Complex manufacturing innovations often take the form of sophisticated methods and techniques. One such popular technique is insert molding—an advanced process in which metal or other materials are smoothly added to plastic parts. As industries evolve to meet demands for efficiency, cost-effectiveness, and for dealing with product durability, understanding insert molding is importance. This comprehensive guide seeks to uncover the intricacies of insert molding techniques. Exploring the various techniques, applications, and subtleties that make it a cornerstone of modern design. While guiding you through the complexities this guide seeks to shed light on how inserts are applied.Molding acts as a catalyst to increase efficiency and versatility in product design and production.
Table of Contents
- 1 Materials Commonly Utilized in Insert Molding Techniques
- 2 How to Insert Molding Unveils its Manufacturing Magic
- 3 Applications Showcasing the Versatility of Insert Molding techniques
- 4 Navigating Challenges and Considerations in Insert Molding techniques
- 5 Advancements of Insert Molding techniques in Manufacturing:
- 5.1 Elevated Component Durability
- 5.2 Streamlined Assembly Processes
- 5.3 Compactness and Weight Reduction
- 5.4 Insert Molding Techniques can apply in Many Design Options
- 5.5 Tailored Customization
- 5.6 Augmented Electrical and Thermal Characteristics
- 5.7 Insert Molding Techniques: Enhanced Resistance to Environmental Factors
- 6 Conclusion
Materials Commonly Utilized in Insert Molding Techniques
The fusion of disparate components into a unified product defines the ingenuity behind insert molding. Picture it as seamlessly incorporating a metal element into a plastic structure, creating a singular, cohesive piece. The process unfolds by selecting an “insert,” a component that could be a blend of metals or plastics. As molten plastic envelops the insert within a mold under intense pressure, a remarkable transformation takes place. The materials of choice play a pivotal role in this alchemy, with thermoplastic resins like ABS or PC offering durability and chemical resistance. However, for applications demanding enhanced strength or electrical conductivity, metals such as stainless steel or brass become preferred choices. The selection of materials in insert injection moulding is a nuanced decision, considering the product’s intended use, desired properties, and aesthetic requirements.
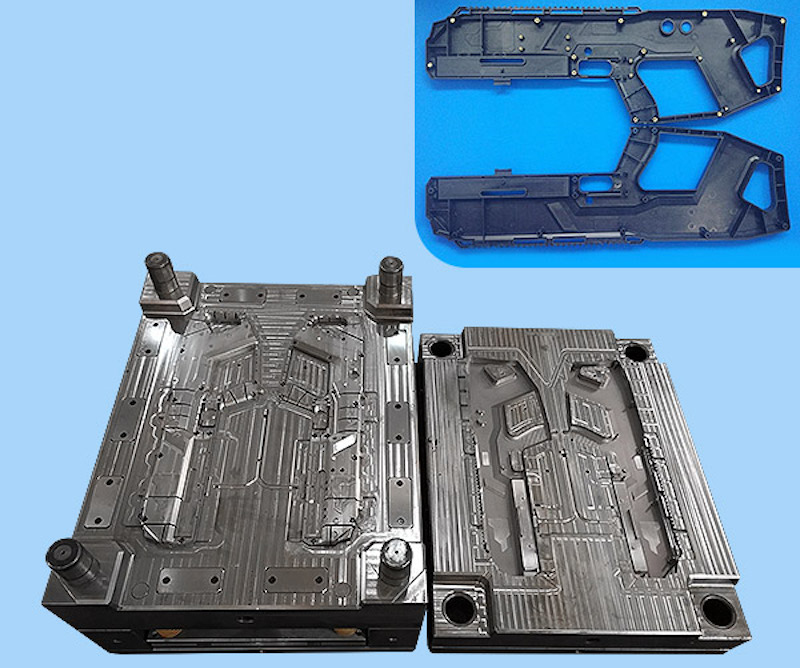
How to Insert Molding Unveils its Manufacturing Magic
Insert molding, a captivating technique, intricately marries pre-shaped inserts with molten plastic, forging a seamless, robust product. The process unfolds methodically: the insert, positioned precisely within the mold, enhances the final product’s strength or features. With the mold sealed tightly, molten plastic rushes in, embracing the insert in a precise dance of heat and pressure. As the plastic solidifies, the mold releases its grasp, unveiling a final piece where the insert is seamlessly embedded. Beyond aesthetics, this combination ensures a product that not only looks appealing. But also boasts the durability and functionality of both plastics and inserts. The intricate dance of heat, pressure, and material selection culminates in a manufacturing spectacle that transcends mere functionality, offering a marriage of form and function.
Applications Showcasing the Versatility of Insert Molding techniques
In the vast landscape of rapid manufacturing, insert molding emerges as a versatile artisan, showcasing its prowess across diverse industries. Its role as a transformative force is most pronounced in aerospace and defence, where lightweight, vibration-resistant, and tightly sealed parts are paramount. Medical and healthcare arenas benefit from the precision of insert molding, delivering tools and implants crafted with meticulous accuracy. In the realm of electronics and consumer goods, insert molding quietly elevates products, seamlessly integrating connectors and fasteners to ensure reliability and aesthetics. As a Swiss Army knife of manufacturing, insert molding transcends the ordinary, leaving its mark across industries and applications.
