Aside from metals, plastic materials are the most common materials used in the automotive industry. With the various plastic materials available to use, such as ABS, PVC, polyurethane, and many others, automotive manufacturers can pick the ones that will be the best fit for their production needs. Different vehicles will need to use different plastic materials in their production process. This guide will help you learn about the plastic materials used in the automotive industry.
Table of Contents
What are the Plastic Materials Used in the Automotive industry?
Manufacturers use various types of plastic and metal materials in the automotive industry to build their vehicles. You can find plastic materials being used for producing various parts of the vehicle’s exterior and interior, which include the dashboard, bumper, vehicle body, small gears, tires, and many others.
Some plastic materials have two forms, which are soft and hard forms. Manufacturers use the soft forms to produce parts like tires, insulator cables, seating, and so on, whereas the hard forms get used for various other parts, such as the dashboard, bumpers, small gears, and many others in the automotive industry.
There are plenty of plastic material variations available today, which are common in the automotive industry. Each plastic material has its own characteristics, which include material properties, benefits, and weaknesses. The manufacturers will use different materials depending on their characteristics and features, through different manufacturing processes such as CNC turning or CNC milling service, etc. to get the end products of their expectation.
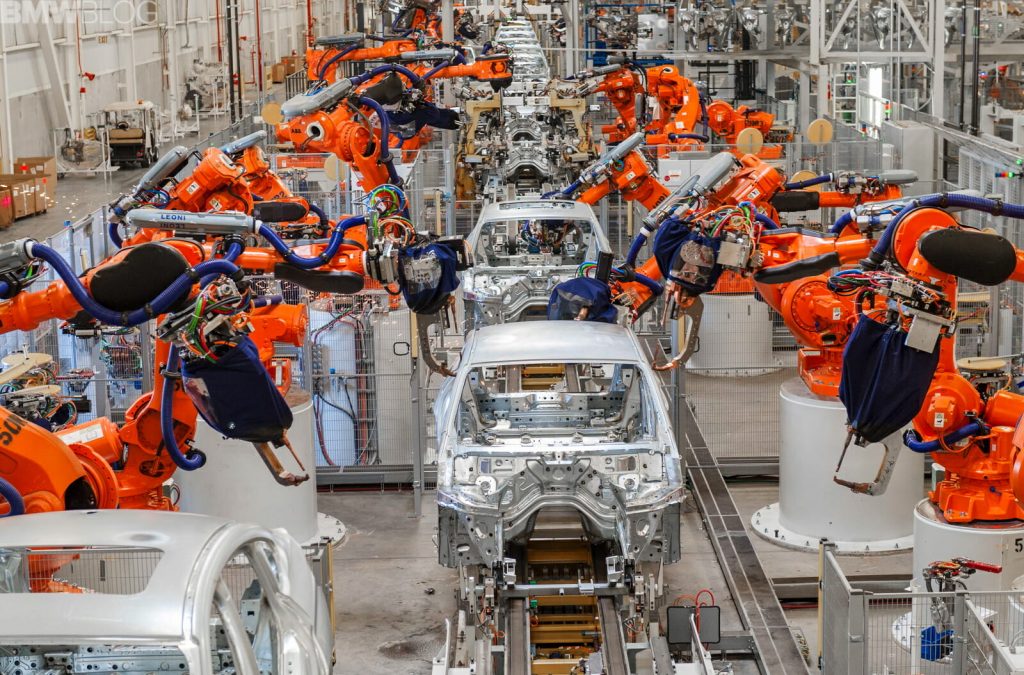
Plastic Materials Used in the Automotive Industry
There are various types of plastic materials that automotive manufacturers will use in their rapid manufacturing and production process. Manufacturers need to use the right plastic materials to get the best results for their vehicle production, as well as to ensure the long-term use of the vehicles. Here are the plastic materials used in the automotive industry:
●ABS
This plastic material is very commonly used for vehicle wheel covers and dashboards in the automotive industry. This material is also resistant to chemical corrosion and physical impact. Aside from that, you can produce a shiny and durable exterior with ABS plastic material.
