Injection molding stands as a cornerstone of modern manufacturing, employed across diverse industries. These molds, pivotal in defining a product’s form, are crafted with meticulous precision. Our journey begins by uncovering the nuanced art of injection molding manufacturing, shedding light on variations, material choices, and stringent quality checks.
Table of Contents
Types of Molds in injection molding manufacturing
In the world of injection molding, a plethora of mold types comes into play, each meticulously chosen for its unique ability to meet distinct product requirements. Allow us to navigate through some of the most prevalent choices:
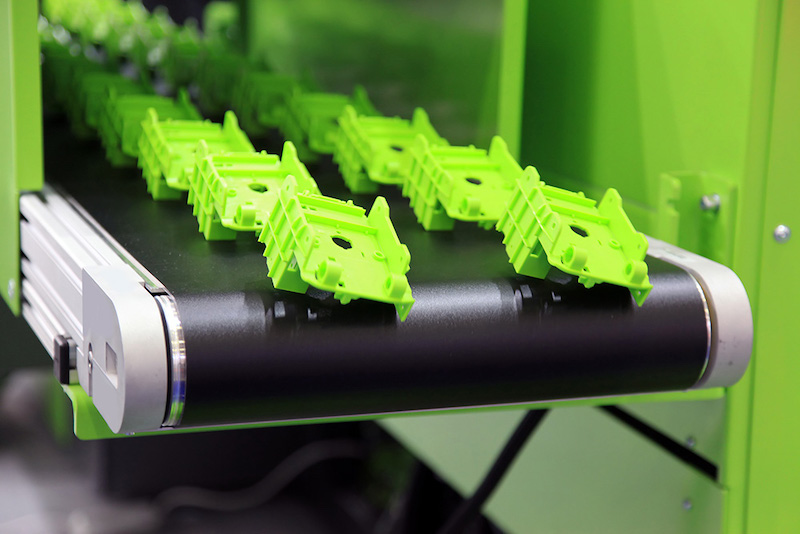
Two-Plate Mold for injection molding manufacturing
This mold variety, boasting simplicity and ubiquity, stands as a favored choice in injection molding. With just one parting plane and two mold halves, it caters to the production of straightforward components that lack intricate features.
Three-Plate Mold for injection molding manufacturing
In contrast, the three-plate mold introduces a layer of complexity. It features two parting planes, facilitating the creation of parts with intricate details or those demanding side-action mechanisms. It’s the go-to choice for intricate components.
Stack Mold for injection molding manufacturing
When production volume takes the front seat, stack molds enter the scene. Characterized by multiple layers, these molds churn out high quantities efficiently. They are ideal for producing identical parts or implementing the concept of family molding or plastic multi-cavity mould .
Family Mold for injection molding manufacturing
The family mold concept is ingenious, allowing for the simultaneous creation of multiple, different parts in one production cycle. This mold type shines when the final products require precision in fitting together, ensuring consistency and efficiency.
Hot Runner Mold for injection molding manufacturing
For large-scale production and superior quality components, hot runner molds come to the forefront. By maintaining plastic in a molten state through heated components, they reduce waste and enhance efficiency.
Apprehending the nuances of mold and rapid tooling types and their specific applications is pivotal in the injection molding landscape. Selecting the right mold equates to optimized production, ensuring a harmonious alignment of product complexity, required quantity, and the desire for top-notch quality. In the realm of injection molding, where precision and efficiency reign supreme, the choice of mold paves the way for product perfection.
Materials Used in Mold Manufacturing
In the realm of mold manufacturing, the choice of materials is a paramount decision, significantly influencing the performance, longevity, and cost-effectiveness of molds. Here, we delve into the common materials employed and scrutinize their respective advantages and disadvantages.
Steel Mold
To commence, steel molds are esteemed for their remarkable durability and precision. Constructed from hardened tool steels such as P20, H13, and S136, they exhibit a plethora of merits. These molds exhibit exceptional resistance to high temperatures and pressures, ensuring extended longevity and the capacity for high-volume production. They are renowned for their ability to capture intricate details, rendering them ideal for the fabrication of complex parts. However, it is imperative to acknowledge that this durability and precision necessitate a higher initial investment and ongoing maintenance costs.
Aluminum Mold
Aluminum molds, in contrast, proffer a cost-effective alternative. They are characterized by their lightweight composition, facilitating ease of handling and accelerated cooling during the injection process. Their domain of excellence primarily encompasses short to medium-production runs and prototype development. Nevertheless, it is worth noting that their relatively limited lifespan and lower durability, compared to steel molds, may render them unsuitable for applications involving high-volume production.
Copper Mold
The beryllium-copper alloy stands as a notable material, distinguished by its exceptional thermal conductivity. This attribute makes it an optimal choice for molds demanding rapid cooling and efficient heat dissipation. Nickel-based alloys are highly esteemed for their exceptional resilience to challenging conditions, such as those involving abrasive materials or elevated temperatures, rendering them a highly attractive choice. They amalgamate strength, heat resistance, and corrosion resistance. Nevertheless, their elevated cost and the intricacies associated with machining may limit their deployment in certain applications.
Composite Mold
Composite molds, commonly fashioned from epoxy or other reinforced materials, are distinguished by their lightweight constitution and cost-efficiency. They carve a niche in the realms of prototyping and low-volume production. Nevertheless, it is prudent to acknowledge that they may not attain the level of durability and precision typified by metallic molds.
Plastic Mold
Lastly, plastic molds, hewn from materials like PEEK or HDPE, deliver the advantages of cost-effectiveness and facile machining. They are apt for applications involving low temperatures and pressures. However, their constrained durability and susceptibility to wear render them unsuitable for high-volume or high-pressure production scenarios.
In the intricate expanse of mold manufacturing, the selection of materials assumes critical significance, significantly shaping the mold’s performance and cost-effectiveness. The key lies in judiciously aligning the material with the particular exigencies of the project, whether it encompasses high-volume production, exactitude in intricate details, or cost-effective prototyping. Each material contributes its distinctive set of advantages and disadvantages, offering manufacturers a diverse panoply of options for meticulously crafting the quintessential mold for their injection molding undertakings.
Quality Control in Mold & injection molding manufacturing
Quality control in mold manufacturing holds a pivotal role, as it directly influences the quality of the end product. It’s the linchpin that ensures the molds are impeccably fabricated, resulting in superior, uniform products. Let’s explore some prevalent quality control measures in mold manufacturing:

Inspection of Raw Materials
Commencing at the root, the quality control process kicks off with a rigorous examination of raw materials. Ensuring the materials used meet exacting standards is of paramount importance, as it profoundly impacts the mold’s durability and performance.
Dimensional Accuracy Checks
Consistent checks are performed to guarantee that the molds adhere to the specified dimensions.
Hardness Testing
Mold hardness is a determining factor in its resistance to wear and tear. Thorough hardness testing is executed to ensure the mold can withstand the rigors of continuous production.
Mold Trials
In the final stages of quality control, mold trials are conducted to validate whether the mold indeed produces parts by the predetermined specifications. Any issues uncovered during these trials are swiftly addressed before the initiation of mass production.
Conclusion of injection molding manufacturing
Conclusively, we have delved into the essential facets of mold manufacturing within the realm of plastic molding. These include an examination of diverse mold types, the materials integral to the process, and the pivotal role of stringent quality control. Mold manufacturing stands as the linchpin of precision and operational efficiency, underlining the critical importance of adhering to exacting standards in producing high-quality, high-performance products.
Besides from injection molding, TEAM Rapid also offers rapid prototyping services, CNC machining services, and die casting to meet your projects needs. Contact our team today to request a free quote.