What makes a workpiece completely smooth and usable for precision applications? Face milling, of course. This powerful machining process not only removes excess material but also creates surfaces that meet the highest precision and quality standards. So why is face milling so important in modern manufacturing, and how does it achieve such impressive results? Let’s read on to learn more.
Table of Contents
What is Face Milling?
Face milling smooths a workpiece surface using machining centers or milling machines. Unlike traditional methods, the machine’s top, not the side, mills the vertically placed workpiece. It can be manual, requiring frequent stops to adjust the workpiece, or automatic, which offers steady feed speed and reduces errors.
Face Milling Process
Face milling consists of several steps, so let’s take a look at them.
Step 1: Fix the Workpiece
First of all, to firmly fix the workpiece to the machine table, we can use fixtures, vise or similar tools, which can allow the workpiece to be milling without disorderly movement. In addition, we need to check that the workpiece is stable and that it is properly aligned with the milling face.
Step 2: Align the Tool with the Workpiece
The second step is to align the workpiece and the cutting tool correctly. In this part, we can use some tools to help us better, such as dial gauges or other devices, such as alignment instruments. Next, adjustments are made until the cutting tool is located directly above the workpiece, ensuring that the surface of the workpiece is at the right Angle to the rotation of the cutting tool.
Step 3: Configure Milling Parameters
Next, in the third step, you need to adjust the control panel of the CNC machine tool by setting the spindle speed, feed speed, and cutting depth. These settings will vary based on the material being machined and the specifications of the tool. After configuring the parameters, it is important to test them on a sample to ensure they are optimized for efficient operation.
Step 4: Perform the Milling Operation
Finally, start milling. First, turn on the machine and slowly lower the tool so that the tool touches the surface of the workpiece. Because we have set the instructions, the CNC system will follow the programmed instructions, and the operator tool will move on the workpiece in an overlapping path to ensure that the entire surface is machined evenly.
Types of Face Milling Cutters and Their Uses
In face milling, we choose different types of tools according to the material to be removed, the desired finish and the characteristics of the workpiece. Here are some common types of face milling tools and their applications.
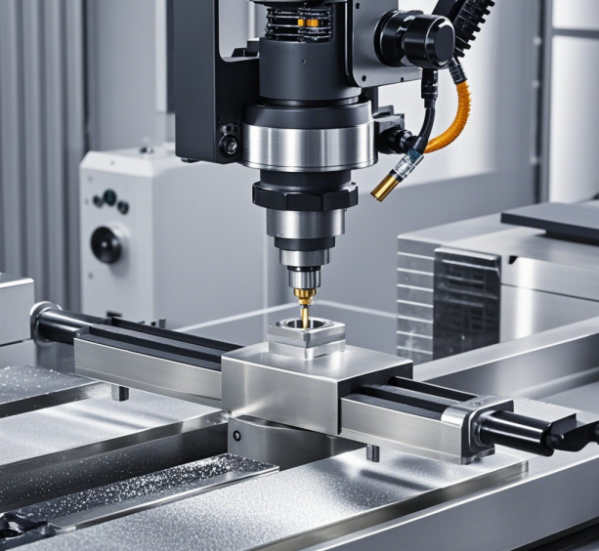
- End Mills
End mills are adaptable and suitable for many tasks. They allow the surface finish to be smooth and precise, and we can create detailed designs using end mills. These tools perform well in both surface and side milling, so it is the first choice for general purpose machining.
- Shell Mills
Shell mills can remove large amounts of material in a short amount of time. Because of the wide diameter of these tools, they are mainly used in roughing tasks, such as when machining larger workpieces that require stability and efficiency. Shell milling cutters are ideal for flattening large surfaces and preparing the workpiece for finishing.
- Fly Cutters
Fly cutters feature a single cutting edge. Although its processing speed is slower, it is able to provide excellent surface quality. Fly cutters are practical and can be used on a variety of materials, and they are especially useful when machining smaller parts that require very smooth surfaces.
Key Applications of Face Milling
Application | Description |
Surface Flattening | The main aim of face milling is to flatten the uneven or rough workpiece surface to create a uniform plane. This is crucial for providing a stable base for subsequent machining or obtaining a clean and polished final product. |
Intensive Material Removal | This method is frequently employed when there is a need to quickly and efficiently remove a large amount of excess material. Additionally, it is often used during roughing operations as a preparatory step to get the workpiece ready for more precise and finishing tasks. |
Fine Finishing Operations | Often, this is the final step to create a smooth and high-quality finish. As a result, the process delivers a polished surface that looks good and works well. |
Slot and Pocket Milling | By adjusting the toolpath, this milling process can be tailored for creating slots and pockets in the workpiece. This flexibility enables the manufacturing of not only flat surfaces but also specific internal features and details. |
Machining of Large Workpieces | For large workpieces, heavy-duty face milling cutters work well to cover big areas. What’s more, shell mills help ensure even surfaces, making them ideal for parts like aircraft wings and car chassis. |
Angular Face Milling | By adjusting the orientation of the face cutter, it becomes possible to create angled surfaces with ease. Additionally, this approach is particularly useful for forming angled features, such as chamfers or sloped surfaces, without requiring a different milling method. |
Preparation for Secondary Processes | Face milling is frequently employed as an initial step in the machining process to prepare the workpiece for further operations, such as drilling, end milling, or peripheral milling. Furthermore, producing a flat and even surface helps to reduce the complexity and precision requirements of the processes that follow. |
Advantages and Disadvantages of Face Milling
Face milling offers many advantages, but it also has some challenges. You need to understand its advantages and disadvantages if you want to take advantage of it.
