A rough surface finish will give a poor impression of your product’s quality. Meanwhile, a polished surface will make your product look more appealing and high quality. Bead blasting is a preferred surface finishing method for differing material types that you can apply to your final products.
Table of Contents
- 1 Basic Information of bead Blasting
- 2 Advantages of Bead Blasting
- 3 Versatile material uses
- 4 Bead Blasting: How It Works
- 4.1 Prepare the equipment
- 4.2 Choose the bead type
- 4.3 Double-check the cabinet’s safety
- 4.4 Insert the material into the Bead Blasting cabinet
- 4.5 Pour the beads into the gun
- 4.6 Use the gloves with the blast Blasting gun to perform bead blasting on the surface material
- 4.7 Finish the bead blasting process
- 4.8 The post-processing
- 5 Tools Used in Bead Blasting
- 6 Conclusion
Basic Information of bead Blasting
This blasting process offers a unique way of polishing the surface materials of metals, plastics, and composites. The blasting process of tiny beads can cover the whole material surface and offer some added benefits.
Advantages of Bead Blasting
A better surface finish is essential for your final machining products. The surface polish of your final products will determine their overall quality. Here are the advantages of this blasting:
Clean the material surface by bead blasting
Surface contaminants are common in various materials in differing industrial applications. The blasting will scatter tiny beads around the surface of these materials to clean them from multiple contaminants, rusts, and other imperfections. The result will be a cleaner and smoother surface finish for the final products.
Versatile material uses
Bead blasting is compatible with differing materials, making it a versatile surface finishing technique for manufacturing. You can use this technique for plastic and metal materials of varying types. It is also suitable for the surface finishing of composite materials.
Create a uniform surface
Creating the same surface quality across your final products and metal crafts will be easier with bead blasting. A uniform surface is essential to provide a uniform user experience for your final products and minimize problems or misunderstandings. It will also give your final products the same textures across the surface body to make them look more appealing.
Create a better surface texture by Bead Blasting
The surface texture created with blasting will be much better in quality, style, and look than the plain surface without it. Bead blasting can help increase the durability of the surface, which can also help prevent scratches and other problems. You can also choose the style for your bead-blasted surface texture based on your preferences.
Material longevity
Blasting also provides a surface polishing technique that can help lengthen the material longevity. The final products will become more usable in the long term and have a higher overall value. The better longevity characteristics of bead-blasted materials come from the reduced surface stress during use.
Reduce the stress of material surface by bead blasting
Reducing the stress of the material surface is essential to keep the surface area’s polish in good condition. Too much stress on the surface during operation can make your final products degrade over time. The blasting will prevent you from damaging the surface area of the materials by reducing the surface stress.
Healthy environment
Bead blasting is a finishing process that doesn’t harm the environment in its operations. It doesn’t make the surface polish toxic when you use the final products. It will also promote material sustainability, as it offers recyclable final products.
Toxic-free
The toxic-free characteristics of bead-blasted surface finish are essential to ensure a healthy environmental condition during operational usage. The blasting also offers a lead-free surface finishing process that further strengthens the toxic-free features of the final products. You can use this process again after recycling it.
These advantages give blasting a preferable surface finishing option for various rapid manufacturing operations. It offers flexibility and versatility for the manufacturers to fit the final product’s polish with their project’s goal. The improved characteristics of the bead-blasted materials can also help raise the selling price of the final products.
Bead Blasting: How It Works
Apply the best surface polish for your final products with blasting. How does this process work?
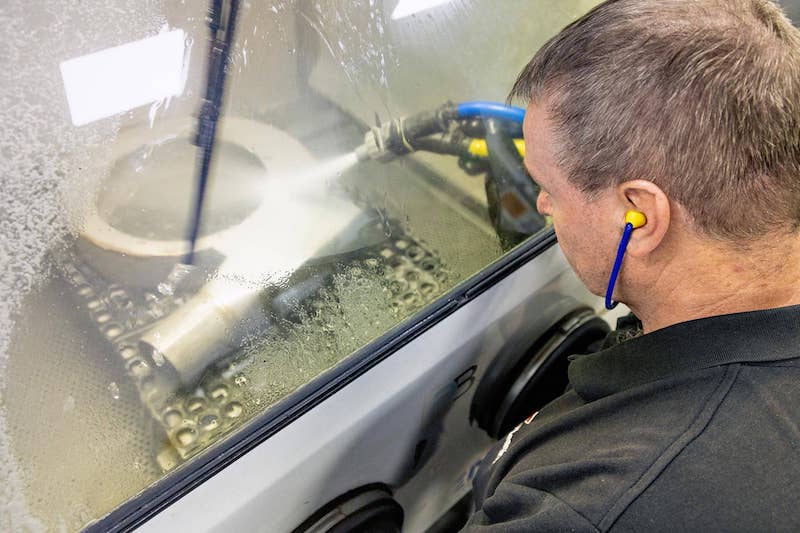
Prepare the equipment
Prepare the equipment for this operation, including the cabinet, gun, gloves, and other accessories. Ensure the equipment is in good working condition before you start the surface finish operation. Clean the equipment as needed to prevent contaminants, dust, and other unnecessary stuff from disturbing the surface finish operation.
Choose the bead type
Different beads will have different effects on the surface finish you apply. The next step is to choose the beads to use, such as glass, ceramic, or steel. It will become the primary media for the surface finishing operation with the blasting method.
