A complex process between art and technology, silicone rubber molding requires a thoughtful combination of design thinking for success In rapid manufacturing, material selection, part and mold design, and precise execution at injection -the curing process defines the difference between mediocrity and excellence -The journey of achieving molding is a journey through the subtleties of physics, geometry and manufacturing craftsmanship, where each design idea becomes a brushstroke shaping the final masterpiece Let’s start looking for a microcosm of it is in silicone rubber manufacturing, where design considerations are not only a technical requirement but manufacture -It is the art of defining the essence of the process.
Table of Contents
Design Considerations
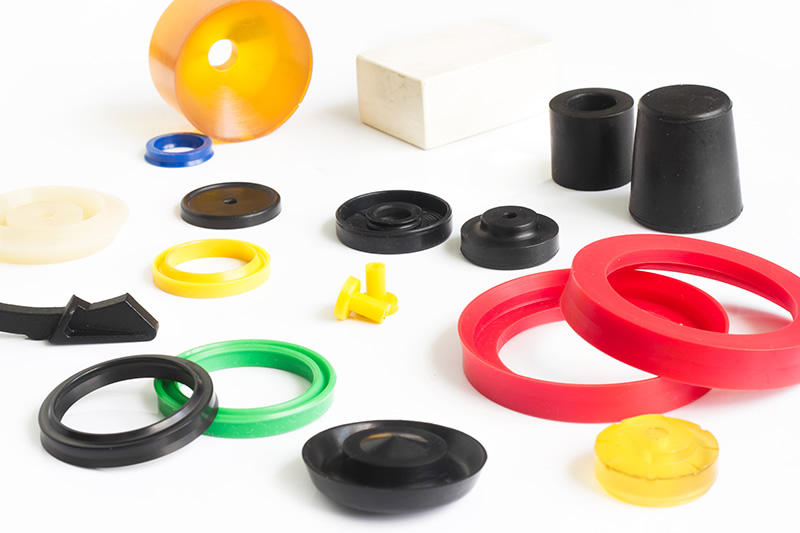
1. Material Selection:
Silicone rubber, regarded for its bend ability, plasticity, and resistance to chemicals, forms the base of successful molding. Customization alternatives for silicone rubber compounds enable tailoring to particular application desires, accentuating the significance of picking materials well suited to the molding procedure.
2. Part Design Considerations:
The geometry of molded parts plays a crucial role in the success of the process. Attention to uniform wall thickness ensures consistent curing, while considerations of draft angles and undercuts facilitate easy demolding, streamlining the manufacturing process.
3. Mold Design considerations:
Material compatibility with molds/rapid tooling is imperative to prevent issues like sticking or bonding. Employing surface finishes and treatments optimizes mold release, and proper venting and degassing ensure complete mold fill for high-quality final products.
4. Injection and Cure Process:
Fine-tuning injection moulding parameters, including pressure, speed, and temperature, is essential for achieving optimal results. Deciding between room temperature vulcanization (RTV) and heat curing influences production speed and part characteristics. Post-cure considerations impact final part properties, demanding precision in execution.
5. Quality Control and Inspection Considerations:
A rigorous quality control process involves visual inspection, dimensional checks, and material property testing. In-process checks during plastic molding provide real-time feedback, and final inspections before release guarantee adherence to specifications, ensuring the reliability of the molded silicone rubber parts.
6. Case Studies:
Real-world examples serve as practical guides, showcasing successful silicone rubber molding projects. Examining the challenges faced and overcome in each case offers valuable insights and lessons learned, contributing to continuous improvement in the molding process.
7. Continuous Improvement:
Silicone rubber molding is an evolving field demanding continuous refinement. Learning from case studies informs ongoing improvements, enhancing efficiency and effectiveness in diverse applications. The adaptability of design considerations to meet changing industry demands ensures the process remains at the forefront of innovation.
8. Balancing Functionality and Aesthetics:
The successful silicone rubber molding transcends beyond mere functionality; it delves into the realm of aesthetics, demanding a delicate balance between material properties to meet both utilitarian and visual requirements.
Dual Nature of Design Considerations
Because of its flexibility and plasticity, silicone rubber has a unique edge when it comes to meeting the aesthetic practical requirements of the material. Silicone rubber textures are twofold, so design considerations must be taken into account to ensure that the finished product is aesthetically pleasing and functional according to purpose.
Visual Aspects to Take Into Account
In many different businesses, including consumer products and medical devices, luxury is crucial. The visual characteristics of objects manufactured using silicone rubber moulds, such as colour, texture, and finish, should be carefully considered by designers. The entire presentation and end-user experience are improved by this meticulous attention to detail.
