Plastic injection molding, a widely adopted manufacturing technique, produces precise plastic components with impeccable accuracy. Unveiling the financial aspects, this article delves into the multifaceted factors influencing plastic injection moulding cost. From mold intricacy to material selection and production volume, we explore the intricacies of pricing in this dynamic industry.
Table of Contents
- 1 Factors Impacting the Plastic Injection Moulding Cost
- 2 Unveiling the Cost Driver: The Mold in Plastic Injection Moulding Cost
- 3 Cost Distribution in Injection Molding: An Economical Solution for Mass Production
- 4 The Impact of Material on Plastic Injection Moulding Cost
- 5 Optimizing Labor Costs through Automation in Plastic Injection Molding
- 6 Conclusion of Plastic Injection Moulding Cost
Factors Impacting the Plastic Injection Moulding Cost
One of the primary influencers of plastic injection molding costs lies in the size and complexity of the mold. A basic mold producing small parts may incur expenses ranging from $1,000 to $6,000, while a standard mold fitting in one’s hand could cost approximately $12,000. As molds increase in size and intricacy, expenses escalate, with large, multi-cavity steel molds demanding a substantial investment exceeding $100,000.
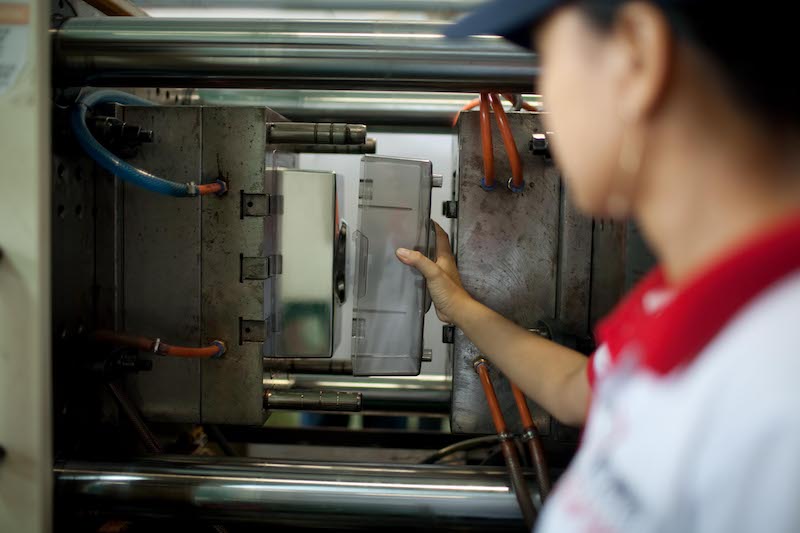
Production Volume and Economies of Scale Affects on plastic injection moulding cost
The cost of plastic injection molding is also heavily influenced by the production volume. Utilizing the concept of economies of scale, the total mold cost gets distributed across the production quantity, making the process economically feasible for mass production. As production volume rises, the cost per part decreases, rendering plastic injection molding a cost-effective solution for manufacturing large quantities of components.
Material Selection affects on plastic injection moulding cost
The choice of materials impacts the overall cost of the plastic injection molding process. Various thermoplastics have different price points, and some materials are expensive than others. Therefore, the selection of the appropriate material directly influences the financial aspect of the injection molding endeavor.
Unveiling the Cost Driver: The Mold in Plastic Injection Moulding Cost
At the heart of plastic injection molding lies the pivotal component, the mold/rapid tooling, often referred to as the tooling. This custom-made apparatus shapes molten plastic into the desired form, making it a critical factor in the overall cost assessment.
Factors Influencing Mold Costs
The expenses involved in designing and crafting a mold hinge on several key factors. The required production volume, intricacy of part design, mold material, and the chosen mold creation process all play vital roles in shaping the final price.
Diverse Cost Spectrum
Mold costs exhibit a broad range, catering to various project requirements. Simple 3D-printed molds for low-volume applications can bear a price tag as humble as $100. In contrast, crafting complex molds for high-volume production can escalate to a substantial investment of around $100,000 or more.
Illustrative Examples
For instance, a basic mold rapid manufacturing small parts might fall within the $1,000 to $6,000 range, while a standard mold, fitting comfortably in the hand, may entail around $12,000. In contrast, large, multi-cavity steel molds, with their extensive capabilities, can demand costs exceeding $100,000.
Cost Efficiency and Scaling
Though the mold entails significant initial fixed costs, the subsequent plastic injection molding process offers compelling advantages. The utilization of inexpensive thermoplastics, swift cycle times, and the potential for automation and economies of scale contribute to low variable expenses. As production volume surges, the cost per part proportionately decreases, rendering plastic injection molding a cost-effective solution for mass-producing plastic components.
Cost Distribution in Injection Molding: An Economical Solution for Mass Production
The cost of the mold constitutes a fixed start-up expense in plastic injection molding. While this initial investment is significant, its implications in mass production are game-changing.
