In the complex world of injection moulding, where precision meets innovation, molding threads are still time-critical. Although wires are used extensively in a variety of sectors, including consumer electronics and the automobile, they are not without difficulty in the process of going from design to finished wireless products. Manufacturers encounter several obstacles in their pursuit of excellence in their injection molding systems, obstacles that call for creativity and knowledge to solve. This piece explores the intricate world of injection molding formulations, highlighting typical problems that producers encounter and providing creative fixes. From the design to the material considerations and details of the molding process, every part of the process is unique. Challenges, which, if not addressed, can compromise product quality and performance.
Join us as we take you on a tour through the complexities of injection moulding threads and reveal the issues that might prevent the smooth manufacture of threaded goods. By comprehending these obstacles and investigating efficacious resolutions, producers may enhance their plastic molding procedures, guaranteeing the production of superior threaded parts that satisfy the exacting specifications of many sectors.
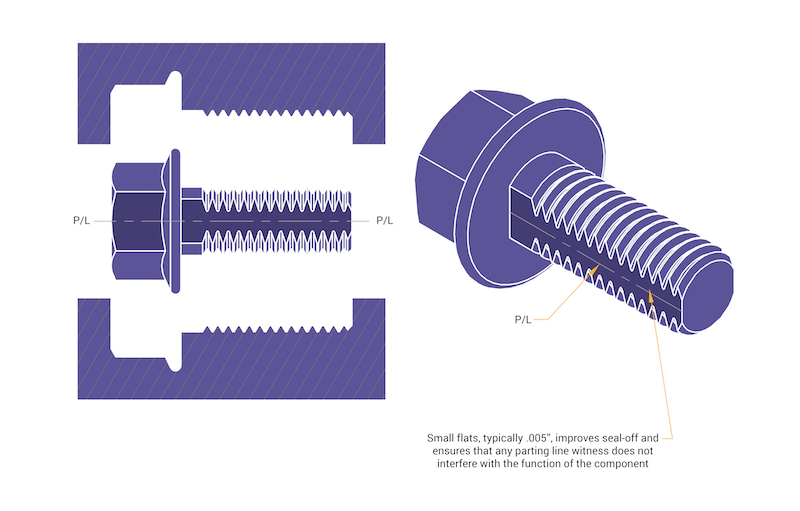
Table of Contents
- 1 Molding Threads: Thread Warping
- 2 Molding Threads: Uneven Shrinkage
- 3 Molding Threads: Flash Formation
- 4 Molding Threads: Inadequate Fill
- 5 Material Flow Issues
- 6 Mold Release Difficulty
- 7 Strength and Durability of molding Threads
- 8 Molding Threads: Tooling Wear
- 9 Molding Threads: Dimensional Variation
- 10 Molding Threads: Residual Stress
- 11 Molding Threads: Sink Marks
- 12 Conclusion
Molding Threads: Thread Warping
Challenge
Threads are prone to warping or distortion during the cooling phase, leading to dimensional inaccuracies.
Solution
Employ advanced cooling techniques, such as conformal cooling channels, to ensure uniform temperature distribution. Adjust mold temperature and injection pressure settings to prevent uneven cooling. Employing materials with lower coefficients of thermal expansion can also mitigate warping.
Molding Threads: Uneven Shrinkage
Challenge
Threads may experience uneven shrinkage, resulting in dimensional variations and compromised thread molding integrity.
Solution
Incorporate homogeneous wall thickness and suitable radii at the thread roots and crests to optimize the mold design. To obtain a more balanced shrinkage profile, choose materials with lesser shrinkage qualities or think about mixing elements. Potential shrinkage problems may be anticipated and addressed with the use of mold flow analysis simulations.
Molding Threads: Flash Formation
Challenge
Excess material or flash may form at the thread edges during injection molding.
Solution
Fine-tune the mold design to minimize pressure variations and enhance mold closing precision. Implement tighter tolerances and precision CNC machining for mold components. Utilize advanced molding technologies like gas-assisted injection molding to reduce the likelihood of flash formation.
Molding Threads: Inadequate Fill
Challenge
Incomplete filling of the mold cavities, particularly in intricate thread patterns.
Solution
Optimize injection parameters, including speed, pressure, and temperature, to ensure complete cavity filling. Employ materials with high-flow characteristics to enhance moldability. Adjust gate size and location to facilitate optimal material flow into intricate thread features. Utilize mold flow simulations to analyze and optimize the injection process.
Material Flow Issues
Molding Threads’ Challenge
Poor material flow can result in inconsistent or incomplete threads.
Molding Threads’ Solution
Evaluate and optimize gate design, size, and location to enhance material flow. Utilize materials with excellent flow properties, such as those with lower viscosity. Consider the rheological behaviour of the material, and if needed, incorporate flow enhancers or nucleating agents to improve material flow during the injection.