Tactile Experience
The tactile experience is as crucial as visible aesthetics, especially in human-interactive products. Silicone rubber’s amazing tactile sensitivity is an end result of its gentle, bendy nature, which makes it best to be used in areas like customer electronics, wearable tech, and medical devices.
Design-Related Issues Consider the following: it’s about prioritizing touch and making objects that are enjoyable and cosy to handle.
Tailoring to the preferences of the final user
Due to silicone rubber’s adaptability, items may be made to order and tailored to the desires of the final consumer. To meet consumer expectations and market trends, designers might experiment with various hues, textures, and finishes for their products. This personalization gives designers the ability to make goods that satisfy end customers’ unique tastes in addition to offering perfect performance.
Harmonizing Form and Function
The challenge lies in harmonizing form and function seamlessly. Designers must strike a balance where the aesthetic enhancements do not compromise the functional integrity of the silicone rubber molded part. This requires a nuanced understanding of how alterations in colour, texture, or surface finish may impact material properties, ensuring that the dual objectives are met without compromise.
Industry-Specific Design Considerations
Different industries place varying values on aesthetics. Medical equipment may place a higher priority on cleanliness and simplicity of sterilization than consumer items, which could prioritize aesthetic appeal. Silicone rubber molding mold design considerations have to match the precise functional and aesthetic specifications set forth by industry norms and end-user demands.
Innovation in Design Considerations
Innovation in silicone rubber molding design is not only about meeting established standards but also about pushing boundaries. Creative use of color gradients, texture variations, and innovative surface finishes can set products apart in competitive markets. Forward-thinking designers explore unconventional design choices that not only meet functional specifications but also elevate the product’s overall aesthetic allure.
Environmental Considerations
Exploring sustainable and eco-friendly silicone rubber options aligns with contemporary environmental consciousness. Minimizing waste and optimizing resource utilization underscores the commitment to responsible manufacturing practices in the silicone rubber molding process.
Collaboration and Communication
Effective communication between design, engineering, and manufacturing teams is paramount. Collaborative efforts to address challenges and optimize design for manufacturability result in a seamless integration of expertise. Ensuring alignment with overall business goals and market demands enhances the success of silicone rubber molding projects.
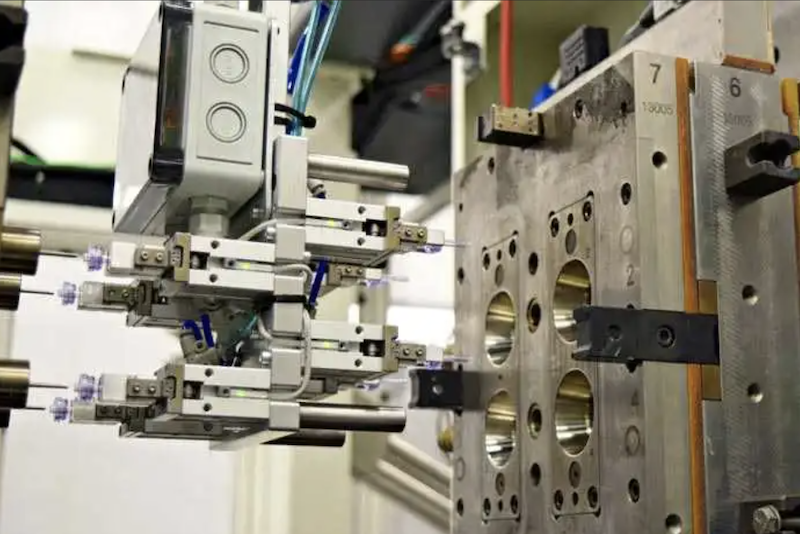
Conclusion
The ultimate artistic ideal in silicone rubber formulation represents a compromise between innovation and precision. As we go through material selection, part and mold design, and careful installation of the injection-cure system, it’s clear that success in silicone rubber molding is a testament to measured technical expertise and creative genius mixed in to make a journey success Not finished; Guided by real-world case studies, it is expanded upon in the context of ongoing artistic development and a commitment to the refinement of practice. In conclusion, the design of successful silicone rubber molds goes beyond mere technical issues; They are the process of transforming materials into functional aesthetic marvels, pushing the boundaries of what can be achieved in the world of architecture.
Besides from injection molding services, TEAM Rapid also offers rapid prototyping, CNC machining, and die casting to meet your needs. Contact us today tor request a free quote now!