CNC prototype processing takes from 1 day to 1 month depends on the quantities, complexity, material, and finish. For business owners and engineers, grasping CNC machining’s essentials is crucial. A frequently asked question is, “What is the duration of CNC machining?” This article covers all you need to know about CNC machining’s time requirements and the factors influencing its duration.
Table of Contents
- 1 CNC Machining Overview
- 2 CNC Machining for CNC prototype processing Duration Insights
- 3 CNC Machining methods in CNC prototype Processing
- 4 Value-added Services for CNC Prototype Processing
- 5 CNC Prototype ProcessingMachining Duration Influences
- 6 Accelerating CNC prototype Processing Machining
- 7 Contact Us
CNC Machining Overview
CNC machining, a method where computers guide machinery via encoded instructions, starts with translating a design into machine code. This code directs the CNC machine in fabricating items from materials by cutting or shaping. The entire process entails designing with CAD software or scanning an object, programming the design into machine-understandable code, preparing the machine with necessary tools and material alignment, executing the operations to alter the material, and finally, cleaning and refining the product for quality. The duration of CNC machining hinges on these integrated steps.
CNC Machining for CNC prototype processing Duration Insights
The completion time for CNC prototyping machining projects varies significantly, influenced by the design’s complexity and the material’s hardness. Simple designs are quicker to complete due to less complex machining paths, whereas detailed designs take longer. Additionally, machining time is shorter for softer materials (like some plastics or softwoods) compared to harder ones (such as metals or hardwoods), as the former requires less effort to machine.
The operational speed of a CNC machine, which depends on the tool and material type, also affects project duration. Typically, CNC machines work at around 1 foot per minute, though this can differ. The length of the material and the amount of material that needs to be removed for the desired product’s depth and shape are crucial. Hence, the material’s dimensions and the machining precision needed significantly influence the total machining time.
CNC Machining methods in CNC prototype Processing
The timeframe for creating your CNC machined part is impacted by the specific machining method required. Common choices include:
- Milling: Involves a rotating tool acting on a fixed piece.
- Turning: Where the piece itself rotates against a stationary tool, often on lathes.
- Drilling: The creation of holes using a cutting tool.
- Boring: Material is removed to form an internal cavity.
- Sawing: A saw blade makes a narrow cut.
- Broaching: Utilized for shallow material removal.
The complexity of these methods varies, with some requiring more time due to their intricate nature.
Value-added Services for CNC Prototype Processing
Moreover, CNC shops offer value-added services that enhance the production process. Additionally, value-added services that improve the production process are provided by CNC shops:
Project management in CNC prototype Processing
This service offers thorough supervision from the start of the project to its completion, stressing the significance of adhering to the project’s scope, guaranteeing quality, and fulfilling deadlines. It coordinates all stages of the CNC machining process to complete each phase efficiently and within budget.
Procurement
This crucial step involves selecting and acquiring the best quality materials for the project. It ensures access to premium materials at competitive prices, which contributes to the superior performance and durability of the final machined parts.
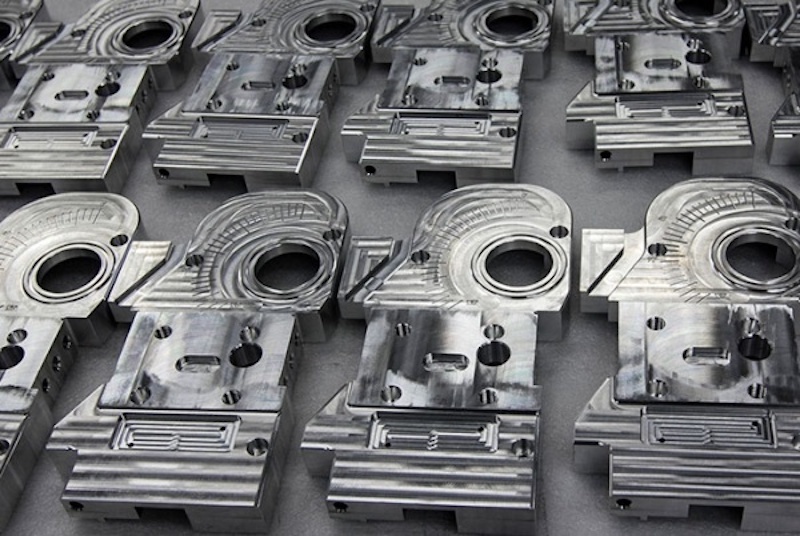
Engineering in CNC prototype Processing
Engineering services are key to optimizing the design, selecting appropriate tools, and precise CNC programming, leading to enhanced manufacturing efficiency and product quality. It involves customizing strategies for each project to maximize CNC machine capabilities through design adjustments and accurate programming.
