Mold tooling is essential in plastic injection molding, shaping the final quality and form of parts or products. Rather than being a single unit, an injection mold comprises multiple components, each with specific roles in a compact design. This article explores the different systems and components of injection mold, illustrating their influence on the mold’s structure and function. It also briefly addresses potential defects and material options for mold manufacturing, offering insights to aid in better decision-making. Let’s dive in!
Table of Contents
What Is Injection Molding?
Injection molding is a prevalent manufacturing technique that forms materials, often plastics, into specific shapes using molds. These molds contain cavities that represent the inverse shape of the desired product. The mold choice greatly impacts the process’s efficiency, cost of injection molding, and product quality.
Types of Injection Molds
There are numerous types of injection molds, each offering distinct production capabilities and assembly configurations for their components and systems. Here are several popular types of injection molds.
Types of Injection Molds | |||
Type | Description | Pros | Cons |
Family Molds | Family molds contain several cavities with unique designs, enabling the simultaneous production of different parts in one cycle. They are generally utilized to create components that will be assembled together. | Versatility: Allows for the production of various injection molding parts at the same time. Lower Tooling Costs: One mold can create multiple parts. | Complex Design & Balancing: Careful design is needed to ensure consistent filling and quality among different parts. Material Limitations: Parts often need to be made from similar materials due to the shared mold environment. |
Two-Plate Molds | Two-plate molds are basic injection molds with a moving and fixed half, meeting at a single parting line. This simple design eases the mold opening to release the finished part. | Simplicity: Easy to use and maintain, offering a straightforward solution for manufacturers. Cost-Effectiveness: Basic design makes them affordable to produce and sustain. | Limited Design Flexibility: Limiting for intricate part designs or those needing multiple gates. Risk of Parting Line Flash: Simple design may cause material leakage at the mold split, affecting product quality. |
Three-Plate Molds | Three-plate molds are sophisticated injection molds that consist of three main plates separated by two parting lines. This design supports complex gating options, enhancing design flexibility and material flow, which leads to higher-quality products. | Improved Design Flexibility: Support producing more complex and detailed parts. Better Gating Options: Allow for optimal placement of gates, enhancing part quality. Enhanced Material Flow: Better control over the flow of material for higher-quality products. | Increased Complexity: More intricate design compared to two-plate molds. Higher Costs: More expensive to manufacture and maintain. Skilled Operation Needed: Additional complexity needs more expertise to operate effectively. |
Stack Molds | Stack molds have multiple cavity levels and parting planes, allowing them to produce multiple parts per cycle. This design increases output without requiring extra clamping force or larger machines. | Increased Production Efficiency: This can produce multiple parts per cycle for higher output and productivity. Reduced Cycle Times: This can minimize production cycle time by producing more parts simultaneously. Space Optimization: Saving floor space without the need for larger machines. | Higher Initial Costs: The intricate design of stack molds leads to higher initial costs for both design and manufacturing. Maintenance Challenges: The multi-level structure can lead to more complicated maintenance and potential downtime if issues emerge. |
Unscrewing Molds | Unscrewing molds are specialized tools that create threaded parts by using a rotating core mechanism. This is essential for creating parts with internal or external threads, like bottle caps and connectors. | Precision: Ensure high precision in the production of threaded parts, critical for ensuring a perfect fit and function. Uniformity: Ensure consistent thread quality, crucial for preserving the parts’ integrity and performance. Efficiency: Automated unscrewing process streamlines production for shorter cycle times. | Complexity: More complex than standard molds due to the need for moving parts and mechanisms to rotate the core. Cost: Higher design and manufacturing costs may impact the overall budget. Maintenance: The intricate mechanisms require regular maintenance to ensure reliability and minimize downtime. |
Insert Molds | Insert molds integrate metallic inserts into injection-molded parts, encapsulating them with the material. Used for threading components and electronic connectors, inserts can be placed manually or automatically with robots or feeders for precise alignment before molding. | Enhanced Part Strength: Using inserts in molded parts enhances their mechanical properties, strength and durability, especially beneficial for load-bearing applications. Material Efficiency: Combine multiple materials in a single part without extra assembly, optimizing material use and minimizing waste. Design Flexibility: Integrates components like bushings directly into molds, enhancing functionality without extra steps or complexity. | Potential Cost: Additional steps and precision hike setup costs, impacting cost-effectiveness for small production runs. Maintenance: Intricate mold setups and material integration increase maintenance frequency, causing more potential downtime. |
Multi-Shot Molds | This tooling creates multi-colored, multi-material parts using multiple injectors and a rotating or shifting mechanism to layer successive shots over the initial one. | Efficiency: Eliminating secondary operations like assembling multiple components, thus saving time. Design Flexibility: Facilitates complex designs by integrating diverse textures, colors, and functions into a single seamless part. Optimize material usage: Apply precisely what’s needed for each section of the part. | Increased Complexity: Sophisticated machinery and precise control are needed to ensure proper material flow and bonding, adding complexity to the production setup. Increased Upfront Expenses: Specialized equipment and tooling requirements can lead to higher initial setup costs. |
Main Components of Injection Molds
Injection molding facilitates the precise and efficient production of intricate plastic parts. At the heart of this process lie the injection molds, especially the Cavity A Side (Stationary Side) and Cavity B Side (Moving Side), which work together seamlessly to form the final product.
