Clear Plastic Molding stands as a vital force within manufacturing, holding a key position in the ever-changing realm of consumer electronics. It meets the industry’s demand for components that strike a balance between affordability, durability, and visual appeal. This technique dynamically shapes market forces, seamlessly adjusting to the swift evolution of electronic devices.
Table of Contents
Deciphering Clear Plastic Molding
Clear Plastic Molding, a dynamic rapid manufacturing process that sculpts plastic through molds. Bestows unparalleled design flexibility onto objects of diverse sizes and intricacies. Its utility spans in many sectors, including automotive, packaging, and consumer electronics, underscoring its versatility. This technique adeptly caters to both rudimentary and highly intricate designs, establishing it as the preferred choice in the contemporary landscape of manufacturing. Its favorability is rooted in its capacity to embrace designs. Ranging from the straightforward to the highly detailed, positioning it as a cornerstone in modern manufacturing practices.
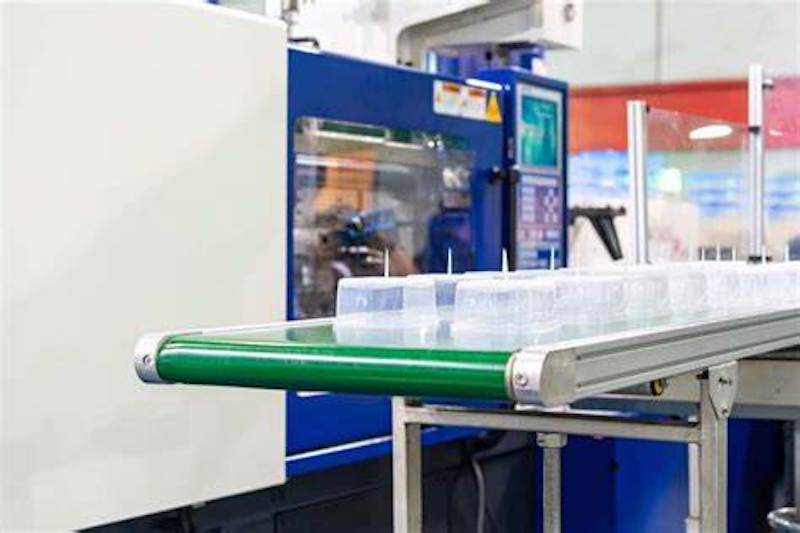
Varieties of Clear Plastics
The varieties of clear plastics deployed in injection molding processes present a rich tapestry of properties and applications. Polycarbonate (PC), renowned for its robustness and high heat resistance, finds a valuable niche in electronic components and medical devices. Acrylic (PMMA), acclaimed for its resilience against weather and UV rays, coupled with optical clarity, assumes a prominent role in lenses, outdoor signage, and automotive components. Polyethylene Terephthalate (PET), a clear, resilient, and lightweight plastic, enjoys widespread usage in packaging, encompassing bottles and containers. Despite its usual opaqueness, Polyvinyl Chloride (PVC) showcases versatility in applications ranging from pipes and window frames to electronics packaging.
Clear Plastic Molding Process
The process of clear plastic molding unfurls through a systematic sequence. The plastic undergoes controlled heating until it attains a liquid state. Post-heating, the plastic seamlessly transitions into a liquid form. This molten substance is then injected into a mold, where it undergoes a meticulous cooling and solidification process. Once solidified, the mold unfurls, and the finalized component is gracefully ejected, paving the way for efficient mass production with minimal waste. This methodology assures a pinnacle of precision in the final products, spotlighting the effectiveness of clear plastic molding in attaining manufacturing goals.
Nurturing Consumer Electronics
Within the intricate tapestry of consumer electronics, Clear Plastic Molding assumes a pivotal role, contributing substantially to the structure and operation of various devices. Its significance lies in the seamless integration of durable, cost-effective, and visually appealing components, establishing a benchmark in consumer electronics.
Precision in Consumer Electronics Device Crafting
Consumer electronics reap immense benefits from the precision afforded by clear plastic molding, enabling the crafting of intricate parts with unparalleled accuracy. This precision becomes especially crucial in devices where dimensions and functionalities tightly intertwine, necessitating a meticulous manufacturing process.
Examples in Consumer Electronics
The impact of clear plastic molding on consumer electronics is vividly illustrated through tangible examples. Take smartphones, for instance, which harness transparent molding to craft casings boasting sleek designs while providing robust protection to delicate internal components.
The application is not limited to smartphones but also extends to wearable devices, where the molding process plays a key role in achieving a harmonious blend of aesthetics and functionality. Wearable devices, too, depend on the molding process to seamlessly integrate visual appeal with functionality, embodying a delicate balance crucial for these compact, multifunctional gadgets.