The Advantages of Production Volume
As production volume escalates, the cost of the mold gets distributed across the increasing number of parts manufactured. This distribution transforms plastic injection molding into an affordable option for mass production.
A Preferred Mass-Production Process
This cost distribution model amplifies the appeal of plastic injection molding for mass-production endeavors. As production volume surges, the fixed start-up costs get spread across a larger quantity of parts, driving down the cost per part, and thereby establishing a highly cost-effective manufacturing process.
The Impact of Material on Plastic Injection Moulding Cost
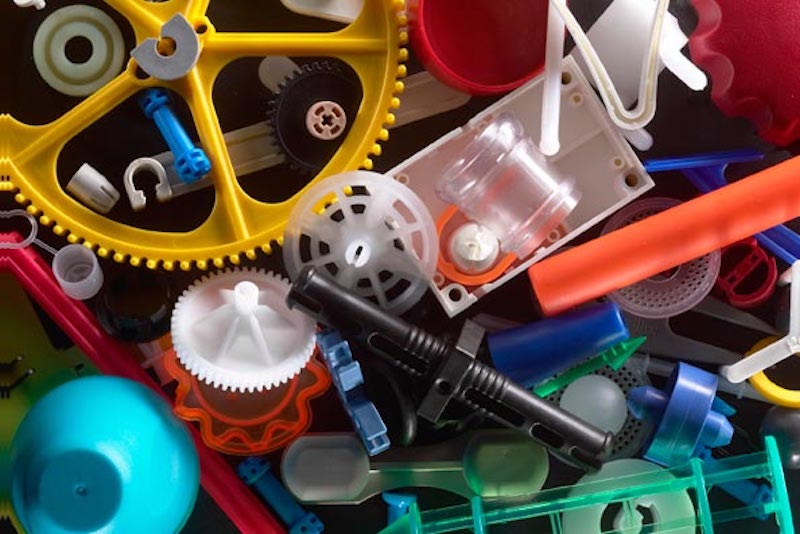
Thermoplastics Selection
An influential determinant in the overall cost of plastic injection molding lies in the selection of raw materials. An array of thermoplastics, such as ABS, PS, PE, PC, PP, and TPU, serves as the foundation for this manufacturing process. The choice of material is contingent upon the specific properties desired in the final part and rapid prototypes, encompassing aspects like strength, flexibility, and resistance to heat and chemicals.
Diverse Price Range
Each thermoplastic material comes with its unique price tag, with some being more economical than others. For instance, materials like ABS and PP tend to be relatively cost-effective, while premium options like PC and TPU may command higher expenses. The material selection significantly influences the overall cost of the injection molding process.
Additional Preparations
Beyond the raw material cost, additional expenses may arise from preparatory steps before injection molding. Certain materials necessitate drying or the inclusion of additives to ensure optimal performance during the manufacturing process. These supplementary measures can contribute to the overall cost of materials in plastic injection molding.
Striking the Right Balance
In conclusion, material costs exert a notable impact on plastic injection molding expenses. By making well-informed material choices aligned with specific project requirements, manufacturers can achieve a delicate equilibrium between cost-effectiveness and superior performance for their injection-molded parts.
Optimizing Labor Costs through Automation in Plastic Injection Molding
Labor Costs: A Consideration in plastic Injection Moulding cost
In the realm of plastic injection molding, labor costs hold significant weight in shaping the overall expenditure. The multifaceted process necessitates skilled labor to execute crucial tasks, encompassing mold design and construction, material preparation, machine operation, and final part assembly. Each step demands expertise and adds to the overall cost.
Harnessing the Power of Automation
Automation emerges as a transformative approach, mitigating reliance on manual labor and enhancing operational efficiency. Contemporary injection molding machines employ computer-controlled systems, minimizing human intervention during the injection process. Moreover, automation extends to other aspects, including material handling and part finishing, streamlining the entire production workflow.
Diminishing Labor Dependency
The strategic integration of automation enables manufacturers to reduce labor requirements across multiple stages of injection molding. Automated machines adeptly manage repetitive tasks, freeing skilled labor to focus on specialized roles requiring their expertise. This reduction in manual labor contributes to a cost-effective approach.
Fostering Cost-Effectiveness
Automation’s impact on labor costs culminates in heightened efficiency and enhanced cost-effectiveness. Reduced labor needs translate to heightened productivity, resulting in shorter cycle times and increased overall output.
Conclusion of Plastic Injection Moulding Cost
The cost of plastic injection molding is shaped by factors like mold size and complexity, production volume, material selection, and labor expenses. Leveraging automation proves instrumental in reducing labor requirements and enhancing overall efficiency, thereby optimizing the cost-effectiveness of the process. By thoroughly considering these aspects and embracing automation, manufacturers can effectively navigate the cost dynamics and achieve successful outcomes in plastic injection molding while ensuring prudent financial decisions.
Besides from injection molding, TEAM Rapid also offers rapid prototyping, die casting, and sheet metal fabrication to meet your projects needs. Contact our team today to request a free quote now!