Clear plastic molding is critical to manufacturing, which presents specific challenges. This piece delves into these obstacles, unveiling practical solutions to deepen comprehension and propel progress in the industry. Look carefully at the intricacies of the situation; the exploration traverses complexities, shedding light on inventive troubleshooting. The story unveils pivotal elements that mold the landscape of clear plastic molding, offering a thorough guide for both novices and experts in the field.
Table of Contents
Exploring the Realm of Transparent Plastic Molding
At the forefront of manufacturing, transparent plastic moulding stands as a pivotal force. Meticulously shaping transparent products that beckon with an irresistible see-through allure. This intricate process involves injecting molten plastic into a mold cavity, which adopts the desired form as it cools and solidifies.
Diverse materials, including Acrylic (PMMA), High-density Polyethylene (HDPE), Polycarbonate (PC), and Polyetherimide (PEI), take center stage in the realm of transparent plastic injection molding. Their selection hinges on unique properties tailored for specific applications, ranging from strength to temperature resistance and chemical resilience.
The resulting transparent components, aptly named clear plastic parts, assume crucial roles in sectors prioritizing visibility. These components are manufactured using molding techniques such as injection molding, blow molding and thermoforming and have found their way into various industries.
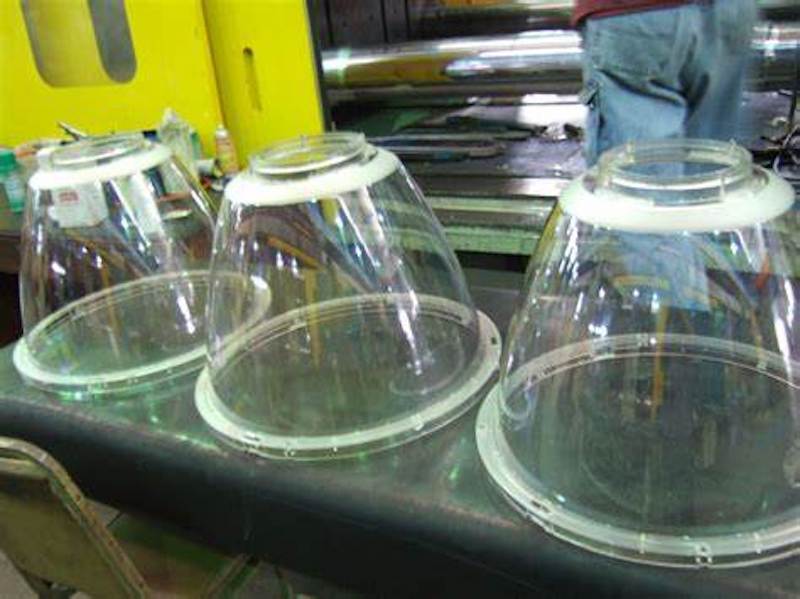
In the automotive domain, transparent plastic injection moulding leaves its mark on components like headlights, taillights, and instrument panels. Meanwhile, the medical field harnesses this technique for creating essential devices, including syringes, IV bags, and medical imaging equipment. Transparent plastic molding has proven its versatility by extending the range of applications to packaging applications such as food, toys, electronics, cosmetics and homewares.
The scope of transparent plastic molding reaches beyond tangible products. It encompasses lenses for eyewear, cameras, optical devices, displays for electronic gadgets, and housings for various appliances. Its significance lies in a distinct advantage—transparency. This coveted feature permeates light, proving indispensable for applications such as windows, lenses, and displays. Clear plastic molding outperforms alternative techniques and leaves an indelible mark on industries like packaging, healthcare, automotive, and consumer electronics. Through the delivery of cost-effective, high-quality solutions, it stands as a transformative force, reshaping manufacturing landscapes and fostering innovation in the process.
Despite the numerous merits attributed to transparent plastic molding, it is not immune to challenges that can impact both the final product’s quality and the molding process’s efficiency. Let’s dissect some prevalent challenges encountered in clear plastic molding:
Short Shots
• Definition: Insufficient filling of the mold cavity.
• Causes: Low die temperature, material temperature, or injection pressure. Other contributing factors include uneven plasticization, poor exhaust, liquidity issues with raw materials, or premature polymer melt curing due to structural design flaws.
Air Traps
• Definition: Occurs when air becomes trapped in the cavity, resulting in bubbles in the final product.
• Mitigation: Requires meticulous attention to parting surface, ram, and vent dynamics during the molding process.
Brittleness
• Definition: Plastic parts prone to cracking or breaking.
• Causes: Inadequate drying, excessive use of recycled materials, incorrect injection temperature, or inappropriate gate and runner system settings.
Silver Streak
• Definition: Common during filling and cooling, characterized by expansion weakening plastic parts.
• Cause: Often induced by the presence of wet resin.
Air Bubble
• Definition: Inadequate filling and excessive cooling can trap water and air in the cavity, leading to vacuum bubbles.
Surface Gloss Defects
• Causes: Poor mold surface polishing or rapid cooling can result in defects, hindering the resin from achieving a desired molded state.
Flow Marks
• Causes: Large melt viscosity and condensed melt flow in the cavity can cause flow marks on the surface.
