Anodizing is one kind of surface finish to protect your custom metal parts against corrosion, resists scratching and enhances aesthetic quality, it is one of the most durable surface finish available for metal parts. Aluminum Anodizing is widely used in many different industries. Today let’s have a look at aluminum anodizing, processes and details that will help to show why anodizing is so popular and critical.
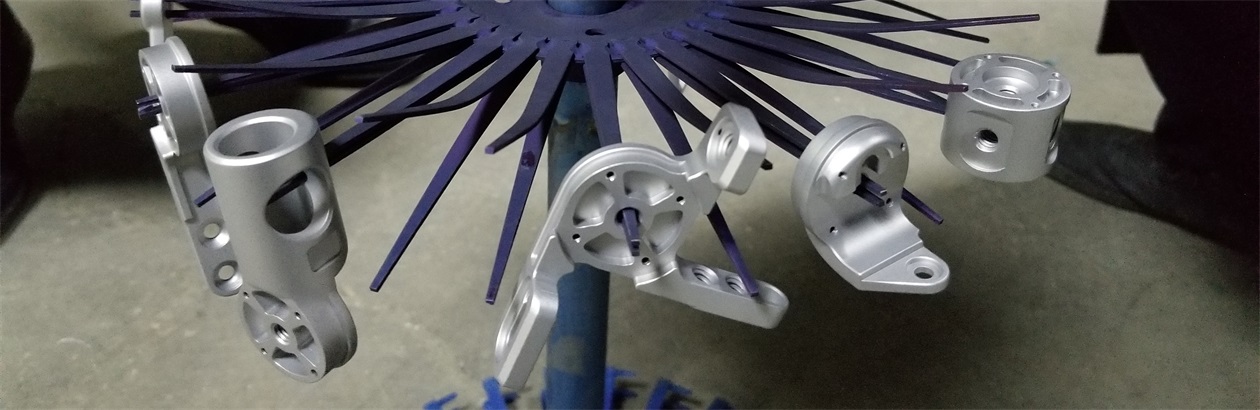
Table of Contents
- 1 What is Anodizing Process?
- 2 How is the Aluminum Anodizing Process?
- 3 Barrier layers in Anodizing Aluminum
- 4 Hard Anodizing
- 5 Does Aluminum Need to have Corrosion Protection?
- 6 How to have Color Aluminum Anodizing?
- 7 Anodized Aluminum has metallic sheen
- 8 Other material can also be anodized
- 9 It is impossible to anodize the whole part?
- 10 What benefit does of Aluminum Anodizing offer?
- 11 Aluminum Anodizing Service for Your Custom Metal Parts
What is Anodizing Process?
Anodizing is an electrochemical process which convert the surface of metal into a durable, corrosion resistant, decorative and anodic oxide finish. Anodizing increase the thickness of the natural oxide oxide layer on the surface of metal. Metal parts are treated forms the anode electrode of an electrolytic cell so the process is called anodizing. Anodizing increase resistant to corrosion and wear. It offer better adhesion for primers and glues. Anodic films is used for many effects. For example, cosmetic effect with thick porous coasting which can absorb dye and cosmetic effect with transparent coasting which add reflected light wave interference effects. Anodic films are commonly applied to protect aluminum alloys. Anodizing process exist for titanium, zinc, magnesium, niobium, zirconium, hafnium and tantalum. Anodizing changes the microscopic texture of the surface and the crystal structure of the metal. Thick coating are porous normally. So a sealing process is usually need to achieve corrosion resistance. Anodized aluminum surface are harder than aluminum but have low to moderate wear resistance which can be improved with increasing the thickness or by applying sealing substances. Anodic films are stronger than most types of paint and metal plating. At TEAM Rapid, you can use our anodizing aluminum service to enhance the functionality and appearance of the metal parts. Anodizing can be done on a wide range of materials. Today, we will talk about anodizing aluminum. Here is the eight things you need to know about anodizing aluminum.
How is the Aluminum Anodizing Process?
