Spindle movements are an essential part of any CNC machine operation, which can affect the rotations of the cutting tools. Maintaining a stable rotational movement at high speed is crucial to ensure the best cutting results in your CNC production. You will need CNC bearings to do that, here are 10 types of bearings that used commonly in CNC machining and CNC machining services.
Bearing Usage
Aside from CNC machining, bearings are also suitable for various mechanical aspects of manufacturing production. This article will focus on the bearing types for CNC machining.
Types of Bearings
The stability and speed of the spindle movements in CNC will affect the quality of your cutting results. Without having a stable spindle rotation, CNC machines can’t maintain the best performance and accuracy during their operations. You will need to use bearings to keep the spindle movement stable. Here’s the list of bearing types to use in CNC machining:
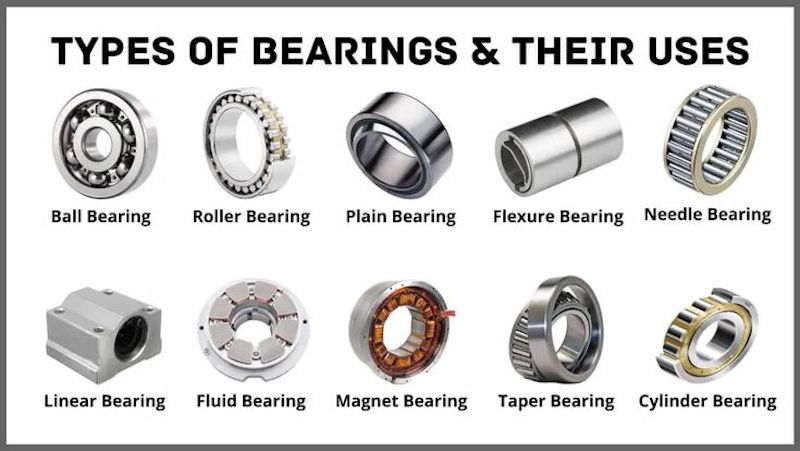
Ball
The high-speed spindle movements need the ball bearing type to accommodate. The ball bearing will handle the high radial load and high-speed spindle movements to maintain accuracy during the CNC operations. It helps deliver the highest performance and precision to any CNC task.
Types of Bearings: Roller
The heavy-duty CNC equipment will require the type of roller bearing to handle its spindle movements. This bearing will keep the machine’s movements smooth during heavy loads. It reduces the spindle friction to support one-directional axial and radial loads.
Plain
Plain bearings use the sliding motion to help reduce the friction between moving parts in CNC equipment. It can contribute to smoother movements between CNC components, including spindles and others. It is available as metal or non-metal bearings, which can give the best performance and reliability in each CNC operation.
Types of Bearings: Flexure
Misalignment and other spindle rotation issues can happen during precision machining services and operations. Flexure bearing can help re-align the spindle rotation when these issues occur. This bearing will keep the balance of the spindle rotation while still carrying a consistent workload.
Needle
For small or lightweight CNC equipment, needle bearings are valuable to help maintain the rotational balance of the CNC spindle. It resembles a needle because it uses a thin cylinder with a small radial size. The needle bearing can help maintain a high rotational speed for the spindle during CNC applications.
Types of Bearings: Linear
Linear bearings are valuable to substitute the traditional bearing type while offering more features. It uses a specialized mechanism that can help increase the accuracy of your CNC applications. It can support one-directional movements for the CNC equipment while maintaining high speed and performance.
Fluid
Fluid bearings use the type of liquid or gas to help control the spindle movements and stabilize it during CNC applications. You will use the high-pressure system to maintain the fluidity of these bearings. Using the fluid bearings will help stabilize the spindle movements without making high vibrations. It can also help reduce noises that come from the rotational movements.
Types of bearings: Magnet
It uses magnetic bearing technology that helps levitate the spindle for better rotational movement. You can use both passive and active magnetic bearings for different purposes. The active type will use the function of mechanical bearing to stabilize one-axis rotation. The active magnetic system uses electromagnetic technology for the magnetic stability of the spindle rotation.