The automotive sector also embraces clear plastic molding in consumer electronics, as seen in the production of clear plastic lenses for headlights. It exemplifies the technique’s vital role in the automotive sector’s pursuit of optimal visibility and safety features.
Clear Plastic Molding emerges as a silent yet indispensable player in the consumer electronics arena. Its significance is underscored by its ability to seamlessly enhance the functionality and aesthetics of electronic devices, solidifying its position as an unsung hero in the dynamic world of consumer electronics.
Revealing the Advantages of Transparent Plastic Molding in Consumer Electronics
Cost-Effectiveness for High-Volume Consumer Electronics Production
Clear plastic molding stands out as the preferred choice in the consumer electronics sector, offering a myriad of advantages that address both practical and aesthetic considerations. Its foremost advantage lies in its inherent cost-effectiveness, providing a notably economical alternative when compared to materials like metal or glass. The molding process, inherently efficient, enables high-volume production at a reduced cost per unit, firmly establishing clear plastic molding as a pragmatic and cost-effective solution for manufacturers in the consumer electronics domain.
Durability and Longevity against Impact, Corrosion, and Wear
Durability and longevity stand as integral guarantees bestowed by clear plastic molding. The resulting molded plastic parts showcase resilience against impact, corrosion, and wear and tear, rendering them ideal for consumer electronics subject to regular use. Moreover, clear plastic maintains its quality over time, ensuring products retain their functionality for an extended period.
Aesthetic Flexibility Enhancing Overall Product Appeal
Clear plastic molding adds another layer to its advantages with excellent aesthetic appeal. The clear plastic utilized in the molding process can be shaped into diverse forms, allowing for extensive product and mold design flexibility. This flexibility empowers manufacturers to create products that not only meet functional requirements but also exude visual appeal. The high-quality look and feel of clear plastic enhances the overall aesthetics of consumer electronic products.
Clear plastic molding emerges as the favored choice in the consumer electronics industry, propelled by its multifaceted advantages. Regardless of its cost-effectiveness, durability, longevity or aesthetics, clear plastic molding proves to be a versatile and reliable solution in the production of a diverse array of consumer electronic products.
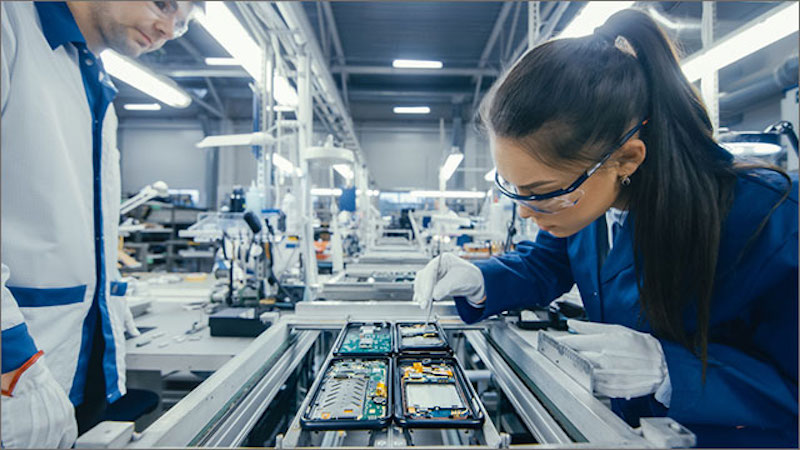
Environmental Impact and Plastic Waste
The application of clear plastic molding in consumer electronics, while promising, is not immune to challenges, prompting a careful examination of these hurdles and the exploration of viable solutions. A significant obstacle arises from the environmental impact associated with plastic waste generated during the molding process. Additionally, the persistent evolution of design complexities in electronic devices poses an ongoing challenge, demanding a continuous stream of innovation.
Evolution of Consumer Electronics Design Complexities
Effectively addressing these challenges demands a collective commitment to sustainable practices, including the implementation of recycling initiatives and the advancement of biodegradable plastics. Furthermore, pivotal strides in mold design and technology are crucial to meeting the demand for intricate electronic components.
By embracing these solutions, the challenges posed by clear plastic molding can be effectively navigated by the consumer electronics industry. This proactive approach ensures a sustainable and innovative trajectory for the integration of clear plastic molding in consumer electronic products.
Conclusion
Clear Plastic Molding stands as a pivotal component in addressing the dynamic requirements of consumer electronics. Its cost-effectiveness, durability, and capacity for aesthetic adaptation highlight its essential role in shaping the modern realm of electronic devices. It ensures seamless integration of functionality and visual appeal, marking Clear Plastic Molding as a crucial element in the ever-evolving landscape of consumer electronics from low volume manufacturing services to mass production.
Besides from injection molding, TEAM Rapid also offers rapid prototyping, CNC machining, and die casting to meet your projects needs. Contact our team today to request a free quote now!