Calculating die casting cost is quite simple. You need to factor in every potential spending in your die casting production, and you will get the total cost. It means you will need to calculate the cost of the die casting equipment, tooling, materials, labor, design fees, potential failures, and other expenses.
It would help if you also considered the taxes and post-finish costs( Such as what is anodized aluminum? What’s the cost?). You can only complete the die casting process by assessing your overall investment. Also, it would help if you prepared for the additional costs you might need to pay, which can be unpredictable. So, it’s best to budget your die casting production cost by factoring in the additional costs.
Table of Contents
Important Factors that Determine Your Die Casting Cost
It would help to consider various factors when planning to start a die casting rapid manufacturing production. It’s about more than acquiring some die casting equipment and materials. Other factors will determine how expensive your die casting process will be. You will need to consider all the factors that determine the die casting cost so that you can prepare the proper spending budget for your die casting production from start to finish. Here are the essential factors:
Design creation.
The design creation cost involves the cost of the design software, the designer’s fees, and the cost of prototyping (trial and error).
Equipment.
You will need to buy the die casting equipment if you don’t have it, or you can rent the equipment through a die casting service. Otherwise, this is quite an expensive cost for you to spend upfront.
Tooling in die casting cost.
Tooling is the cost of creating the die casting molds you will use to create your die casting parts and components. The tooling process can also require prototyping and some trials and errors, which can add more costs for you.
Materials of die casting cost.
You must prepare the die casting materials you will use to create the hardware parts or components you want to produce. Depending on the material quality, the cost can get more expensive for your die casting process.
Workers.
You also need to hire workers to oversee the die casting process and ensure you get the best results in your production. The workers will also inspect the quality of each die casting part you are producing so that you can use it further in your subsequent manufacturing process.
Service fees.
You can use plenty of services to help ensure the best result for your die casting production process. You will need to pay for all these services—another factor you need to consider in determining your overall die casting cost.
Taxes.
You can expect to pay some value-added taxes for your metal die casting production, so you will also need to consider this factor. However, the amount will depend on your area of operation and the government’s regulations.
Packaging of die casting cost.
You will need to pack the completed hardware parts before delivering them to your warehouse. Packing and handling fees should apply here.
Delivery.
It’s the same with delivering the completed hardware parts you have produced. The freight or shipping cost can be a significant factor here, as it will get more expensive depending on the delivery area and the packaging volumes you will need to deliver.
Production failures.
There are also some risks of production failures during the die casting process, which can lose you a lot of money. This risk of failure will also add to more costs for your die casting production.
Energy.
You will need the electricity to power up your die casting equipment. The more die casting equipment you have and the larger your production volume, the more energy cost you will need to pay.
Cleaning.
The die casting process will produce material waste that you will need to clean, so you can keep the process healthy for the environment. You will also need to pay for the cleaning process in your production.
Misc.
You might need to pay unpredictable costs during your die casting production process. So, be sure to prepare for these costs as well.
Tips to Minimize Your Die Casting Cost
Die casting for industrial component can be very expensive, even more so if you want to get the highest quality hardware parts or components out of your production process. Also, all costs can add up quite fast when you start your hardware parts production. However, there’s always a way for you to minimize your casting cost and make the entire process more cost-effective for you.
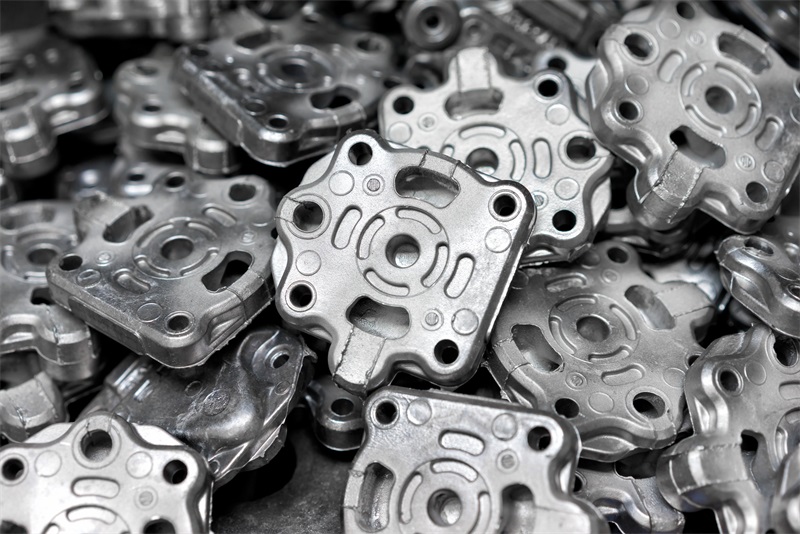
Lower material quality.
The first step is to lower the material quality in your die casting production. Of course, you still need to maintain specific quality standards if you don’t want to lower the quality of the completed hardware parts.
Fewer workers.
You can also hire fewer workers to work on your die casting production process. You might even automate some tasks. It means you can look for a small company for the business.
Less complex design.
The more complex the design of the part, the more cost you will need to pay for the tooling, prototyping, and casting processes. So, you can cut costs when you go with a simpler design for your hardware parts and components.
Efficient prototyping can minimize die casting cost.
Prototyping is creating samples of your hardware parts and components before putting them into full production. The more efficient the prototyping process, the more you can avoid any production mistakes that can cost you a lot of money later. You should look for a high- efficient rapid prototyping services by working with an expert die caster.
Conclusion
Various factors determine the cost of die casting production. It requires quite an expensive initial cost, including equipment, tooling, post machining, and post finishing costs. However, you can reduce the die casting cost by changing certain factors in your die casting operation. You must calculate and prepare for your die casting production’s overall cost before starting the production process.
TEAM Rapid is an ISO 9001 certified manufacturer Of aluminium die casting and zinc die casting. We based In China, and we are geared to handle all your die casting needs. Want to know more, contact us today!