It is commonplace for aluminum die casting parts to have problematic quality. A wrong configuration in your die casting equipment can make or break your entire production.
Table of Contents
The Problems with Aluminum Die Casting Parts
Die-cast aluminum won’t always come out scratch-free. There are some issues you need to deal with in this manufacturing production. Check for these concerns before proceeding further. Here are the problems you can find on aluminum casting parts:
Aluminum Die Casting Parts Cracks and Deformation
Cracking is a commonplace material defect in die-casting aluminum. The cause of this phenomenon is the wrong element you put for the alloying or melting process. The cracks on the aluminum die-casted part can cause deformations that can ruin the component’s overall look.
Porosity Caused by Gas
Porosity means the formation of small holes inside the aluminum die-cast component. Trapped gas during the casting process can cause this problem. It can weaken the overall structure of the aluminum die-casting part.
Flow Marks
Flow marks can appear on the surface of the die-casted aluminum part. It will make the component look non-polished and bad for aesthetics. The flow mark patterns will depend on the flow direction of your molten material during the die-casting process.
Network Cracks
Network cracks are worse than just plain cracks on the die-casting aluminum component. These cracks appear as interconnected lines on various parts of the die-casting component. It creates a poor appearance for the aluminum die casts. Also, it will build poor structural integrity.
Interlayers
Problematic interlayers can cause poor bonding within the aluminum structure. The die-casting process can cause unnecessary interlayers that can ruin the material characteristics of the component. It can further lead to poor component quality.
Inclusion
It is a common problem that can happen when external materials create holes within the body of the die-casted aluminum component. This problem can also appear on the aluminum component’s surface. It destroys the purity of the die-casted aluminum component and might lead to other unforeseen issues during application.
Dents on Aluminum Die Casting Part
These defects form dented shapes around the aluminum die cast’s surface. These dents can deform the component’s shape and render it useless. The dents can get worse when you use an improper cooling process.
You can improve the quality of your cast components by dealing with these commonplace problems. These problems are preventable. It will depend on how you run the die-casting process.
Enhance Aluminum Die Casting Parts’ Quality
Defects can lower the overall quality of your aluminum die-cast component. It’s best to take precautions and ensure your die-casting process is well-prepared. Optimize your die-casting method with these tips:
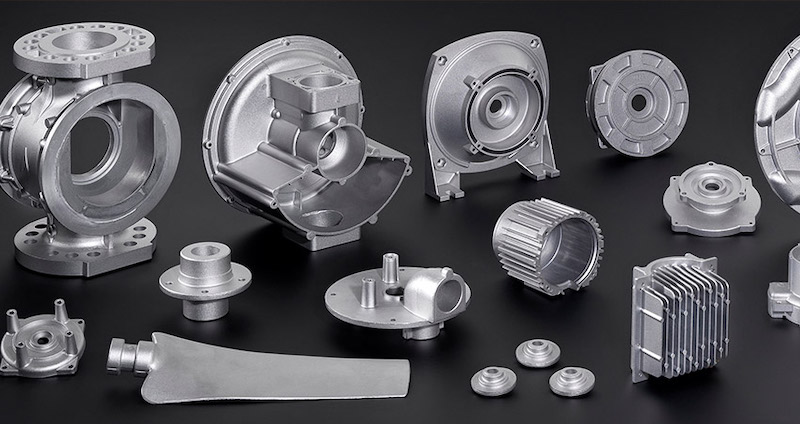
Induction Melting
Induction melting gives you a much more refined die-casting process by controlling the temperature of the materials. Perform this process before pouring the melted materials into the die-casting mold. It allows you to provide the precise temperature for the die-casting aluminum, resulting in improved results.
Surface Polish
Surface polish will allow you to fix flow marks and other surface-level defects in aluminum die casts. You can perform the surface polishing procedure after completing the cooling down process. Apply various surface polishing options depending on the polish quality you want to achieve. It can improve the component’s appearance.
