Injection Molding Color is important as color for injection molded product could be a huge difference in the success of the product. For example, consumer products, different colors and appearances differentiate your products from the one next to them on the shelf. The right color of injection molded products can take a person from just looking to must have. When using the color in the right way, it can strengthen your brand and build reputation in the eyes of your customers.
Color is not only aesthetics, but also serve a functional purpose of the parts. For example, safety products, they often must have bright color which will be extra visible. Important parts in electrical applications, they will have different color to identify and differentiate with others. At TEAM Rapid, we will meet customers’ need if they have requirement for injection Molding Color.
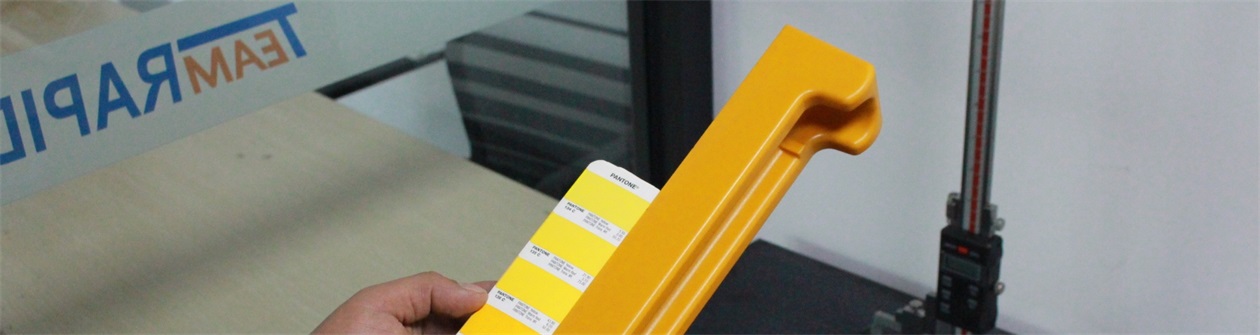
Plastic injection Molding Color technology has evolved to a place, if not all, these kinds of applications can be met with ease. The versatility of plastic injection molding means that manufacturers and inventor have more freedom than before to think outside the box for the color and appearance of the products.
There are many factors need to be considered when exploring plastic injection Molding Color. How to control the color in the most important part. It is not enough to look at the pantone chart or list of color options and pick up one. At TEAM Rapid, we often have unique customization requirement, so the color control is very important. Color control is important in reducing the time of iterations and decreasing the number of incorrect yielded which will lower your product cost.
To control the injection Molding Color, you need to understand the types of technology, how the technology works and the different strengths of the technology. The more information your have, the better equipped your will be an active role in developing and perfecting the injection Molding Color.
Table of Contents
What to consider when controlling injection Molding Color?
1.Liquid or solid
Depending on the chosen materials and the type of effect which you are looking for in its color, you many choose a solid or liquid colorant. Each of them is compatible with certain types of plastic and yields different effects. Liquid colorants are suitable for translucent or semi-transparent effect. The intensity of the effect is be increased or decreased by the amount and concentration of the colorant added. Liquid colorant can produce flowing or glowing effect. It is suitable for PET and PVC.
Solid colorant which mixed with the base material offers an opaque look. Similar to liquid colorant, the concentration of the solid colorant addition can be adjusted to offer opaque appearance or lighter color.
2.Color or appearance
There is more to a desired color addition than the color itself. Customers will say they want your part to be blue. Manufacturers will ask it is a light blue, organic looking, or dark blue? A pantone code which serves as a good instruction of different between color or appearance. Appearance of the product is highly subjective. It means something different to customers which many things need to be considered in service of the goals and requirements of the products.
TEAM Rapid, as a professional injection molding manufacturer, we will listen to customers’ ideas of the appearance of their products. We will adjust the color if necessary to offer what customers have in mind. Even the experienced plastic colorant mixers are not able to explain their formulation or methodology exactly. They just know how it work. If you understand the appearance of the product is more important than the color, you are helping your injection molding manufacturers to make the results you need.
3.Acceptance standard
It is impossible to one hundred percent control your injection Molding Color because too many variations come into effect. Even use the same machinery, temperature, operator, colorant formulation and concentration will impact the appearance of the parts.
To offer an efficient and productive yield, understanding and reviewing variations before production run is important. Think about if the overall effect what you want, if the color is exactly what it was supposed to be, if consumers will literally see the products differently than you do. This will maintain perspective if you are worried about the differences in color saturation or opacity.
Acceptable color variation range is around 10% – 30%. The more leeway is allowed, the higher percentage of accepted parts you will have. This will reduce waste.
How to use color matching process to make customized injection molded parts?
In the manufacturing industry, custom color matching does not mean referring to the paint color you are choosing for your house. Product designers are working for companies which often need their supplier to make plastic injection molded parts which are pantone color matched to company requirement such as branded color. At TEAM Rapid, our injection molding service provide color matching on customer-offered pantone number and customers’ original sample.
At TEAM Rapid, our injection Molding Color matching process is simple and fast. Color-matching process offer many benefits.
1. Injection Molding Color matching process reduces the time to develop the color, which enable to launch the new products to the market faster.
2. Injection Molding Color matching process allows to customize branding and enhance recognition.
3. Consistent quality and colorant properties can be achieved by injection Molding Color matching process.
4. Injection Molding Color matching process reduce color-matching costs and colorant inventory.
At TEAM Rapid, our custom injection Molding Color matching process enable us to make custom colors for injection molded plastics. We combine liquid or solid colorants and software which help to us to match and produce color on site. At TEAM Rapid, for best result with color matching, we use pantone or PMS color, no sample is required. If customers want to use their own sample part, the part must have a flat area and cannot be smaller than a quarter to make sure it can be scanned by our spectrophotometer. When we receive color matching order, our engineers will send a plaque of sample for approval. Contact us today to learn more now!