Double-check the cabinet’s safety
The blasting cabinet must follow the safety standards before you operate the surface finishing process. You must double-check the functions and safety of the cabinet before proceeding to the next step. Ensure all cabinet windows have robust sealing to prevent the beads from leaving the cabinet area.
Insert the material into the Bead Blasting cabinet
Next, it’s time to put the material you want to polish into the cabinet. Be sure to check the measurements of the material. Place the material into the designated area within the cabinet. Then, you can prepare the blasting procedure.
Pour the beads into the gun
Insert your chosen bead type into the blasting gun. The blasting gun will use an air compressor to blast the tiny beads onto the material surface via the nozzle. Insert enough beads into the gun before starting the bead-blasting operation.
Use the gloves with the blast Blasting gun to perform bead blasting on the surface material
You will need to use the gloves to handle the nozzle gun more easily. You can point the gun onto the material surface you want to polish. Be sure to distribute the tiny beads evenly throughout the material surface area. The small beads will stay on the surface area and give the surface polish characteristics based on your preferences.
Finish the bead blasting process
Continue blasting the beads onto the material surface until you finish the blasting process. The process will finish until you cover all the areas on the material surface with the chosen bead types. Use the gloves to distribute the beads onto the surface area that the nozzle gun cannot reach.
The post-processing
Wait for some time after the blasting process is complete. Then, you can perform post-processing, which involves cleaning the material surface from any residue. You will also need to check for the quality of the polished surface. Then, you can take out the material from the cabinet.
Bead blasting is a straightforward surface polishing technique that requires multiple tools and equipment. You can choose the beads based on the material you want to polish and the features you want to get. Using gloves and a gun for bead blasting is essential to ensure the best result in your surface polishing operation.
Tools Used in Bead Blasting
Bead blasting is a high-speed surface polishing method that requires a series of equipment. You will integrate the tools before using them on the blasting operation. Here are the tools to use:
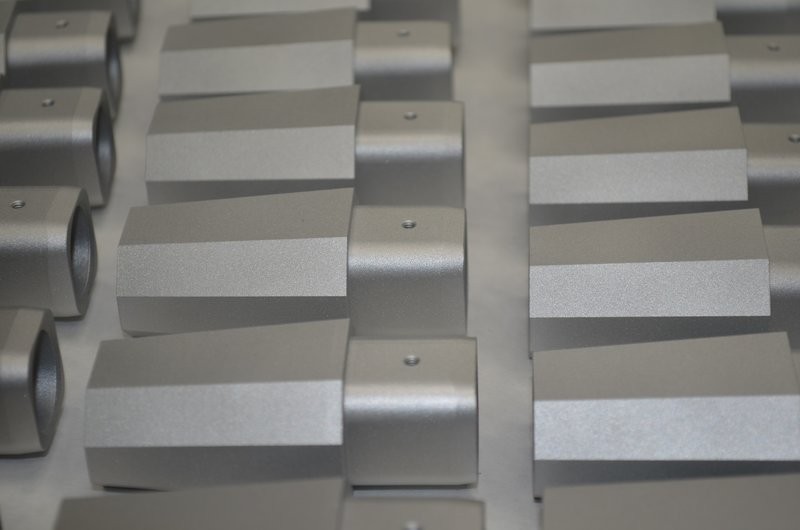
The tiny glass beads
The glass beads are the primary material usable in the bead-blasting surface polish operations. You will blast these tiny glass materials using a specialized bead-blasting gun and scatter them around the material surface. These glass beads will use a gentler approach to surface polishing compared to other abrasive materials. Other bead types are also available.
Gloves
The gloves you use in the blasting operation will ensure your safety and comfort when you carry the glass beads around. The gloves will have a specialized connection with the bead blasting cabinet. It will allow you to spread the glass beads around the material surface to ensure the perfect distribution of the glass beads.
Gun
It is the tool to blast the tiny glass beads into the material surface. You will insert the glass beads into the blaster gun before using it. Next, you can use the foot pedal to activate the blaster gun and spread the glass beads more comfortably for a long blasting session.
Cabinet
The cabinet is the primary equipment you will use to undergo the bead blasting process. It is where you will place the material for bead blasting and perform the blasting process. You will connect the other tools to the bead blasting cabinet, such as the gloves and the bead blasting gun.
Extra protection
Extra protection is available for the cabinet viewing window, allowing you to observe the blasting process with a bigger view. With it, you can spread the glass beads evenly throughout the material surface. The extra protection on the viewing window will also give you a more thorough examination of the bead blasting operation and avoid potential problems.
Sealing
The cabinet must have a secure seal to prevent the glass beads from getting outside. The dust from the blasting process can pose a health risk when you catch or inhale it. The sealing will offer the cabinet double safety and security to ensure a safe bead blasting operation.
These are the tools usable in the blasting operations. Bead blasting requires high-quality tools with proper safety features to run the process. Without the right tools, you can’t run the bead blasting operations because of the safety risks you will get.
Conclusion
Use bead blasting to get the best surface polish for your final products and strengthen your product’s characteristics. Choose the bead types that are suitable for your material type. Determine the features you want to get from the bead-blasting procedure before proceeding. TEAM Rapid offers the value-added post finishing for your rapid prototypes, and volume manufacturing needs. Contact us at [email protected] today to request a free quote now!