Injection molding is a pivotal manufacturing process wherein molten plastic finds shape within molds. This process is critical to ascertaining the requisite tonnage, or clamping force, indispensable for maintaining mold and rapid tooling closure during injection. This article is an illuminating journey into precision, elucidating the art of accurately computing the required tonnage for seamless injection molding.
Table of Contents
- 1 The Significance of required Tonnage and Clamping Force in Injection Molding
- 2 •Tonnage: The Pillar of Mold Stability
- 3 Unraveling the Significance of Projected Area in required Tonnage Determination for Injection Molding
- 4 Deciphering the Empirical Tonnage Calculation Formula in Injection Molding
- 5 Unveiling the Significance of required Tonnage Factors in Injection Molding
- 6 The Vital Role of Safety Factors in Injection Molding
- 7 Conclusion of required tonnage
The Significance of required Tonnage and Clamping Force in Injection Molding
Within the intricate domain of injection molding, the interplay of two vital components, cargo, and clamping force, takes center stage. Tonnage represents the pinnacle of clamping force that an injection molding machine can exert, ensuring the mold remains firmly shut throughout the injection process. Simultaneously, the clamping force acts as the steadfast guardian, countering the pressure of molten plastic and preserving the integrity of the final product.
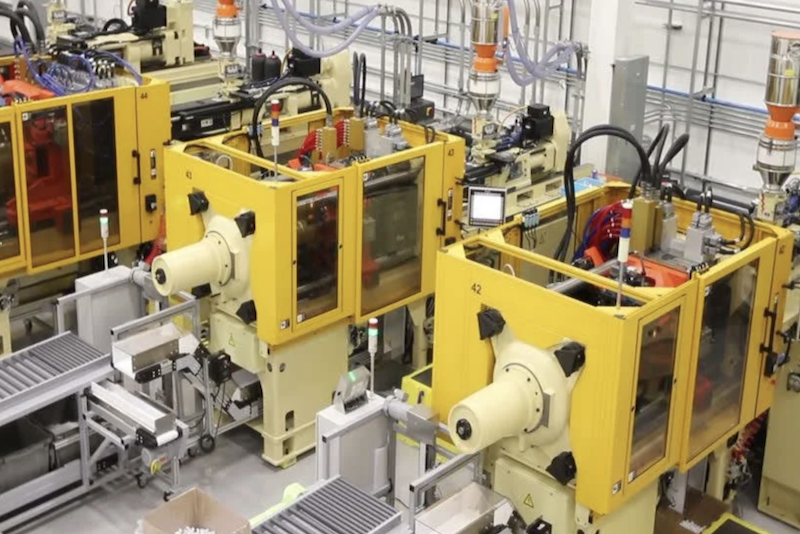
•Tonnage: The Pillar of Mold Stability
Tonnage, synonymous with maximum clamping force, epitomizes the power to maintain a secure mold closure while plastic is injected. As the bedrock of stability, it prevents unwarranted openings, guaranteeing flawless results during the manufacturing process.
•Clamping Force: The Shield Against Imperfection
On the other hand, clamping force stands as the defensive bulwark, resolutely withstanding the relentless molten plastic pressure. Its unwavering nature ensures that not a single drop of plastic escapes the confines of the mold, thereby thwarting defects and deviations.
•The Delicate Balance: Precision at its Core
Achieving an exquisite balance between tonnages and clamping force is an art. A meticulously calculated tonnage prevents issues like flash or short shots, safeguarding the product’s perfection. Meanwhile, avoiding excessive clamping force preserves the longevity of the mold and machine, ensuring efficient, sustainable production.
Unraveling the Significance of Projected Area in required Tonnage Determination for Injection Molding
In the intricate world of injection molding, the projected area of a part emerges as a critical player in the quest for optimal tonnage determination. Understanding this two-dimensional facet unveils the force required to maintain mold closure during the injection process, paving the way for flawless manufacturing outcomes.
•Projected Area: The Dimensional Crucible
At the heart of the matter lies the projected area – the two-dimensional expanse of the part visible from the perspective of the clamping force. This pivotal metric allows manufacturers to gauge the force necessary to secure the mold during the injection phase, playing a decisive role in tonnage calculation.