Mold Release Difficulty
Challenge
Threads may stick to the mold, making demolding challenging.
Solution
Apply appropriate mold release agents compatible with the chosen molding material to prevent sticking. Optimize mold surface finishes and textures for easy release. Implement draft angles on thread surfaces to facilitate demolding without causing damage to the threads or the mold.
Strength and Durability of molding Threads
Challenge
Getting the molded threads to have the appropriate mechanical qualities, strength, and longevity.
Solution
Choose materials with the necessary mechanical properties, taking wear resistance, impact resistance, and tensile strength into account. Consider adding reinforcements, such as carbon or glass fibers, to improve thread strength. Rapid prototypes should undergo mechanical testing to confirm the material’s functionality in real-world settings.
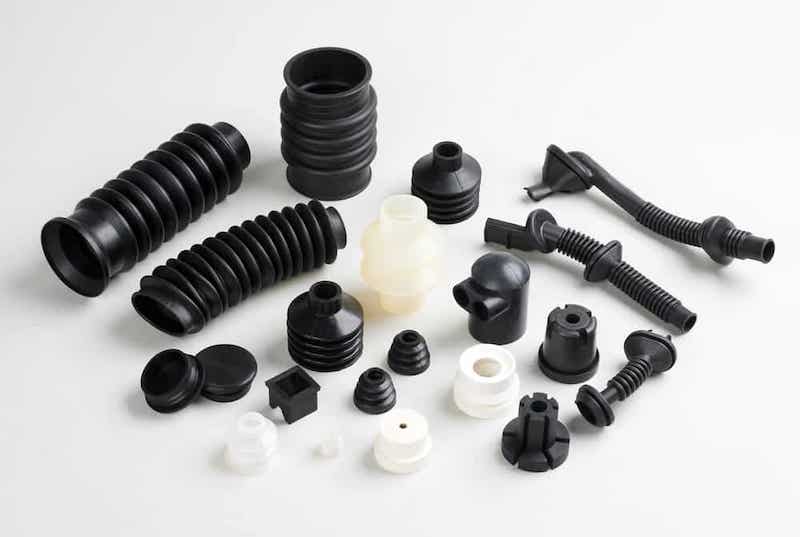
Molding Threads: Tooling Wear
Challenge
Excessive wear on molds can affect thread quality and lead to increased production downtime.
Solution
Use premium tool steel and coatings that are resistant to wear and abrasion. Performed routine maintenance programs, including cleaning, lubrication, and inspection of manufactured parts. Use corrosion-resistant coatings such as nitriding or physical vapour deposition (PVD) to improve yarn quality and extend tool life in many weaving machines.
Molding Threads: Dimensional Variation
Challenge
Inconsistent thread dimensions may result in products that do not meet specifications.
Solution
Implement rigorous process control measures to monitor and adjust critical parameters, including injection pressure, temperature, and cooling rates. Conduct regular inspections using precision measurement tools to ensure dimensional accuracy. Employ statistical process control (SPC) techniques to identify and address variations in real-time.
Molding Threads: Residual Stress
Challenge
The performance and lifespan of molded threads might be adversely affected by residual strains.
Solution
To reduce residual stresses during the molding process, optimize cycle times and cooling rates. Consider post-molding treatments such as annealing or stress-relieving processes to alleviate residual stresses. Utilize advanced simulation tools to predict and analyze residual stresses during the design phase and adjust accordingly.
Molding Threads: Sink Marks
Challenge
Sink marks can form on the surface of molded threads, especially in areas with variations in wall thickness.
Solution
Design the mold with consistent wall thickness throughout the thread geometry to minimize differential cooling and avoid sink marks. Modify gate locations to optimize material flow and distribution. Adjust injection parameters, such as packing pressure and time, to alleviate the formation of sink marks. Additionally, consider using materials with higher melt flow rates to improve the packing of material into the mold cavity, reducing the likelihood of sink marks. Conduct mold flow simulations to identify potential sink mark issues during the rapid tooling design phase and implement preventative measures accordingly.
Conclusion
In injection molding where accuracy is paramount, the challenges faced in threading components serve as evidence of a complex manufacturing process. As we go into the intricacies of design, material selection, and moulding process, it becomes clear how flawlessly threaded barrier-filled materials With insight, manufacturers can turn obstacles into opportunities for growth. By embracing advances in technology, material choice reduction, and design efficiency, the injection molding industry can pave the way for increased efficiency and unmatched quality in threaded component production. Whereas we conclude this research, it is clear that the mixture of knowledge and innovation is injection. Weaving is key to overcoming challenges and ensuring a future of continuous accuracy and excellence. Contact TEAM Rapid today for your injection molding projects.