Quality Control
Quality control measures, including control plans, FMEA, supplier audits, and PPAP, are rigorously applied to maintain high standards. These procedures guarantee consistency, compliance with specifications, and defect-free machined parts.
Integrating these services streamlines the CNC machining process, potentially reducing production times. The synergy between project management, procurement, engineering, and quality control optimizes every aspect of machining, achieving faster results without sacrificing quality.
CNC Prototype ProcessingMachining Duration Influences
Several main factors impact the time needed for CNC machining:
Complexity in CNC prototype Processing
Simple parts are faster to produce than those with detailed, complex designs. Production times can range from minutes for basic shapes to hours or days for intricate models.
Material
The machining speed varies with material choice—plastics tend to be quicker than metals. Softer metals like aluminum and brass machines are faster than harder ones like stainless steel due to the latter’s increased resistance.
Machining Time Factors in CNC prototype Processing
Machining time varies by process, with some, like CNC turning, being quicker and more cost-effective for cylindrical shapes than CNC milling.
Machine Capacity and Availability
Larger machines can handle bigger or multiple parts at once, shortening overall production time. However, equipment availability and order backlogs can affect lead times.
CNC Machine Type in CNC prototype Processing
The efficiency of CNC machining is heavily influenced by the machine’s speed and technology. Modern, high-speed machines equipped with sophisticated software can complete tasks more rapidly than older models.
Order Volume
The quantity of low volume manufacturing to mass production parts required influences machining duration, with larger orders needing more time due to the increased number of parts to be machined.
Accelerating CNC prototype Processing Machining
Although it’s impossible to skip essential steps in CNC machining, you can adopt measures to hasten the process:
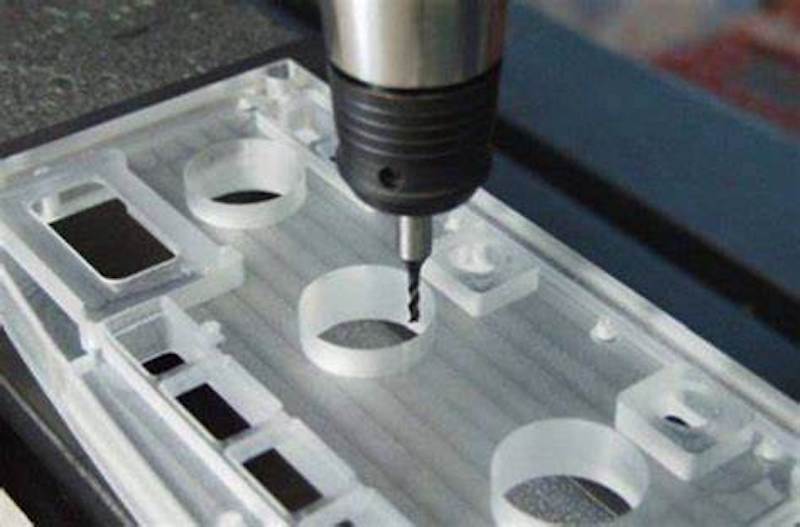
Design Simplification
Streamlining designs removes complex elements that slow down programming and machining. A simpler design leads to faster production without compromising the end product’s quality or function.
Tool Path Optimization
Strategically planning the tool’s movement reduces machining time by minimizing unnecessary cutting paths. This not only speeds up production but also prolongs tool life by reducing wear.
High-Speed CNC Prototype Processing Techniques
Leveraging advanced technology for high-speed machining boosts production rates and completes jobs quicker, especially for complex parts. This technique maintains precision and quality while increasing efficiency.
Quality Tooling Investment
Using high-quality tools enhances performance and durability, reducing the need for replacements and allowing for faster cutting speeds. This investment cuts machining time and often results in cleaner cuts, decreasing the need for further finishing.
Efficient Setup CNC prototype Processing
Reducing setup time for each job significantly lowers overall machining time. Optimizing setup, such as utilizing quick-change fixtures, minimizes downtime and enhances productivity across the workshop.
Ultimately, while CNC machining times can greatly vary due to several factors, applying these optimization techniques can help reduce production timeframes without sacrificing part quality. When seeking CNC machining services, opting for a provider known for both excellence and efficiency can be beneficial.
Contact Us
TEAM Rapid provides custom rapid prototyping, CNC machining services, and injection molding services to engineers, product developers, designers, and more through our vetted network of 10,000+ suppliers. Contact us today for a rapid manufacturing project!