Perfecting the art of insert molding mirrors the delicate precision of baking a flawless cake. Attention to detail is paramount in addressing the intricacies of mold design, material shrinkage, and heat management. The materials chosen for the process are akin to selecting the finest ingredients for a recipe; their compatibility and synergy are crucial for success. Trials and meticulous testing become essential, ensuring that the chosen materials complement each other seamlessly. As we navigate the complexities of insert plastic molding, understanding the challenges and considerations becomes a roadmap to achieving manufacturing excellence. Having explored its applications, the focus now shifts to the future of insert molding—a horizon ripe with possibilities and innovations. Stay tuned for the unfolding chapters of this evolving manufacturing saga!
Advancements of Insert Molding techniques in Manufacturing:
Elevated Component Durability
The incorporation of inserts crafted from materials such as metals or ceramics elevates the durability and strength of the end product in insert molding. This holds particular significance in industries where robust and resilient components are paramount.
Streamlined Assembly Processes
The conventional methods of assembling plastic parts with inserts involve numerous steps. Insert molding simplifies this process into a singular operation, diminishing assembly time and bolstering overall production from low volume manufacturing to mass production efficiency.
Compactness and Weight Reduction
Insert molding makes it easier to create parts that are both strong and light. Through the use of inserts made of materials such as lightweight metals or speciality polymers, manufacturers are able to design products with reduced total weight.
Insert Molding Techniques can apply in Many Design Options
The field of insert molding provides opportunities for the development of complex and sophisticated product and mold design that might be difficult to realize with other techniques. This flexibility is especially useful for businesses with unique or strict design requirements.
Tailored Customization
Manufacturers find ease in tailoring products through the selection of varied inserts and plastic materials in insert molding. This flexibility empowers the creation of customized solutions that align precisely with specific customer requirements.
Augmented Electrical and Thermal Characteristics
Insert molding, when employing specialized inserts, has the capability to enhance a product’s electrical insulation or thermal conductivity. This attribute renders the product suitable for a broad spectrum of applications, expanding its utility across diverse industries.
Insert Molding Techniques: Enhanced Resistance to Environmental Factors
An additional stride in insert molding lies in the improvement of products’ resistance to environmental factors. By carefully selecting inserts and plastic materials with heightened resistance to elements such as humidity, temperature variations, and chemical exposure, manufacturers can ensure that the final product maintains its integrity and performance even in challenging environmental conditions. This advancement expands the range of applications for insert molding, making it a crucial consideration for industries where environmental durability is a key requirement.
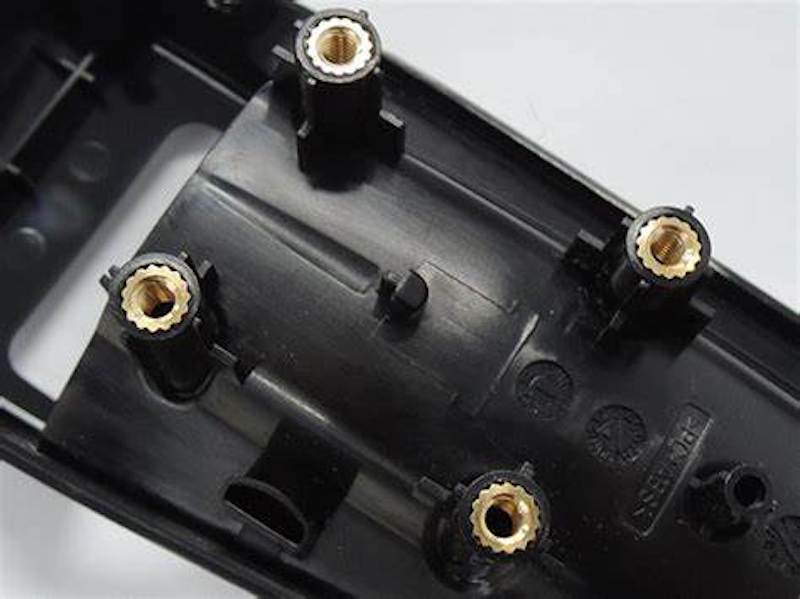
Conclusion
In a dynamic manufacturing environment, where precision and innovation intersect, insert molding emerges as a transformative force. This comprehensive guide travelled through the intricacies of packaging methods and techniques, focusing on an area where disparate components come together to form complex and functional products well. As the industry continues to evolve, the knowledge presented in this guide serves as a valuable compass that increases productivity for manufacturers, reduces costs, and maximizes product life. Whether in automotive, electronics or the medical field, the flexibility and accuracy of inputs promise to play an important role in shaping the future of manufacturing. As we conclude this review, it is clear that materials the insertion stands not only as a sculpture but as a beacon, pointing the way forward in the relentless pursuit of excellence.
Besides from insert molding, TEAM Rapid also offers rapid prototyping, CNC machining, and die casting to meet your needs. Contact our team today to request a free quote now!