●Polyurethane
This material has two forms, which are soft and hard forms. You can often find polyurethane in various vehicle applications, including tires, seats, and others. It has the characteristics of high tear and high tensile resistance, along with strong bonding properties, high performance in challenging environments, and so on.
●Polypropylene
You can find polypropylene in various parts of the vehicle, which include bumpers, cables, carpet fibers, and more. This material is lightweight, and it has the characteristics of impact resistance, high chemical resistance, and low moisture absorption in the automotive industry.
●Nylon 6/6
This is a plastic material that has top material strength, and high durability, it also offers high resistance from wear and tear. You can produce various vehicle parts with nylon 6/6, and manufacturers can save their production costs when they use this material. You can also find nylon 6/6 to be a suitable material for weatherproof coatings in some vehicles.
●Polyvinyl chloride (PVC)
PVC is a common material used in both the exterior and interior parts of the vehicle. It has soft and hard forms, and manufacturers can pick the form best suited for their production requirements. PVC has the characteristics of heat resistance, flexibility, high density, high durability, and strength.
●Polycarbonate
Most vehicle bumpers nowadays in the automotive industry use polycarbonate as their primary material. It is weatherproof and heat resistant, and it also has a reliable hardness, rigidity, and durability. It also has high impact resistance, perfect for producing bumpers to minimize the vehicle’s damages during a crash.
●Polyoxymethylene (POM)
Besides the rapid sheet metal parts, Manufacturers use this plastic material to produce various vehicle parts, which include small gears, fuel system parts, and trims. It has the characteristics of high strength, excellent impact resistance, great sliding properties, wear resistance, and low moisture absorption.
●Polyethylene
For vehicle bodies with glass reinforcements, polyethylene is the most suitable plastic material manufacturers can use in their parts production. It’s also best for electrical insulation in the vehicle. This material has the characteristics of puncture resistance, heat seal-ability, durability, moisture resistance, and low density.
The Plastic Injection Molding Service in the Automotive Industry
To produce the hardware parts using plastic materials, the automotive industry manufacturers will use the injection molding process to get it done. Most automotive parts production processes use the injection molding system to process the various plastic materials and mold them into certain shapes and designs. Injection molding is also useful to produce prototypes for various vehicle parts before they get into the mass production cycles. Here are some benefits of the plastic injection molding process in the automotive industry:
●Cost-effectiveness for the automotive industry.
Most plastic materials are affordable, and they are cheaper than metals. Manufacturers use various plastic materials in the insert molding and overmolding to cut costs of production, even more so for the large production cycles. The more they produce plastic parts, the more they can keep the costs down.
●Scalability.
With plastic injection molding, manufacturers can also scale their production volumes depending on their needs. For instance, they can start by producing certain prototypes for their automotive parts and components. Then, they can put them into mass production with no hassles when the prototypes can deliver the features they need.
●Material compatibility for the automotive industry.
Injection molding can accommodate various plastic materials, so there will be no problem for the manufacturers to pick the right materials for their automotive parts production. They can even try different plastic materials for the same automotive parts before picking the best one.
●Accuracy and repeatability for the automotive industry.
The injection molding system can deliver the best accuracy for each automotive part. Precision is important because these parts need to work with other parts to ensure the best overall performance for the vehicle. Also, injection molding offers repeatability for the manufacturers to produce the same parts repeatedly, with no loss in quality.
●Surface finishes and color options.
With injection molding, automotive manufacturers can also pick the right surface finish and color option for each vehicle part they are producing. It will allow them to create variations for their automotive parts and components.
Conclusion
Various types of plastic materials are being used in the automotive industry to make various vehicle parts, starting from the exterior parts, such as bumpers, to the interior parts, such as the dashboard and seating. Each plastic material will have certain characteristics that are best suited for certain parts of the vehicle.
Also, automotive manufacturers use cheap 3d print service, metal die casting, and injection molding to process plastic materials into ready-to-use parts and components. TEAM Rapid offers a series of manufacturing methods from rapid prototyping services to mass production to meet your needs, contact us today to request a free quote now!