Delve into the world of injection moulding, a pivotal manufacturing process that moulds molten materials into a variety of products, from intricate components to substantial automotive panels. Elevating the production efficiency of injection moulding machines is a pivotal endeavour for manufacturers, translating to cost savings, heightened productivity, and elevated product quality.
Table of Contents
- 1 Unveiling Injection Molding Machines: Masters of Precision Manufacturing
- 2 Unveiling the Mechanics: The Intricacies of Injection Molding Machine Operations may affects on production efficiency.
- 3 Navigating production Efficiency’s Landscape: Factors Impacting Injection Molding Machine Production
- 4 Production Efficiency Amplifiers: Elevating Injection Molding Machine Productivity
- 5 Navigating production Efficiency Enhancement: Challenges and Remedies
- 6 Conclusion of production efficiency
Unveiling Injection Molding Machines: Masters of Precision Manufacturing
Injection moulding machines, the craftsmen of the industrial landscape, possess the finesse to shape molten materials into intricate plastic components. Through a fusion of heat and pressure, these machines meticulously mould liquid materials within a closed mould, resulting in diverse plastic products. From diminutive parts to expansive automobile panels, they epitomize modern rapid manufacturing‘s precision and versatility.
Unveiling the Mechanics: The Intricacies of Injection Molding Machine Operations may affects on production efficiency.
The journey of injection moulding machines unfolds as a symphony of precision, orchestrating plastic pellets into refined products. This mechanical masterpiece is orchestrated through distinct stages:
Clamping
The mould’s halves unite under the clamping unit’s tenacious grip. This steadfast embrace counters the impending pressure of molten plastic infusion, forming the foundation for subsequent stages.
Injection
Plastic pellets journey from the hopper into the heated barrel, undergoing a metamorphosis orchestrated by a screw or plunger. This molten transformation flows through a nozzle into the mould’s intricate contours.
Cooling
As the molten plastic finds its mold-bound sanctuary, a cooling ritual begins. The duration of this interlude is influenced by parameters such as part thickness and plastic characteristics, culminating in solidification.
Ejection
With the cooling’s denouement, the mould/rapid tooling unfurls its treasure. Ejector pins elegantly usher forth the solidified creation. This ceremonial release punctuates the symphony’s crescendo.
These stages epitomize an injection moulding machine‘s operational essence. Beyond this choreography, a myriad of factors coalesce, influencing overall efficiency. Elements like mould configuration, plastic composition, and machine calibration harmonize to compose the distinctive rhythm of each production. When admiring a meticulously crafted plastic artefact, recognize the intricate interplay of engineering, finesse, and manufacturing process that grants it existence.
Efficiency in injection moulding machines is an intricate dance choreographed by a myriad of factors, each with its role to play. Let’s spotlight some of these factors that wield influence:
Machine Maestro
The machine’s settings reign supreme. Temperature, pressure, and injection speed weave together to conduct this symphony. Optimizing these settings orchestrates smoother, more efficient performances.
Moulding Mastery
The mould’s design holds secrets to streamlined efficiency. A well-crafted mould shortens cycle times and elevates part quality, casting an artistic touch on the production stage.
Material Magic
Material selection casts its spell on efficiency. Diverse plastics possess unique temperaments, with some demanding more time to cool or navigate processing hurdles that can slow the tempo.
Sustaining Excellence
Maintenance emerges as a guardian of efficiency. Nurturing the machine through cleaning, lubrication, part replacements, and regular inspections ensures a harmonious, uninterrupted production rhythm.
These factors harmonize as conductors of the efficient orchestra. By attending to these variables and employing best practices as a guide, manufacturers can elevate the efficiency of their plastic moulding performances. Through this meticulous choreography, the dance of molten materials and technology advances, setting the stage for an enchanting symphony of manufacturing excellence.
Production Efficiency Amplifiers: Elevating Injection Molding Machine Productivity
Underneath the surface of injection moulding lies a realm of techniques poised to elevate production efficiency. Let’s delve into some key strategies that can be harnessed:
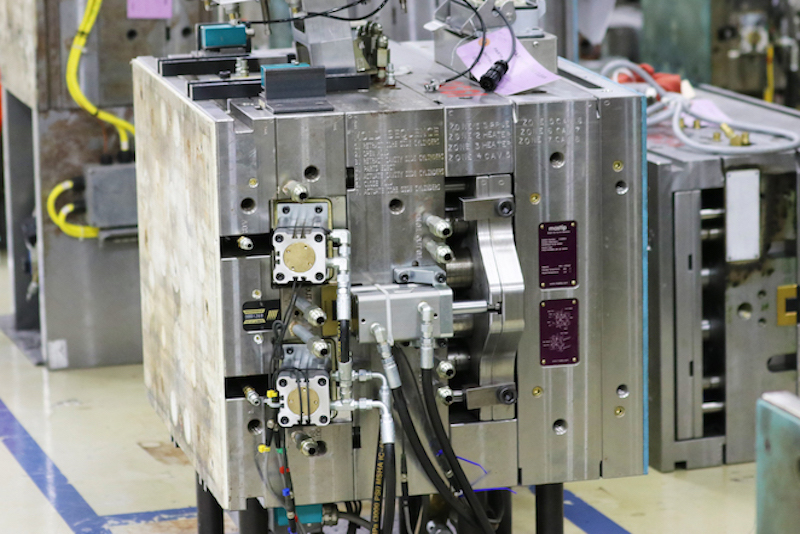
Optimizing Machine Mastery to raised the production efficiency
The machine’s prowess is maximized through meticulous settings adjustment. Fine-tuning parameters like temperature, pressure, and injection speed can be orchestrated through trial and error or simulated via specialized software, shaping a precision performance.