Cavity A Side (Stationary Side)
Cavity Side A, fixed to the molding machine’s stationary plate, stays immobile during the cycle. It houses the runner system and aligns precisely with the moving Side B using guide pins and bushings. Additionally, this side includes cooling channels to circulate coolants as the material solidifies.
Cavity B Side (Moving Side)
The Cavity B Side, known as the moving side, is responsible for opening and closing during the molding process. It typically contains an ejector system and insert holder, mounted on the machine’s movable platen. Proper movement and alignment of this cavity are crucial for achieving precise dimensions and ensuring the smooth release of finished parts.
Components of Injection Molds by Function
After discussing the core components, here we will analyze the injection mold components according to their functionality. Some of them are responsible for transferring raw materials, guiding mold operations like opening and closing, and providing cooling. Each set of parts is specifically designed to perform distinct tasks for desired results.
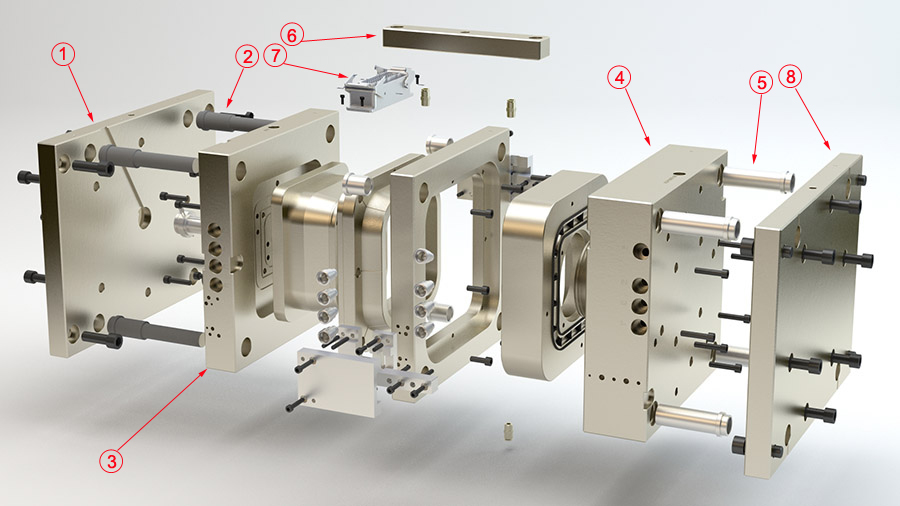
Runner System
The runner system is responsible for channeling molten material from the barrel nozzle to the injection gate, which leads into the mold cavity. This system may also consist of a network of channels to distribute the material efficiently in multi-cavity molds.
A typical runner system in an injection mold includes several key components:
- Sprue Bushing
- Runner Network
- Gate
When considering pressure and temperature in the runner components of an injection mold, the nozzle plays a key role by maintaining high injection pressure to ensure a consistent material flow. Runner systems can be cold or hot: cold runners simply guide the material without additional heating, while hot runners include heating elements to maintain temperature and prevent early solidification.
Components of Injection Mold: Cooling System
The cooling phase is vital in injection molding, taking up 50 to 80% of the process time, and is essential for creating defect-free plastic parts. The cooling system, a network of water lines or sometimes ethylene glycol and oils for high temperatures, surrounds the main cavity to shape the molten material. It allows precise control of temperature and flow, preventing warping, boosting production efficiency, and reducing mold wear.
In complex and large molds, water circulation is conformal rather than in straight lines. The cooling system components include:
- Baffles
- Thermal Pins
- External Pump
- Bubblers
Components of Injection Mold: Molding Components System
These essential elements of an injection mold define the parts’ final shape, dimensions, and accuracy. They define the surface details and internal features, including elements like the core, molding rod, cavity, and lifter. You can identify these components by their direct contact with the material as it enters the cavity from the gate.