Advantages of Face Milling
Smooth Surface Quality: This method creates surfaces that are very smooth and polished, which is important for precision work, even low volumn manufacturing.
Efficient Material Removal: Face milling is capable of swiftly removing substantial amounts of material, which makes it extremely efficient.
Wide Range of Applications: It works well on a variety of surfaces and can handle many types of materials, making it a flexible option for machining.
Disadvantages and Challenges
Handling Chips: In the milling process, some materials will produce a lot of chips, especially materials that will form long and curly chips. Dealing with these chips can be tricky.
Tool Life Issues: Through a long time of use, the cutting edge will be worn, especially when processing hard materials, the wear will be more serious, so we need to replace the tool regularly.
Vibration Problems: If the machine setup is not stable, vibrations can occur. This may reduce surface quality and increase wear on the tools.
Face Milling Tools: Coatings and Materials
The material and coating of a face milling tool are crucial as they impact performance, durability, and efficiency, enabling effective handling of diverse machining tasks.
Tool Coatings
The coating applied to a face mill impacts its wear resistance, heat management, and overall performance. Below are two commonly used coatings and their characteristics.
Coating | Benefits | Applications |
Titanium Nitride (TiN) | It not only enhances hardness and improves wear resistance, making the material more durable, but it also minimizes friction. Also, it helps to reduce heat buildup during machining, which ensures a smoother and more efficient operation. | Ideal for machining at high speeds and handling hard or challenging materials. |
Diamond Coating | It is extremely durable against wear and ideal for machining very hard and abrasive materials, such as composites. | Costly, yet perfect for handling certain hard materials. |
Tool Materials: Carbide vs. High-Speed Steel (HSS)
The material of a face milling cutter influences its strength, durability, and suitability for different operations. Below is a comparison of the two most common materials:
Material | Characteristics | Uses |
Carbide | Known for its high hardness and heat resistance. Excellent for high-speed and heavy-duty applications. | Commonly used in high-end CNC machines where tool durability and efficiency are crucial. |
High-Speed Steel (HSS) | More affordable and versatile for moderate-speed operations. | Ideal for easier tasks or when working with softer materials. |
Advice on Best Practices for Face Milling
If you want to perform accurate face milling, you need to consider many factors, such as the right tool, the appropriate machining Settings, and so on.
Choose the Right Tool
The right tool increases efficiency and reduces tool wear. Therefore, it is first necessary to select a tool that matches the workpiece material, the required surface finish and the removal rate.
Maintain Tool Balance
Balanced tools reduce vibration and improve surface quality. If the tool is not balanced, it may wear out faster and affect the end result.
Use the Recommended Spindle Speed
During machining, if you use the correct speed, you can ensure smooth operation and extend tool life. Therefore, you should set the recommended spindle speed for the material and tool type.
Avoid Milling on Slots or Holes
Do not cut on slots or holes unless necessary. Doing so prevents the tool from deflecting and protects the tool and workpiece. In addition, careful planning of the path can help achieve better results.
Using CNC Automation
CNC machines provide better accuracy and consistency. They are ideal for large-scale production runs that require uniform quality.
Conclusion
Face milling is a significant machining technique that comes with its own unique features, benefits, and constraints. Therefore, gaining a thorough understanding of it and applying it correctly is crucial for achieving high-quality machining results.
If you are looking for a reliable partner to handle your face milling and other manufacturing needs, TEAM Rapid Tooling is an excellent choice for CNC machining China.
- Advanced Equipment and Professional Team: TEAM Rapid Tooling is equipped with the most advanced machine tools and a team of highly skilled technicians. The team has extensive experience in face milling, and their careful operation ensures that the workpiece surface meets the highest accuracy and flatness standards.
- Comprehensive Service Range: Our services are not limited to face milling. We offer many services, such as die casting for metal parts, CNC machining for precise and detailed forming and sheet metal machining. These comprehensive services streamline your production process, saving you time and effort.
- Quality and Efficiency Focus: We have a strict quality control system to ensure that our products are of top quality. In addition, we constantly strive to optimize our manufacturing processes to improve efficiency.
Click on our website today and let us be your trusted ally in realizing your manufacturing visions and taking your projects to new heights.
Click to take your engineering business to the next level>>>
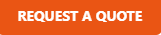