EDM machining, which stands for Electrical Discharge Machining, is the metal fabrication process that uses electrical discharges to create the shape of the prototype or part you want to get. With this manufacturing process, you will control the sparks generated from the electrical discharges to melt or vaporize the metal materials. By controlling these sparks, you can create metal prototypes or hardware parts according to your design requirements. In this guide, you will learn about various aspects of this process in rapid manufacturing.
Table of Contents
- 1 What Makes EDM Machining and EDM manufacturing Unique?
- 2 Advantages of EDM Machining and eDM manufacturing
- 3 EDM Machining and eDM manufacturing Process
- 4 Using the EDM Machining and EDM manufacturing Process the Best Way
- 4.1 ●Use the EDM machining and EDM manufacturing process only for tasks that traditional machining can’t complete.
- 4.2 ●Use the EDM machining and EDM manufacturing method for hard metal materials and complex prototype designs.
- 4.3 ●Choose the wire EDM instead of the traditional EDM machining and EDM manufacturing equipment.
- 5 Conclusion
What Makes EDM Machining and EDM manufacturing Unique?
EDM machining is a non-traditional machining process that has its own unique method of creating metal prototypes, which is by using the sparks generated from electrical discharges. It doesn’t involve any cutting like the CNC machining and CNC turning process. Instead, it shapes the metal prototypes by removing various parts of the metal materials by melting and vaporizing them. Here are some important points that make this process unique:
●Using high-temperature electrical discharges or sparks.
Compared to the other prototyping process, such as CNC prototyping, which cuts metal materials to follow the prototype design, EDM machining has a unique way to create metal prototypes. It uses high-temperature sparks to mold and shapes the metal materials to follow the prototype designs. Also, you can control how the sparks or electrical discharges behave during the manufacturing process.
●Creating metal prototypes where you need to make sharp corners.
EDM machining is an exceptional machining process because you can use it to produce prototypes that have sharp corners. Other manufacturing processes might not have the capability for it, but the EDM method can get the job done well.
●Metal prototyping for difficult or very hard metal materials.
Some metal materials might be too hard or too difficult to handle for the traditional prototyping process. However, with the EDM manufacturing method, you can melt and vaporize even the hard and difficult metal materials, allowing you to create prototypes from those materials with no problem.
●Creating better finishing without polishing.
You can also use the EDM machining process to create better finishing for your prototypes, even without the need to polish the surface. It’s something that makes this process unique and better than traditional machining processes.
Advantages of EDM Machining and eDM manufacturing
In manufacturing, EDM offers a manufacturing method that can provide certain advantages over regular metal fabrication processes. For instance, you can rely on this process when you can’t create metal prototypes using the traditional machining method. Here are some advantages of the process in manufacturing:
●Fast machining process.
EDM machining can provide a fast machining process to create metal prototypes when compared to regular machining methods, such as traditional milling machining. Thus, it is suitable for rapid prototyping and high production cycles.
●Creating molds.
You can also use the EDM machining method to create molds for various prototyping and volume plastic injection molding service projects. Steel mold materials can be very hard to cut. Thus, the best way to create molds from steel materials is to use the EDM manufacturing process.
●Machining for tight tolerances.
EDM machining can provide you with a very accurate result, so it is suitable for machining with tight tolerances. The tighter the tolerances, the more difficult it will be for you to produce the prototypes based on the design requirements. By using this machining method, you can achieve your goal of producing components, sheet metal parts, or prototypes with tighter tolerances much easier.
EDM Machining and eDM manufacturing Process
The EDM machining works by configuring the equipment to release electrical discharges and then using these electrical discharges on the steel materials you would like to work on. For this process to work, the work environment needs to be submerged in a dielectric fluid. The dielectric fluid will ensure that the machining process will provide a stable result for the metal prototype material.
With the design calculations you have inputted on the EDM equipment, the machine will work on applying the sparks or electrical discharges to melt or vaporize certain parts of the metal materials based on your configurations. This way, you can get the prototype shape you want. After the process is complete, you can remove the prototype from the dielectric fluid and use it for your project.
Using the EDM Machining and EDM manufacturing Process the Best Way
Despite all the benefits of EDM machining, there are also some drawbacks you need to know. For instance, EDM manufacturing will require a lot of power consumption when you use the equipment, which can increase your electricity costs and power usage if you keep on using this method. So, it’s best for you to use EDM in the most efficient way possible. Here are some tips on using the EDM process in the best way:
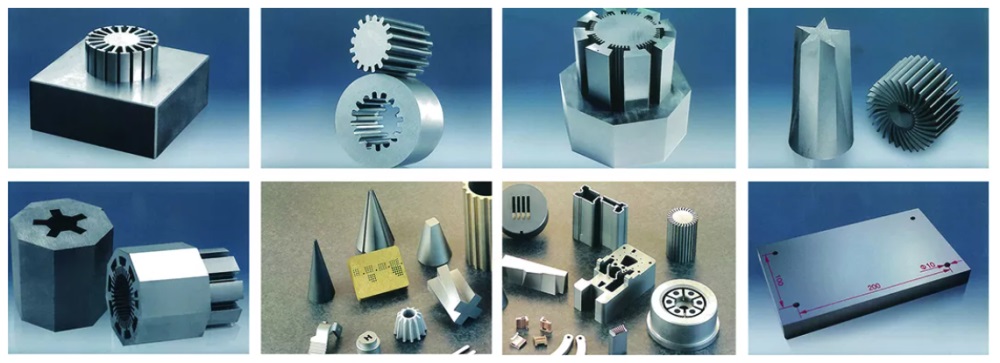
●Use the EDM machining and EDM manufacturing process only for tasks that traditional machining can’t complete.
It’s best to use the EDM machining process for tasks that traditional machining can’t do. This way, you can get more efficiency in working on your prototypes, while keeping your energy usage at a minimum.
●Use the EDM machining and EDM manufacturing method for hard metal materials and complex prototype designs.
EDM machining can cut hard metal materials much better than the traditional or CNC machining process. It can also help create complex prototype shapes with tighter tolerances. Use EDM only when you need to complete these tasks in your manufacturing process.
●Choose the wire EDM instead of the traditional EDM machining and EDM manufacturing equipment.
The traditional EDM equipment will be susceptible to erosion, whereas the wire EDM manufacturing equipment is not susceptible to erosion and will require only minimal maintenance. It’s best for you to use the wire EDM equipment to increase your production efficiency and save a lot more time and resources for the production cycles.
Conclusion
EDM machining is an advanced machining process that allows you to create complex metal prototypes using electrical discharges or sparks. It is suitable for producing metal prototypes that regular machining methods might have difficulty working on.
To get the best result out of the EDM machining method, it’s best for you to use the wire EDM equipment and use it only for tasks that the regular machining methods cannot complete. This can help increase the efficiency of your production and get your prototype manufacturing done faster. Contact us for your upcoming prototyping and molding projects now!