The molding system includes key components:
- Mold Cavity
- Core
- Molding Sliders
- Lifters
Components of Injection Mold: Venting System
Trapped air and gases during molding can cause defects such as voids, burn marks, bubbles, weak spots, and incomplete filling. To address these issues, a venting system is crucial in injection molds to expel trapped air and manage injection pressure. In simpler molds, vents are typically located along the plating line and include vent pins on the cavity body. However, as mold complexity increases, the venting system components also become more intricate.
Here are other common venting systems:
- Grooves and Channels
- Air Vacuuming
- Venting Valves
- Vents Around the Components
Guiding System
The guiding system components are essential for maintaining the alignment of mold halves and other elements during each open and close cycle. They are essential for maintaining precision and consistency in the molding process. As repetitive clamping forces can cause misalignment, components such as guide pins, bushes, and plates are employed to prevent these deviations.
Ejector System
After the part has cooled and solidified, the mold opens, and the ejector system safely extracts the parts and runners. Ejector pins, thin cylindrical pins fixed to an ejector plate on the moving side, are used to ensure even force distribution, preventing damage to the parts.
Other components often include:
- Return Pins
- Ejector Sleeves
Components of Injection Mold by Structure
Injection mold components can be categorized based on their structural attributes. This classification method allows for a deeper understanding of how each part functions within the overall mold assembly.
Mold Base
The mold base acts as the crucial support system for the entire mold setup, holding various components securely in place. Made with robust and durable materials like hardened steel, it offers the essential structural resilience needed to endure the substantial pressures encountered during the injection molding process. This construction ensures precise alignment and consistent stability, thus minimizing wear and tear on the more delicate components of the mold assembly.
Components of Injection Mold: Mold Core
The mold core shapes the hollow and internal features of a part by combining with the cavity. It supports the structure and handles some clamping pressure, often featuring rounded corners and draft angles. Proper alignment with the cavity creates a space for the molten plastic. Following molding, the core retracts, and the ejection system removes the part. Core pulling can be mechanical, hydraulic, or pneumatic.
Auxiliary Parts
Auxiliary parts are temporary components that support the function of injection mold parts without being part of the mold structure. While they don’t influence shape or geometry, they are vital for ensuring tight tolerances, structural integrity, and the overall quality of molded plastic parts. These may include:
- Locating Ring
- Sprue Bushing
- Ejector Pins
- Material Grabber
- Support Pillers
- Ejector Plate
- Guide Pins and Bushes
- Ejector Retainer Pin
Auxiliary Systems
Auxiliary systems support the injection molding process, similar to auxiliary parts. Examples include the runner, ejection, and cooling systems.
Auxiliary Setups
The primary auxiliary setups in injection molds include lifting eye bolt holes and KO holes, which aid in mold transfer and support the ejection process.
Components of Injection Mold: Dead Corner Handling Structures
Dead corners are hard-to-reach areas in processing, like undercuts and deep channels. Structures such as angle ejectors, hydraulic cylinders, and slides help manage these complexities.
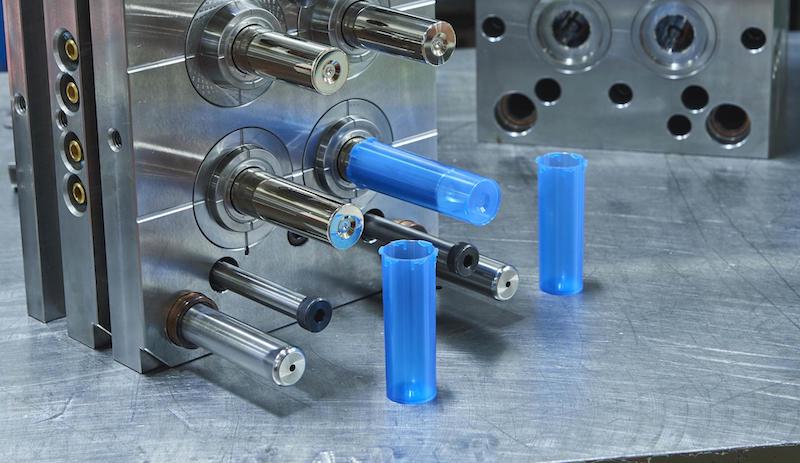
Conclusion
Each component of an injection mold works in harmony to produce high-quality molded parts efficiently. Whether you’re new or experienced in manufacturing, knowing the basics of injection mold components helps you better deal with the injection molding process and handle your projects.
TEAM Rapid Tooling offers a full spectrum of injection molding services, where precision mold machining with CNC, EDM, and other advanced techniques meets an array of surface finishing options to perfect your products. Step into superior results on every project by uploading your design files to our user-friendly online platform today!