation.
However, internal features such as drafts, bosses, and ribs may need to be modified to accommodate the movement of the lift. In addition, the design of injection mold lifters can be complicated beyond your expectation. This requires careful planning and testing. Besides, the design and timing of the ejector plate will empower proper takeoff and retraction.
injection molding side action: Sliders
Unlike lifters, this kind of side action is designed to manage and release external undercut features. They provide flexible actuation methods such as cam-driven, solenoid-driven, or hydraulic systems, making it possible to create parts with intricate external designs. Sliders in injection molding are critical for manufacturing parts with external undercuts or features that need to be detached without affecting the main core and cavity, such as external threads or features that require precise positioning. This approach minimizes the necessity for additional operations like drilling or machining.
However, there is no doubt that slider design can be complex. It needs meticulous planning and thorough testing. Proper timing and coordination with other mold functions are essential to guarantee smooth slider engagement and disengagement.
Unscrewing Action
Unscrewing actions in thread injection molding, no matter automatic or manual ones, enable the precise formation of threaded features by carefully managing the screwing process. This ensures that the high quality of thread can be achieved and the damage can be prevented during each cycle. While essential for consistent thread production, adopting hand-loaded cores might be a more cost-effective choice for smaller production runs.
Parts with threaded features like screws and fasteners may be difficult to remove in injection molding. External threads that are perpendicular to the draw line can be seamlessly incorporated into the mold design easily. However, both internal and external threads require an external unscrewing mechanism. This mechanism is placed into the mold before the injection process begins and is then meticulously removed from the part once the material has solidified.
Collapsible Core
Collapsible cores are instrumental in releasing circular undercut features and the operation is similar to that of lifters. They retract inward to create the necessary clearance for ejecting parts. In the molding process, components are shaped directly around the core, and once the material solidifies, the mechanism retracts. This makes it easy to remove actions and parts from the mold. Therefore, they are particularly suitable for the features with sizable internal threads or circular undercuts. Also, collapsible cores can be employed to produce threaded features, enhancing their versatility in molding applications.
Types of Side Actions | Pros | Cons | Applications |
Cams | Complex movements possible, accurately positioned, versatile for various designs, high durability | More expensive, challenging & time-consuming process | Complex geometries, high-volume production |
Lifters | Simple structure, cost-effective, high demolding force | Limited precision, wear and tear over time, not ideal for complex geometries | Undercuts, holes, recesses, large items with simpler geometries |
Sliders | Smooth movement, low friction, straightforward to design | restricted movement, unsuitable for complex geometries | Basic structures such as slots, grooves, and ribs |
Unscrewing Action | Accurate control, robust durability, and well-suited for intricate threading tasks | Higher costs, intricate design, skilled labor required | Consistent thread production, threaded components like screws, bolts, and nuts |
Collapsible Core | Allow for negative draft, precise control, exceptional durability | Higher cost, complex design, regular maintenance | Holes, pockets, recesses, complex geometries with negative draft |
Tips on Manufacturing of Side Action Molds
The production of side action molds covers various key stages, from design and to assembly. You need to pay enough attention to details in each stage to ensure that the final product meets the required standards and best performance. Here are some useful tips on side action molds, from design considerations to manufacturing tips.
Design Considerations
Undercut features
The side actions are essential to create undercut geometries that cannot be achieved with straight-pull molds. They allow part features such as holes, slots and recesses to be formed.
Perpendicular Movement
Ensure that the side movement is perpendicular to the direction of the main opening and closing mold. This movement is usually guided by angled pins or cams.
Parting Line Placement
Positioning the side action on the external parting line of the part is essential for efficiently controlling the mold’s opening and closing operations.
Size and Travel Restrictions
Note the size limits and travel distances of cam features. These constraints may affect the design and functionality of the side actions.
Manufacturing Tips
Select Suitable Mold and Component Materials
Choosing the appropriate materials for the mold and side action components is vital for optimal performance. These materials must exhibit the expected strength, durability, and thermal characteristics to withstand the rigors of the injection molding process.
Machining and Fabrication
This phase demands meticulous machining and fabrication methods to ensure exact dimensions and tolerances. CNC machines and other specialized tools are employed to achieve the necessary precision. It’s important to consider surface finish and texture for optimal performance.
Heat Treatment
This phase necessitates careful management of temperature and timing to attain the preferred material characteristics. Manufacturers apply heat treatment methods such as annealing, quenching, and tempering to enhance material strength, hardness, and thermal conductivity.
Assembly
Accurate alignment and positioning of components at this stage help to ensure precise movement and operation. Clearances and tolerances are critical to smooth operation, as excessive gaps between components may affect precision and accuracy.
TEAM Rapid: Your Best Mold Maker
When it comes to a plastic injection mold maker, it is necessary to choose a partner with rich experience, advanced technology and a skillful team. In other words, a dependable collaborator can deliver top-notch molds tailored to match your exact needs and deadlines. TEAM Rapid comes as your best mold maker.
- We prioritize quality and innovation for better customer satisfaction. we keeps delivering high-quality molds for your expectations.
- We offer flexible customization options for side action injection molding to better accommodate your unique part designs. With quality materials, advanced rapid manufacturing technology and professional engineers, it ensures efficient production cycles to reduce lead times and on-time delivery to satisfy your production schedules.
- We provide clear pricing to avoid hidden costs, responsive after-sales support, and open lines of communication.
For professional injection molding services that drive business success, consider partnering with a trusted mold maker like TEAM Rapid.

Conclusion
In conclusion, mastering the intricacies of injection molding side actions is essential for achieving outstanding results in your manufacturing projects. This process makes it possible to realize complex geometric designs, though it poses challenges for mold removal. Luckily, manufacturers like TEAM Rapid help you overcome different challenges during the whole product lifecycle, from prototyping to production. Try contacting TEAM Rapid for professional project ideas NOW.