In dynamic manufacturing, injection molding emerges as a versatile process, shaping objects of diverse shapes and sizes. Widely adopted across industries, this method holds substantial potential for crafting silicone products. The precision of an injection molding machine becomes pivotal, guaranteeing the flawless creation of silicone marvels. As we unravel the intricacies of this process, we’ll delve into its applications, shedding light on the numerous advantages it offers.
Table of Contents
Understanding Injection Molding
In the vast manufacturing landscape, plastic molding stands out as a process capable of producing parts on a grand scale. It carves its niche in mass-production scenarios, where the replication of the same component occurs successively, numbering in the thousands or even millions. This method serves as a linchpin in large-scale production, ensuring both efficiency and consistency.
This intricate process involves the injection of molten material into a meticulously crafted mold. Once injected, the material undergoes cooling and solidification, adopting the precise shape dictated by the mold. This custom-made mold becomes a pivotal player in the production line, capable of being utilized repeatedly to recreate the same part. This repetitive utilization serves as a testament to the method’s cost-effectiveness and reliability.
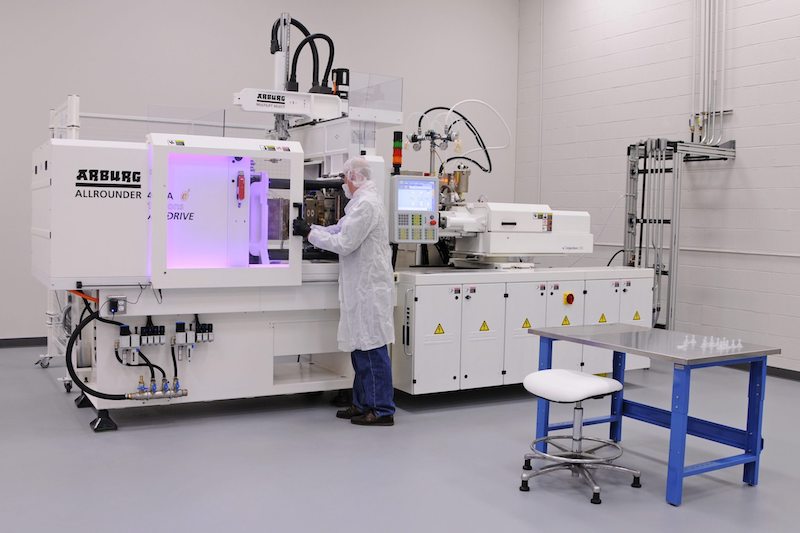
A diverse array of materials finds utility in injection molding. Thermoplastic and thermosetting polymers, elastomers, and metals each fulfill a unique purpose dictated by the desired characteristics of the product and its economic viability. Within injection molding, thermoplastics assume a prominent role due to their versatility and user-friendly nature, incorporating materials such as polyethylene, polypropylene, and PVC. In contrast, thermosetting polymers like epoxy and phenolic resins step in when heat resistance is paramount. Elastomers such as rubber and silicone offer flexibility, while metals, including steel and aluminum, find application in die casting, a variation of the process.
Making Silicone Products: Silicone as a Material for Injection Molding
Silicone, a renowned elastomer valued for its versatility, takes center stage in injection molding courtesy of its distinctive properties. This rubber-like material not only flaunts unmatched flexibility and resilience, making it ideal for crafting intricate products, but it also extends its appeal beyond elasticity.
Silicone showcases exceptional thermal stability, withstanding high temperatures without degradation—a trait that seamlessly aligns with the injection molding process. It involves heating the material to a molten state for precision molding. Additionally, its commendable chemical resistance enhances its suitability for diverse environments.
A standout quality of silicone lies in its biocompatibility, a vital trait for medical applications. Its inherent non-toxicity and absence of reactivity with human tissue render it an optimal material for medical devices, ensuring a harmonious balance between safety and effectiveness. Additionally, its hypoallergenic nature serves to minimize the risk of allergic reactions, further enhancing its suitability across various applications.