Sculpting Mold Brilliance
Mould design metamorphosis can redefine efficiency. By integrating innovative elements such as conformal cooling channels and quick-release features, cycle times shrink while part quality thrives.
Material Marvels Relates on production efficiency
Opting for premium materials crafts a path to excellence. High-quality plastics translate to fewer defects, bolstered consistency, and ultimately, a smoother production process.
Preventive Vigilance
The guard of preventive maintenance stands tall. Regular inspections and care of machine components safeguard against unexpected disruptions, nurturing an uninterrupted flow of production.
Operator Empowerment
Operator prowess drives efficiency. Investing in comprehensive training arms operators with skills for optimal machine operation and maintenance, ensuring a harmonious production journey.
These methods serve as beacons, illuminating the path to heightened efficiency. By interweaving these strategies and nurturing a culture of continuous improvement, manufacturers can sculpt a production landscape that resonates with enhanced output, reduced waste, and unwavering quality. The symphony of production finds its crescendo through the harmonious orchestration of these techniques, setting the stage for a manufacturing masterpiece.
The journey to augment the production efficiency of injection moulding machines is marked by certain challenges, each harbouring a remedy to illuminate the path forward. Here, we explore these challenges and the solutions they inspire:
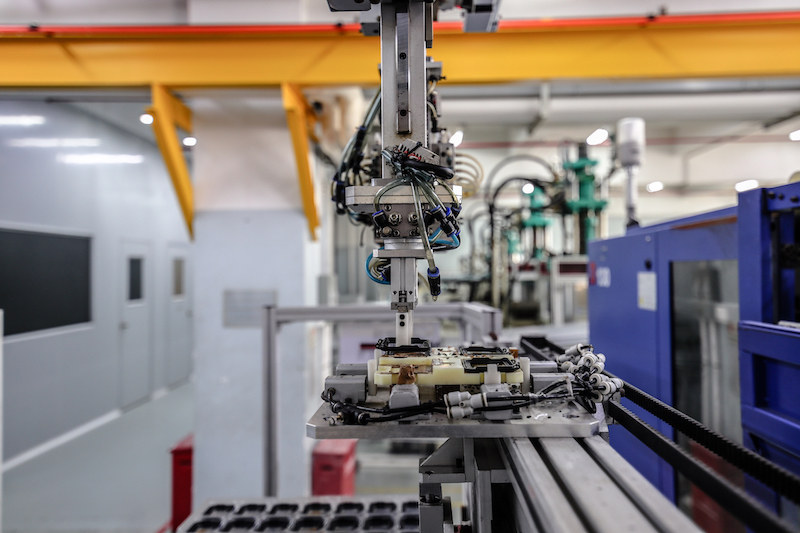
Capital Outlay Challenge
Elevating efficiency frequently necessitates substantial upfront investments in equipment, training, or software. This challenge can be particularly daunting for smaller manufacturers with limited resources. Solution? Seek financial support through grants or explore financing options to ease the initial financial burden.
Process Complexity
The intricate web of variables in injection moulding can confound efficiency enhancements, complicating the identification and implementation of improvements. Solution? Leverage specialized software for process simulation, offering insights into areas ripe for refinement.
Change Resistance
Introducing efficiency-improving changes may be met with resistance from stakeholders driven by unfamiliarity or apprehension. Solution? Foster consensus and provide comprehensive training to ensure smooth transitions and alignment with the broader vision.
Unforeseen Hurdles affects on production efficiency
Despite careful planning, unexpected challenges can emerge during the efficiency enhancement journey – equipment glitches or shifts in market dynamics. Solution? Establish contingency plans and maintain adaptability to gracefully address unforeseen circumstances.
In the realm of production efficiency, challenges serve as catalysts for growth and transformation. Manufacturers equipped with strategic solutions can deftly navigate these challenges, emerging with refined processes and optimized production. By harnessing innovation and collaboration, the symphony of efficiency plays on, undeterred by obstacles, propelled by the collective determination to excel.
Conclusion of production efficiency
In the intricate landscape of injection moulding, the pursuit of heightened production efficiency orchestrates an interplay of variables and solutions. From calibrated machine settings to innovative mould design and operator empowerment, a repertoire of strategies emerges. Embracing these methodologies, manufacturers can usher in an era of streamlined, high-calibre production.
Besides from injection molding, TEAM Rapid also offers rapid prototyping, CNC machining, and die casting to meet your projects needs. Contact our team today to request a free quote now.