The hot and cold runner systems in injection molding are the two most common molding systems you will need to use in your production cycles. Each one of them will have its own use within your production plan, so you need to know the differences between these runners in your injection molding process. This guide will help you understand more about the key differences you need to know between hot runner vs. cold runner injection mold.
Table of Contents
Understanding The injection Molding Runner Systems
In injection molding(including insert molding and overmolding), hot runner and cold runner have a similar system, with the only difference being that hot runner uses heat in their injection molding process. The goal for these processes remains the same, which is to deliver the plastic materials to the mold cavities, so that the injection molding process can happen.
With a hot runner injection mold, the injection mold system will use constant heat around the pipes to ensure that the plastic materials remain at their melting temperature. By maintaining the plastic materials at their melting temperature, it will be easier for the materials to go through the injection mold system into the mold cavities for further molding processes. The heat on the hot runner system can come from the internal or external heating system, depending on the preferences of the manufacturer.
Meanwhile, the cold runner injection mold doesn’t use heat to run the plastic materials through the injection molding system into the mold cavities. Instead, it uses plates to help move the plastic materials into the mold cavities for further molding processes. However, the cold runner injection mold is often slower than the hot runner counterparts because it doesn’t use heat in its injection molding system, which can affect your overall production cycles.
The Benefits of Hot Runner vs Cold Runner
Hot runner vs. cold runner, both the hot and cold runner injection molds have their own benefits. Depending on the rapid manufacturing needs and preferences, the manufacturers might use one method over the other. For instance, a hot runner might provide faster production cycles, whereas a cold runner might provide the manufacturers with the lowest cost of production.
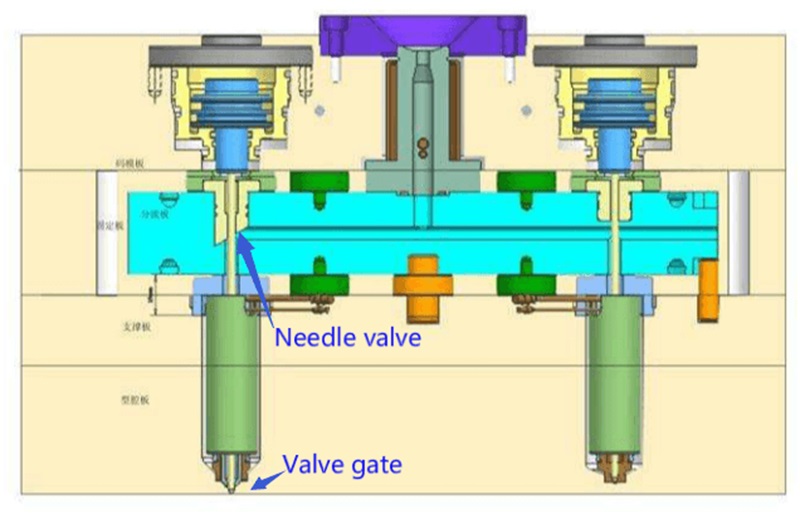
Hot Runner Injection Mold Benefits
●By using the heated injection molding system, the runner can transfer the plastic materials to the mold cavities faster, which helps speed up the overall production cycles.
●It’s most suitable for large parts production, as it is easier to direct the large plastic materials into the mold cavities using heat.
●You can fine-tune the molding process with ease, as there are various configurations you can change at any stage of production.
●The quality of the end product will be consistent and reliable, minimizing any instances of product defects during fabrication.
●Compared to the cold runner injection mold, the hot runner system produces fewer waste materials.
Cold Runner Injection Mold Benefits
●It doesn’t require expensive production and maintenance costs for the manufacturers.
●You can change the colors of the materials with ease.
●You can schedule your production time in a much simpler way.
●It’s most suitable for a wide variety of polymers and resins.