•Cracking the Code: Projected Area Calculation
Unlocking the projected area’s secrets demands an elegant yet straightforward calculation. Armed with the part’s length and width, manufacturers multiply these dimensions to unveil the projected area. For instance, a part measuring 5 inches in length and 4 inches in width would yield a projected area of 20 square inches (5 x 4 = 20).
•Depth of Understanding: Projected vs. Surface Area
It is crucial to discern that the projected area diverges from the part’s surface area. At the same time, the projected area encompasses solely the portion perpendicular to the clamping force; any features or cutouts parallel to this force remain excluded, keeping the calculation focused and precise.
Deciphering the Empirical Tonnage Calculation Formula in Injection Molding
Within the realm of plastic molding, determining the required tonnage for a mold is a crucial undertaking. Various methods exist for this purpose, with one prominent empirical formula shining through – Tonnage = Tonnage/Clamping Force Constant x Surface Area x Safety Factor. This versatile equation provides manufacturers with a swift estimation of the tonnage needed for a specific part, a pathway to enhanced efficiency in plastic production.
•Understanding the Elements: Unveiling the Formula
The empirical formula comprises three integral components, each playing a pivotal role in the tonnage calculation process:
1.Tonnage/Clamping Force Constant
A key value representing the intricate relationship between tonnages and clamping force, tailored to the specific material and machine characteristics. This constant bridges the gap between material properties and the force required for mold closure.
2.Surface Area
At the heart of the formula lies the projected area of the part, a two-dimensional measure achieved by multiplying the part’s length by its width. This critical dimension illuminates the expanse that comes into contact with the clamping force during injection.
3.Safety Factor
An indispensable value introduced to account for potential variations and uncertainties that may arise during the injection molding process. This safety factor fortifies the calculation, instilling confidence in the tonnage estimation.
•The Path to Precision: Utilizing the Formula
Armed with the tonnage/clamping force constant, surface area, and safety factor values, manufacturers embark on a journey of efficiency and accuracy. By plugging these variables into the empirical formula, they swiftly ascertain the required tonnage for their injection molding mold, a stepping stone towards flawless plastic part production.
Unveiling the Significance of required Tonnage Factors in Injection Molding
Within the realm of injection molding, the art of precise clamping finds guidance through tonnage factors. Crafted by material suppliers, these invaluable recommended clamp forces in tons per square inch impart manufacturers with the knowledge to mold parts flawlessly and efficiently.
•Understanding required Tonnage Factors: Tailored to Material Demands
At the heart of tonnage factors lies material-specific clamping demands. Ranging from 2 to 8 tons per square inch, these factors showcase materials’ diverse nature and varying requirements. From softer materials like polyethylene, demanding lower tonnage factors, to harder counterparts such as polycarbonate, necessitating higher values, the tonnage factors offer a bespoke approach to precision.
•Consulting Material Suppliers: The Path to Accuracy
Collaboration with material suppliers becomes paramount to unlock the full potential of tonnage factors. Their expertise in recommending the ideal tonnage factors for specific materials ensures optimal mold closure and unwavering product quality.
•Calculating Required Tonnage: Harmonizing with Projected Area
By seamlessly integrating projected area and tonnage factors, manufacturers chart the course toward calculating the essential tonnage. Armed with the projected part area and the designated tonnage factor, they unveil the requisite clamping force in tons, a gateway to precision molding.
The Vital Role of Safety Factors in Injection Molding
A critical aspect of injection molding, the safety factor, is a protective shield in the tonnage calculation process. This additional value is incorporated to account for any potential variations or uncertainties during molding, ensuring a reliable and resilient manufacturing process.
•The Essence of the Safety Factor: Shielding against Uncertainties
The safety factor acts as a safety net, mitigating the risk of unexpected deviations in the injection molding process. By including this buffer value, manufacturers fortify their calculated tonnage requirements, assuring consistent product quality and minimizing the possibility of mold failure or defects.
Conclusion of required tonnage
Calculating tonnage for injection molding involves understanding tonnage factors, employing a 10% safety factor, and using the empirical formula for precision and efficiency.
Besides from injection molding, TEAM Rapid also offers 3d print services, CNC machining services, and die casting to meet your project needs. Contact our team today to request a free quote now!