An Injection molding machine plays a pivotal role in the manufacturing industry, reshaping raw materials into usable products. The need for comprehensive classification is evident, and it’s pivotal to grasp the various criteria utilized for this purpose, ultimately enhancing our comprehension of their diversity and functionality.
Table of Contents
Classification by An Injection Molding Machine Type
When it comes to injection molding machines, understanding their classification by type is a fundamental step in navigating the world of rapid manufacturing. There are two primary categories: mechanical, and hybrid.
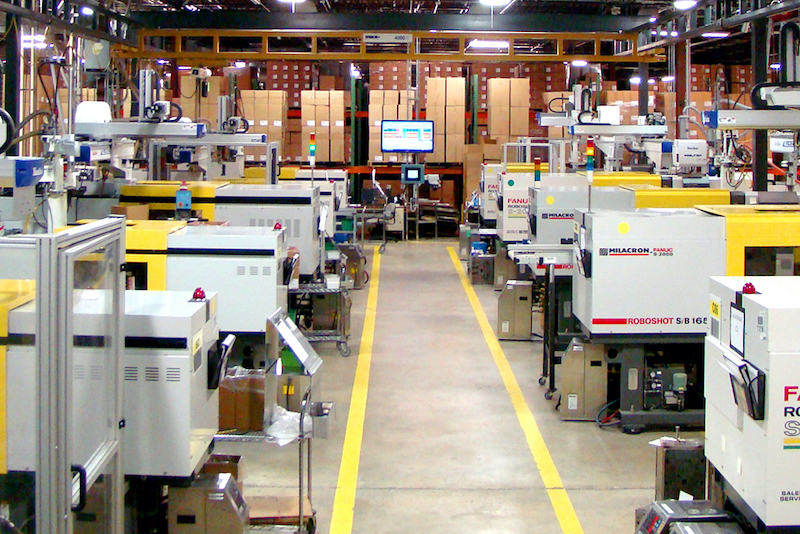
Mechanical Injection Molding Machines
These machines employ mechanical systems for generating motion. They were once prevalent, but their energy consumption and lower precision have led to a decrease in their usage in recent times. On the other hand, electric injection molding machines have gained popularity. They utilize electric motors to power the machine’s movements, offering precision, energy efficiency, and shorter cycle times. Nevertheless, it’s worth mentioning that electric machines often come with a higher price tag in comparison to hydraulic or mechanical alternatives.
Hybrid Injection Molding Machines
These innovative machines bring together the strengths of hydraulic and electric types. They leverage electric motors for swift and precise movements and employ hydraulic systems for robust clamping forces. This hybrid approach strikes a balance between performance, energy efficiency, and cost-effectiveness. In the dynamic world of manufacturing, comprehending these classifications is pivotal for decision-makers. By doing so, manufacturers can make informed choices, ensuring they select the most suitable injection molding machine for their specific needs, ultimately optimizing their manufacturing processes.
Classification by Clamping Force
In the domain of plastic injection molding machines, a pivotal factor for classification lies in the magnitude of machine clamping force, often measured in tons. This parameter profoundly influences the machine’s capabilities. Machines with clamping forces under 200 tons find their niche in applications necessitating precision and smaller-scale production. Their effectiveness lies in their ability to craft intricate and delicate components. Ascending the tonnage scale, machines wielding forces ranging from 200 to 500 tons exhibit versatility across a spectrum of manufacturing requirements. This class of machines adeptly balances precision and speed, rendering them indispensable in industries demanding diverse production capabilities.
Conversely, when heavy-duty operations are in order, machines endowed with clamping forces surpassing 1000 tons come to the fore. These robust machines excel in handling substantial molds and efficiently producing sizable components. It is imperative to acknowledge that clamping force directly influences a machine’s cost, energy consumption, and spatial requisites. Machines boasting lower clamping forces not only prove cost-effective but also display superior energy efficiency. On the contrary, high-tonnage machines, though more expensive, yield remarkable efficiency when engaged in large-scale production.
Furthermore, the selection of an apt clamping force holds paramount significance in averting machine overloading and ensuring precision and safety in the manufacturing process. Within the realm of injection molding, the multiplicity of options in clamping force serves as a testament to the versatility of this manufacturing technique. Empowered by their specific production prerequisites, manufacturers are adept at making informed choices regarding a machine’s clamping force, thereby streamlining and optimizing their manufacturing endeavors. This comprehension of clamping force classifications provides decision-makers with the knowledge needed to make judicious selections, guaranteeing the efficient operation of manufacturing processes, irrespective of the production scale at hand.