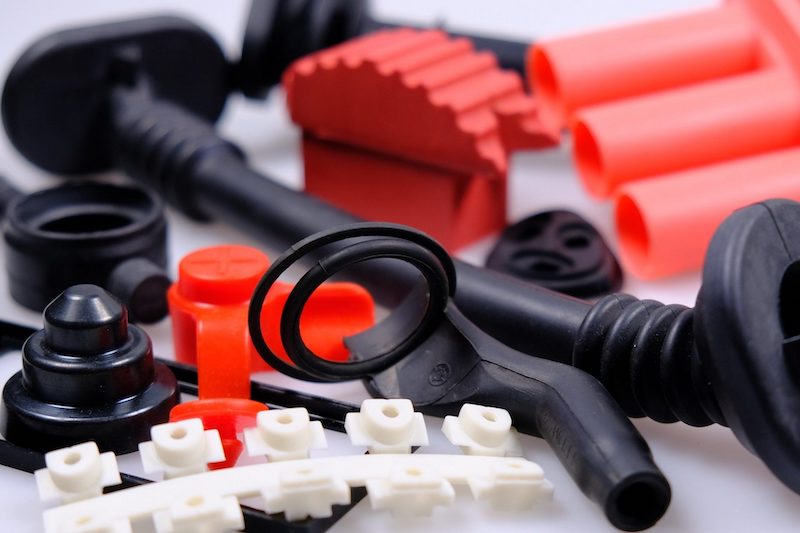
Exploring the varieties of silicone employed in injection molding, we encounter a diverse trio: Liquid Silicone Rubber (LSR), High Consistency Rubber (HCR), and Fluorosilicone Rubber (FSR). LSR, a two-part, platinum-cured silicone, is ideal for producing flexible, durable parts resistant to extreme temperatures. On the other hand, HCR, also known as gumstock, offers a denser alternative, perfect for molding extra-tough components. Its supply in sheets or strips and more intensive processing set it apart.
FSR introduces a unique twist by incorporating fluorine modification for enhanced chemical resistance. Its ability to withstand fuels, oils, and various fluids positions it as a go-to choice in the automotive and aerospace industries, showcasing silicone’s adaptability across diverse manufacturing sectors.
The Process of Silicone Injection Molding
In the intricate interplay between technology and material, the process of silicone injection molding unfolds like a meticulously orchestrated symphony. Executed through an injection molding machine, this methodical procedure seamlessly transforms raw silicone into precision-crafted products, with each step a carefully choreographed maneuver towards perfection.
The journey commences with the meticulous preparation of the silicone material. Raw silicone is precisely measured and introduced into the injection molding machine in either pellet or liquid form. This crucial initial step, essential for ensuring consistency in the final product, sets the foundation for subsequent intricate processes.
Once loaded, the machine engages in a carefully orchestrated heating process. The silicone transforms into a molten state, reaching the optimum temperature for injection. This liquefied silicone, akin to the molten core of creativity, is now ready for precise shaping.
Within the heart of the injection molding machine, the mold awaits the molten embrace. The machine injects the liquefied silicone into the meticulously crafted mold, ensuring every recess with precision. This step demands exactitude, as the mold dictates the final form of the product.
Following mold filling, a period of patient cooling ensues. The once-liquid silicone solidifies, adopting the precise contours of the mold. This cooling process is pivotal in determining the product’s structural integrity and resilience.
The final act unfolds as the mold releases its creation. The injection molding machine carefully opens, unveiling the newly formed silicone product. This delicate separation is a testament to the harmonious interplay between material and machine.
In a denouement of efficiency excess material, often referred to as flash, is meticulously trimmed away. This precise touch ensures the finished product meets the desired specifications with utmost accuracy. The excess, a byproduct of the molding process, is discarded to reveal the refined and flawless silicone creation.
Applications of Silicone Products from Injection Molding
Silicone products, meticulously shaped through the precision of injection molding, seamlessly integrate into industries, leveraging the material’s distinct properties. The medical sector reaps significant benefits from silicone’s biocompatibility, producing devices such as catheters, seals, valves, and implants.
Simultaneously, the automotive industry capitalizes on silicone’s resilience to high temperatures and harsh conditions. Seals, gaskets, and hoses, crafted through injection molding, withstand the rigors of vehicular environments. The electronics sector taps into silicone’s insulating prowess, utilizing it to create keypads, connectors, and wiring insulation.
The food and beverage industry finds a reliable ally in silicone, given its non-toxic nature and capacity to endure extreme temperatures. Baking molds, spatulas, and various kitchen utensils emerge as silicone-crafted essentials. Similarly, the aerospace industry benefits from silicone’s resistance to extreme conditions, employing it in the production of seals, gaskets, and insulation for wiring.
Conclusion
The adaptability of silicone in injection molding stands as a cornerstone across various industries. Its biocompatibility in medical applications, resilience in automotive and aerospace sectors, and insulating properties in electronics underscore its unique versatility. Products like catheters, seals, keypads, and kitchen utensils highlight silicone’s integral role in the diverse landscape of rapid manufacturing.
Besides from silicone products manufacturing, TEAM Rapid also offers rapid prototyping, CNC machining, and die casting to meet your projects needs. Contact our team today to request a free quote now!