These challenges find real-world manifestations across industries. For instance, in the automotive sector, clear plastic parts like headlights and taillights may exhibit brittleness or surface gloss defects if molding precision is compromised. Similarly, the medical field, with clear plastic parts such as syringes and IV bags, faces challenges like air traps or flow marks without meticulous molding control. These tangible examples underscore the critical need for precision in addressing challenges to ensure optimal outcomes in clear plastic molding.
Precision Solutions for Clear Plastic Molding Challenges
Meeting the challenges head-on in transparent plastic molding demands a symphony of precision and strategic low volume manufacturing services solutions. Let’s dissect these hurdles and unveil the exacting measures required:
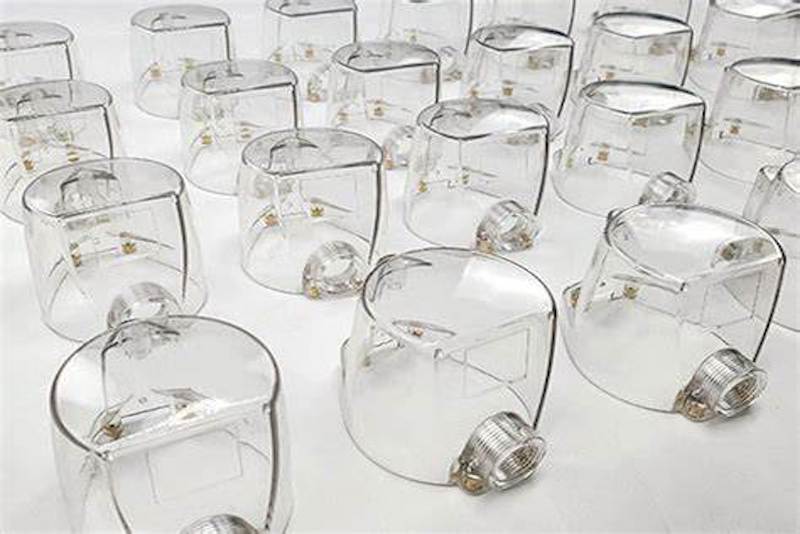
Clear Plastic Molding solutions for Short Shots
Comprehensive Optimization
• Fine-tune die and material temperatures, injection pressure, and speed.
• Ensure meticulous uniformity in plasticization, exhaust, and material liquidity.
• Guard against premature curing through structural enhancements.
clear plastic molding solutions for Air Traps
• Refined Design Dynamics: Enhance mold and vent design for a seamless escape of air during the convergence of melt fronts.
clear plastic molding solutions for Brittleness
Essential Adjustments
• Uphold optimal dry conditions.
• Exercise controlled management of recycled material usage.
• Fine-tune injection temperatures and precision-tailor gate and runner system settings.
Silver Streak
Vigilant Resin Management
• Exercise vigilant control over resin management to mitigate expansion.
• Ensure a pristine, dry resin environment to effectively counter silver streak challenges.
Air Bubbles
• Meticulous Control: Exercise meticulous control over filling and cooling parameters to counter the formation of air bubbles.
Surface Gloss Defects
Precision Polishing
• Implement precise mold surface polishing techniques.
• Exercise control over cooling rates, allowing the resin to attain an optimal molded state.
Flow Marks
• Viscosity Management: Mitigate flow marks by judiciously managing melt viscosity and ensuring a balanced flow during cavity filling.
These solutions, executed with surgical precision, pave the way for success in transparent plastic molding. In the automotive sector, manufacturers deploy cutting-edge mold technologies, orchestrating temperature control and optimizing injection parameters to ensure that clear plastic parts meet and exceed stringent quality standards. Similarly, in the medical industry, the deployment of precision molding machines coupled with continuous process monitoring guarantees transparency in products like syringes and IV bags, free from air traps or flow marks.
Revolutionizing the Clear Plastic Molding Landscape
The implementation of targeted solutions to address challenges in clear plastic molding has ushered in a new era of quality and efficiency within the industry. These strategic measures not only minimize unplanned downtime but also alleviate material cost pressures and regulate process variations, resulting in the production of top-tier plastic parts. The ripple effect of this positive impact extends across diverse sectors, leaving an indelible mark on industries such as automotive, healthcare, and consumer electronics.
As regulatory landscapes shift towards sustainable practices, these solutions emerge as linchpins in the industry’s response to the pressing issue of plastic pollution. With a concerted focus on circular economy models, the clear plastic molding(including overmolding and insert molding) industry is poised to play a crucial role in mitigating environmental impacts. This transformative journey not only enhances the industry’s current standing but also sets the stage for future investments and widespread adoption of sustainable practices, ensuring a greener and more responsible future for clear plastic molding.
Conclusion
When faced with challenges like short shots and air traps, the clear plastic molding industry has seamlessly incorporated robust solutions. Through the meticulous optimization of injection parameters and the embrace of cutting-edge mold technologies, the industry boldly signifies an ongoing evolution. Envisioning a future characterized by heightened efficiency and sustainability, clear plastic molding stands as a symbol of continuous innovation and enduring growth.
Besides from injection molding, TEAM Rapid also offers rapid prototyping, CNC machining and die casting to meet your projects needs. Contact our team today to request a free quote now!