When to prepare aluminum for anodizing, make sure the surface is cleaned and rinsed. And then place it into a bath of some electrolytic solution like sulfuric acid. How does the anodizing aluminum process work? When is the process is ongoing, a positive electric charge is sent through the aluminum and a negative charge is applied to plates in the electrolyte. How the An electrolyte is an electrically conductive solution. A positive electric charge is applied to the aluminum to make it anode. A negative charge is applied to plates which are suspended in the electrolyte. The electric in circuit create positive ions to be attracted to the negative plates. The electric in circuit create positive ions to be attracted to the negative plates. And negative ions to flock to the positive anode.
Barrier layers in Anodizing Aluminum
The electrochemical reaction causes pores to form on the surface of the aluminum because excess positive ions escape. The aluminum at the surface combines with the negatively charged O2 ions to create aluminum oxide. This is the barrier layer which defense against further chemical reactions. The pores will continue to penetrate deeper into the substrate. For non-hard coatings, the depth can be more than 10 microns. When this level is done, if it is no need to add color, the process is stopped and the suface can be sealed by rinsing in water. You will get the hard and natural aluminum oxide coating which withstand chemical attack and scratch resistant.
Hard Anodizing
Hard anodizing is also called type III. This method also used sulfuric acid. It produce a thicker anodized layer. Hard anodizing is suitable for coloration. It provides greater corrosion protection and resistance to wear in hard environments. Hand anodizing needs more times and it is more expensive. It creates superior results.
Does Aluminum Need to have Corrosion Protection?
Aluminum can deteriorate in the presence of oxygen although aluminum does not rust. Oxygen is reactive. When the aluminum parts is exposed to the atmosphere, a layer of aluminum oxide is formed on the surface which protect against corrosion. Aluminum withstand more than just pure water and air. Acid rain, salt water can exploit weaknesses in the surface.
How to have Color Aluminum Anodizing?
Colored aluminum is increasing need when it comes to anodizing. The pores etched into the surface are ideal for introducing tints or pigments. The pigment fills the empty pores up to the surface. Anodized colors are durable. The color can not be scratched off from the surface as the colors are deep down. It can be removed only by grinding away the substrate.

Anodized Aluminum has metallic sheen
After adding color to the anodized aluminum, it has a characteristic of metallic look. It caused by the uniform electro-chemical etching, a rough surface is left behind. The surface is rougher and the colors are more durable when the pores is deeper. Light striking the surface parts interacts with the colorant and partly with the uncolored metal.
Other material can also be anodized
Anodizing can work with other material like magnesium, titanium and conductive plastics. Anodizing process is not expensive. It is reliable and durable. Anodizing process is widely used in architectural fittings as it is beautiful and impervious to the effects of weathering.
It is impossible to anodize the whole part?
Anodizing requests a part is immersed in a series of chemical baths. The parts should be hung to keep it from failing to the bottom of the tank. When the holding fixture touches the parts, the anodizing chemicals will not work right. So, it it better to design a place on the part that can be used for hanging.
What benefit does of Aluminum Anodizing offer?
Anodizing aluminum process is widely used for a wide range of applications. For example, you will find anodized aluminum parts in aircrafts, consumer goods, sport equipment, electronics and more. Anodized aluminum parts are durable and hard. As anodized aluminum parts are abrasion resistant and corrosion resistant, they are suitable to be placed in harsh environment. It also provide thermal insulation to metal products. Anodizing aluminum process makes metal parts last longer than raw parts. The the coating is thinner than paints and powders. Anodizing aluminum parts have eco-friendly finish, it is recyclable. Compared to painting and powder coating, the post-processing technique is affordable.
Aluminum Anodizing Service for Your Custom Metal Parts
TEAM Rapid is able to offer advice on the many different finishing services including aluminum anodizing service, painting, silk printing etc for your rapid prototyping and low volume manufacturing needs. Our engineers will help you to find the solution that fits your time, budget to market, let’s get started today!