The Disadvantages of These 2 Runners
Each of the injection mold runners will have its own disadvantages too. So, you can’t just rely on one runner and expect everything will go well in your production. Every runner system, both hot and cold, can give you certain disadvantages that might affect your overall production plan or schedule.
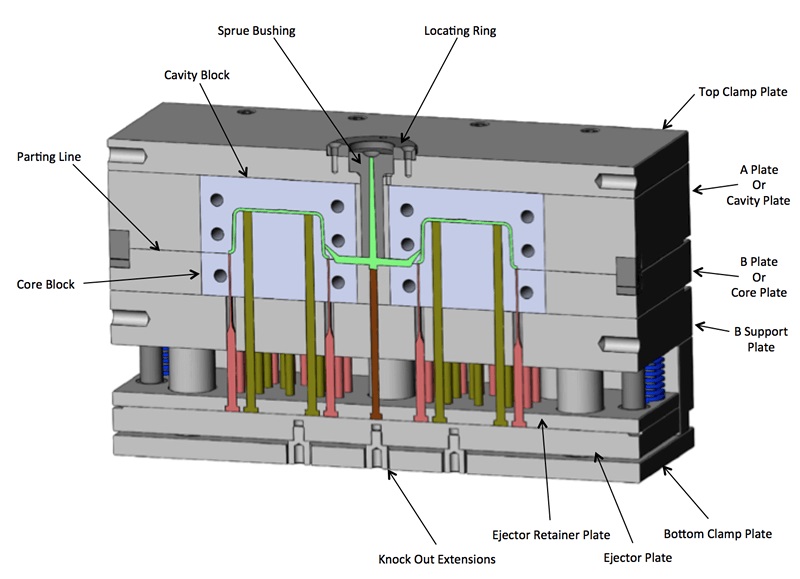
Hot Runner Injection Mold Disadvantages
●You cannot change the plastic material color just as you want it.
●It is not suitable for materials that don’t react well to heat, such as polymers and resins.
●You will need to wait for some time before the plastic materials can cool down during the injection molding process.
Cold Runner Injection Mold Disadvantages
●In most cases, you can’t recycle the waste materials produced by the cold runner molding system.
●It will give you a slower overall production cycle.
●You can only use specific materials for this process, such as resins and polymers.
Is Hot Runner Better than Cold Runner?
Determine whether the hot runner or cold runner system is better, it will depend on your manufacturing needs. For example, with some plastic materials, such as resins and polymers, you can’t use the hot runner system to process them.
These materials will not have a stable form when exposed to the heat generated by the hot runner system. So, you will need to use the cold runner system to process the resin and polymer materials in your production cycles.
Thus, there is no such thing as a better or worse injection molding method between the hot runner and cold runner systems, as they both have their own use.
Choosing between These 2 Runners in Manufacturing
Manufacturers, they will choose to use the hot runner injection mold if they need to process large production volumes at the fastest production cycles. They will also use the hot runner molding system for most plastic materials, as these materials are easier to manage during the molding and die cast metal process.
However, manufacturers will still use the cold runner system, although it is slower than the hot runner system if they need to process resins and polymers in their production cycles. Also, the cold runner system allows them to change the colors of the materials at will, making it easier for them to create variations of their products.
All that matters is the production needs of each manufacturer, the materials they are using, and the production schedule they are planning. They will match these aspects and use the runner system that can accommodate their production plan in the best way.
Conclusion
Hot runners and cold runners are an important part of any injection molding process. Each runner system has its own pros and cons, which gives the manufacturers the options on which runner system to use depending on the projects or production requests they need to complete. Both the hot and cold runner systems have their own compatibility with certain plastic materials for injection molding, so you can’t just abandon one runner and pick the other one, as you will need to use both runners at some point.
Faster doesn’t mean better, while slower also doesn’t mean worse. It’s best for you to pick the right runner system to use, depending on the project requirements you need to fulfill from your clients. TEAM Rapid offers professional injection molding services and rapid prototyping services, contact our team today to get the right runner system for your upcoming tooling projects!