Aluminum Die Casting Parts’ Design Optimization
Optimizing your component’s design can also help with improving its overall quality. Complex geometric designs can cause problems during the die-casting process. It can increase material incompatibility and lower the bonding level. Optimizing your component’s design can often remedy this problem and keep your product’s quality at the highest level.
Parting Line Management
Wrong parting lines will prevent the molten metals from going smoothly to the die-cast mold. Managing the parting lines can help maintain the die-casting aluminum’s quality for the long term. Also, better parting lines can help prolong the life of the die.
Fillet Addition
A fillet can help handle sharp corners in your aluminum die-casting design. Sharp corners can lead to defects and incompatibility during the assembly process. Using a fillet will prevent any problematic design choices from creating defects in your aluminum die-cast. It will result in a smoother removal of the component.
Optimize Solidification
Many problems can arise in the aluminum die-cast parts during the solidification process. Poor solidification will lead to more potential defects for the component. Optimize the solidification process using machine learning to minimize defects and maintain high-quality standards.
Try these optimization steps to enhance your component’s quality during die-casting. One small step can bring better-quality components for rapid manufacturing and mass production.
Cast Aluminum vs. Die-Cast Aluminum
Cast aluminum and die-cast aluminum are similar. You can consider the die-cast aluminum as the upgraded version of cast aluminum. Here are some insights on their differences:
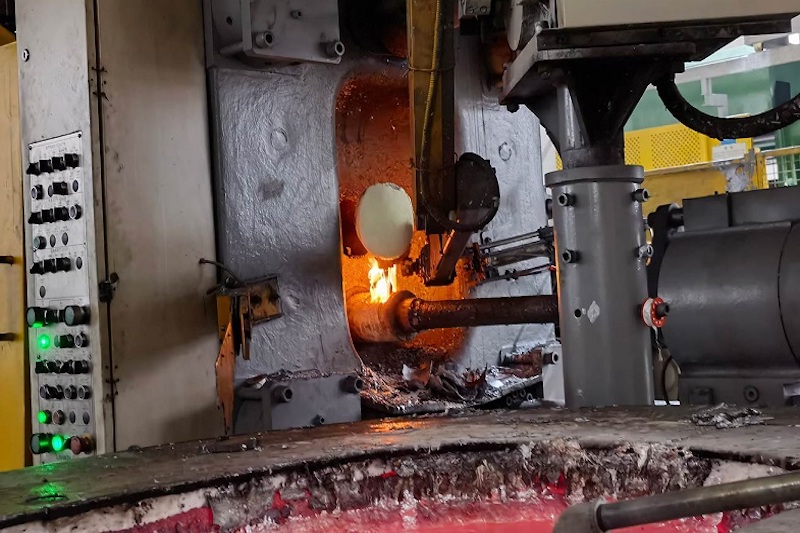
Material Components
You can only use molten aluminum components in the cast aluminum process. Meanwhile, die-cast aluminum allows you to use molten aluminum and other metals in the die-casting process. Incorporating different metals with aluminum materials helps you create the best bonding strategy for these materials. It will result in better-quality aluminum die-cast parts.
Cast Pressure
Cast aluminum uses a regular pressure system to cast molten aluminum materials. Meanwhile, die-cast aluminum requires a high-pressure casting system for this production process. The high pressure from the die-casting process allows a smoother flow for the molten materials.
Geometrical Shapes
Cast aluminum allows you to create aluminum components with simple geometrical shapes. Meanwhile, die-cast aluminum can offer more complexity for your geometrical designs. It can handle more complex shapes with more features.
Cast aluminum and die-cast aluminum have a similar working process, except for these differences. You can choose whether to incorporate other materials into your product design. It will also depend on the overall designs of your component, and the die design.
Conclusion
You can always find a small percentage of die cast keychains, and components to be defective and unusable. The primary concern is ensuring these defects stay at the lowest amount. You can follow the tips to improve your die-cast aluminum quality to keep the defect percentage near zero. Also, enhancing your production value during the die-casting process is essential for manufacturing success.
TEAM Rapid is a professional die casting manufacture who offers both tooling and casting for your rapid prototypes\, small volume manufacturing, and mass production needs. Contact us today to request a free quote now!