Taper
This bearing has a similar role to the roller type, which allows for heavy-duty workloads. However, its conical design can help reduce heat during the spindle rotation. Also, taper bearings can reduce torque within the CNC equipment while keeping its speed consistent.
Cylinder
Cylinder bearings can handle heavy loads in your CNC operation while maximizing the machine’s performance. It uses a cylinder-based design with double rows, making it easier to handle heavy-duty spindle movements. You can combine cylinder bearings with precision-type bearings to maintain high accuracy in CNC operations.
Without these bearings, CNC machines won’t work well during any applications. These bearings have the essential function of stabilizing the spindle movements and keeping the CNC machine’s performance at its best.
Challenges with Types of Bearings
Using bearings will not always be smooth sailing for your CNC production and rapid manufacturing. Some issues will appear every once in a while, which will require your swift response. Here are some challenges of using CNC bearings:
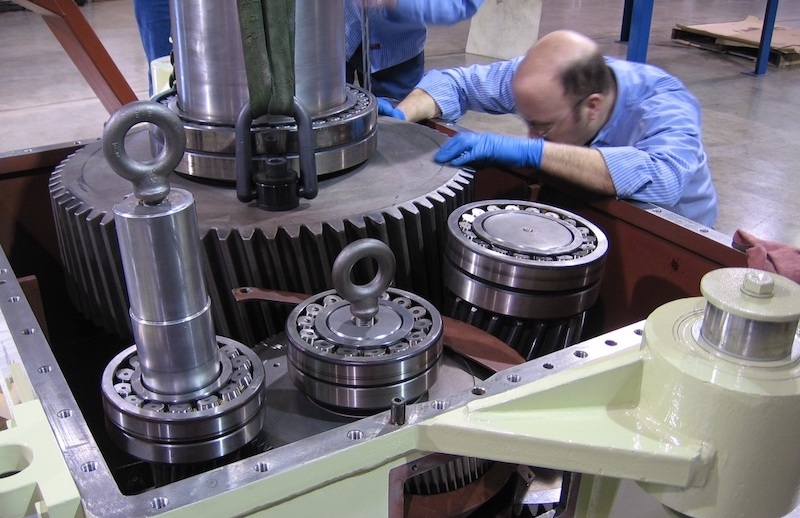
Machine requirements
Each bearing type will only correspond with specific machine requirements. So, different bearings will be usable for different CNC machine types. Each bearing will also have specific functions, which might be un-switchable with other bearings.
Workloads
Each bearing can only handle a specific workload requirement. There are CNC bearings that can only handle light workloads. Some can handle heavy-duty workloads. You must pick the bearing to use accordingly and match it with the workload specifications of your CNC equipment.
Skilled technicians
The installation and management of CNC bearings require skilled technicians who understand the workings of CNC equipment. The hiring of these technicians can incur some significant expenses on your part. Also, the work of skilled CNC technicians is essential to fix any issues related to using the CNC bearings.
Cost-effectiveness
You must replace the bearings regularly, which can incur additional costs for your production. Also, the issues related to the malfunctioning CNC bearings can cause massive expenses in fixing them. So, the cost-effectiveness factor in choosing the perfect bearings for each CNC application is paramount to your production success.
Replacements
Replacing the bearings can be daunting, as you must stop the production for maintenance purposes. It can also take a long time, depending on the complexity of the installation process. Also, you must readjust and reconfigure the bearings before using them for production.
These challenges of using CNC bearings can sometimes hinder your production progress. Be sure to have some risk mitigation plans ready to handle these challenges.
Conclusion
Understanding the types of CNC bearings, their functions, and how to apply them in your CNC operation is crucial for your production success. Different bearings work on different CNC equipment, making it essential for you to choose them carefully. Using incompatible or low-quality bearings for your CNC machine can destabilize the movements or rotations of the machine during operations. It is something you need to avoid. Be selective in the quality of bearings you use for the CNC equipment. Their durability will affect the success of your production operations and the quality of your final products. Contact TEAM Rapid today for your custom made product or metal craft.