Classification by Material Type
Materials Matter: Classification by Material Type
In the exciting world of injection molding, the type of material a machine processes is a defining factor. Let’s explore the three main categories: thermoplastics, thermosets, and elastomers.
Thermoplastics: Shape-Shifters of the Molding World
Imagine a material that’s flexible when heated and magically transforms into a solid when it cools. That’s thermoplastics for you! The incredible thing is that this transformation is entirely reversible. You can melt and mold them again and again without any major identity crisis.
Casual Tip
Envision widely utilized household plastics such as polyethylene (PE), polypropylene (PP), and polyvinyl chloride (PVC). These are everyday examples of thermoplastics, ever-ready to be molded into something fantastic.
Thermosets: Once and Forever
Now, let’s move to the enigmatic world of thermosets. Unlike their shape-shifting cousins, thermosets are all about commitment.
Casual Tip
When you think of thermosets, envision epoxy, phenolic, and silicone. These materials are steadfast in their mission – once they’ve solidified, they’re here to stay.
Elastomers: Where Flexibility Meets Resilience
Elastomers bring a touch of rubbery magic into the mix. They’re all about elasticity and resilience.Casual Tip
When it comes to elastomers, think of natural rubber, neoprene, and nitrile rubber. These are the materials that make your car tires grippy and your seals, well, sealed.
Why Does it Matter?
Understanding these material classifications isn’t just for molding aficionados. It’s like knowing the ingredients to a recipe – it’s essential for a tasty dish. Manufacturers use this knowledge to select the perfect machine for their materials, ensuring top-notch product quality and a smooth plastic molding manufacturing ride.
Classification by Application of an injection molding machine
Injection molding machines find extensive application across a diverse range of industries, each sector benefiting from their unique capabilities. Let’s delve into some examples:
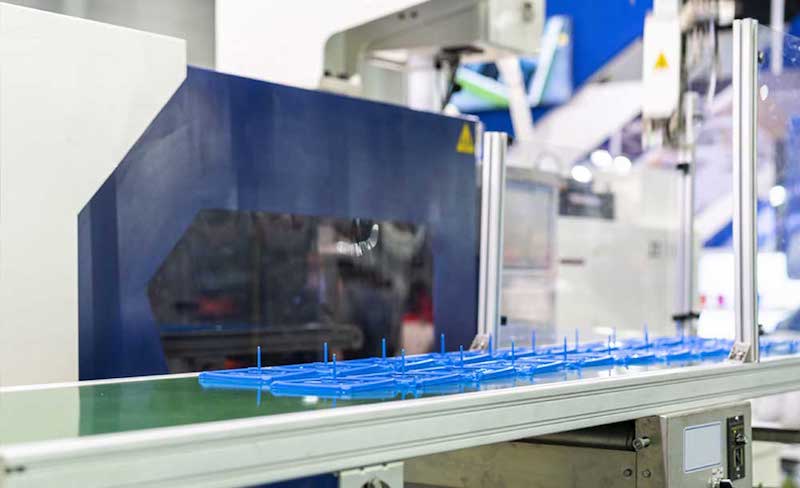
In the automotive sector, these machines take the lead in crafting essential components, from robust bumpers to intricate car interiors. Their precision and efficiency are instrumental in meeting the demanding standards of this industry.
Transitioning to the packaging sphere, injection molding machines are the workhorses behind the production of caps, containers, and films of varying sizes and shapes. Their remarkable speed and versatility in handling different materials are invaluable in this domain. The medical industry places stringent demands on machinery, and injection molding machines rise to the occasion.
In the domain of consumer electronics, these machines play a pivotal role in manufacturing parts for an array of devices, encompassing smartphones, laptops, and televisions. Understanding these classifications empowers manufacturers to make informed decisions, selecting the most suitable machine for their specific applications. This not only enhances product quality but also optimizes manufacturing efficiency, a critical factor in today’s competitive industrial landscape.
Conclusion
The delineation of injection molding machines by application underscores their profound versatility across a spectrum of industries. From automotive intricacy to medical sterility, these machines prove indispensable. Their pivotal role in fabricating components for electronics and packaging materials further exemplifies their versatile capabilities, fundamentally shaping industries worldwide.
TEAM Rapid invests a series of advanced machines to meet the customers’ rapid prototyping, injection molding, CNC machining, and die casting needs. Contact our team today to request a free quote now!